Torniamo a parlare di DIGITbrain, il progetto co-finanziato dalla Commissione europea nell’ambito della sua iniziativa I4MS (Innovation For Manufacturing SMEs), per muovere un passo avanti rispetto al digital twin tradizionale, in cui l’associazione Start 4.0, insieme ad altri cinque Digital Innovation Hubs (DIHs) europei, avrà il ruolo di agire come facilitatore del modello di business Manufacturing as a Service (MaaS), ma non solo.
Nel progetto l’associazione ha il ruolo di leader del Work Package dedicato al design e all’implementazione di tutti gli esperimenti che riceveranno supporto tecnico e finanziario (tramite Open Call aperte a terze parti) nel corso dei tre anni e mezzo del progetto. Questo anche in virtù del fatto che l’associazione incorpora la competenza tecnica di realtà che, come STAM e DGS, per citarne alcuni, in DIGITbrain capitalizzano i risultati già raggiunti con precedenti progetti europei nell’ambito I4MS, quali CloudiFacturing e le piattaforme industriali Fiware e IDS.
Cosa significa orchestrare i lavori di una fase di progetto cruciale per il testing e in un certo senso la democratizzazione delle soluzioni DIGITbrain? Naturalmente, coordinare gli altri DIHs, promuovere il raccordo tra i beneficiari degli esperimenti e i c.d. “Technical Core Partners” – tra cui l’Istituto Fraunhofer IGD per la ricerca in computer grafica e SUPSI (la Scuola Universitaria Professionale della Svizzera Italiana) per citarne alcuni – a cui è in capo lo sviluppo delle soluzioni DIGITbrain.
Ma oltre a questo fondamentale ruolo di cerniera in qualità di DIH europeo, il centro di competenza Start 4.0 scende quotidianamente nella cabina di regia per supportare da vicino gli end-user e i provider tecnologici di due dei sette esperimenti di questa prima ondata.
Indice degli argomenti
Gli esperimenti
Digital Brain for Laser-Cutting and Forming of Aluminum
L’esperimento mira a creare il digital twin delle linee di produzione di lamiere di alluminio.
L’utente finale è Gigant, Pmi manifatturiera che offre soluzioni complete e integrate per la lavorazione della lamiera. L’Independent Software Vendor (ISV) è TTS – Technology Transfer System S.r.l. sviluppatore di software per la virtualizzazione dei processi industriali, affiancato dal Value-Added Reseller (VAR) NXT control, azienda che offre soluzioni per padroneggiare la complessità dell’automazione moderna sfruttando principalmente la tecnologia di controllo IEC 61499.
Lo stato dell’arte della linea di produzione oggetto dell’esperimento (che contempla macchine laser, presse idrauliche, trasportatori, sistemi di movimentazione e robot) è rappresentato da un sistema di produzione complesso e automatizzato in cui coesistono e collaborano diverse tecnologie, vari fornitori e altrettanto differenti sistemi di controllo.
Le limitazioni relative all’attuale linea di produzione Gigant riflettono lo stato corrente della maggior parte delle PMI manifatturiere europee e possono essere così riassunte:
- incapacità di eseguire analisi “what-if” in tempo reale sulla base dei dati reali dell’impianto, che compromette fortemente la capacità di affrontare tempestivamente le esigenze e i vincoli produttivi;
- impossibilità di utilizzare il digital twin in fase di offerta/negoziazione, che ostacola la possibilità di mostrare live le configurazioni dell’impianto, portando a un potenziale di personalizzazione della macchina non adeguatamente sfruttato;
- incapacità di fornire servizi di simulazione e analisi potenziati dalle conoscenze sviluppate lungo tutto il ciclo di vita dell’impianto, che porta a ridurre produttività, efficienza e – in ultima analisi – la soddisfazione del cliente.
Per sopperire a queste limitazioni, la soluzione implementata in DIGITbrain semplificherà il flusso di lavoro per la progettazione e le simulazioni di nuovi impianti per la fabbricazione di merci a partire da lastre di alluminio, customizzati in base alle esigenze del cliente.
I layout saranno composti utilizzando moduli riutilizzabili con una semplice interfaccia drag and drop, generando un modello 3D del nuovo impianto e integrando il motore di simulazione degli eventi per stimare le prestazioni produttive. Il modello di simulazione sarà poi interfacciato con l’impianto reale attraverso la tecnologia CPSizer sviluppata da NXT. Lo strumento leggerà quindi i parametri di configurazione dall’impianto reale e verrà utilizzato per ottimizzare la pianificazione della produzione con un maggiore livello di affidabilità.
Il prodotto consentirà inoltre di esportare il modello di simulazione dell’impianto progettato e di distribuirlo in cloud nella piattaforma DIGITBrain per essere collegato all’impianto reale attraverso Fiware permettendo di leggere i parametri da uno stabilimento esistente a Verona.
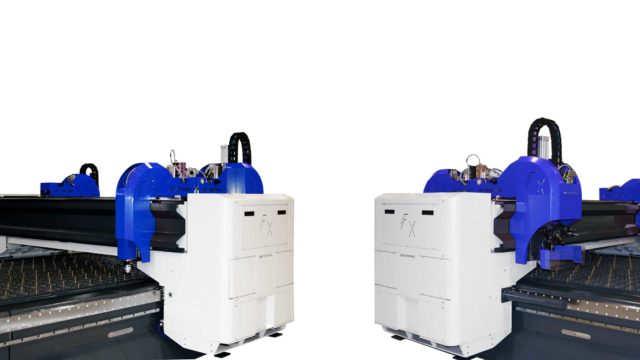
Macchina a taglio laser
Se attualmente il processo di progettazione di un nuovo layout d’impianto richiede circa 14 giorni e la collaborazione di diverse figure professionali di diversi fornitori, la soluzione sviluppata nell’esperimento ridurrà il tempo necessario a 1 giorno e richiederà una sola persona per essere eseguito. Inoltre, la produttività dell’impianto sarà stimata con un maggiore livello di accuratezza, anche grazie ai perfezionamenti dei modelli di simulazione derivati dai dati acquisiti sul campo da impianti distribuiti.
L’utilizzo del nuovo strumento ridurrà i tempi e i costi della fase di offerta con potenziali nuovi clienti e si stima aumenterà il tasso di successo delle trattative di almeno il 10%.
Inoltre, la possibilità di attuare regole decisionali e logiche di controllo in un ambiente simulato che imita fedelmente il mondo reale, migliorerà l’ottimizzazione e l’efficienza delle risorse, riducendo i tempi per acquisire tali risultati, con un impatto quantificato del “time to production” in calo del 20% (compresa la modellazione degli impianti, l’iterazione con il cliente, il ramp-up e le prime prove di produzione).
Un esperimento di “Digital Style”
Obiettivo più circoscritto quello del secondo esperimento, che mira a ottimizzare specifici parametri nella linea di produzione dei tessuti.
End-user e quindi beneficiario principale del pilota è F.lli Piacenza, PMI produttrice di tessuti di lana pregiati per il mercato del lusso. Porini è l’ISV che fornisce l’algoritmo di ottimizzazione e che eseguirà tecnicamente l’esperimento. Domina, già IT provider di Piacenza, è invece responsabile della raccolta e della fornitura dei data set.
In questo caso l’elemento sfidante è dato dal fatto che le nuove soluzioni tecnologiche devono integrarsi in una strategia produttiva basata su un controllo rigoroso della produzione. Piacenza infatti non affida all’esterno ma gestisce internamente tutte quelle fasi produttive che danno un valore aggiunto percepito dal cliente (ad esempio acquisizione materie prime, finitura, ispezione) o una flessibilità produttiva e un vantaggio in termini di costi (ad esempio la tessitura e la tintura del filato). Il tutto con una strategia competitiva focalizzata sulla massima differenziazione del prodotto.
Avendo quindi ben chiaro in mente che l’obiettivo strategico di questo particolare produttore non è quello di aumentare le quantità ma il prezzo medio, imponendo barriere di mercato basate su design, know-how, servizio personalizzato e consegna puntuale, l’obiettivo dell’esperimento è quello di creare un digital twin “potenziato” del processo produttivo che mostri tutti i parametri necessari per la sua elaborazione e analisi. Verranno utilizzati software e servizi basati sul cloud (Machine Learning, AI, Advanced Analytics) per configurare algoritmi di ottimizzazione in grado di fornire alternative e simulazioni what-if per valutare l’impatto di determinate scelte sul mix di produzione, sull’allocazione delle macchine e sul rispetto o meno dei termini di consegna (in termini di tempo, quantitativi e di qualità).
Questo ottimizzerà la pianificazione della produzione nel reparto tessitura, tenendo conto di tutti i vincoli esistenti (macchine, compatibilità degli articoli, tempi tecnici di fornitura, date di consegna al cliente). Si otterranno miglioramenti in termini di accuratezza ed efficacia di questa pianificazione, riducendo allo stesso tempo il ricorso a lotti di produzione intermedi, diminuendo lo stock di semilavorati e prodotti finiti generati in quantità superiori al necessario al fine di soddisfare i vincoli tecnici.
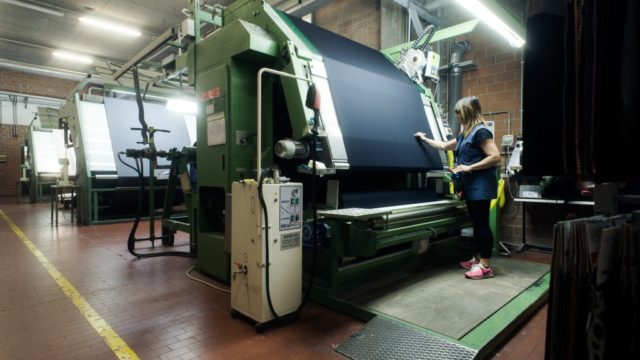
Lanificio F.lli Piacenza
Il pilota influirà inoltre direttamente sull’ottimizzazione del funzionamento dei macchinari nella tessitura dei prodotti, grazie ad algoritmi che permetteranno di sfruttare al meglio tutti i dati condivisi dagli attori della filiera, dai filati alla consegna. Si otterranno in ultima analisi suggerimenti sul raggruppamento degli ordini e sull’ottimizzazione delle dimensioni degli stessi, che si tradurranno in una riduzione dei tempi di tessitura, un aumento della lunghezza dell’ordito e una maggiore efficienza del personale grazie a una drastica riduzione delle modifiche da apportare manualmente agli articoli.
Gli esperimenti sono circa a metà del loro percorso e stanno procedendo in linea con la pianificazione iniziale, e grazie al puntuale lavoro del collega Matteo Mangini, nonostante qualche difficoltà di avvio dovuta all’introduzione di una filosofia e di concetti di Manifacturing as a Service particolarmente innovativi. Si è rivelato fondamentale il ruolo di guida e di coordinamenti tecnico dei technical core partners del progetto, ma anche quello di collante da parte dei vari DIHs.
Si entra ora nel vivo delle implementazioni, fase in cui il ruolo degli ISV diventa preponderante, per poi concludere la prima ondata di esperimenti con il follow-up e l’integrazione dei risultati. Quest’ultimo task vedrà la crescita della piattaforma DIGITbrain verso un vero ambiente di digital twin evoluto, un’entità intelligente che consenta di migliorare i processi produttivi e prendere decisioni informate secondo l’innovativo paradigma del Manufacturing as a Service”.
Come abbiamo visto, gli end-user appartengono a segmenti molto differenti del manifatturiero e questo rappresenta una sfida ma anche la ragion d’essere delle soluzioni DIGITbrain, che vogliono essere accessibili a tutti in maniera distribuita e senza barriere geografiche. Imperativo costante: incrementare la massa critica di utilizzatori delle soluzioni DIGITbrain.
Prossimo step: caccia a nuovi casi d’uso con la prima Open Call
Mentre gli esperimenti della prima ondata continueranno, come la maggior parte dei progetti nell’ambito di I4MS, DIGITbrain, nel suo ciclo di vita, si appresta a finanziare soggetti terzi da tutta Europa che prendano parte al progetto sviluppando piloti ad alto contenuto di innovazione, in questo caso in grado di adottare le soluzioni DIGITbrain per testare e implementare il modello di business MaaS.
Il meccanismo è quindi quello del cascade funding, un modo intelligente (trasparente e ben regolamentato ndr.) per trasferire finanziamenti dalla Commissione europea a quelle PMI, start-up e società a media capitalizzazione, che non hanno esperienza nell’applicare a grandi progetti europei d’innovazione (operazione che richiede spesso business unit dedicate). Un meccanismo che permette quindi alle Pmi di avere accesso a finanziamenti europei eliminando molte delle barriere burocratiche e massimizzando le possibilità di networking e di accesso a supporto tecnico altamente qualificato. Con questo strumento molte Pmi possono implementare e testare le innovazioni digitali per sviluppare nuovi prodotti, processi e servizi.
Come già detto in precedenza, l’apertura della prima delle due Open call che si susseguiranno nel corso di DIGITbrain è prevista per il 31 marzo 2021, data per la quale sarà messa a disposizione una piattaforma dedicata per le application online. La call resterà aperta 3 mesi per dare il tempo di presentare proposte competitive, ma i potenziali proponenti sono invitati già da ora a un confronto per la verifica preliminare dei requisiti per la partecipazione.
Il budget totale a disposizione è di 700mila euro per finanziare sette esperimenti della durata di 12 mesi ciascuno. Potranno rispondere alla “chiamata” piccoli consorzi formati da almeno un partner tecnico (fornitori di tecnologia software, società di consulenza ingegneristica, enti di ricerca) e un end-user del settore manifatturiero nella sua accezione più ampia.
Gli use case che verranno proposti da pool idealmente transnazionali, per poter essere valutati da una commissione di partner tecnici e soprattutto di valutatori indipendenti esterni, dovranno dichiarare chiaramente il loro impatto industriale per le aziende manifatturiere coinvolte, in base ai benefici attesi dall’utilizzo di servizi avanzati di ingegneria computazionale basati sulle tecnologie DIGITbrain.
Per chiarire meglio le idee ai potenziali proponenti, è in corso di calendarizzazione per le prime settimane di aprile 2021 il primo di una serie di Webinar gratuiti di affiancamento. L’evento virtuale, aperto a stakeholder di tutta Europa e moderatore da Start 4.0, offrirà una chiara panoramica del progetto, dei requisiti delle Open Call e degli use case attesi (inclusa la prospettiva del pool di aziende che stanno implementando uno degli esperimenti già finanziati nella prima ondata), per poi lasciare ampio spazio a una sessione Q&A in cui potenziali proponenti potranno contare sulla competenza tecnica di rappresentanti dei 6DIHs e dei partners tecnici di DIGITbrain.