La fabbrica di ‘s-Hertogenbosch (Den Bosch) di Omron, nei Paesi Bassi, è oggi un eccellente esempio di innovazione di prodotto e di processo “made in Europe”. Ma solo cinque anni fa le cose non stavano così. Vediamo come questa fabbrica è riuscita a imporsi come modello di riferimento all’interno dell’organizzazione della multinazionale giapponese.
Indice degli argomenti
L’opportunità del cambiamento
Fino al 2012, la fabbrica Omron di Den Bosch fungeva da supporto a una serie di attività decise dalla Casa madre. L’attività principale riguardava la fabbricazione di prodotti progettati in Cina e Giappone per il mercato europeo. Il team di Den Bosch aveva la possibilità di apportare modifiche e migliorie ai prodotti. Il sito, inoltre, avvalendosi del proprio reparto di Ricerca e sviluppo, del proprio Centro di riparazioni per l’Europa (ERC, European Repair Centre) e del proprio European Distribution Centre, ha potuto contare sempre su elevate capacità e potenzialità tecniche in loco.
Sulla base di tutte queste competenze e conoscenze, a Den Bosch hanno voluto fare di più: piuttosto che apportare il proprio contributo all’azienda attraverso l’evoluzione dei prodotti, hanno ritenuto di poter fare la vera differenza attraverso l’innovazione. I tempi inoltre erano maturi per un nuovo approccio, specialmente perché anche le dinamiche di mercato stavano cambiando. Ad esempio, i costi della manodopera in Asia, precedentemente fattore chiave per il successo nella regione, erano aumentati. Questo e altri fattori, quali i tempi e i costi di trasporto, hanno fatto sì che le fabbriche europee potessero iniziare a competere con le controparti asiatiche e l’innovazione ha rappresentato il mezzo per farlo.
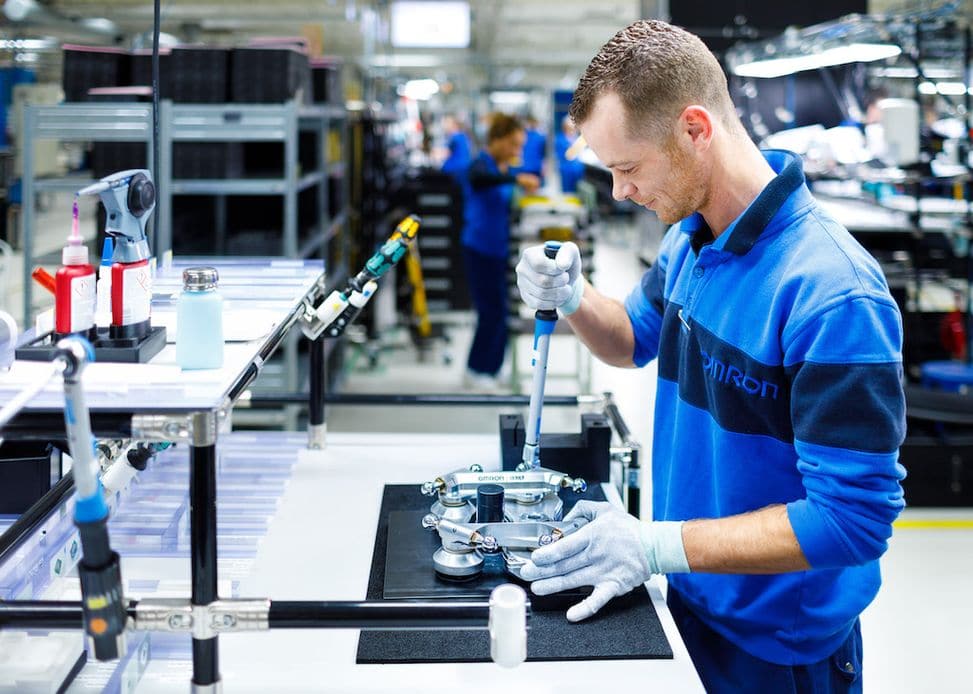
Parola chiave: innovazione
Innovazione è diventata la parola chiave a Den Bosch. L’ispirazione deriva dalla natura high-tech e particolarmente innovativa di tutta l’area produttiva di Den Bosch. La regione dei Paesi Bassi rappresenta infatti una zona calda dell’innovazione, ricca di persone talentuose.
Sotto la direzione del responsabile della catena produttiva e distributiva in Europa e nel Nord America, Paul Sollewijn Gelpke, è stata introdotta una nuova linfa vitale che ha permesso l’insediamento di una nuova cultura del “guardare avanti” e l’applicazione di questo approccio filosofico.
La prima linea di attacco riguardava l’innovazione della fabbrica stessa. I processi di produzione, quindi, sono stati completamente riprogettati utilizzando la loro stessa idea di automazione – ossia sfruttando lo stesso approccio di Omron nei confronti dei suoi clienti. Così facendo, è stato possibile creare linee di produzione automatizzate ad alta efficienza che hanno consentito una notevole riduzione dei costi di fabbricazione riducendo al minimo la manodopera manuale e automatizzando la fase di test. Più che ridurre semplicemente i costi, l’automazione ha definito nuovi parametri di riferimento in termini di prestazioni e versatilità. Inoltre, le linee di produzione sono state implementate in modo da rappresentare le basi su cui sviluppare future innovazioni.
Efficienza pienamente ripagata
La realizzazione di prodotti più convenienti ha portato rapidamente i suoi frutti. Omron ha spostato la produzione di alcuni prodotti dalle fabbriche asiatiche all’impianto di Den Bosch. Un segno questo di quanto i collegamenti con la capogruppo in Asia stessero diventando forti. La sede centrale di Omron inoltre ha voluto sostenere ulteriori sviluppi dell’impianto di Den Bosch, investendo in nuove strutture e nuovo personale che gli conferissero un’effettiva importanza globale. Oggi, l’impianto vanta 350 dipendenti e dispone di tre linee di montaggio per circuiti stampati e venti linee di assemblaggio.
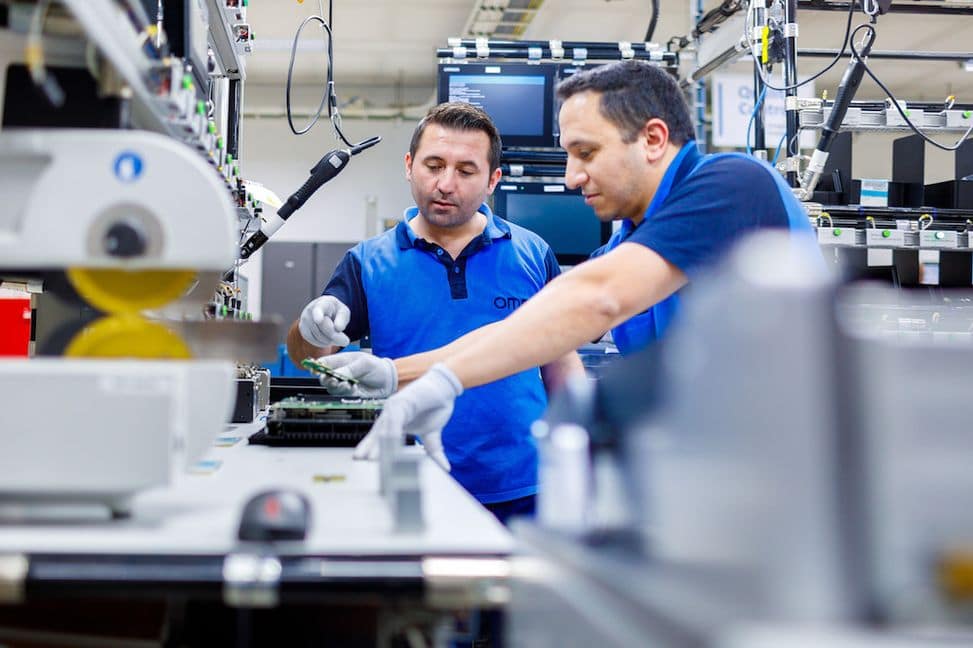
Una fabbrica locale con un obiettivo globale
Il passo successivo riguardava la realizzazione di prodotti innovativi, partendo dai PC industriali. Progettato e realizzato dal team di Den Bosch, l’IPC è stato subito un successo. È stata poi la volta di altre soluzioni innovative, tra cui le interfacce uomo-macchina (HMI) e i sensori di sicurezza. Mano a mano che crescevano le capacità dell’impianto cresceva anche la sua reputazione nella fornitura di prodotti innovativi affidabili e nella conformità con gli standard di alta qualità di Omron. Grazie alla crescente fiducia dei suoi clienti e della sede centrale dell’azienda, l’impianto di Den Bosch si è aggiudicato la gestione della nuova produzione di robotica.
Due nuove linee di robotica
L’impianto di Omron a Den Bosch ha così ottenuto il via libera per le due nuove linee di produzione, confermando l’evoluzione da impianto secondario a leader assoluto in soli cinque anni.
Le nuove linee di robotica portano anche nuove sfide. La produzione di robotica richiede la combinazione di numerosi elementi: elettronica, meccanica e l’assemblaggio di tutti questi componenti. Avvalendosi di un “approccio aperto”, l’impianto di Den Bosch riesce a combinare perfettamente e in modo estremamente facile questi elementi.
La richiesta di robot che consentano un notevole risparmio sulla manodopera è diventata sempre più elevata e realizzarli localmente ha apportato un aumento della produttività tale da soddisfare la richiesta nella regione. Tutto ciò offre ad Omron anche la possibilità di rispondere rapidamente alle richieste dei clienti con tempi di consegna più rapida. Le nuove linee producono i robot paralleli delle serie Quattro e Hornet che aggiungono funzionalità pick & place ai progetti relativi alle linee di imballaggio e assemblaggio di componenti di piccole dimensioni.
Condivisione dell’esperienza
Un ulteriore risultato del passaggio dell’impianto di Den Bosch da costruttore di prodotti esistenti a leader nell’innovazione è rappresentato dall’esperienza ottenuta durante l’intero processo. Il team ha affrontato numerose difficoltà, molte delle quali vissute anche dai clienti Omron sempre soggetti alla pressione di dover ridurre i costi di produzione e i cicli di fornitura. Avendo risolto le varie difficoltà presentatesi, il team di Den Bosch ha appreso molto e ha sviluppato una conoscenza approfondita dei problemi che possono insorgere durante le fasi di revisione dell’automazione. Questo know-how pone il team in un’eccellente posizione in quanto gli offre la possibilità di aiutare le altre aziende a migliorare i propri processi nel modo più semplice ed efficiente possibile.
A dimostrazione di quanto riportato, gli open day presso la fabbrica di Den Bosch consentono di vedere con i propri occhi quest’impianto all’avanguardia. Una delle caratteristiche principali delle nuove linee di produzione è la versatilità: possono essere adattate facilmente a prodotti diversi in modo da rendere più convenienti i cicli di produzione brevi.
Innovazione continua
Oggi, il 70% della redditività della fabbrica di Den Bosch è rappresentato da prodotti o processi nuovi. In cinque anni questa cifra è raddoppiata e l’obiettivo è di raddoppiarla ancora nei prossimi cinque anni. I nuovi processi e le innovazioni sviluppati presso l’impianto di Den Bosch vengono poi implementati nelle altre fabbriche di Omron, un risultato questo che soddisfa a pieno l’obiettivo prefissato di un continuo sviluppo di nuovi metodi al fine di garantire sempre la posizione di leader nell’innovazione.
Quattro e Hornet
Con una velocità di 300 prelievi al minuto, Quattro è il robot parallelo pick & place più veloce e flessibile al mondo. Con i suoi quattro bracci, Omron Quattro ha un’area di lavoro più ampia e una capacità di manipolazione impareggiabile. Dedicato ad applicazioni di picking e confezionamento ad alta velocità, Hornet aumenta la capacità produttiva e riduce il costo per operazione di picking. I potenti comandi integrati nella base consentono anche un ingombro ridotto del robot e costi di installazione e complessità inferiori.
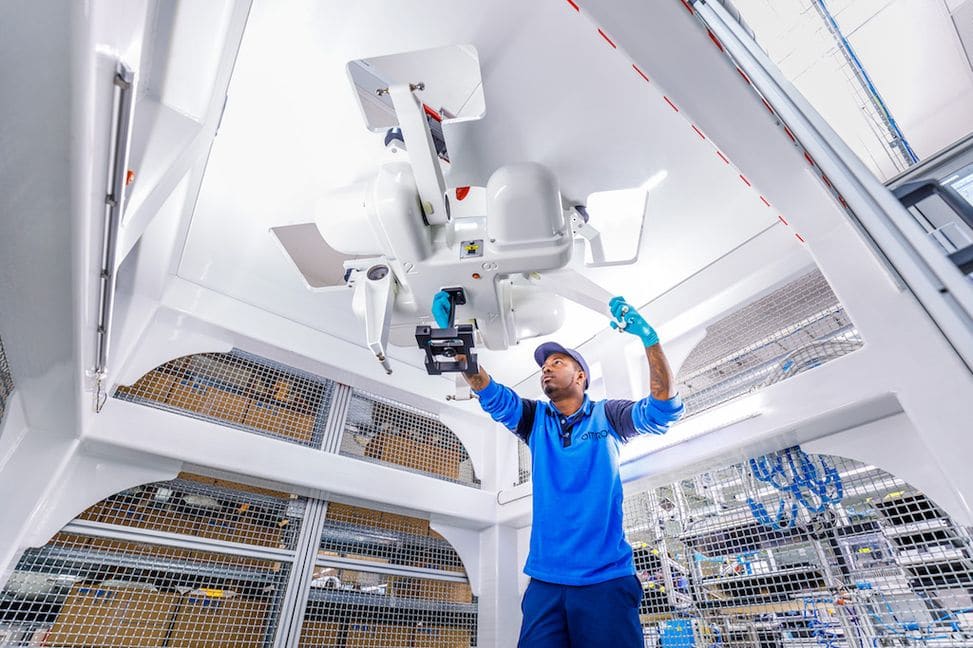