Per superare le sfide attuali, il comparto manifatturiero necessita di soluzioni integrate che permettano una visione olistica sull’intero ciclo di vita del prodotto, dalla progettazione al Field Service.
Il tema ha rappresentato il fulcro della Demo Experience organizzata dal centro di competenza MADE – Competence Center Industria 4.0 insieme ai partner Siemens, SAP e con la partecipazione di TeamViewer e Engineering.
Durante l’evento, sono stati presentati alcuni esempi virtuosi di ottimizzazione dei processi industriali (dall’engineering alla produzione all’assistenza post-vendita) grazie alle tecnologie digitali e alla loro integrazione.
Indice degli argomenti
Sviluppare progetti di innovazione con MADE
In apertura, Davide Polotto di MADE 4.0, riassume le caratteristiche del Competence Center e le opportunità per le aziende. “Siamo un partenariato – spiega – composto da 46 soggetti, che rappresentano il mondo accademico e l’industria tecnologica. I nostri servizi includono attività di orientamento con eventi divulgativi e dimostrativi, formazione, realizzazione di progetti industriali, con possibilità di iniziative finanziate”.
Nel dettaglio, MADE4.0 ha realizzato 430 eventi, 130 corsi per un totale di 1.800 partecipati, 200 progetti di innovazione, molti sovvenzionati tramite il bando che attinge direttamente dalle risorse del PNRR (Piano Nazionale di Ripresa e Resilienza).
Sono infatti a disposizione 12,5 milioni di euro per finanziare a fondo perduto progetti di ricerca industriale e sviluppo sperimentale. Qualsiasi azienda, dalle startup alle PMI alle Grandi Imprese, può accedere ai contributi. “MADE – prosegue Polotto – è il soggetto attuatore e valuta i progetti in ordine cronologico, a seconda della sottomissione della domanda. Ciascuna iniziativa deve avere una durata di 12 mesi e può ottenere un contributo massimo di 400mila euro”. Le spese rendicontabili devono essere sostenute per almeno il 70% con MADE4.0, mentre per il 30% possono riguardare acquisti di hardware e software oppure i costi del personale aziendale coinvolto.
Digital thread per la progettazione collaborativa
Nell’intervento successivo, Radu Simionescu, Senior PLM Consultant di Siemens, spiega come abilitare la progettazione collaborativa di prodotti e processi grazie al digital thread, ovvero un modello di comunicazione basato su una fonte dati univoca, che permette di connettere i silos all’interno della filiera fornendo una vista integrata su tutto il lifecycle industriale, dall’engineering alla manutenzione.
Siemens infatti sostiene una visione di Digital Twin ”a circuito chiuso” (Closed-Loop). Le copie virtuali simulano l’intero ciclo di vita del prodotto o del processo manifatturiero e vengono alimentate in real-time con le informazioni provenienti dal campo. Si crea quindi un rimando continuo tra mondo reale e digitale, con un collegamento bidirezionale tra asset fisico e gemello, all’interno di un anello.
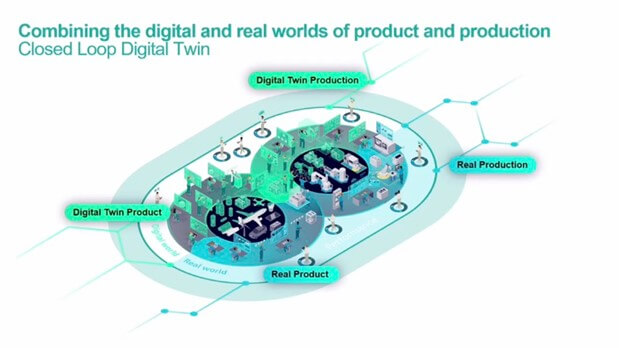
“Il Closed-Loop Digital Twin – spiega Simionescu – aumenta l’efficacia dei processi, accelera la ricerca di informazioni e migliora la qualità dei prodotti, rendendo l’organizzazione più competitiva”.
All’interno del framework, come chiarisce Simionescu, si inserisce il software PLM (Product Lifecycle Management), in particolare la piattaforma Teamcenter di Siemens, che permette di ottimizzare il digital thread e la collaborazione tra dipartimenti lungo il ciclo di vita del prodotto, dalla progettazione al Field Service. L’applicativo garantisce una gestione dei dati strutturata e univoca (le informazioni possono essere aggiornate senza creare copie), con controlli rigorosi per l’esecuzione sia degli accessi sia delle modifiche.
Le soluzioni del portafoglio Teamcenter intervengono nelle diverse fasi del product lifecycle. Ad esempio, supportano il Change Management ovvero la gestione delle modifiche di prodotto, abilitando per ogni cambiamento le procedure di verifica, la sincronizzazione delle informazioni e la tracciabilità.
In ambito Manufacturing Engineering, invece, Teamcenter permette la gestione delle distinte di produzione (mBOM – manufacturing Bill Of Materials) che derivano dalle distinte di ingegneria (eBOM – engineering Bill Of Materials) e determinano il Bill Of Process (BOP) ovvero la distinta che descrive l’approccio di produzione per il bene specifico. Qui i dettagli di processo vengono incrociati con le informazioni sugli strumenti necessari alla lavorazione e con i dati sulle caratteristiche dell’impianto, provenienti tipicamente dal software gestionale. Infine si può generare documentazione aggiuntiva contenente ulteriori istruzioni sul ciclo produttivo, ad esempio sulla distribuzione dei carichi tra le linee. Qualsiasi modifica effettuata nell’eBOM si ripercuote a valle, in modo trasparente e sequenziale.
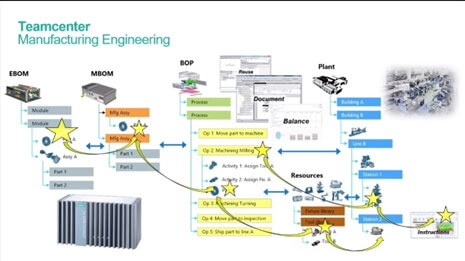
Il PLM di Siemens copre anche la fase di Service Engineering così da integrare le distinte di servizio (sBOM – service Bill Of Materials) e progettazione (eBOM), pianificare le operazioni di assistenza, fornire ai tecnici informazioni e documentazione per monitorare gli asset fisici e attuare gli interventi, tracciare le attività manutentive e i componenti in riparazione.
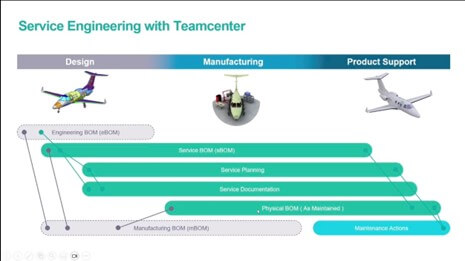
L’interoperabilità del PLM Teamcenter con il gestionale SAP è fondamentale per garantire lo scambio di informazioni lungo il product lifecycle ampliando le opportunità di ottimizzazione dei processi. Come evidenzia Simionescu, l’integrazione avviene attraverso un metadominio che neutralizza le tipologie di oggetti nei due sistemi, definendo un linguaggio comune per creare una mappatura condivisa.
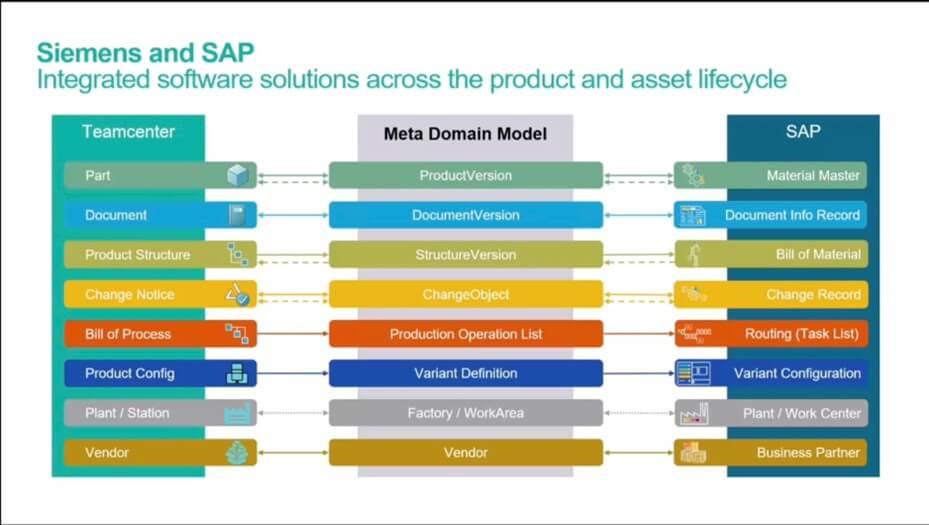
Bonfiglioli: soluzioni integrate per ottimizzare i processi
Simionescu insiste sulla necessità e i vantaggi delle soluzioni integrate portando l’attenzione su un caso di successo italiano.
Con sede nel bolognese, Bonfiglioli produce soluzioni per la trasmissione e il controllo di potenza, come motoriduttori e inverter, per una varietà di applicazioni nei settori automazione industriale, macchinari mobili e energia eolica.
La società utilizza Teamcenter per l’omologazione dei processi di sviluppo presso tutte le filiali, l’integrazione con il mondo SAP e la configurazione delle regole per la generazione delle distinte di base.
Il progetto realizzato fa leva anche sull’integrazione delle componenti Teamcenter con le soluzioni di realtà aumentata (AR) e Mixed Reality (MR) incluse nella piattaforma Frontline di Teamviewer.
Teamcenter permette la definizione della distinta di produzione dei cicli, con arricchimento grafico e testuale. Il contenuto è quindi trasferito lato TeamViewer. Le informazioni vengono ulteriormente arricchite nel client Spatial Editor, infine l’esperienza AR / MR viene caricata sul server Command Center e da qui messa a disposizione dell’operatore in fabbrica.
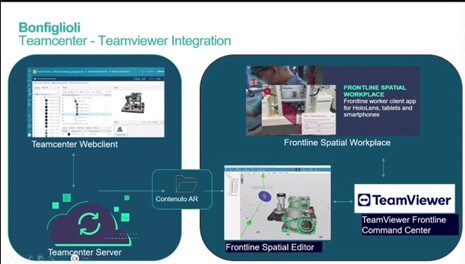
Cogliere le opportunità del Service in evoluzione
Con l’intervento successivo a cura di Piero Basso, Senior Solution Advisor di SAP Italia, si affronta il tema dell’evoluzione del Service.
“Come rivelavano gli analisti Idc, Accenture e Gartner – esordisce Basso – la manutenzione si sta evolvendo sulla spinta di alcuni fattori: la migrazione in cloud e gli applicativi SaaS, l’intelligenza artificiale, i dispositivi mobile e così via. Sull’onda della digitalizzazione, cambia anche il concetto dell’asset da manutenere: oggi alla vendita dello strumento si associa direttamente anche il contratto di assistenza”.
Mentre prima veniva gestita con personale interno, adesso la manutenzione diventa un servizio affidato a terze parti. Tali fornitori hanno la necessità di ottimizzare le risorse e le tempistiche per erogare le attività di maintenance presso i clienti.
SAP propone pertanto un sistema integrato di soluzioni per il Service Management, che permette di gestire in continuità la componente di assistenza clienti, Service Operations e interventi sul campo. Le tecnologie coinvolte sono i servizi cloud del vendor tedesco, il gestionale S/4HANA e la piattaforma Field Service Management. A completamento del quadro, l’applicazione SAP Asset Performance Management permette di gestire centralmente tutti i dati e le funzionalità necessarie alla manutenzione, monitorando e ottimizzando lo stato di salute e le performance di tutte le risorse, con possibilità di analisi predittive.
Basso entra nel dettaglio della soluzione Field Service Management, che permette di gestire l’assistenza in loco con il supporto dell’intelligenza artificiale. In particolare, mostra l’utilizzo del software nell’ambito del processo di planning & dispatching. Ricevuta la segnalazione di guasto e la richiesta di intervento, la pianificazione può essere attuata in tre modalità: manuale (l’addetto sceglie il tecnico che reputa ottimale e programma l’operazione in autonomia, utilizzando l’interfaccia click and point dell’applicazione); assistita (il sistema suggerisce potenziali candidati e schedulazioni); automatica (grazie all’AI, il software pianifica direttamente il task secondo logiche di ottimizzazione, attingendo informazioni anche da fonti esterne). Nell’ultimo caso, gli algoritmi di intelligenza artificiale permettono ad esempio di selezionare il tecnico in base alle competenze richieste, alla disponibilità, alla distanza geografica dal luogo dell’intervento e alle condizioni del traffico in tempo reale.
L’integrazione di SAP Field Service Management con le soluzioni di TeamViewer permette di affinare ulteriormente la pianificazione dell’assistenza, grazie alle informazioni fornite dagli operatori sul campo, ad esempio relative alla tipologia di guasto e al luogo dell’intervento.
Assistenza remota e realtà aumentata a supporto della forza lavoro
Ad approfondire le potenzialità delle tecnologie di TeamViewer è Carlo Bertozzi, Senior Enterprise Account Executive della multinazionale tedesca.
Il portafoglio di offerta include tre piattaforme di connettività: Remote che permette l’accesso ai dispositivi e il supporto IT a distanza; Tensor che si indirizza alla fascia enterprise, garantendo la gestione remota di device e problemi tecnici su larga scala; Frontline che integra strumenti di realtà aumentata (AR) per l’assistenza sui processi industriali.
“La aziende – asserisce Bertozzi – sono chiamate ad affrontare una serie di criticità: carenza di forza lavoro e skill; aumento della complessità dei prodotti; necessità di ridurre i tempi di risoluzione dei problemi; urgenza di abbattere i costi esorbitanti dei fermo-macchina, derivanti soprattutto dalle sanzioni legali per eventuali SLA disattesi”. Per aiutare le imprese a superare le sfide, TeamViewer è impegnata nello sviluppo di soluzioni che impattano trasversalmente tutta la catena del valore, dalla progettazione del prodotto all’assistenza post-vendita. “Ovunque ci sia un lavoratore – dichiara Bertozzi – le nostre piattaforme abilitano un collegamento con un esperto, fornendo supporto a distanza nell’esecuzione delle attività”. L’assistente remoto sarà infatti in grado di visualizzare lo schermo dell’operatore oppure, nel caso di Frontline, di acquisire e fornire le informazioni necessarie attraverso visori e altri strumenti AR.
“Frontline – prosegue – è una suite che include soluzioni per la logistica, l’assemblaggio, la manutenzione e il supporto remoto. L’esperto visualizza ciò che vede l’operatore e fornisce una serie di guide, con flussi di lavoro e immagini 2D o 3D, per svolgere attività ordinarie o emergenziali”.
Tra le altre caratteristiche della piattaforma, Bertozzi cita la recente introduzione di funzionalità AI, l’integrazione nativa con gli ambienti in uso (ad esempio, Siemens Teamcenter e SAP Field Service Management) e l’interoperabilità tecnologica. TeamViewer infatti è agnostica rispetto ai dispositivi utilizzati (ad esempio, gli smart glasses o i telefonini) che quindi possono essere scelti a seconda dello scopo, in assoluta libertà.
Secondo le statistiche riportate da Bertozzi, i clienti di TeamViewer dichiarano di avere ottenuto significativi vantaggi in termini di: formazione e velocità di on-boarding dei lavoratori; insights in tempo reale e riduzione degli errori a fronte della maggiore complessità dei prodotti; accelerazione nella risoluzione dei problemi; riduzione dei downtime, con relativi rischi legali ed economici.
Business case sostenibili grazie alla continuità del dato
Il convegno si conclude con la visione di Engineering, multinazionale italiana che si presenta nella veste di ”ecosystem integrator”, con il compito di supportare i clienti nella messa a terra delle strategie digitali.
L’intervento di Fabio Raffo, EMEA Solution Strategy Director della società, si concentra sull’importanza della continuità del dato per realizzare business case sostenibili, che possono essere trasformati in progetti scalabili.
Raffo porta l’attenzione sul problema occupazionale, citando McKinsey: sebbene la Generazione Z sia disposta a lavorare nel Manufacturing, la vera criticità si presenta dopo l’assunzione, nel tenere alto il livello motivazionale. Ciò succede perché il mondo delle fabbriche è orientato alle macchine e non mette al centro l’uomo. In questo contesto, l’automazione può arginare il progressivo disinteresse, dispensando gli operai dai compiti più noiosi e ripetitivi.
Tuttavia, emerge un’ulteriore considerazione. Le nuove generazioni oggi sono meno inclini a chiedere supporto ai colleghi, mentre preferiscono risolvere problemi autonomamente, traendo informazioni dai video. Ecco perché è importante fornire ai giovani lavoratori gli strumenti con cui sono più familiari.
Come sottolinea Raffo, per la Gen Z, la sensazione di svolgere un lavoro significativo rientra tra i principali fattori che determinano l’ingresso in azienda, la permanenza e l’abbandono; conta addirittura più del compenso economico.
“Pertanto – prosegue – è importante creare un’esperienza lavorativa coinvolgente, diversa dal passato, all’insegna dell’Extended Reality (XR). Ciò include tecnologie di Virtual, Mixed e Augmented Reality, oltre a strumenti per l’assistenza remota”.
Tuttavia, spesso i progetti di “realtà estesa” falliscono per una serie di fattori: scarso commitment dei C-Level; mancanza di documenti e condivisione della conoscenza; assenza di un struttura organizzativa e di governance; nessuna visione dell’ecosistema; miopia su prospettive e finalità dell’XR; poca comprensione e motivazione della forza lavoro.
Secondo Engeenering, la formula del successo è affrontare i programmi XR con un approccio a piattaforma. La fabbrica è un ecosistema dove applicare progetti di Extended Reality, ma occorre un percorso strutturato, che includa la definizione della governance come prerequisito e parta dall’analisi dell’infrastruttura dati.
“Il percorso – approfondisce Raffo – si articola in quattro step: valutazione preliminare e selezione dello use case in ottica strategica, con reperimento delle informazioni abilitanti; definizione dei controlli e degli obiettivi con monitoraggio delle performance in corso d’opera; condivisione globale dell’esperienza all’interno dell’organizzazione; scaling dell’iniziativa su diversi impianti”.
Per garantire la sostenibilità del business case e la conversione del proof-of-concept in iniziative concrete, è fondamentale infine che il dato rimanga consistente, attraverso le diverse fasi del processo, i layer tecnologici che compongono la piattaforma XR e tutti gli impianti aziendali.
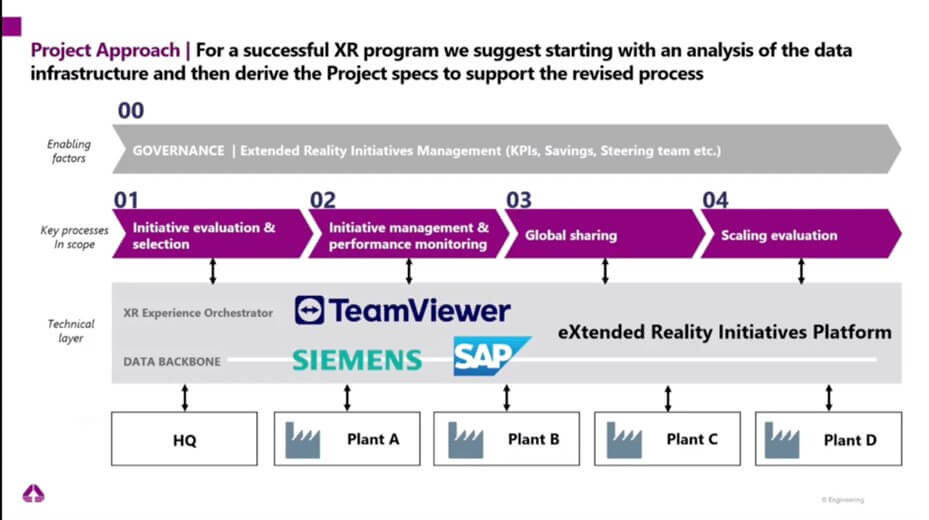