Il settore del packaging sta vivendo una profonda trasformazione grazie all’integrazione sempre più spinta dei robot. Un esempio emblematico di questa tendenza è rappresentato dal caso di successo di Lindt & Sprüngli S.p.A., presentato in occasione dell’ABB Robotics Packaging Day tenutosi il 27 marzo nella sede ABB di Vittuone.
Lindt ha ottimizzato i processi di confezionamento del suo stabilimento di Induno Olona, in provincia di Varese, attraverso l’adozione delle soluzioni robotiche firmate ABB.
Indice degli argomenti
I robot ABB per il packaging di Lindt
Lindt ha saputo cogliere le potenzialità della robotica per migliorare l’efficienza, la flessibilità, la qualità e la sicurezza del suo packaging. Nel sito produttivo di Induno Olona, focalizzato sulla produzione delle celebri boules, uova di Pasqua e altri prodotti, sono impiegati ben 41 robot ABB.
Michele Nicolardi, Electrical Maintenance Engineer di Lindt & Sprüngli S.p.A., ha spiegato come i robot ABB siano impiegati in diverse fasi del processo produttivo: 15 robot articolati a 4 assi, modelli IRB 260, IRB 660 e IRB 760, si occupano della palettizzazione sia del prodotto finito in cartoni che del semilavorato in cassette di plastica.
Un robot più grande, l’IRB 760 si distingue per la sua capacità di operare su tre linee differenti e di gestire sia scatole di cartone che cassette di plastica. L’adozione di un sistema a doppia presa su uno dei robot ha permesso di ottimizzare i tempi di produzione.
Ci sono poi 8 robot a sette assi, modelli IRB 4600 e IRB 2600, che sono deputati alla depallettizzazione, alimentando le linee di confezionamento a partire dal prodotto in cassette di plastica.
C’è poi spazio anche per i robot Delta con cinematica parallela. Ben 11 robot a quattro assi modello IRB 360 alimentano infatti le linee di incarto e controllano la qualità del guscio del prodotto nudo. Questi robot, dotati di sistemi di controllo mediante telecamera, verificano la corretta posizione del prodotto e leggono il codice, garantendo così la qualità e la sicurezza del prodotto.
Da ultimo 7 robot SCARA controllano la qualità del prodotto finito, eliminando i prodotti privi di ripieno grazie a sistemi di controllo mediante termocamera.
La collaborazione con ADS Automation, partner storico di Lindt, è stata fondamentale per la realizzazione delle isole di palettizzazione e depalettizzazione.
L’offerta ABB per il packaging: robot articolati, delta e SCARA
ABB Robotics vanta un’esperienza consolidata nel settore del packaging, con una gamma completa di soluzioni robotiche progettate per rispondere alle diverse esigenze applicative.
Ne ha parlato Paolo Pellicciardi, Sales Specialist di ABB Robotics Italia, che ha fornito una panoramica dettagliata sull’offerta, sottolineando come la chiave di lettura dei prodotti si basi su aspetti di protezione, performance e specializzazione per il packaging.
I robot articolati rappresentano una colonna portante dell’offerta ABB per il packaging, distinguendosi per la loro versatilità e capacità di eseguire un’ampia gamma di operazioni. La gamma si articola in robot di piccole, medie e grandi dimensioni, con diverse configurazioni in termini di payload e sbraccio per adattarsi a molteplici applicazioni.
Tra i robot articolati di piccole dimensioni, l’IRB 1300, con un payload fino a 12 kg e sbraccio fino a 1.4 m, offre elevate performance in un pacchetto compatto, ideale per operazioni che richiedono velocità e precisione in spazi ristretti. L’IRB 1600, disponibile con payload fino a 10 kg e sbraccio fino a 1.45 m, si caratterizza per la sua affidabilità e flessibilità di montaggio. L’IRB 2600, con payload fino a 20 kg e sbraccio fino a 1.85 m, è progettato per applicazioni che richiedono carichi maggiori mantenendo un’elevata produttività. Questi robot possono essere configurati con diversi gradi di protezione (fino a IP67 e Foundry Plus 2) e per l’operatività in clean room (fino a ISO 4), rendendoli adatti a settori con stringenti requisiti igienico-sanitari come il farmaceutico e l’alimentare.
La categoria dei robot articolati di medie dimensioni include modelli come l’IRB 4600, con payload fino a 60 kg e sbraccio fino a 2.5 m, un robot altamente produttivo adatto a diverse applicazioni di packaging. Le serie IRB 5710 e IRB 5720 offrono payload fino a 180 kg e sbraccio fino a 3 m, combinando elevate performance con versatilità di montaggio. Per applicazioni di palettizzazione, ABB propone robot articolati dedicati, come l’IRB 460, l’IRB 660 e l’IRB 760, con payload che variano da 110 kg a 450 kg e sbraccio fino a 3.2 m. Le serie IRB 7710 e IRB 7720 estendono la capacità di palettizzazione fino a 700 kg di payload, rispondendo alle esigenze di movimentazione di carichi elevati. Tutti questi robot per la palettizzazione sono generalmente dotati di protezione IP67, un elemento distintivo che ne sottolinea l’affidabilità anche in ambienti gravosi.
I robot delta eccellono in applicazioni di pick and place ad alta velocità. ABB offre una gamma molto ampia, con payload che variano da 1.5 kg a 15 kg. L’IRB 360 FlexPicker è uno dei prodotti più iconici, una macchina eccezionalmente versatile e flessibile, disponibile con configurazioni a 4, 6 o 8 assi e con opzioni washdown per settori con elevati standard igienici. L’IRB 365, con un payload di 1.5 kg e un quinto asse, offre maggiore flessibilità per operazioni di confezionamento complesse. L’IRB 390 FlexPack, con payload fino a 15 kg nella versione a 4 assi e 10 kg in quella a 5 assi, rappresenta una soluzione all’avanguardia per applicazioni di pick and place che richiedono sia velocità che capacità di carico. I robot delta ABB sono progettati per il montaggio invertito e disponibili con diversi gradi di protezione, inclusa l’opzione Clean Room ISO 5.
I robot SCARA completano l’offerta ABB per il packaging, fornendo soluzioni altamente produttive per operazioni di assemblaggio, manipolazione e pick and place che richiedono precisione su piani orizzontali. La gamma include l’IRB 910INV per montaggio a soffitto e le serie IRB 920 e IRB 930 per montaggio a pavimento, con payload fino a 20 kg e sbraccio fino a 1.05 m. Una caratteristica distintiva di alcuni modelli scara ABB è l’assenza della tipica zona “morta”, ampliando l’area di lavoro operativa. I robot SCARA sono disponibili con protezione fino a IP67 e opzioni per clean room fino a ISO 1. La loro elevata ripetibilità e velocità li rendono ideali per applicazioni come l’inserimento di prodotti in imballaggi e il controllo qualità, come dimostrato nell’applicazione presso Lindt.
Item Picker, visione e AI aiutano il robot
La soluzione Item Picker è stata specificatamente progettata per il prelievo di oggetti non uniformi, superando la sfida iniziale di manipolare oggetti senza una forma geometrica definita. Successivamente, la sua applicazione è stata estesa ad altri settori, tra cui il fashion, il tessile e l’e-commerce, con un focus anche sul settore farmaceutico.
Sebbene questi settori possano apparire simili, presentano problematiche distinte, come il riconoscimento di forme e colori variabili, la gestione di luci e il movimento degli oggetti nel settore del fashion e dell’e-commerce, e la necessità di alta velocità e precisione nel farmaceutico.
Un elemento fondamentale della soluzione Item Picker è l’integrazione dell’intelligenza artificiale e di un sistema di visione artificiale pre-tarato prima di essere implementato, che garantisce una accuratezza prevista del 99%. Lo sviluppo del software si concentra sull’integrazione efficace di hardware (robot, sensori, telecamere) e software, con particolare attenzione alla prevenzione delle collisioni durante le operazioni di picking.
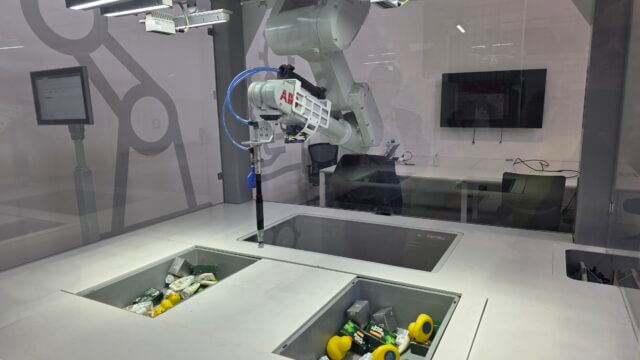
La flessibilità è un altro aspetto rilevante: l’Item Picker può gestire spazi di lavoro variabili e di adattarsi a diverse velocità di picking e deposito. Nel settore farmaceutico, ad esempio, è stata sviluppata una pinza specifica per la manipolazione di oggetti di forma sconosciuta, sfruttando la capacità del sistema di apprendere e memorizzare le caratteristiche degli oggetti, associandole a strategie di presa ottimali.
Ultimo, ma solo in ordine di esposizione, la semplicità d’uso ottenuta attraverso la combinazione integrata di software, hardware e robot, supportata da sistemi di intelligenza artificiale che rendono l’applicazione più semplice per l’operatore.
Di recente ABB ha potenziato l’offerta di item picking con soluzioni basate sull’intelligenza artificiale per il fashion e la logistica.
Il FlexBuffer per la logistica
La soluzione FlexBuffer di ABB è un sistema robotizzato progettato per offrire una gestione efficiente e flessibile delle merci, nato per rispondere alle esigenze del settore della logistica. Come ha spiegato Nicola Tricomi, Sales Business Development Manager della divisione Robotica di ABB, il FlexBuffer è in grado di svolgere tre funzioni principali: buffering di grandi quantità di merci, come l’accumulo di bevande prima dell’ulteriore confezionamento o pallettizzazione; stoccaggio e recupero di merci, come articoli resi in magazzini di abbigliamento; e sequenziamento di contenitori prima della pallettizzazione nella distribuzione di prodotti alimentari.
Il sistema FlexBuffer è composto da diverse componenti:
- Un robot ABB, tipicamente un IRB 6700 con un payload fino a 150 kg e uno sbraccio di 3.2 metri. Tuttavia, come accennato, la scelta del robot può variare in base alle esigenze di performance.
- Un gripper appositamente sviluppato per la manipolazione di totes (cassette in plastica) o box (scatole di diverse forme e dimensioni). Sono disponibili pinze a singolo o doppio contenitore.
- Una scaffalatura modulare a doppio scomparto che permette una maggiore capacità di stoccaggio. Il numero di scaffali può variare (ad esempio, 15 paia di scaffali).
- Trasportatori di alimentazione e di uscita per collegare il FlexBuffer con l’automazione a monte e a valle. Questi possono interfacciarsi anche con gli AMR (Autonomous Mobile Robots) di ABB.
- Un software Application Controller che gestisce tutte le operazioni all’interno del FlexBuffer, inclusa l’archiviazione dei colli nella scaffalatura e l’interfacciamento con diversi sistemi aziendali (QMS, WMS, MES).
- Sistemi di sicurezza come recinzioni con accessi controllati e un PLC di sicurezza.
Il FlexBuffer è disponibile in diverse configurazioni, principalmente Mixed (per scatole di diverse dimensioni) e Totes (per contenitori standard). Le performance del sistema sono misurate in termini di capacità di stoccaggio (che varia a seconda delle dimensioni degli oggetti, ad esempio 210 o 480 item assumendo dimensioni standard) e cicli di lavoro (single cycle e combined cycle, che indicano la velocità di carico e scarico del magazzino). Una caratteristica importante del FlexBuffer è la sua modularità, che permette di collegare più unità in serie per aumentare la capacità e la velocità del sistema. L’interfacciamento con il cliente avviene tramite il system integrator, che conosce l’architettura logistica complessiva e definisce il flusso delle merci. Il software di controllo del FlexBuffer ottimizza la posizione degli oggetti all’interno del magazzino in modo dinamico.
Cobot e AMR: collaborazione e logistica intelligente
L’evoluzione della robotica industriale vede una crescente importanza dei cobot (robot collaborativi) e degli AMR (robot mobili autonomi). La combinazione di cobot e AMR può offrire alle aziende nuove opportunità per migliorare l’efficienza, la flessibilità e la resilienza delle proprie operazioni.
ABB offre la gamma di cobot GoFa CRB 15000, con payload da 5 kg a 14 kg e sbraccio fino a 1.52 m, progettati per una collaborazione sicura e intuitiva con gli operatori umani. Sono robot facili da programmare e implementare, ideali per applicazioni di handling e palettizzazione in contesti in cui la flessibilità e l’interazione uomo-robot sono fondamentali. Tutti i cobot ABB sono certificati per l’utilizzo in clean room.
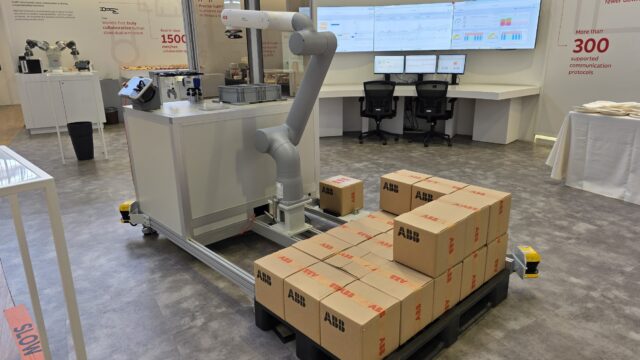
in una demo di pallettizzazione nel demo center ABB di Vittuone
Oltre ai GoFa ABB propone anche i robot Swifti, derivati dai robot tradizionali e quindi in grado di operare ad alta velocità, pur garantendo la sicurezza grazie a sensori avanzati, e il celebre Yumi nelle varianti dual arm e single arm con sette gradi di libertà.
Nel campo della logistica interna, gli AMR ABB rappresentano una soluzione all’avanguardia per l’automazione del trasporto di materiali. Ne ha parlato Marco Locatelli, AMR Sales and Market Development Manager di ABB.
Il portafoglio AMR include le famiglie Flexley Tug (carrelli trainatori), Flexley Mover (per il sollevamento di pallet e altro) e Flexley Stack (transpallet e carrelli controbilanciati).
Questi veicoli autonomi, guidati da sistemi di navigazione Visual SLAM basati su telecamere e intelligenza artificiale, sono in grado di muoversi in modo sicuro e flessibile all’interno degli ambienti di fabbrica e di magazzino, ottimizzando i flussi logistici.
Il software di gestione della flotta AMR Studio semplifica la mappatura, il commissioning e la gestione dei veicoli, consentendo l’integrazione con i sistemi di fabbrica di alto livello (ERP/MES) e con l’automazione di fabbrica (PLC, sensori) tramite protocolli standard come API REST e OPC UA.
Le applicazioni tipiche degli AMR includono il buffering di contenitori, lo stoccaggio e il recupero di merci e il sequenziamento di contenitori prima della palettizzazione.
L’acquisizione della spagnola ASTI da parte di ABB ha ulteriormente rafforzato la sua presenza nel settore della robotica mobile, con un parco installato di oltre 7000 AMR a livello globale.
Il ruolo del software: RobotStudio e OptiFact
RobotStudio è il celebre software di simulazione e programmazione offline di ABB che permette agli utenti di creare, simulare e testare applicazioni robotiche in un ambiente virtuale.
RobotStudio consente una simulazione accurata del comportamento dei robot e dell’intero sistema automatizzato prima della sua implementazione fisica. Tra le sue funzionalità principali vi sono la comparazione in tempo reale tra il controllo virtuale e quello reale, la generazione automatica di traiettorie, la valutazione del consumo energetico, la possibilità di importare direttamente file CAD, la modifica online dei programmi, la simulazione dello spazio di lavoro e la prevenzione delle collisioni. L’utilizzo di RobotStudio mira a ridurre significativamente i tempi di commissioning e a semplificare la fase di installazione degli impianti.
OptiFact, basato su NodeRed, è invece un software progettato per la raccolta e l’analisi dei dati provenienti dai dispositivi di campo, come robot, PLC e sensori.
OptiFact raccoglie dati dai dispositivi tramite diversi protocolli e li salva in un database locale aziendale o nel cloud del cliente. L’obiettivo è quello di monitorare le performance dei robot, lo stato operativo, gli allarmi e lo storico produttivo per identificare problematiche, che possono essere di programmazione o fisiche della macchina.
OptiFact offre un’interfaccia web con widget personalizzabili per visualizzare e analizzare i dati raccolti, permettendo ai clienti di avere un controllo sui dati di produzione e di prendere decisioni informate per migliorare l’efficienza.