La luce laser promette di rivoluzionare il sistema industriale, così come lo sta già facendo nel mondo delle comunicazioni ottiche. Quando si tratta di lavorazione laser, l’unica cosa che si trova tra i dati e la “forma” è un raggio di luce focalizzato. Eppure quella luce può fare così tanto, dall’ablazione e dalla deposizione del materiale alla perforazione, al taglio, all’unione, alla produzione di cambiamenti metallurgici e all’induzione di tensioni intrinseche nel vetro, nonché alla levigatura e pulizia delle superfici. I laser, in pratica, sono pronti per qualsiasi cosa.
I sistemi laser erano attivi e funzionanti nelle fabbriche molto prima che qualcuno parlasse di industria digitale. Con l’avvento dell’elettronica digitale, la tecnologia laser si sta dimostrando sempre di più come strumento maturo industriale per soddisfare i nuovi requisiti funzionali.
L’industria 4.0 si basa su una visione della fabbrica che mette al centro l’automazione e lo scambio di dati. Questo cambierà il modo in cui i processi laser sono ottimizzati. I processi basati su laser devono infatti diventare più intelligenti per ottenere la massima efficienza e potenza: la visualizzazione dei dati deve funzionare insieme con il sistema visivo umano per fornire un rapido accesso e una reazione rapida durante l’elaborazione, e una comprensione dei problemi in spazi di dati multi-parametrici ed eterogenici.
I dati di processo includono informazioni sulla temperatura, l’ambiente e la potenza, la registrazione su diversi milioni di immagini termiche, oltre a risultati di analisi delle immagini. L’uso di qualsiasi strumento di analisi dei dati richiede al ricercatore di adattare opportunamente questi parametri per un set di dati specifico per evitare risultati arbitrari in termini di numero di cluster di dati, dimensioni o densità.
Indice degli argomenti
La tecnologia Laser
Un laser è un dispositivo che emette un raggio di luce coerente attraverso un processo di amplificazione ottica. Esistono molti tipi di laser, inclusi quelli a gas, a fibra, i laser a stato solido, a diodi e ad eccimeri. Tutti questi tipi di laser condividono un insieme di componenti di base.
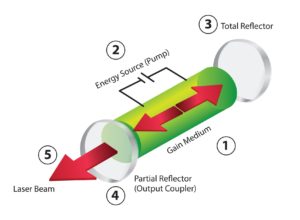
Il laser emette luce attraverso un processo basato sull’emissione stimolata di fotoni. A differenza della luce naturale di un bulbo o del sole che è di molte lunghezze d’onda diverse, la luce laser emessa è notevole per il suo alto grado di coerenza spaziale e temporale (o lunghezza d’onda), irraggiungibile usando altre tecnologie. I fasci possono essere focalizzati con una lente in punti molto piccoli, raggiungendo un’irraggiamento molto elevato (energia per area) o possono essere lanciati in un fascio di divergenza molto bassa (espansione) al fine di concentrare la loro potenza a grande distanza.
La coerenza temporale (o longitudinale) implica un’onda polarizzata a una singola frequenza la cui fase è correlata su una distanza relativamente grande (la lunghezza di coerenza) lungo il raggio. Un fascio prodotto da una sorgente di luce termica o altra incoerente ha un’ampiezza e una fase istantanee che variano in modo casuale rispetto al tempo e alla posizione, e quindi una lunghezza di coerenza molto breve.
Visualizzazione interattiva con apprendimento automatico
I sistemi laser industriali sono molto complessi sia per l’acquisizione che per l’elaborazione dei dati. I progressi tecnologici aumentano costantemente le dimensioni e la complessità dei dati di sensori, immagini e video derivanti dai suddetti processi laser industriali. E poiché i cambiamenti ambientali e l’incertezza sono intrinseci al processo, il flusso di dati non può essere controllato con metodi manuali.
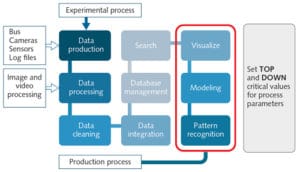
Di conseguenza, è diventato essenziale tenere traccia automaticamente dei tipi di errori e dei valori dei parametri critici che possono verificarsi durante l’elaborazione laser. Un approccio percorribile per affrontare questo problema è l’applicazione della visualizzazione interattiva combinata con algoritmi multiparametrici.
Un sistema di visualizzazione interattiva fornisce agli utenti l’interfaccia integrata necessaria per l’analisi. Gli strumenti che combinano visualizzazione e apprendimento automatico possono quindi consentire un’analisi dei dati più efficace preservando il controllo dell’utente. Di conseguenza, l’apprendimento automatico ha il potenziale per consentire ai computer di assistere l’utilizzatore nell’analisi dei parametri di processo e dei dati complessi prodotti dal processo di produzione.
L’apprendimento automatico può iniziare a comprendere rapidamente le risorse e le relazioni causali tra tutti i segnali e i parametri esistenti che influiscono sui processi laser e sui potenziali guasti. La visualizzazione interattiva e l’apprendimento automatico possono quindi creare un modello di affidabilità in grado di monitorare le prestazioni in tempo reale e identificare quando le prestazioni degli asset iniziano a discostarsi dalla norma.
Ottica laser anziché produzione meccanica
Le grandi case automobilistiche hanno progressivamente eliminato diverse fasi di lavorazioni meccaniche a valle della pressa di formatura sostituendole con stazioni laser.
Un esempio sono le portiere delle auto: i progetti attualmente utilizzati dalle case automobilistiche consentono di tagliare dai pannelli metallici pressati il maggior numero possibile di modelli diversi. Dopo tutto, non fa differenza per un laser a valle se un angolo nella porta della macchina A deve essere più piatto o se il diametro di un foro nella porta della macchina B è più grande.
Il laser riceve semplicemente le sue istruzioni sotto forma di pacchetti di dati e li mette immediatamente in pratica. Tutto ciò di cui l’ottica dello smart scanner ha bisogno sono i dati di un programma di simulazione 3D. Anche la parola “set-up” non si applica più, perché è la macchina stessa a effettuare le regolazioni necessarie per ogni parte.
Conclusioni
Combinando i dati della tecnologia relativa al laser installata su macchine diverse e controllata da un sistema di monitoraggio che include sensori per temperatura, file di registro, velocità e tanti altri, il sistema può ridurre l’esposizione al rischio, migliorare la qualità in modo collaborativo, ed eseguire analisi delle cause principali più velocemente e con maggiore precisione.