Il 28 dicembre 2021 è stato un giorno speciale per la produzione europea di batterie. Memorabile. Oltre che un giorno particolarmente green, perché la data ha segnato il primo assemblaggio di batterie agli ioni di litio a Northvolt Ett, nel nord della Svezia, il primo cioè ad essere stato progettato, sviluppato e assemblato in una gigafactory costruita da una società europea di batterie. Da allora la produzione è aumentata, e Northvolt intende raggiungere una capacità di 60 GWh all’anno per soddisfare la domanda della clientela, che già include i maggiori produttori di veicoli elettrici, come BMW, Scania, Volkswagen e Volvo.
Le consegne commerciali dallo stabilimento sono iniziate nel 2022 e non sorprende che la società stia investendo pesantemente nella produzione di ioni di litio (Li Ion), con più siti che saranno costruiti in altri paesi europei.
La densità di energia di una batteria agli ioni di litio è in genere il doppio di una batteria al nichel-cadmio standard. Vista la bassa autoscarica, attestata a meno della metà di quella delle batterie a base di nichel, e le basse esigenze di manutenzione, non è difficile capire perché la batteria ricaricabile Li-Ion è oggi la più popolare.
Mentre il mondo cerca di passare a forme più green di energia, l’elettrificazione e le fonti rinnovabili sono sempre più viste come la via da seguire. Una forma di energia molto versatile, l’elettricità può alimentare tutto, dalle case, all’industria, ai veicoli. C’è anche il numero sempre crescente di dispositivi digitali e prodotti di consumo che hanno trasformato sia la nostra vita quotidiana che il modo in cui facciamo affari. Questi richiedono il supporto di data center che sono essi stessi grandi consumatori di elettricità e hanno bisogno di una fornitura crescente e continua per supportare il mondo digitale.
Una delle principali sfide del passaggio all’elettricità sta nel suo immagazzinamento in modo efficiente e sicuro. I veicoli elettrici hanno bisogno di alte densità di energia in una massa che sia la più bassa possibile. Anche il bilanciamento dei carichi per le reti elettriche che utilizzano la generazione rinnovabile è un altro requisito vitale che richiede immagazzinamento. I prodotti di consumo hanno anche bisogno di batterie leggere e compatte, e devono garantire un lungo tempo di funzionamento, mantenendo il peso al minimo, e accettando anche un gran numero di cicli di ricarica.
Le batterie agli ioni di litio possono soddisfare queste esigenze, il che ha portato a prevedere che il settore raggiungerà oltre 135 miliardi di dollari entro il 2031, crescendo a un CAGR del 13,1% tra il 2022 e il 2031. Si prevede che la Germania da sola aumenterà la sua produzione di quindici volte fino a 164 GWh nei prossimi quattro anni e Northvolt ha in programma di costruire una gigafactory anche li.
Indice degli argomenti
Le sfide da affrontare
Il mercato delle batterie agli ioni di litio è enorme, ma per raggiungere quel potenziale i produttori di batterie devono affrontare diverse sfide di produzione: passare dalle materie prime ai prodotti finiti è un processo complesso che richiede un alto grado di precisione e ripetibilità e che le materie prime e i componenti finiti non vengano sprecati per problemi o errori.
In ogni fase, parametri come pressione e temperatura devono essere misurati con precisione per garantire la produzione secondo le specifiche. La prima fase è la produzione degli elettrodi. In questo processo viene miscelato un impasto di materiali attivi, leganti e additivi. La misurazione della temperatura è importante in questo caso poiché la miscelazione dell’impasto viene condotta a una temperatura compresa tra 20 e 40 °C.
Con l’impasto vengono quindi rivestiti entrambi i lati dei collettori di corrente. È richiesta un’elevata precisione poiché la fase di rivestimento richiede la misurazione dello spessore del film secco con una precisione del rivestimento di +/- 2 g/m2 .
La fase di rivestimento prevede il rivestimento con l’impasto di due strati di lamina metallica, in alluminio per il catodo e rame per l’anodo. Questi strati vengono quindi spostati costantemente attraverso una sezione di essiccazione per rimuovere il solvente. Le velocità dello strato durante l’essiccazione devono essere mantenute tra 35 m/min e 80 m/min, mentre la temperatura deve essere mantenuta tra 50 °C e 160 °C.
Le proprietà fisiche degli elettrodi possono essere regolate comprimendoli in un processo di calandratura. La calandratura richiede velocità dei rulli precise e il mantenimento delle temperature dei rulli comprese tra 50 °C e 250 °C.
Questo è seguito da una fase di taglio e stampaggio per portare gli elettrodi alle giuste dimensioni. Segue una fase di essiccazione sottovuoto per rimuovere l’acqua in eccesso e richiede una pressione di esercizio compresa tra 0,07 e 1000 mbar e una temperatura compresa tra 60 e 150 °C. Dopo questa fase, gli elettrodi passano in un locale di asciugatura insieme ai separatori essiccati.
L’assemblaggio effettivo delle celle comporta l’avvolgimento o l’impilamento degli elettrodi e del separatore in strati per formare una cella.
Nel processo finale, gli elettrodi e il separatore vengono sigillati nella confezione, che viene quindi riempita con elettrolita. Questa è un’altra fase delicata che richiede alta precisione, con una pressione misurata a circa 0,01 mbar. L’invecchiamento della cella può comportare una misurazione della temperatura di 50 °C per un periodo prolungato.
I complessi procedimenti e i preziosi materiali coinvolti nella produzione delle batterie agli ioni di litio implicano che i produttori devono mantenersi con precisione entro questi parametri. In questo modo, ciò eviterà di dover rottamare parti o materiali, o di perdere tempo nella produzione, ma assicurerà di poter soddisfare le crescenti richieste degli utenti di batterie, in una moltitudine di settori.
Passaggio al digitale per un’elevata precisione
Rispetto ai loro equivalenti analogici più vecchi, gli strumenti digitali possono ora fornire una precisione molto maggiore per soddisfare le impegnative esigenze dei produttori di batterie agli ioni di litio. A differenza dei dispositivi analogici, che dipendono da un segnale con un’ampiezza costantemente variabile e aperto ad interpretazioni errate o errori, gli strumenti digitali inviano un flusso di zeri e uno. Ciò significa che il valore visualizzato sarà sempre una rappresentazione accurata di ciò che sta effettivamente accadendo nel processo.
Oltre al parametro primario per la cui misurazione sono progettati, come la portata ad esempio, i dispositivi digitali possono anche inviare altri valori, come densità, pressione e temperatura.
Gli strumenti digitali sono anche facili da configurare, rendendo più semplice per le aziende aggiungere ulteriori strumenti se necessario.
Questa facilità di impostazione si ottiene attraverso l’integrazione di interfacce utente grafiche che rendono semplice l’interpretazione delle informazioni, nonché l’impostazione di procedure guidate che guidano i tecnici attraverso il processo di messa in servizio. Molti strumenti ABB, ad esempio, dispongono di un’interfaccia uomo-macchina (HMI) comune su diversi dispositivi, rendendo la formazione molto più semplice.
Un altro vantaggio degli strumenti digitali è la loro capacità di segnalare i propri malfunzionamenti o difetti. Con l’accesso ai dati sulle loro prestazioni, molti strumenti digitali possono auto-diagnosticare i propri errori e possono segnalare le loro condizioni. Spesso utilizzano protocolli di connettività come GSM o Fieldbus, consentendo ai tecnici e ai responsabili di produzione di comporre uno strumento e acquisire dati su modifiche e nuove configurazioni.
Gli strumenti digitali ABB dispongono anche di elettronica modulare, rendendo molto più facile effettuare aggiornamenti e/o sostituzioni.
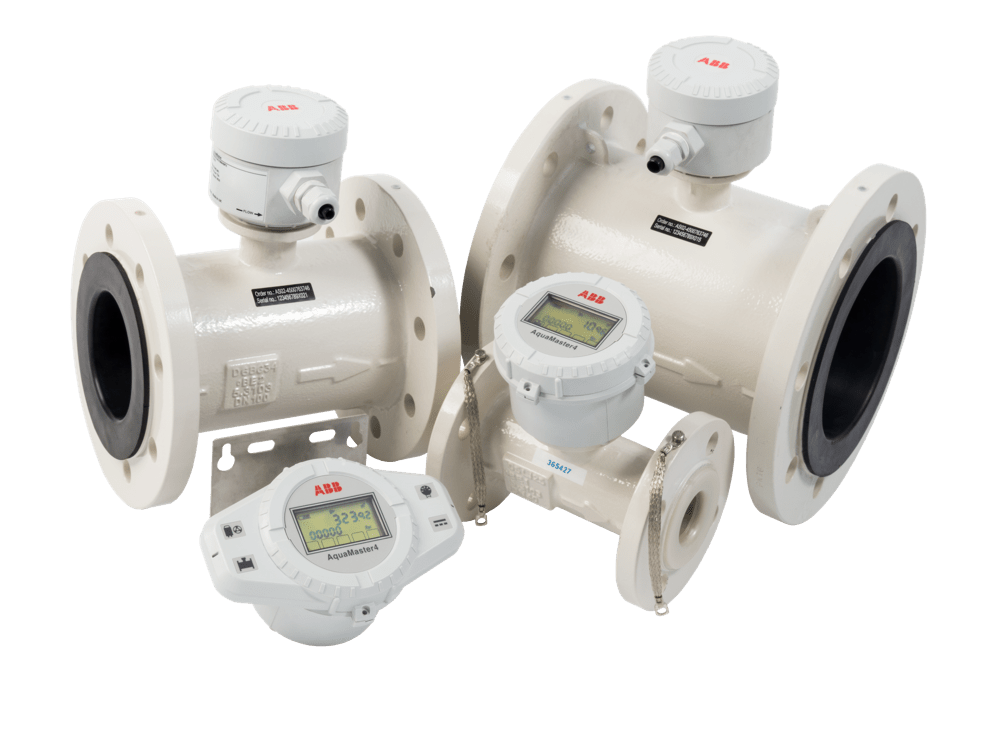