Da qualche anno ormai, termini come “industria 4.0” e “digitalizzazione” sono entrati nel nostro vocabolario quotidiano e ne abbiamo dunque assimilato il significato in maniera più o meno contestualizzata e approfondita compatibilmente con i nostri settori di provenienza. Spesso però, tutto questo viene percepito ancora con un po’ di distanza, come se questi argomenti non ci avessero toccato o come se fossero ancora fuori dalla nostra portata. Quale percorso potrebbe fare una Pmi per entrare nella quarta rivoluzione industriale? Il retrofitting può essere una via percorribile?
Indice degli argomenti
La necessità di essere un’impresa data driven
L’adattamento al nuovo paradigma richiede spesso degli investimenti economici e un ripensamento del proprio business plan, ragion per cui precursori della digitalizzazione sono state molte grandi aziende che potevano permettersi consistenti investimenti in innovazione e molte start up che già nascevano in digitale.
Da qualche anno lo Stato ha messo in campo degli aiuti finanziari finalizzati a incentivare molte imprese del comparto produttivo ad acquistare macchinari intelligenti, spesso anche con esiti positivi. Tuttavia non è un macchinario di ultima generazione a fare di un sito produttivo una vera smart factory e talvolta, il ricorso a tali incentivi si è limitato al mero acquisto di una nuova macchina e poco più.
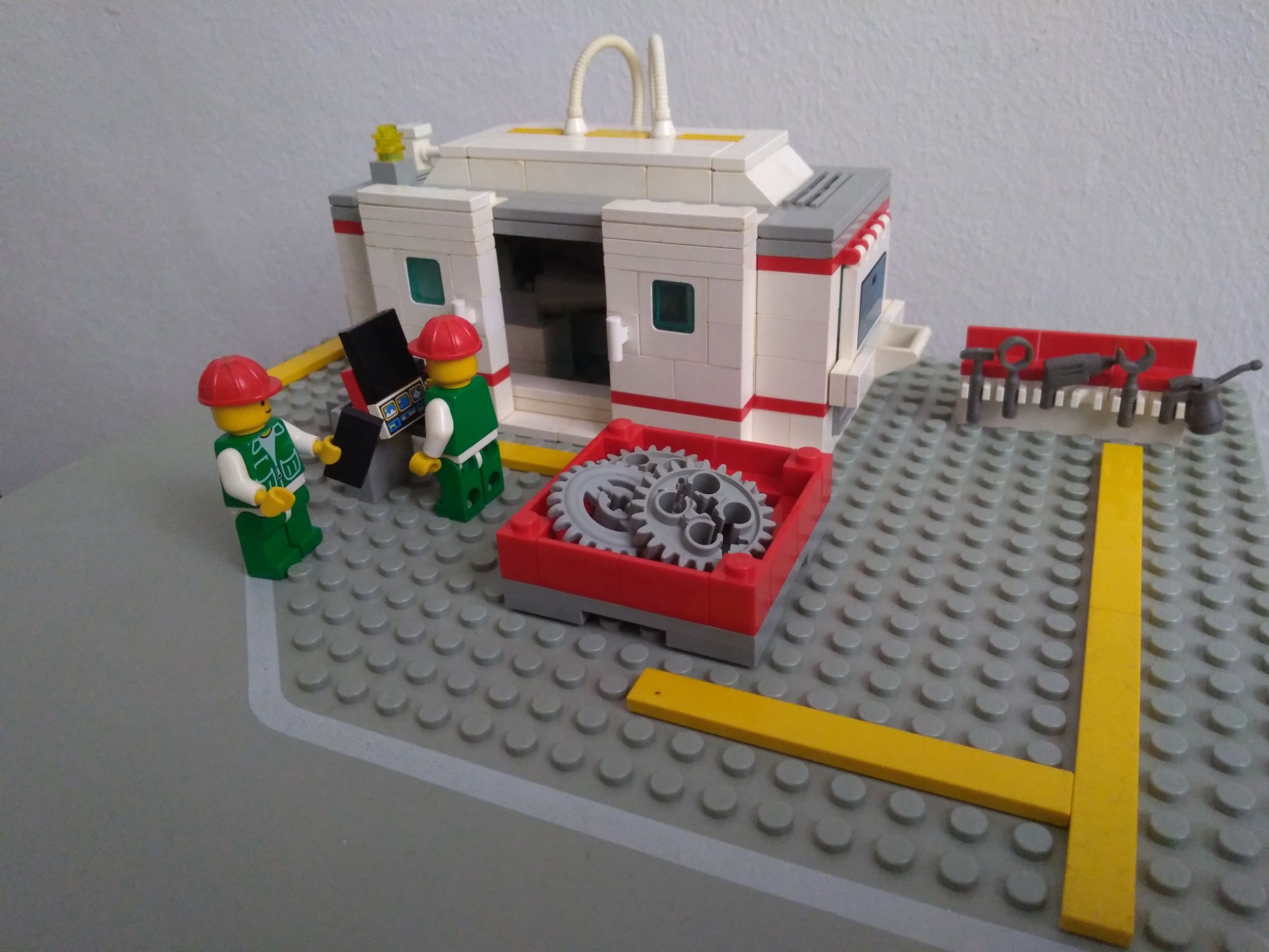
Tuttavia le macchine di nuova generazione possono dare un valore aggiunto se sono connesse tra loro e se tutti i dati che sono in grado di fornire vengono adeguatamente raccolti, processati e impiegati nelle valutazioni del caso che permettano di estrarre valore da essi (data driven).
Per fare un’analogia, se acquistassimo un macchinario moderno senza implementare un’adeguata raccolta e trattamento dei dati sarebbe come se acquistassimo uno smartphone di ultima generazione e lo usassimo solo per telefonare e inviare sms rinunciando a tutta una serie di potenzialità quali la possibilità di consultare una pagina web, di seguire delle indicazioni stradali, di acquistare con un tap un biglietto per il trasporto pubblico ecc; in tal caso non staremmo sfruttando appieno il potenziale dello smartphone e ci staremmo perdendo molti dei benefici che quel device ci può dare.
Come può una Pmi approcciare la quarta rivoluzione industriale in maniera concreta e a fronte di investimenti che siano quanto più possibile alla sua portata?
Implementazione del retrofitting
Il retrofitting è una pratica volta ad ammodernare macchinari non recentissimi in modo che possano avvicinarsi al funzionamento di sistemi più moderni, allungarne la vita utile e fornire dati sul loro funzionamento in maniera molto simile alle macchine di ultima generazione (anche detti “Industry 4.0 ready”).
Dal lato pratico, cosa comporta il retrofit di una macchina o di un impianto? Poniamo il caso di una pmi manifatturiera che voglia eseguire un intervento di retrofit su un macchinario recente ma non di ultima generazione. A seconda della sua età, esso potrebbe avere già implementato nel suo plc un sistema avanzato di raccolta dati sul funzionamento; elaborando tali dati si possono estrarre informazioni preziose su eventuali anomalie non segnalate o su danni incipienti ad alcuni dei suoi organi.
Il più delle volte questo sistema di diagnostica è ad accesso esclusivo del costruttore (OEM) che tendenzialmente preferirà custodire gelosamente le informazioni in questione a meno di non sottoscrivere un contratto di service per il monitoraggio della macchina. A questo punto si presentano tre possibili vie:
- si può pensare di sottoscrivere con l’OEM un servizio di assistenza affinché questo, monitorando costantemente la macchina da remoto, ne assicuri un funzionamento ottimale programmando prontamente eventuali interventi;
- ci si può affidare ad aziende specializzate che svolgano il lavoro del punto precedente in sostituzione dell’OEM; in tal caso bisogna accedere al “cervello” della macchina oppure realizzare un sistema parallelo di raccolta dati andando ad applicare nuovi sensori sulla macchina;
- si implementa in-house il punto sopra ricorrendo a risorse interne.
Le opzioni appena elencate richiedono sforzi diversi sia in termini di lavoro che di costo: rivolgersi al costruttore del macchinario potrebbe rivelarsi la scelta più onerosa in termini di costo ma più semplice in quanto si demanda in toto l’intervento a chi già conosce la macchina e dispone di tutti gli strumenti per mettervi mano.
Affidare a una ditta terza il compito di sensorizzare una macchina potrebbe rivelarsi più economico per la pmi presa come esempio.
Infine eseguire autonomamente il retrofit della macchina in analisi richiederebbe di possedere in casa le risorse nonché la capacità di raccogliere ed elaborare i dati che il sistema di diagnostica fornisce quindi processarli tramite software dedicati.
In linea con queste ultime due scelte risulta molto interessante la soluzione realizzata da Bosch al fine di connettere e gestire da remoto diversi macchinari tramite una semplice app il cui core è un software di tipo open source e quindi customizzabile in autonomia o comunque a fronte di una spesa potenzialmente ragionevole.
In linea di massima quindi, scegliendo una soluzione che sia un buon compromesso fra costo e complessità del lavoro, la seconda via potrebbe essere quella più alla portata di una pmi.
Questo approccio vale per macchine di recente costruzione e in una certa parte anche per macchinari più vetusti, dove si renderebbe necessario sensorizzare la macchina da capo.
Elencate le possibili scelte, una volta che la macchina “campione” sarà stata ammodernata essa sarà in grado di fornire informazioni utili sul suo funzionamento, ad esempio:
- assorbimenti anomali di corrente possono essere indice di qualche malfunzionamento di natura elettrica;
- eccessivi livelli di vibrazione (e di rumore) possono indicare usura dell’utensile o di un componente della catena cinematica della macchina con conseguenti ricadute sulla qualità dei pezzi prodotti;
- anomalie nelle temperature possono indicare strisciamento di alcuni componenti o problematiche nei sistemi di raffreddamento.
A questo punto, conoscere il regime di funzionamento della macchina permette di processare le informazioni raccolte tramite un software basato su algoritmi di intelligenza artificiale ed eseguire la manutenzione predittiva, ovvero un approccio di manutenzione che ragionando a priori permette di monitorare e anticipare un possibile guasto e quindi di pianificare al meglio gli interventi di manutenzione riducendo invece quelli di riparazione. Le conseguenze sono quindi una diminuzione delle riparazioni, una pianificazione più consapevole e mirata della manutenzione nonché una miglior qualità dei pezzi prodotti e della pianificazione della produzione nel suo insieme.
Potenzialità del retrofitting
Ma i benefici del retrofitting non si limitano solo alla manutenzione, in quanto esso non è limitato alle singole macchine ma è estendibile all’intero impianto produttivo; pertanto è possibile fare un intervento di retrofit di uno stabilimento anche implementando sistemi di logistica interna automatizzata (AGV) adattandoli al layout esistente, sistemi di catalogazione con droni o inserendo stazioni dove operano robot collaborativi (COBOT) posizionati in nodi cruciali. Questi elementi sarebbero sorgenti di informazioni sul funzionamento del ciclo produttivo in esame e potrebbero fare da guida per individuarne le criticità o i punti di forza.
Questo può anche aprire le porte all’introduzione di un digital twin dell’impianto con un notevole vantaggio in termini di flessibilità: poter simulare un cambiamento nella produzione o nel layout consente di individuare in anticipo le criticità che si potrebbero incontrare.
Si vuole far notare come queste nuove potenzialità siano ottenibili partendo dalla vecchia configurazione del layout ma implementando solo alcune innovazioni.
Un intervento di retrofit può essere un buon modo per ottenere un primo riscontro sul campo su quali benefici possono apportare le nuove logiche e tecnologie industriali, anche in vista di un eventuale intervento di più ampio respiro: eseguire il retrofit su una macchina particolarmente importante per un dato impianto può essere di aiuto a valutare meglio il peso delle nuove funzionalità ottenute, inoltre può aiutare a capire se (e quali) altri macchinari potrebbero essere sottoposti a trattamento analogo oppure sostituiti direttamente con macchinari di ultima generazione.
Retrofitting: quali attori coinvolge?
Come detto, un intervento di retrofitting non è alla portata di tutti, almeno dal punto di vista del know how necessario all’implementazione. Ad affiancare le pmi in un percorso di retrofitting si possono inserire i competence center dislocati sul territorio e le università, insieme con la funzione di integrare la ricerca con il percorso di digitalizzazione del tessuto produttivo italiano.
Inoltre anche gli istituti professionali potrebbero contribuire a formare operatori macchina preparati a “dialogare” con le logiche delle macchine di ultima generazione. Ecco che queste realtà, affiancate ad innovation manager preparati e combinate insieme, potrebbero inserirsi come quarta opzione nell’elenco iniziale riguardo la scelta di chi possa supportare una pmi nell’implementazione del retrofit, forse anche come opzione più economica.
Le conseguenze di una possibile situazione, a parere di chi scrive, non possono che essere positive dal momento che in questo modo si potrebbero ridurre le distanze fra il mondo accademico e quello produttivo, formando così risorse che una volta uscite dalle università e dagli istituti professionali avranno già la possibilità di inserirsi tramite un canale diretto in un settore fiorente del mercato del lavoro e dare già un contributo personale senza bisogno di ulteriori percorsi formativi.
Va tenuto in conto che, qualora la pmi presa ad esempio facesse parte dell’indotto di una grande azienda 4.0 (o un consorzio), l’ammodernamento dei suoi asset produttivi andrebbe a vantaggio anche della grande azienda e degli altri attori della filiera, soprattutto se anch’essi facessero uso di tecnologie 4.0 consentendo di digitalizzare non solo il singolo processo di un’azienda ma buona parte della filiera produttiva dell’indotto.
Inoltre una strategia di retrofitting non deve necessariamente partire su iniziativa delle imprese produttive interessate ad ammodernare il proprio ciclo produttivo e il proprio parco macchine. La spinta può arrivare anche dal comparto del service: infatti anche chi si occupa di manutenzione può avanzare ad un cliente la proposta di ammodernare i propri asset produttivi al fine di potersi proporre per mantenere gli impianti in efficienza se non candidarsi per eseguire il retrofit stesso. Da parte sua, l’azienda di service, a fronte di questo cambio del proprio business plan, può trarre vantaggio dal poter pianificare al meglio gli interventi di manutenzione potendo incontrare la soddisfazione dei clienti.
Anche in questo caso, partire da uno study case semplice può essere di aiuto per ottenere un piccolo successo iniziale che getti le basi per ulteriori interventi futuri nonché per tracciare la rotta di un cambiamento di più ampio respiro.
Conclusioni
È mia opinione che uno degli aspetti più interessanti della digitalizzazione sia una sorta di democraticità del potenziale che ne deriva: mentre l’introduzione del vapore prima e della robotica dopo, hanno dato grande spinta principalmente al comparto produttivo, la digitalizzazione va incontro a molti altri settori grazie a tecnologie abilitanti come l’IoT, l’intelligenza artificiale e i big data.
Inoltre c’è un altro elemento di discontinuità nel fatto che oggi la ricchezza di un’azienda non sia più legata alla mera proprietà di un generico bene (sia esso un macchinario o un software) ma dal suo uso e dal capitale umano che se ne serve; una conseguenza è anche la diffusione del concetto di open source mettendo quindi a disposizione di tutti molti strumenti e lasciando che sia la capacità dei singoli individui (o delle singole aziende) di scegliere gli strumenti giusti e usarli al meglio per estrarne valore. Tutto questo però senza prescindere dalla risorsa più diffusa: l’uomo e le sue capacità.