Grazie alla tecnologia e all’innovazione dei modelli di business, le aziende manifatturiere possono incrementare la produzione, aumentare la resilienza e creare organizzazioni agili.
Nel settore produttivo, l’imperativo categorico è realizzare la convergenza tra sistemi informativi aziendali (IT), ambienti di fabbrica e tecnologie operative (OT), integrando al meglio la supply chain, e sfruttando tutte le più moderne tecnologie per innovare il proprio modello di business. L’obiettivo della trasformazione digitale in ambito manifatturiero è, quindi, creare infrastrutture di produzione sempre più agili, flessibili, intelligenti, nativamente orientate al cambiamento e al miglioramento continuo, in rapporto alle variazioni di mercato e domanda.
Di questo tema, d’importanza cruciale per il futuro del comparto produttivo italiano, abbiamo parlato con Andrea Testarmata, Industry X Lead di Avanade, che lavora in azienda da oltre 22 anni e da circa sei è specializzato nell’Internet of Things (IoT), di cui segue tutti gli sviluppi e le verticalizzazioni che incidono su diversi ambiti industriali.
La continua evoluzione è il messaggio chiave sintetizzato nella locuzione “Industry X“, che si focalizza sul tema della trasformazione del settore manifatturiero guidata da dati e digitale, di fronte alle sfide epocali che ne stanno mettendo a dura prova la tenuta e resilienza. “Dopo Industry 4.0, c’è uno spazio di miglioramento continuo che vogliamo sviluppare per i clienti; attraverso un’adozione sempre più significativa, capillare ed efficace di tutte le tecnologie che si rendono via via disponibili e delle metodologie di cui siamo in possesso”.
Per fornire ai clienti esempi concreti e applicabili di come un’azienda del Manufacturing possa mettere in pratica una trasformazione guidata da dati e digitale, Avanade ha realizzato una Demo con il suo Manufacturing Hub Europeo, che consiste nella rappresentazione fisica, in miniatura, di un impianto industriale in cui viene simulato il ciclo completo di un processo produttivo.
Le soluzioni presenti nella Demo ricalcano le tre aree strategiche che secondo Andrea consentono alle aziende manifatturiere di migliorare le proprie operation.
Indice degli argomenti
Sfida numero uno: l’ottimizzazione dei processi produttivi
“Occorre anzitutto ottimizzare il modo in cui si produce”, spiega Testarmata. “Questo significa utilizzare meno energia e materiali, grazie a processi che riducono gli scarti e garantiscono visibilità e resilienza rispetto alle perturbazioni del mercato, che possono verificarsi sia a monte della catena di fornitura – in fase di approvvigionamento materiali – sia a valle, in fase di consegna dei prodotti. È poi fondamentale non solo produrre la corretta quantità di merce, ma anche consegnarla a destinazione al momento giusto, perché, ad esempio, anche una consegna anticipata può creare difficoltà di stoccaggio a chi la riceve”.
Il primo passo è quindi implementare un monitoraggio completo e costante del processo produttivo, installando dei sensori e connettervi quindi dispositivi, macchine e attrezzature di fabbrica. I dati generati possono essere elaborati da applicazioni analitiche in modalità differita per produrre report che servono, ad esempio, a misurare l’efficienza operativa dell’impianto. “Il secondo step è poi riuscire a incidere sul processo produttivo in tempo reale”, prosegue Testarmata. “Può trattarsi d’identificare un problema di safety che sta mettendo a rischio l’incolumità di un operatore, o di evidenziare tempestivamente un’anomalia qualitativa, per isolare subito il lotto di merce interessato. Quest’ultimo caso riguarda in particolare settori come quello farmaceutico o alimentare, che devono governare con particolare attenzione la tracciabilità e qualità dei prodotti”.
Casi d’uso come questi rientrano nelle applicazioni IoT “time-critical”, dove la ridotta latenza delle comunicazioni e il comportamento deterministico del sistema sono requisiti essenziali. “In tali applicazioni, Avanade può fornire soluzioni di connettività che prevedono la distribuzione di una parte dell’intelligenza elaborativa sulla rete e sugli apparati periferici, quindi sull’infrastruttura edge. È poi sempre possibile implementare una connettività verso il cloud, per eseguire la fase di training dei modelli di machine learning, che supportano l’ottimizzazione produttiva e possono quindi identificare in anticipo anomalie e malfunzionamenti di asset e infrastrutture di produzione, minimizzando i tempi di fermo non programmati dei macchinari”.
Seconda sfida: migliorare la collaborazione
Un altro elemento critico per accelerare e incrementare la competitività delle imprese manifatturiere è dotarle di strumenti adeguati a innalzare la produttività all’interno e, soprattutto, migliorare l’integrazione e la collaborazione verso l’esterno, con fornitori e partner. “Chi opera in un’azienda manifatturiera deve vivere una user experience efficace, ottenendo dati e informazioni in modo semplice, per diventare più produttivo e fare meno errori”, dice Testarmata. “Ciò determina un impatto economico positivo sull’efficienza aziendale, perché si risparmia sul numero di persone richieste per eseguire una data mansione, migliorando al contempo la qualità del lavoro svolto. Sul versante esterno, le imprese che puntano a controllare in maniera sistematica i flussi di merce, necessitano di piattaforme digitali capaci di attivare un workflow, un’interazione e una collaborazione strutturata con fornitori e partner, superando processi di comunicazione totalmente basati sulla posta elettronica. Non a caso, molti clienti ci stanno chiedendo di dotarli di portali web in grado di realizzare questo livello di comunicazione. Tale soluzione sta diventando di grande importanza strategica, anche per rilevare con immediatezza tutti gli eventi e le variazioni che possono impattare sulle tempistiche di consegna, sulla disponibilità e sull’andamento dei processi, sia a monte, sia a valle della supply chain”.
Terza sfida: innovare il modello di business
Le imprese produttive devono percepire e adottare le moderne tecnologie a disposizione per fare cose nuove e generare un’innovazione dirompente. Ne sono un esempio i cosiddetti “smart connected products“, che hanno il potenziale di ridefinire i modelli di business del mondo manifatturiero. “Anche qui esiste una roadmap da seguire” chiarisce Testarmata. “Si parte connettendo il prodotto a una piattaforma analitica per monitorarlo e comprendere come, quando e quanto viene utilizzato. Ciò consente in primo luogo all’azienda di ricavare dati d’inestimabile valore per ottimizzare di continuo l’ingegnerizzazione del prodotto stesso. In secondo luogo, l’azienda in questione ha l’opportunità di sviluppare e commercializzare una serie di servizi digitali e consulenziali che completano il prodotto fisico e ne migliorano l’utilizzo da parte del cliente. Ad esempio, è possibile implementare un servizio proattivo di assistenza tecnica che previene guasti, attivandosi per tempo e risolvendo il problema al primo intervento. In sostanza, in questo modo, l’impresa manifatturiera riesce a innovare il proprio modello di business, vende più servizi, aumenta il fatturato e, contemporaneamente, accresce il livello di fidelizzazione dei propri clienti”.
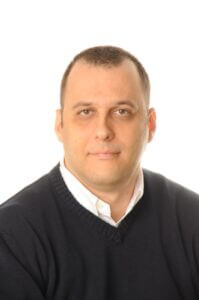
Altre opportunità d’innovazione, come in parte già accennato, risiedono nel fare leva sulla capacità computazionale disponibile nel cloud e sull’intelligenza artificiale, per la simulazione e ottimizzazione di determinati processi e scenari produttivi. È ad esempio possibile identificare, regolare e mitigare le derive che si verificano nei processi produttivi per effetto di fattori ambientali, che incidono sul deterioramento degli impianti, provocando un decadimento del livello qualitativo dei prodotti e un aumento degli scarti. “L’analisi puntuale dei dati è affidata ad algoritmi che possono migliorare di continuo e indicare le compensazioni ottimali per ridurre o addirittura annullare tali derive”.
In altri casi, le tecnologie di realtà virtuale (VR), realtà aumentata (AR) e realtà mista (MR) possono essere un Game Changer nella formazione degli operatori, che hanno il compito di eseguire controlli qualitativi o interventi di manutenzione sugli impianti. “VR, AR, MR permettono a chi si trova sul campo di avvalersi, in modalità remota, dell’ausilio di personale altamente specializzato con cui collaborare e da cui ottenere suggerimenti chiave sulle operazioni per supportare interventi manutentivi” aggiunge Testarmata.
L’innovazione che guida la sostenibilità
Quando i processi produttivi industriali usano meno energia, risorse, materiali e scartano meno prodotti, diventano automaticamente più sostenibili. “Da questo punto di vista, Avanade è in grado di supportare le aziende manifatturiere non soltanto nel miglioramento e nell’ottimizzazione, ma anche nel monitoraggio e nella valutazione del livello di sostenibilità dei processi, attraverso l’analisi e misurazione di KPI e indicatori critici, codificati anche da precise normative di settore. L’approccio di Avanade si fonda su sistemi e tecnologie che consentono di stabilire a che punto di maturazione l’impresa si trova esattamente, in termini di sostenibilità, fornendo evidenze numeriche ricavate da un elevato numero di variabili, che contribuiscono ad alimentare il modello di calcolo della sostenibilità stessa”.
La Demo Manufacturing Modernization Journey nel Centro di Innovazione Microsoft
Per fornire ai clienti esempi concreti e applicabili di come un’azienda del settore manufacturing possa mettere in pratica le soluzioni precedentemente descritte è nata la Demo Manufacturing Modernization Journey di Avanade. Come detto, questa rappresenta fisicamente, in scala ridotta, un impianto industriale in cui viene simulato il ciclo completo di un processo produttivo. Il modellino è connesso a una piattaforma analitica di monitoraggio dell’andamento della produzione, che fornisce aggiornamenti sullo stato della stessa in termini di pezzi prodotti, stock di magazzino, anomalie di funzionamento. “La Demo illustra i benefici ottenibili tramite il monitoraggio dello stato della produzione e la comunicazione bidirezionale tra piattaforma e ambiente di fabbrica, in cui macchine e robot sulla linea di produzione vengono istruiti tramite algoritmi continuamente aggiornati sulle operazioni da eseguire. È possibile monitorare anche la supply chain tramite una varietà di indicatori che fanno emergere schemi virtuosi o problematici nel ciclo di distribuzione e movimentazione dei materiali all’interno dei magazzini. Un’altra sezione della Demo mostra anche l’uso di visori a realtà mista HoloLens per supportare gli addetti a test qualitativi”.
La Demo è ospitata presso il Microsoft Technology Center di Milano e, prenotando una sessione dedicata con Avanade, l’azienda produttrice ha la possibilità di svolgere un workshop per approfondire e analizzare, con gli esperti di settore, sfide e opportunità applicative emerse. “La Demo è stata realizzata dal nostro European Manufacturing Hub di Bologna, nel quale sono accentrate competenze eterogenee, dai tradizionali consulenti, agli esperti con esperienza decennale nel settore manifatturiero, come Andrea Morselli, che ricopre il ruolo di Lead del Manufacturing Hub. Queste competenze sono particolarmente apprezzate dai clienti, che finalmente possono incontrare interlocutori in grado di parlare la loro stessa lingua, in termini di mentalità tecnica specificamente centrata sui problemi delle realtà produttive e di fornire un contributo concreto a livello di esperienze già maturate in altri progetti. Ciò facilita il dialogo e permette di rendere molto più fluido e spedito il percorso d’implementazione della soluzione“.