Indice degli argomenti
Recovery dell’industria italiana: il ruolo chiave della trasformazione digitale
Quali sono gli ingredienti giusti per una vera ripartenza del mondo industriale? Con quali prospettive il sistema delle imprese del manifatturiero guarda ad uno scenario futuro in cui non mancano i segnali positivi ma che certamente impone una profonda trasformazione? Che ruolo è chiamato a svolgere il software industriale in un contesto in cui la trasformazione digitale permette di cambiare prodotti, processi, modalità di relazione con i clienti e di attuare nuovi modelli di business? E’ per affrontare queste tematiche che il Gruppo Software Industriale di ANIE Automazione e SPS Italia – Messe Frankfurt Italia hanno organizzato l’evento “Trasformazione digitale. La via per il recovery dell’industria italiana” . Un incontro che si affianca alle attività previste dal Forum Software Industriale e ha focalizzato l’attenzione sui temi della digitalizzazione di fabbrica, dello smart manufacturing, della servitizzazione, della sicurezza in ambito industriale e della sostenibilità.
Digitale e sostenibilità: gli ingredienti principali del recovery industriale
Oggi più che mai, quando si parla di recovery industriale ed economica si deve parlare di trasformazione. Il digitale può svolgere un ruolo fondamentale per sostenere questa ripresa, ma occorre avere ben chiaro, come sottolinea anche un recente servizio del World Economic Forum, che non si può più parlare “solo” di digital transfomation, ma di una trasformazione più vasta e profonda che comprende e si innesta nella sustainability transformation. Una trasformazione economica oltre che tecnologica e industriale che ha il suo presupposto nella certezza che senza i dati del digitale non possiamo stabilire, realizzare e misurare percorsi di trasformazione ecologica dell’economia.
E se pensiamo alla grande sfida della sostenibilità e al ruolo determinante del digitale non possiamo non constatare che tra tutti i settori il manifatturiero è quello che più di altri può incidere su questa trasformazione. La digitalizzazione dei prodotti e delle infrastrutture, il ripensamento dei processi operativi e la trasformazione, in alcuni casi anche radicale, del rapporto tra prodotti produttori e utenti, permette di intervenire e di incidere in modo radicale a livello di ottimizzazione dell’utilizzo delle risorse, di riduzione degli sprechi e sotto il profilo della generazione di nuovo valore per le imprese e per la società. E il fenomeno della servitizzazione appare destinato a rivestire un ruolo fondamentale nel raggiungimento di questi obiettivi.
Uno scenario in miglioramento per la ripresa industriale
Nello scenario di ripresa, per il mondo della produzione si intravedono una serie di segnali positivi. Grazie all’aumento dei nuovi ordini e all’espansione della domanda a metà del secondo trimestre, diversi indicatori ci dicono che le prospettive in termini di sviluppo del manifatturiero sono molto buone. In particolare, il Purchasing Managers’ Index elaborato da IHS Markit tocca quota 62.3 punti segnando il record assoluto dal 1997, anno in cui è stato creato l’indice PMI. Uno stato di salute positivo che sarebbe molto migliore se non si sentisse il peso dei ritardi e delle criticità in tante catene di fornitura che purtroppo stanno frenando la ripresa in diversi settori. A questo contesto dobbiamo aggiungere uno scenario estremamente favorevole in termini di prospettive di investimento, soprattutto nel momento in cui si considera la trasformazione digitale sempre più strettamente connessa alla trasformazione green. E qui non si può non richiamare il Next Generation EU che porta in Europa 750 miliardi di investimenti di cui 670 per i Dispositivi di Ripresa e Resilienza RFF. Ciascun paese come sappiamo ha il compito di preparare e indirizzare i propri Piani Nazionali di Ripresa e Resilienza PNRR. Il nostro PNRR conta sulle risorse del Recovery & Resielnce Facility RFF (191 miliardi) sulla componente React EU e sul Fondo complementare italiano pari a 30 miliardi e mette a disposizione risorse per 231 miliardi di Euro che la struttura del PNRR suddivide in 6 grandi missioni.
La prima Missione Digitalizzazione, Innovazione competitività e cultura e la seconda Missione Rivoluzione Verde e Transizione ecologica sono senza dubbio le due che più possono contribuire al recovery del mondo industriale e produttivo. Si tratta di 50 miliardi di Euro destinati alla digitalizzazione in generale e 30 espressamente indirizzati alle imprese a cui si aggiungono altre voci che vanno a beneficio delle imprese stesse e che sono di competenza della Missione 4 nell’ambito del ruolo affidato ai Competence Center. Nell’ambito della Missione 2 si trovano poi le risorse destinate alla trasformazione sostenibile che ammontano a 70 Miliardi di Euro e che prevedono interventi per l’agricoltura sostenibile, per la gestione delle risorse, per la trasformazione energetica, per la ricerca e l’implementazione di progetti destinati alle fonti rinnovabili, per il ripensamento del ciclo dei rifiuti, per spingere le filiere industriali verso la trasformazione ecologica, per la mobilità sostenibile, per l’efficientamento del patrimonio immobiliare oltre che per altri ambiti tutti accomunati dalla consapevolezza del ruolo che il mondo manifatturiero può giocare a livello di trasformazione digitale e di sustainability transformation, fenomeni che possono contare anche sulle risorse che arrivano dalle politiche ESG.
Al fine di comprendere il ruolo delle imprese più impegnate sugli ambiti del software industriale nel sostenere questa doppia trasformazione è partito il confronto su due tavoli, uno dedicato alla digitalizzazione dei prodotti e delle infrastrutture e l’altro alla digitalizzazione dei processi produttivi.
Recovery industriale: il ruolo del digitale per i prodotti e per le infrastrutture
Alleantia: l’importanza di fare sperimentazione e di disporre di soluzioni plug & play
Antonio Conati Barbaro, Chief Operation Officier Alleantia
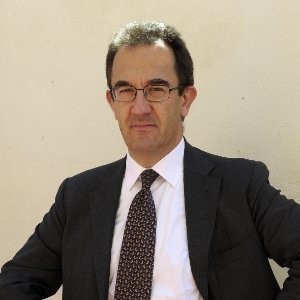
IoT, Analytics, Edge e Cloud permettono di attivare un nuovo rapporto tra prodotti o sistemi e clienti: come sta cambiando la costruzione del vantaggio competitivo nelle aziende e come state supportando questo passaggio verso la service transformation?
Alleantia è una PMI italiana riconosciuta a livello internazionale per le soluzioni software innovative applicate all’ “Industrial Internet of Things”. Da tempo lavoriamo per mettere a disposizione dati e il nostro mantra è da sempre: impara a usare i dati e capirai che ne avrai sempre più bisogno. Attraverso l’IIoT, interconnettendo tutti i tipi di macchina, si possono creare soluzioni utili per il controllo degli avanzamenti, per aumentare la flessibilità della produzione, per implementare la manutenzione predittiva e tanto altro. E tutto ciò rappresenta un valore aggiunto ma solo se si dota l’impianto della capacità di usare i dati per rendere la fabbrica più efficiente. Ognuno deve avere chiaro il piano e dove intende arrivare, mettendo così in campo le risorse necessarie per farlo. Serve relativamente poco tempo per evolvere in maniera organica in azienda, ma per gestire una trasformazione sono tante le risorse che servono.
Alleantia invita a sperimentare e adesso, occorre farlo in fretta: lato nostro la sfida non è solo creare un sistema IoT potente in fabbrica, ma una rete di applicazioni e partner pronti all’uso perché non vogliamo che il cliente spenda tempo a integrare app, vogliamo creare un ecosistema plug and play dove lavorare sulla specifica implementazione, capire come usare i dati avendo già gli strumenti pronti. In questo sens.o stiamo facendo un lavoro di grande integrazione. Ho l’IoT, ho i dati, l’applicazione li mette a disposizione e il cliente può già iniziare ad usarli, a lui resta il compito di capire come farlo bene. Possibilmente con modalità as-a-service evitando di spendere troppo tempo per progetti di integrazione.
L’implementazione del lean manufacturing è fondamentale per l’Industria 4.0?
Secondo me sono due percorsi che vanno in parallelo, l’Industria 4.0 ti mette in mano gli strumenti e ti porta in direzione del lean. È un percorso di continous prototyping. Bisogna saper usare le informazioni per cominciare a capire cosa posso fare della mia azienda, come posso cambiarla, con la consapevolezza che sono cambiamenti non solo tecnologici ma che impattano l’organizzazione per rendere in definitiva la capacità produttiva e l’industria più flessibile, più connessa e più agile.
Focalizziamo l’attenzione sulla gestione da remoto degli asset produttivi, sul mondo dei Machine builder e sui nuovi vantaggi che possono garantire ai loro clienti in termini di Servizio 4.0
Secondo me occorre accelerare i processi di innovazione, gli end-user sono andati più avanti rispetto al machine builder che si dedicato fino ad ora quasi esclusivamente alla costruzione di macchine. Per noi è fondamentale pensare alla loro nuova vita come fornitori di soluzioni digitali integrate alle macchine che non vanno solo in direzione del remote service ma anche “dell’intelligenza sopra la macchina”. Il costruttore di macchine non può rimanere indietro di fronte a nuovi modelli di business che implicano nuovi servizi a valore aggiunto.
Orchestra: IoT, Edge e Cloud Computing per attuare nuovi modelli di business
Guido Colombo, AD e Presidente Orchestra
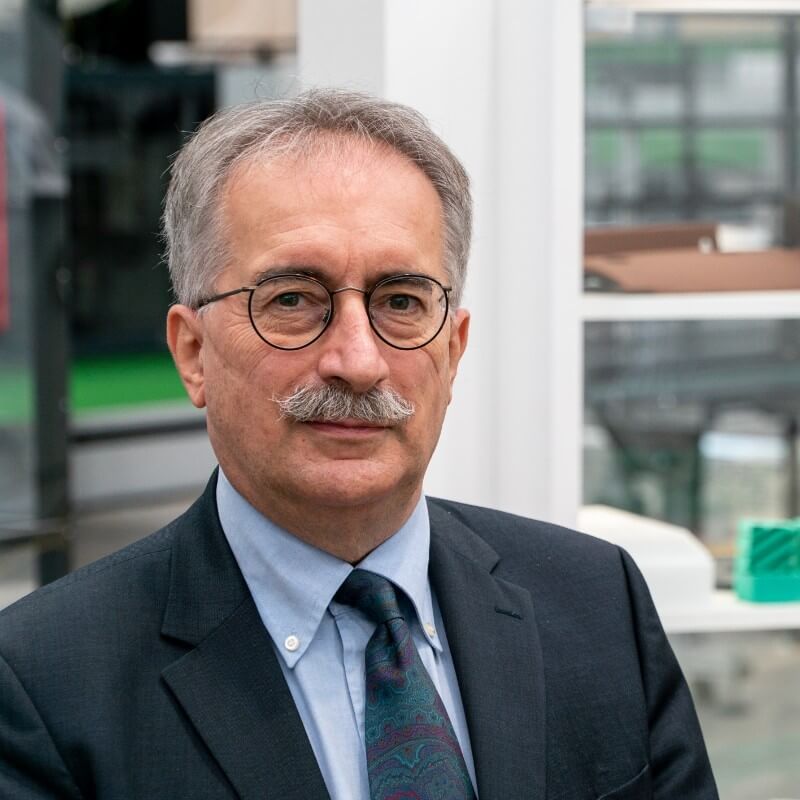
La servitizzazione è una delle prospettive sulle quali si gioca la competitività di molte imprese in particolare quella dei produttori di beni strumentali o Machine builder. Quali sono i presupposti tecnologici e le soluzioni, in termini di architetture, IoT, Edge computing, per permettere a queste imprese di sviluppare progetti di service transformation e mettere in pratica nuovi modelli di business?
Noi di Orchestra siamo nati come startup innovativa dell’I3P, l’Incubatore del Politecnico di Torino, e forniamo tecnologie e soluzioni progettate per l’Industria 4.0 sfruttando il paradigma dell’Edge Computing e del Cloud Computing. La servitizzazione è a nostro avviso il prossimo giro di boa, i competitor si stanno affacciando prepotentemente su questo nuovo modello di business in chiave pay per use, in cui i beni strumentali vengono venduti dai produttori di macchine ai manifatturieri come servizio. L’IIoT prevede che le OT siano integrate con l’ICT, due mondi che non hanno mai dialogato facilmente fino ad ora. Con il 4.0 è iniziato un percorso che fa parlare le macchine. Il problema è che ci sono macchine nuove, vecchie e anche molto vecchie. Avendo un parco così eterogeneo le imprese devono normalizzare i dati per fare in modo che la fabbrica nel suo complesso possa parlare con i sistemi, i dati devono poi essere certificati dalla fonte all’arrivo altrimenti gli analytics rimangono “monchi”, e soprattutto il dato originale deve essere consistente.
Per questo occorre lavorare sull’architettura, Orchestra ha definito la propria. L’Edge per noi è importante perché abilita la data fusion a bordo macchina. Se trasformo i dati grezzi in informazioni pronte all’uso a bordo macchina devo poi occuparmi di utilizzare le varie declinazioni del Cloud per il trasferimento dati e capire con quali Infrastrutture (in chiave IaaS) devo collaborare. Se un produttore di macchine intende procedere verso la servitizzazione deve mettere a disposizione i servizi digitali ad alto valore aggiunto, che non sono solo quelli di manutenzione. Come ad esempio servizi per verificare il buon disegno delle lavorazioni. E per questo è importante capire come si progetta nel modo corretto, come ottimizzare i tempi, come indirizzare al meglio la produzione per risparmiare ore di lavorazione. Sappiamo che non sempre queste skill sono presenti in azienda e per il machine builder c’è sempre di più la necessità di capire come viene utilizzata la propria macchina e come lavorano gli operatori che la utilizzano.
C’è uno spazio molto ampio per chi fa digitale, ma serve una visione di trasformazione, della specifica capacità di valorizzare i propri dati e una visione dei modelli di business che possono essere sperimentati in funzione del proprio posizionamento sul mercato. Considerando che il parco macchine delle imprese è molto variegato stiamo cercando di puntare sull’integrazione perché è impossibile disporre di tante piattaforme diverse per ogni produttore, al contrario bisognerà convergere su una piattaforma.
La servitization necessita di un ecosistema multidisciplinare, che vedrà convergere le eccellenze della meccanica, dell’elettronica e del digitale per progettare assieme e fornire quei nuovi servizi a valore aggiunto che faranno la differenza nella scelta dei fornitori di beni strumentali al manifatturiero. Occorre poi considerare che nessuno può fare tutto da solo e bisogna costruire una filiera di partner sincronizzati sul risultato di un’architettura solida che va dal produttore al cliente finale.
Quali altri comparti produttivi possono trarre vantaggio dalle prospettive della servitizzazione, in quali settori vedete maggiori prospettive e come li state affrontando?
La nostra esperienza si basa sul target del cliente finale, tipicamente le PMI, a cui però accediamo solo tramite i partner. Il nostro modello di business è indiretto, quindi ci occupiamo di mettere la tecnologia in campo aiutando il cliente con le prime esperienze. Il segmento delle PMI trarrà il maggior beneficio da tale modello, potendo attingere ad un panorama di servizi digitali a supporto delle proprie lavorazioni, per migliorare la propria efficienza, i propri prodotti ed essere più competitivo e resiliente sul mercato globale.
Rockwell Automation: unire l’esperienza dell’automazione con quella del digitale
Alberto Pinzello, Sales Executive, IoT & AR, Rockwell Automation
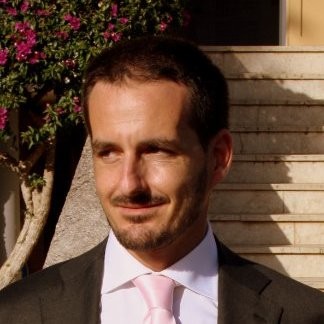
Che ruolo svolgono le infrastrutture nell’attuazione di progetti di servitizzazione e che ruolo giocano le aziende che possono accompagnare e supportare questo processo di trasformazione?
Rockwell Automation nasce dal mondo dell’automazione e dell’IT e negli anni ha sviluppato partnership strategiche per supportare tutto il digital journey. La nostra proposizione è combinare l’esperienza dell’automazione con l’esperienza digitale. Come azienda lavoriamo tantissimo con i costruttori di macchine perché sempre più il cliente finale richiede un certo servizio sul parco macchine. Da qui nasce la volontà di rispondere alle esigenze del mercato. Il machine builder può fruire delle tecnologie digitali per aumentare il proprio valore aggiunto ed è proprio questo valore che sta cambiando la visione del costruttore di macchine e del cliente finale.
Un altro aspetto fondamentale è nel fatto che ogni cliente finale ha i suoi obiettivi. Sino a qualche tempo fa il costruttore vendeva solo il macchinario senza instaurare nessun tipo di interazione con il cliente finale se non per attività e servizi di manutenzione. Ora lo scenario sta cambiando. L’Industrial Internet of Things (IIoT) ha consentito ai costruttori di macchine (OEM), con i quali Rockwell Automation ha una forte collaborazione in Italia, di sviluppare nuovi modelli di business a partire dalla servitizzazione. Oltre alla vendita del singolo macchinario, gli OEM oggi possono offrire una vasta gamma di servizi ai clienti finali al fine di aiutarli a migliorare le prestazioni operative e ridurre, ad esempio, i fermi macchina imprevisti. I costruttori di macchine aumentano del 10% la revenue, abbattono i costi del 10% monitorando proattivamente la macchine e con costi più bassi di servizio evitano le trasferte, e ottengono fino al 30% di miglioramento dell’efficienza del servizio ai clienti.
In questo contesto, trovano ampio spazio tecnologie come la Realtà Aumentata che permette un’interazione senza precedenti tra l’OEM e il cliente finale soprattutto per ciò che concerne l’assistenza in remoto: il costruttore ha infatti la possibilità di collaborare con il cliente e di guidarlo passo dopo passo, anche tramite una semplice videochiamata, nei diversi interventi da eseguire sul macchinario. Ciò permette di ridurre significativamente il tempo per la risoluzione dei problemi e di conseguenza, i costi dei servizi post-vendita.
Siamo sempre più attenti alla centralità della persona nei processi di innovazione, vediamo il ruolo delle tecnologie che ne “aumentano” le potenzialità in un rapporto nuovo con i sistemi di produzione, come le soluzioni di Augmented Reality. Qual è il vostro approccio a questo tema?
Innanzitutto, occorre sottolineare che la Augmented Reality va differenziata dalla Virtual Reality: la prima è in grado di sovrapporre un’informazione aggiuntiva digitale alla realtà arricchendola, la seconda è intesa come un ambiente totalmente immersivo che simula ambienti reali. L’Augmented Reality mette al centro le persone perché fornisce informazioni critiche, di sicurezza sull’operatività degli impianti prima disponibili solo su alcuni sistemi. L’AR migliora l’operatività, ma anche la sicurezza con le segnalazioni in real time che avvisano l’operatore di potenziali pericoli in cui potrebbe incappare. L’Augmented Reality permette un rapporto continuo tra machine builder e cliente finale che possono dialogare a distanza condividendo informazioni critiche al momento giusto e con la possibilità di operare in continuità con una forma di “vision” che mette al centro le persone.
Servitecno: il ruolo del Cloud nell’integrazione IT-OT
Mario Testino, Chief Operating Officer, Servitecno
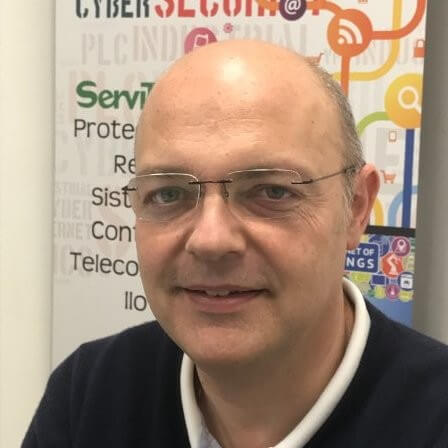
Nell’integrazione IT – OT il ruolo delle infrastrutture e il “rapporto” con il Cloud sono un fattore chiave per superare le criticità del passato e aprire a nuove prospettive. Che ruolo svolgono le architetture virtualizzate e software defined?
Servitecno è presente sul mercato da più di 40 anni con soluzioni per il controllo della produzione in ambito Operations. Recentemente siamo evoluti verso una digitalizzazione sempre più spinta che deve essere funzionale agli obiettivi dell’azienda. Ci siamo accorti che i temi della virtualizzazione e dell’infrastruttura sono sempre più importanti non sono in ambito IT ma anche nelle operations. In effetti anche il più tradizionale mondo OT sta progressivamente abbandonando i sistemi on premise per migrare verso architetture virtuali che cercano di eliminare i tradizionali problemi di gestione dell’infrastruttura raggruppando i sistemi di impianto in forma di hosting nei data center per poterli gestire in conformità con gli standard IT in uso nell’azienda.
La virtualizzazione può portare a nuove soluzioni iper-convergenti, permettendo di svincolare l’applicativo dall’infrastruttura per ottimizzare le operations IT anche nel nuovo perimetro esteso sino alla rete industriale. In questo modo si riesce a migliorare il servizio. E in questa evoluzione è ipotizzabile fare ulteriori passaggi, in forma di shift verso il cloud.
Ma talvolta «alzare» e «spostare» (lift and shift) non vuol dire risolvere: è importante capire come è possibile gestire le problematiche specifiche Operazionali (Connettività, Disponibilità e Cyber Security) nelle nuove architetture convergenti. Se facciamo riferimento al mondo OT, il discorso è infatti spesso più complesso. Alcune risorse sono facilmente virtualizzabili, ma bisogna considerare che si parla di sistemi real time, con tempi stretti, dove occorre la massima attenzione alla latenza di rete, alla disponibilità di livelli di servizio informatici e dove c’è un problema di protocolli, di monitoraggio continuo dei processi, di segmentazione critica. Ma il futuro è lì, occorre studiarlo in maniera specifica e dedicata.
Mettiamo in diretta relazione l’integrazione IT – OT e la ricerca di nuove forme di competitività e di nuovi modelli di business per il manifatturiero
La digitalizzazione non è l’obiettivo, non è la religione, ma un mezzo per raggiungere i propri obiettivi e quelli dell’industria 4.0 sono di ottimizzazione, flessibilità e competitività dell’azienda. Si tratta quindi di capire bene gli obiettivi e sulla base di questi, creare delle proprie tempistiche di raggiungimento. In questo senso c’è una grande differenza culturale. Per le PMI è importante magari la sensibilità meccanica ma fanno fatica a spendere soldi in digitalizzazione. Per questo occorre preparare il terreno affinché ci siano le condizioni giuste per la digitalizzazione.
Stormshield, cybersecurity prioritaria per il mondo manifatturiero
Davide Pala, Senior Presales Engineer, Stormshield
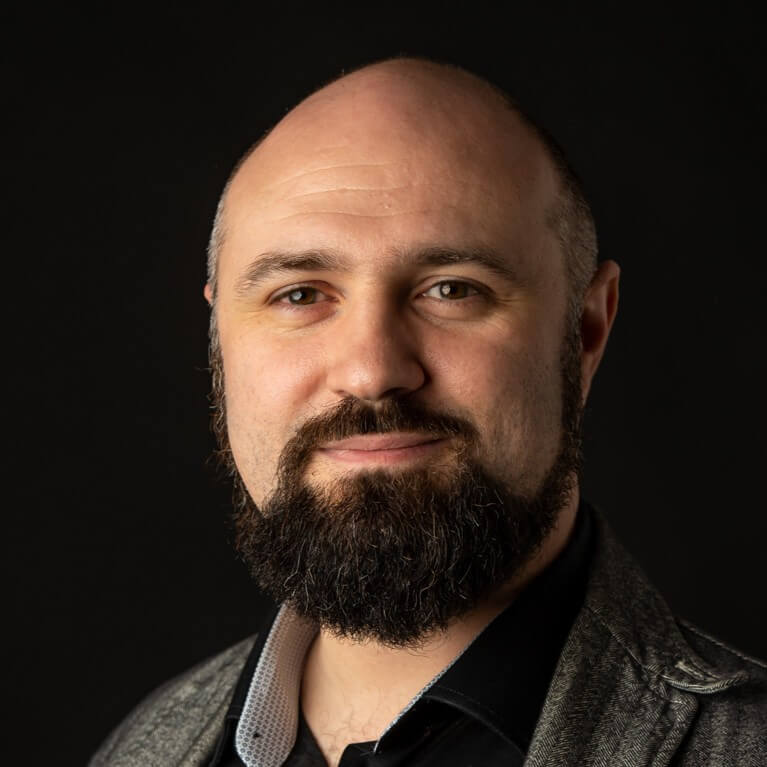
Quanto sta cambiando il peso e l’importanza della cybersecurity nell’ambito industriale e con quali strategie è necessario affrontarla?
Stormshield è un vendor che fa parte del gruppo Airbus, e opera come una divisione specifica dedicata alla cybersecurity con un focus sulla protezione delle infrastrutture critiche. Il nostro background è estremamente tecnico. Sicuramente oggi la cybersecurity sta assumendo un ruolo sempre più rilevante. Nel contesto dell’interconnessione le organizzazioni devono prendere coscienza che prima o poi saranno costrette a far fronte a problematiche di sicurezza. Quello che cambia è il perimetro, ossia la superficie esposta a entità diverse da quelle organizzative che possono interagire con gli asset aziendali, sia che si tratti di interazioni lecite o meno. Quando un’organizzazione dà in mano ad altre i propri asset, come nel caso della servitizzazione, deve tener conto che sta assumendo responsabilità molto importanti nei confronti dei propri clienti, lo stesso accade per il fornitore nei confronti dell’organizzazione.
Anche per queste ragioni dobbiamo considerare che la cybersecurity è diventata un fenomeno trasversale, amplia i propri orizzonti a tutta la supply chain e bisogna prenderne atto al di là del perimetro aziendale.
Restiamo sul tema della sicurezza associata ai nuovi modelli di business della servitizzazione in cui la sicurezza dei sistemi deve essere garantita anche ben al di fuori del perimetro aziendale.
Vivere il processo di digitalizzazione dell’impresa non deve essere visto solo come l’accodarsi a trend attuali e favorevoli all’azienda, bensì come un’importante opportunità di modernizzazione in grado di conferire all’intera organizzazione caratteristiche quali resilienza e affidabilità. Dobbiamo partire dalla consapevolezza che la servitizzazione è un’opportunità ma anche un rischio. È accaduto in passato in impianti industriali con control room bloccate da ransomware per una macchinetta del caffè connessa con il vendor. In questo senso la filosofia zero trust permette di trattare tutti gli asset aziendali come entità sulle quali non fare affidamento, garantendo l’accesso alle risorse di connessione al minimo indispensabile. Si tratta di una delle metodologie più utili in tal senso.
L’assessment in termini di piano d’azione per la sicurezza rappresenta un passaggio assolutamente importante, ma è ancora più importante comprendere che ci troviamo in situazioni come quelle del cloud dove le organizzazioni devono gestire in modo diverso le loro responsabilità. Si tende a pensare che quando l’asset sia fisicamente da altre parti, non ce se ne debba preoccupare. Per sopperire a questo problema, parlando di responsabilità e skill gap, è importante affidarsi a partner qualificati che abbiano le capacità di orchestrare le tecnologie. La collaborazione è la chiave di risoluzione del problema: ovvero disporre della conoscenza giusta e saperla condividere.
In questo processo l’approccio alla cybersecurity gioca un ruolo fondamentale in quanto porta a svolgere prima di tutto un’attenta analisi della struttura tecnologica aziendale e, di conseguenza, la possibilità di evidenziare le situazioni critiche che in qualche modo impattano sulle performance della stessa. Si tratta di un approccio consapevole e maturo che ci auguriamo possa essere preso come modello dall’intero settore manifatturiero italiano.
TeamViewer, verso una collaborazione a 360° con IoT, nuovi device e Augmented Reality
Annamaria Rossi, Account Manager Canali di vendita, IOT & AR, TeamViewer
TeamViewer, Annamaria Rossi, Account Manager Canali di vendita, IOT & AR
La nuova fase della “remotizzazione” è nel segno delle applicazioni distribuite, quali sono i vantaggi di una integrazione con IoT e nuovi device come visori per l’Augmented Reality?
Teamviewer è un’azienda di riferimento nella remotizzazione degli assets di valore e sta fornendo da anni gli strumenti software di controllo via web, nel segno delle applicazioni distribuite. Partiamo dal presupposto che una volta ricavati i dati è possibile visualizzarli su dispositivi mobili e visori di realtà aumentata. I dati possono così essere utilizzati ad esempio per disporre di informazioni predittive sul funzionamento di una macchina. Il digitale consente di fornire soluzioni di analisi e monitoraggio delle risorse di sistema e permette di esplorare e attuare modelli di business basati sull’analisi dei dati. L’avvento della pandemia ha poi accelerato i processi di remotizzazione e controllo.
Il nostro motto è “la persona al centro” e non a caso chiamiamo le macchine Machine Personsas. TeamViewer tiene in grande considerazione gli operatori attivi in fabbrica e ha raccolto feedback di operations a livello di sicurezza, salute, service reporting, costi di viaggi e interventi sulle macchine. Distribuire l’intelligenza di sistema presso ogni singolo operatore consentirà anche a chi produce e al committente finale, di ottimizzare al meglio tutte le risorse in termini di tempo e di pianificazione.
Tra le leve di innovazione più potenti per il manifatturiero c’è sicuramente la manutenzione predittiva, guardiamo ai vantaggi per il manifatturiero che sceglie di lavorare sui dati e sugli analytics dell’IoT?
TeamViewer parte da una posizione privilegiata rispetto all’IT, noi ci occupiamo da tempo di attuare la convergenza con l’OT. La disponibilità dei dati su Cloud porta a due prospettive: la manutenzione deterministica in cui si hanno dati a disposizione, li si visualizza e li si utilizza per la creazione di soluzioni come la manutenzione predittiva che elabora algoritmi statistici con regole di intervento e di intelligenza del software che decide la prossima azione.
Recovery industriale: il ruolo della digitalizzazione dei processi operativi
Engineering: il digitale al servizio della gestione delle risorse per raggiungere obiettivi di sostenibilità
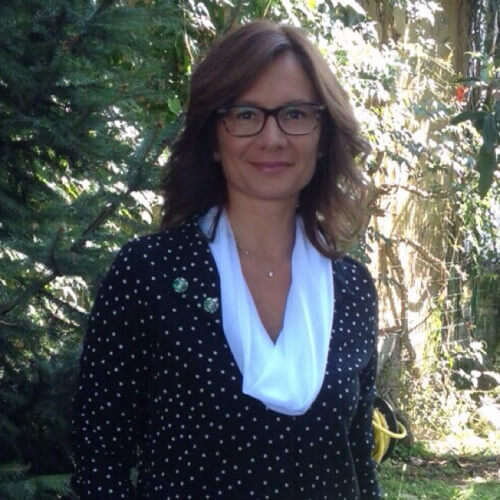
Morena Pietraccini, Expert Manager, Engineering
Per raggiungere gli obiettivi di sostenibilità tutte le imprese devono trasformare le logiche di gestione delle risorse a partire dall’energia. Che ruolo rivestono le soluzioni digitali per il monitoraggio dei consumi?
Dal punto di vista della gestione dei consumi e delle risorse, le soluzioni nate già da tempo per l’acquisizione dei dati dal processo produttivo si arricchiscono adesso grazie all’introduzione di nuove tecnologie. I nuovi dispositivi IoT consentono di acquisire queste grandezze in modo facile e veloce rispetto al passato. Il primo step è molto importante e riguarda l’individuazione dei punti su cui installare la sensoristica più adeguata per acquisire vettori che non sono solo energia, ma anche flussi come il consumo di acqua, l’aria compressa ecc. In altri termini, la prima fase per acquisire e monitorare al meglio i consumi è capire correttamente da dove prendere i dati.
Le grandezze acquisite devono poi essere rapportate al processo produttivo. I KPI si arricchiscono con i vettori di consumo e permettono di effettuare comparazioni in termini di consumi e di previsioni, permettono di individuare i processi più energivori con la possibilità di ripianificare la produzione per ottimizzare i consumi. Nella nostra esperienza come integratori, è emerso che poter comparare queste informazioni diventa importante anche sulla base del calendario produttivo, con i dati di consumo a riposo (mentre una linea era ferma consumava ad esempio tanta aria compressa e questo ha permesso di effettuare azioni di saving, ma i dati di consumi a riposo possono servire anche per la individuazione di perdite e guasti o per la creazione di sistema di monitoraggio adeguato).
Un altro passaggio importante riguarda la gestione del dato raccolto e il suo utilizzo, questo dato va rapportato con i piani di produzione e va in pasto ad un sistema di simulazione che con analisi “what if” permette di ripianificare il calendario produttivo e individuare la combinazione che consente di ottenere saving ancora maggiori. Spesso i modelli con algoritmi di machine learning possono dare indicazioni per gestire un impianto in modo diverso, con comandi puntuali da inviare ai sistemi di monitoraggio che diventano anche sistemi di controllo. Queste informazioni e questi dati possono permettere di cambiare la rappresentazione delle performance della società offrendo indicazioni anche in termini di bilancio di sostenibilità.
L’abbinata che mancava adesso c’è: IoT e 5G, vale a dire dati dal territorio (qualunque esso sia) e velocità-affidabilità di connessione, che prospettive vedete per il mondo del manifatturiero?
Prospettive estremamente interessanti. Stiamo lavorando con i provider di queste tecnologie. Poter installare nuovi dispositivi con una connettività affidabile, veloce e non invasiva nell’approccio infrastrutturale come network aziendale diventa importante. Quello che diventa possibile fare è acquisire dati attraverso un nuovo modello di connettività che non impatta sull’infrastruttura di rete che gestisce la produzione, che non ha impatti sul cliente e sulla sua infrastruttura. Un lavoro approfondito con diversi partner è utilizzare il 5G sulla remotizzazione dei controlli numerici, PLC ecc. Un ambito di ricerca per spostare su un dispositivo virtuale questi controlli e per ridurre costi di hardware, di manutenzione e di interventi.
Il Piano Nazionale di Ripresa sostiene il percorso verso la trasformazione digitale delle imprese, ponendo particolare attenzione alla trasformazione ecologica ed energetica. Il ruolo delle imprese diventa anche un ruolo sociale, orientato ad una gestione più innovativa e responsabile. L’attenzione si sposta verso gli operatori che utilizzano e applicano le tecnologie innovative e gli obiettivi riguardano non solo una maggiore produttività, ma una vita lavorativa migliore, più sicura e tutelata. La spinta è notevole e ha stimolato anche le aziende di integrazione ad una maggiore propositività. Da qui la sinergia tra produttori di tecnologie, integratori e aziende manifatturiere, per cercare di offrire soluzioni e competenze in grado di inserirsi nel contesto produttivo portando benefici sia alla qualità del prodotto che alla qualità della vita.
Oracle, il ruolo strategico delle operations
Simone Marchetti, Digital Supply Chain Sales Development Manager, Oracle
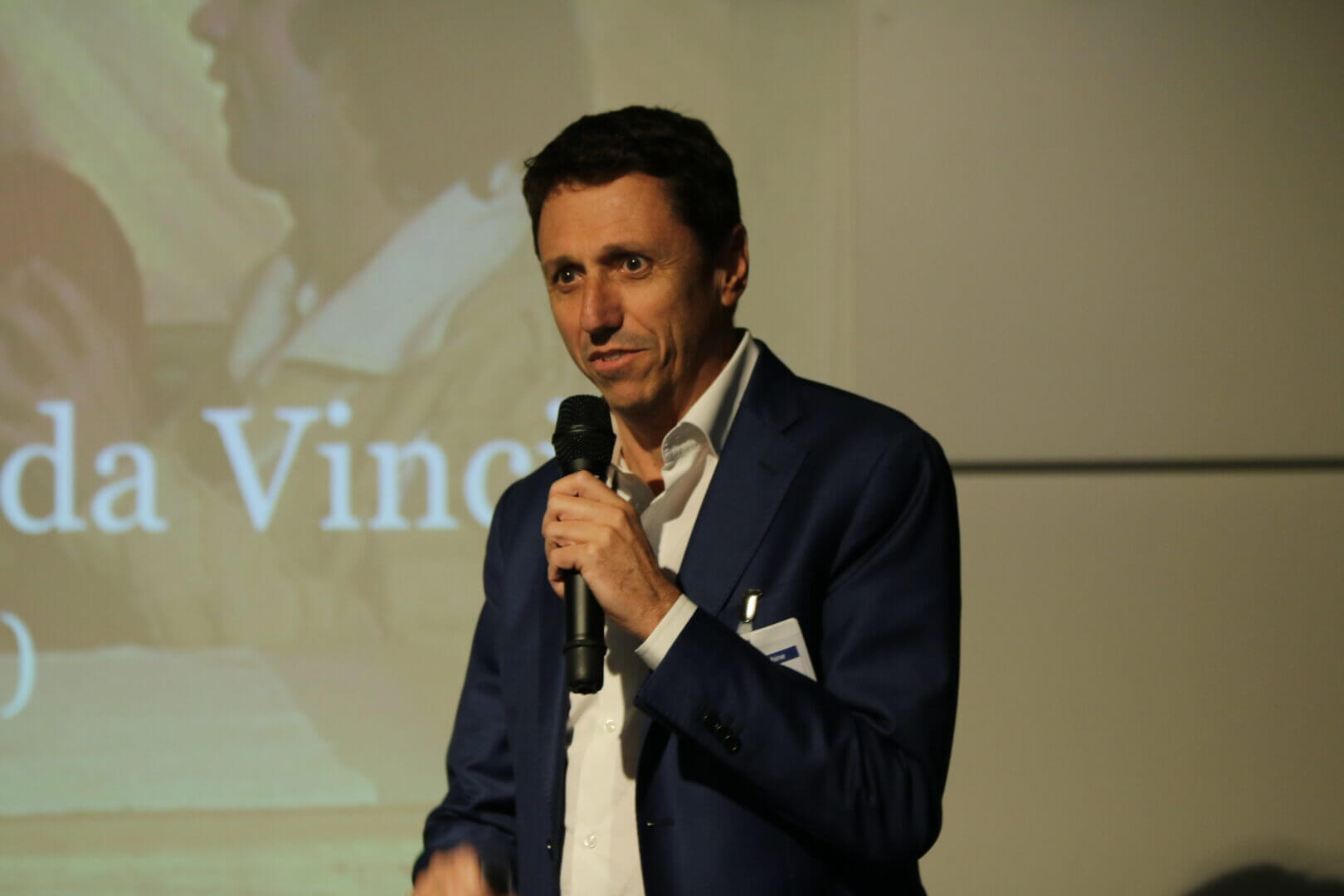
Dai nuovi modelli di business, alla garanzia di business continuity, alla resilienza e alla sostenibilità, possiamo dire che le operations sono chiamate a svolgere un ruolo sempre più strategico nel ripensamento e nell’execution della competitività aziendale?
Il 2020 è stato l’anno delle operations, ci siamo scontrati con le difficoltà emerse dalla pandemia, criticità di cui parlavamo da tempo. In questo periodo molto particolare si sono visti limiti in molte organizzazioni principalmente su 4 aree:
- nella componente di innovazione prodotto-servizio si è assistito a un forte cambiamento dei modelli di business con nuove tecnologie e player di servizi digitali che hanno portato una perturbazione importante anche a livello di customer experience;
- nella pianificazione: i modelli tipicamente adottati sono stati stravolti, un esempio importante è rappresentato dal mercato del Food che è cambiato drasticamente con l’esplosione del food delivery, con cambiamenti importanti a livello di abitudini alimentari e con il canale HoReCa che ha risentito pesantemente la penalizzazione dei consumi fuoricasa;
- a livello di execution è emersa con maggior evidenza la necessità di produrre con qualità secondo i volumi richiesti;
- e infine il tema della logistica: in questo contesto per le aziende l’obiettivo è diventato quello di soddisfare il cliente finale, chiunque esso sia, business o consumer, con puntualità, presso le imprese o le abitazioni.
In sostanza, possiamo dire che per chi opera nel settore della produzione e della logistica, gli anni che stiamo vivendo hanno segnato una forte rottura con il passato. L’affermarsi di player nativi digitali, i nuovi modelli di business, la pandemia in corso sono solo alcuni dei fattori che hanno contribuito a ridisegnare lo scenario nel suo complesso, dagli schemi di consumo alle catene del valore. In uno scenario caratterizzato da queste condizioni, l’innovazione diventa la vera chiave per la competitività. Occorre dunque recuperare produttività ed efficienza e per farlo, riconfigurare le organizzazioni ed i processi, aderire alla nuova cultura del digitale e guardare alla sostenibilità di impresa. Un ruolo fondamentale in questo senso è svolto dalle Operations che si confermano come una leva competitiva, il motore del cambiamento. Obiettivo di Oracle è garantire la capacità di sostenerle al meglio con strumenti e soluzioni in grado di abilitare le migliori decisioni di business.
La sostenibilità è qualcosa di più di una sfida, è una trasformazione economica, valoriale e culturale che sta cambiando le aziende e che ha bisogno di innovazione digitale per creare un nuovo rapporto con le risorse, con i prodotti, con i processi e con i clienti stessi. Come si devono orchestrare le tecnologie abilitanti?
Oggi la supply chain deve diventare uno strumento di competitività che genera reddito. Questo risultato si può ottenere solo se ci muoviamo su due dimensioni: l’aspetto legato alla digitalizzazione, e quindi con un allineamento delle catene del valore e mettendo “in ordine” i processi; in tutto questo occorre considerare poi la domanda e la garanzia di sostenibilità e quindi la necessità di disegnare prodotti con forme di sostenibilità by design, senza scaricare a valle della catena la necessità di ridurre la footprint. Per questo devo avere strumenti capaci di ridurre il consumo delle risorse, devo ottimizzare i passaggi eliminando l’impatto ambientale, devo partire dalle origini del processo e non pensarci solo alla fine. Dare visibilità, garantire collaboration, gestire i rischi: è fondamentale tenere tutto in considerazione fin da subito.
Schneider Electric, sostenibilità come nuovo rapporto con i sistemi di produzione

Marco Gamba, Industry Innovation and Communication Leader, Schneider Electric
Non si può essere competitivi se non si risponde alla crescente domanda di sostenibilità che arriva dai consumatori. Che ruolo può svolgere il digitale e con quali soluzioni si può costruire un nuovo rapporto con i sistemi di produzione?
Ci sono oggi condizioni che rendono questo momento unico per le imprese italiane: il Piano Transizione 4.0 incentiva lo sviluppo di progetti digitali e sostenibili e con il PNRR porta risorse su progettualità che premiano la trasformazione industriale. Per questo digitale e sostenibilità sono due temi strettamente correlati: i progetti di digitalizzazione si trasformano in spunti per rendere più sostenibile un’azienda e, al tempo stesso, i progetti di sostenibilità fanno leva sul digitale per realizzarsi appieno. La digitalizzazione è partita in concreto un po’ prima rispetto alla sostenibilità che però adesso si sta rafforzando. Ma tutto parte dai dati e dalla loro gestione: una delle conseguenze della raccolta dati e del lavoro sugli analytics in ambito industriale è la consapevolezza dell’efficienza produttiva e quindi la capacità e la scelta di utilizzare i dati per ottimizzare le performance aziendali che possono coincidere con ottimizzazione del consumo energetico e, ad esempio, con la riduzione degli scarti. E così, il progetto digitale applicato al mondo della produzione diventa anche sostenibile. Digitalizzare significa raccogliere dati, non solo da macchine e impianti nuovi, ma anche da una base installata esistente, condizione questa molto diffusa in Italia: per questo, utilizzare soluzioni ingegnerizzate per la raccolta dei dati in modo agnostico anche da macchine installate vent’anni fa, permette ad un’azienda di poter conoscere meglio il suo processo produttivo, ottimizzando consumi e risorse e avviando un percorso concreto di sostenibilità.
Oltre alla sostenibilità ambientale ed economica, c’è anche la sostenibilità sociale che ha a che fare con la sicurezza dell’operatore. L’Augmented Reality, ad esempio, aiuta nella manutenzione di macchinari e impianti mettendo a disposizione esattamente le informazioni che servono agli operatori grazie ai dispositivi mobile senza mettersi in pericolo. Se la catena si ferma perché insorge un problema, l’operatore chiama la manutenzione e la produttività inevitabilmente si riduce; al contrario la disponibilità e l’accesso rapido a procedure guidate immediate consentono all’operatore di fare proprio il paradigma del 4.0 aumentando la propria capacità di azione grazie a strumenti che aumentano la conoscenza e la sicurezza.
Per chi non parte da zero, vale a dire per la stragrande maggioranza delle imprese, che ruolo può avere il “digital retrofit” per sfruttare le opportunità della transizione 4.0?
Per tutte le realtà è sempre importante “fare i conti” con la base installata. Con gli incentivi che ci sono quando parliamo di nuove macchine e ampliamento di stabilimenti produttivi è molto importante capire anche come utilizzare macchine con qualche anno di vita lavorativa. Consideriamo che il nostro paese conta su una base installata esistente fatta di tante imprese che hanno macchinari di età differenti con tecnologie differenti di costruttori differenti. In un siffatto scenario il beneficio del digitale e l’avvio di progetti di sostenibilità deve essere alla portata anche di queste imprese. Il digital retrofit sostiene queste imprese con soluzioni pre-ingegnerizzate che raccolgono dati grezzi, li portano in dispositivi di automazione attuali che li mandano al sistema informativo di fabbrica realizzando l’interconnessione auspicata oppure, direttamente in cloud senza impattare sull’infrastruttura IT. Oggi la tecnologia permette di aggiungere dati in più a macchine datate con diversi sensori wireless che non impattano sul funzionamento ma che aumentano la conoscenza sulla macchina. È molto importante in questo contesto avere un chiaro assessment dei dati di cui si ha bisogno, e occorre avere una visione di insieme del valore del dato che si intende ottenere. E per questo serve una piena collaborazione tra tutti gli attori coinvolti.
Techsol: la spinta del Cloud e delle reti mobili
Techsol, Michele Ugatti, CEO
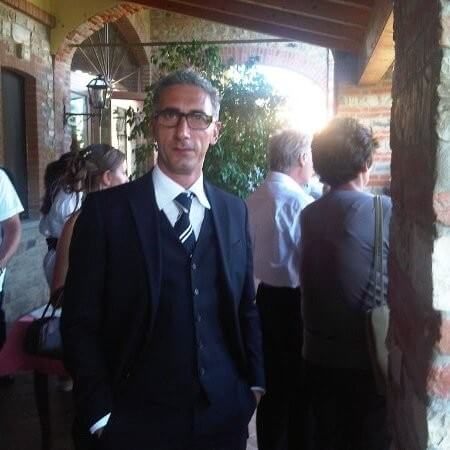
Le imprese hanno un patrimonio di dati straordinario, quale ruolo possono svolgere oggi Cloud, IoT e reti mobili per mettere questi dati al servizio del controllo della produzione e dei processi di fabbrica?
Queste tre tecnologie stanno accelerando le capability di controllo della produzione e dei processi di fabbrica. Sicuramente a partire dall’Internet of Things che permette di far transitare i dati attraverso i vari stack tecnologici. Il Cloud ci consente di abbattere i silos permettendo a tutti di accedere ad un repository centralizzato di dati. L’IoT unitamente alle app in cloud abilita la raccolta centralizzata di informazioni sottoponendole a sistemi di analisi avanzati. Inoltre, poter sottoporre queste informazioni ad un processo di analytics o machine learning permette di distribuire un’analisi intelligente su tutta la catena del valore con un monitoraggio in tempo reale a tutto vantaggio dell’efficienza. Si tratta di un ripensamento delle execution e di una leva competitiva estremamente importante per portare i sistemi di controllo produttivo anche in quelle realtà come le PMI che non hanno potuto farlo fino ad ora.
Il tema delle reti mobili è a sua volta molto importante perché concerne la possibilità di raccogliere le informazioni di quegli asset produttivi in cui è difficile cablare un’infrastruttura di rete ad alta affidabilità: anche le PMI possono adottare sistemi appannaggio di realtà strutturate, con la conseguenza che per tutte le realtà c’è la possibilità di raccogliere informazioni sugli asset costituiti da materiali voluminosi collegando in modo veloce la logistica e l’approntamento dei materiali in produzione. Servono per questo sistemi di controllo e di avanzamento produzione che devono essere strutturati per poter dare alle aziende il massimo beneficio. In questo senso l’edge rappresenterà un nodo focale di questa architettura con temi di business continuity fondamentali per sopperire ad esempio a situazioni in cui possono emergere criticità di connettività verso il cloud. Coniugando tutte queste tecnologie, molte PMI potranno adottare modelli di gestione e di efficientamento in grado di modificare la loro competitività.
Quali sono i vantaggi per le PMI che arrivano dal controllo totale sui processi produttivi in termini di “efficientamento”, di riduzione degli sprechi e di capacità di concorrere al raggiungimento di obiettivi di sostenibilità?
Ci sono delle grandi correlazioni tra gestione dei processi produttivi e sostenibilità. Il consumo energetico è il più importante, la raccolta di queste informazioni può efficientare il processo in tutto lo stack della produzione: partendo dal planning, con informazioni sui consumi energetici, ma anche sugli aspetti qualitativi che generano uno scarto fino all’execution con sistemi intelligenti che permettono di attuare soluzioni di previsioning. Ottimizzare l’uso di risorse, diminuire lo scarto ed efficientare il sistema energetico, rappresenta uno degli elementi che contribuisce alla sostenibilità ambientale. Certamente si deve andare nella direzione di una sostenibilità by design, controllando già a monte del processo quali sono i fattori che possono incidere su questo tema. Una visione di insieme tra prodotto e processo è essenziale in tal senso.
Var Group: Digitalizzazione e sostenibilità convergono e generano competitività
Fabio Massimo Marchetti, Head of Digital Industries, Var Group
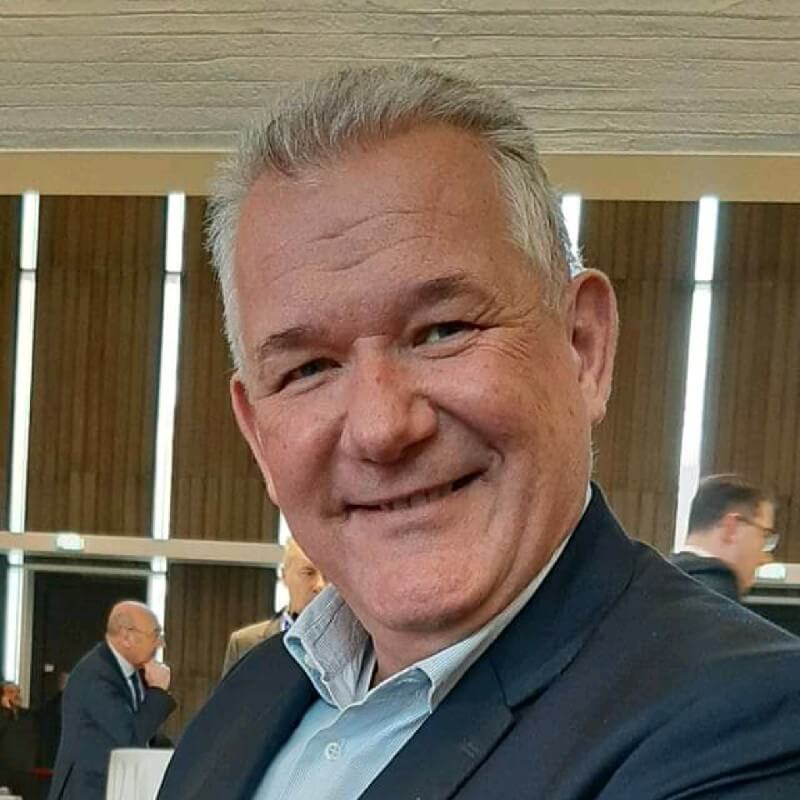
Il paradigma 4.0, o meglio ancora la digitalizzazione dei processi di produzione e delle operations, ci consegna quella conoscenza sulle risorse e sui sistemi di produzione che rendono concretamente raggiungibili obiettivi di sostenibilità un tempo impensabili. Quali sono le roadmap per le imprese per attuare questa trasformazione?
Dobbiamo partire da un dato: ad oggi solo il 14% delle aziende ha identificato nella digitalizzazione un percorso strategico. Questa situazione deve farci riflettere sul fatto che il messaggio non è ancora arrivato in maniera coerente alle imprese con tutti i benefici di sostenibilità che ne conseguono. A volte si dà per scontato che tutti ne siano consapevoli, ma evidentemente non è esattamente come speravamo. Digitalizzazione e sostenibilità convergono e dal mio punto di vista, si valorizzano reciprocamente. I temi sono diversi e vanno dalla pianificazione spesso estremamente sottovalutata anche da un punto di vista sostenibile; a una interconnessione che è non solo delle macchine, ma anche tra le aziende, tra le app, e non ultimo all’interno dell’organizzazione aziendale; e poi c’è il tema della flessibilità legata alla riconfigurazione dei processi produttivi; della ricerca di efficienza e quindi di una capacità produttiva che aumenta riducendo il consumo di risorse; e di una efficacia che permette di produrre meglio riducendo gli scarti e il consumo di energia. Sono tutti temi di una trasformazione industriale che permettono di costruire un percorso di vera convergenza in chiave di digital-sustainability.
E oggi la vera parola chiave è percorso. Un percorso per step in funzione di un approccio ben definito. La nostra convinzione è che questo percorso parte dall’assessment della maturità digitale, da cui deriva una roadmap che include sia le modalità di intervento, sia uno scouting per la sostenibilità. La nostra proposta di tools e di soluzioni permette poi di costruire una roadmap digitale. Tutto questo è ancora più importante oggi con il PNRR.
La possibilità di disporre di un ambiente interconnesso apre a tante sperimentazioni e innovazioni, come possono le imprese, anche quelle di minori dimensioni, sfruttare veramente il 4.0?
Senza interconnessione non esiste il 4.0 nel senso di paradigma, l’interconnessione crea la possibilità di abilitare la roadmap, soprattutto per le PMI. Le singole app verticali si appoggiano su questi layer e attraverso sperimentazioni si creano percorsi estremamente importanti. Oggi le aziende lavorano ancora con troppa carta. E, in generale, la gestione della produzione e la valutazione delle performance attraverso l’interconnessione consente valutazioni e analisi legate anche alla sostenibilità.
La digitalizzazione rappresenta un percorso necessario per rispondere in maniera coerente e rapida all’evoluzione del contesto complessivo in cui le aziende si troveranno sempre più ad operare. Efficienza operativa, flessibilità e particolare attenzione alla sostenibilità diventano espressione dei nuovi paradigmi 4.0 per accompagnare le imprese nell’ottimizzazione dei processi in ottica anche di rispetto ambientale. La disponibilità di tecnologie e gli incentivi rendono oggi la trasformazione digitale alla portata di tutte le aziende. Una grande opportunità per cambiare rotta, orientarsi verso un approccio strategico e avvicinarsi così ad un percorso di innovazione più efficace, ma anche e soprattutto sostenibile.
Wonderware: knowledge Management e collaboration al servizio del manifatturiero
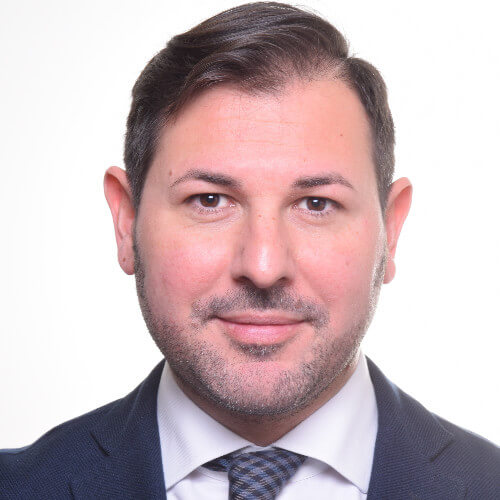
Mirko Magrini, Sales Area Manager – MES Business Developer, Wonderware
Lo Smart manufacturing non può più prescindere dall’introduzione di nuove forme di collaboration, anche per garantire business continuity e resilienza. Che opportunità e prospettive si stanno creando nel mondo operations?
Knowledge Management e condivisione delle informazioni, unitamente a sistemi MOM (Manufacturing operation management) evoluti e centralizzati, permettono oggi di convergere verso il concetto di Unified Operations Center. La collaboration è uno dei pilastri del 4.0, ma affinché possa portare valore occorre individuare i KPI che abilitano le performance più adeguate. La collaborazione oggi non è adeguatamente valorizzata, ma possiamo migliorarla e lo dobbiamo fare anche in termini di competitività. Il turn over di personale esperto influisce sulle performance di produzione e le difficoltà incontrate poi dal personale inesperto rende complesso tutto il processo di problem solving. Bisogna investire nella formazione e abilitare un’intelligenza collettiva che operi in maniera sinergica ed organica. Dobbiamo spostarci verso una gestione integrata della conoscenza tramite best practice tornando a rendere gli operatori in fabbrica protagonisti in grado di migliorare il processo.
Come sta evolvendo il manufacturing operation management e che vantaggi può portare alle imprese?
Abbiamo trovato una situazione eterogenea negli anni: nell’OT ci sono sistemi diversi che complicano le situazioni, ma dobbiamo guardare avanti cercando di razionalizzare questi strumenti e portarli ad un nuovo grado di integrazione. Si stanno affermando strumenti di gestione unificati coerenti e multi-stabilimento che raggruppano i principali KPI, portando con sé la possibilità di integrare processi contigui con logiche e know how aziendali; inoltre, in futuro, algoritmi di Machine learning potranno anticipare la previsione delle anomalie. Si tratta di progetti evoluti non alla portata di tutti e che rappresentano la nuova frontiera delle operations. Per questo serve una nuova visione nella condivisione delle competenze. E’ utile costruire un database della conoscenza di fabbrica con tool digitali che consentono di gestire on the job le nuove competenze e semplificare la comunicazione, collaborando alla soluzione dei problemi con un processo di continous improvement, creando un repository di foto e video che semplifica l’operatività e la rende anche più coinvolgente per le nuove generazioni.
Siemens, grandi quantità di dati per grandi opportunità di sviluppo
Giuseppe Biffi, Digital Portfolio Business Development Manager, Siemens
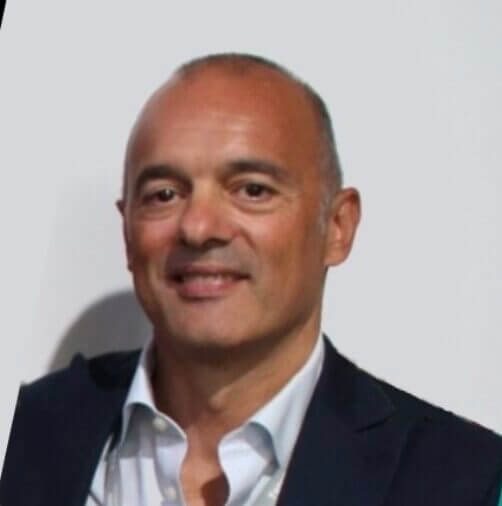
Infinite Data for Infinite Opportunities: dallo SCADA, al Cloud, all’Edge, all’A.I. l’evoluzione del data processing dalla semplice raccolta dei dati ad un full stack tecnologico
Oggi nelle aziende non manca certamente la disponibilità di dati che si creano sull’impianto produttivo come è relativamente facile accedere a molti modelli di data acquisition e data analytics per analizzarli. In passato era molto meno scontato. I dati sono infiniti però le risorse aziendali, tecnologiche e umane sono finite. Le tecnologie tradizionali hanno una loro storia di gestione dei dati a livello locale, con forme di controllo totale sul posto dei dati creati e con una flessibilità limitata che si è cercato di superare grazie al cloud. Si tratta di un modello basato su risorse scalabili che si “pagano” a consumo e che spostano l’elaborazione su una struttura esterna. Un approccio che dipende strettamente dalla connettività internet e dalla sua stabilità. Uno step evolutivo importante è rappresentato dall’Edge, una delle tre tecnologie chiave dei prossimi 5 anni insieme ad Augmented reality e Intelligenza Artificiale, una soluzione promettente e d’impatto che parte dal concetto di riportare l’elaborazione in un luogo che sia vicino alla generazione dei dati con connettività verso il cloud a garanzia della cyber security. Si sposta l’intelligenza a livello locale e si realizzano app complesse a livello di elaborazione locale. Un esempio tipico è rappresentato da app di Intelligenza artificiale che svolgono attività appannaggio di un essere umano, elaborano immense quantità di dati trasformandole in informazione di valore e condividono know how distribuendolo su più aziende dello stesso gruppo. Il discorso si fa più complesso rispetto allo SCADA del passato. Serve un ecosistema che connetta tutti i sistemi e gli applicativi e che si basa sostanzialmente sul software low code distribuendolo su tutte le piattaforme e integrando tutti i mondi.
Digitalizzazione e pandemia: in che modo questi due fenomeni globali si influenzano reciprocamente e come le imprese possono ”vaccinarsi” rispetto agli improvvisi mutamenti dei mercati e dell’economia, grazie anche alle opportunità offerta dai piani come recovery fund e Transizione 4.0?
La strategia del cambiamento e dell’aggiornamento tecnologico segue due direttrici imprescindibili per la sopravvivenza delle imprese manifatturiere. È sotto gli occhi di tutti che la pandemia ha accelerato la digital transformation e che la digital transformation può aiutare le imprese a sopravvivere in tempi di pandemia e di catastrofi globali. In questo senso la manutenzione da remoto permette di continuare a controllare l’operatività senza essere fisicamente sul posto e in maniera collaborativa. Esistono tecnologie, know how, partner affidabili e strumenti di incentivazione che consentono agli imprenditori di intraprendere un percorso di trasformazione digitale remunerativo e a basso rischio. Se immagino l’azienda come un organismo vivente, la tecnologia può essere vista come un vaccino che aiuta a proteggere l’economia intera non solo da pandemie, ma anche da catastrofi naturali, instabilità politica o commerciale e da imprevisti su scala globale. La chiave del successo della digital transformation risiede certamente nel ruolo del management aziendale, ma soprattutto nel supporto di un partner tecnologico in grado di guidare un miglioramento complessivo dell’impresa secondo una visione capace di combinare il mondo virtuale e quello reale.
Miraitek4.0: industria e servitization, un binomio possibile
Sergio Terzi, co-fondatore Miraitek4.0
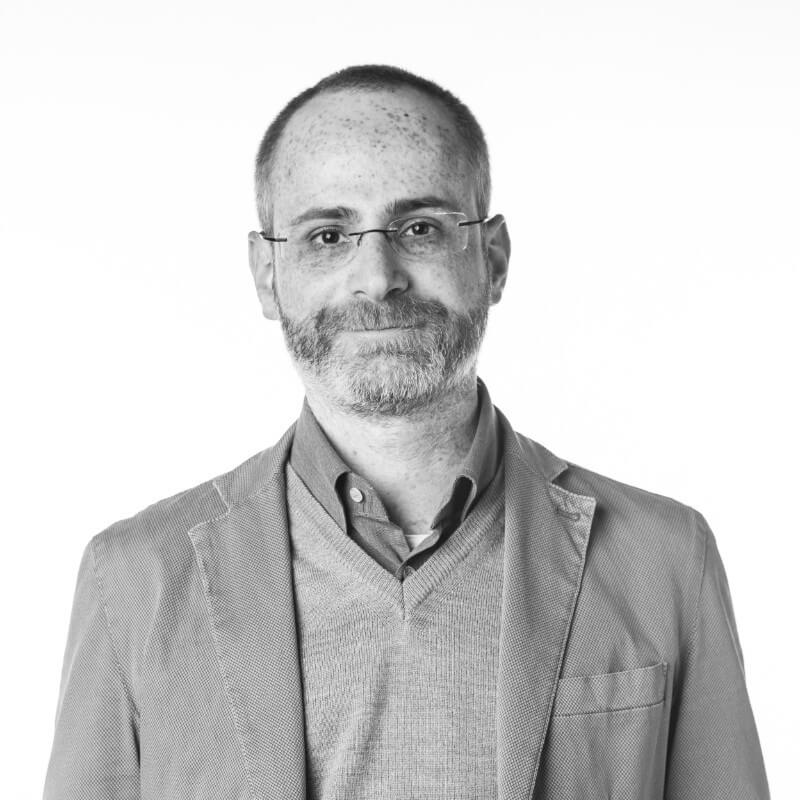
Abbiamo visto che la pandemia ha alzato il livello di attenzione verso tecnologie, soluzioni e modelli che consentono ampie forme di controllo da remoto di prodotti o sistemi di produzione. Se la priorità in molti casi è stata subito focalizzata sulla business continuity si sono poi apprezzati tanti vantaggi, che possono condurre alla servitizzazione. Come sta cambiando l’atteggiamento delle imprese verso la service transformation?
La pandemia ci ha messo di fronte a soluzioni tecnologiche che non avevamo ancora compreso. Il contesto della servitizzazione è di un altro livello ontologicamente parlando. Un modello di business che ha subito un’accelerazione negli ultimi 5 anni grazie al ruolo del digitale. Ma l’approccio, per ottenere tutti i possibili vantaggi, sta anche nella sfida e nella capacità di ripensare by design l’azienda prima di agire nel concreto.
La tecnologia è ovviamente il principale fattore abilitante, ma la servitizzazione cambia il sistema di relazioni tra fornitore e cliente, cambia il modello di business e impone un nuovo approccio alla governance dei dati. Come ci si prepara a questi scenari?
Industria e servitization, sono un binomio ormai possibile. La crisi pandemica ci ha ulteriormente spinti fuori dalla nostra zona di comfort. Lo ha fatto per i singoli e anche per le imprese. La spinta ha aiutato – e sta aiutando – le imprese a pensare in modo diverso, a porsi come attori diversi, non più fornitori di soli prodotti, ma di soluzioni capaci di risolvere problemi. E questa è una nuova prospettiva, soprattutto per i costruttori di beni durevoli. La servitization è però resa possibile da una solida digitalizzazione, per monitorare, controllare e gestire in modo integrato le soluzioni. Questo è il futuro delle imprese impiantistiche, speriamo di non dover attendere una nuova pandemia per comprenderlo del tutto!
Immagine fornita da Shutterstock