Il progetto DIGITbrain consentirà la customizzazione di impianti manifatturieri facilitando una produzione efficiente dal punto di vista dei costi e degli impatti ambientali, distribuita e localizzata. Questo avverrà grazie a strumenti di modellazione, simulazione, ottimizzazione, analytics e intelligenza artificiale che sfruttino risorse computazionali in edge, cloud e HPC (High Parallel Computing). Ciò consentirà di superare ed estendere il concetto di Digital Twin (gemello digitale) fornendolo di una ‘memoria’ che gli consenta di tenere traccia dell’evoluzione dell’impianto manifatturiero lungo il suo ciclo di vita e che permetta a una rete di Digital Innovation Hub (DIH) di implementare un modello di business innovativo chiamato “Manufacturing as a Service”.
Il progetto ha l’ambizione di fare evolvere il concetto di gemello digitale (Digital Twin) verso un’entità intelligente che consenta di analizzare diversi scenari produttivi e prendere decisioni informate che garantiscano l’adattabilità e la costante evoluzione degli impianti manifatturieri.
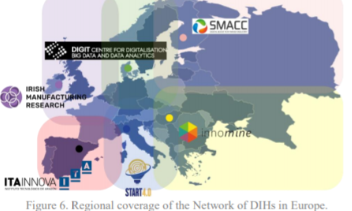
Indice degli argomenti
Cos’è DIGITbrain, il progetto europeo di START 4.0
DIGITbrain è uno dei progetti portati avanti dal Centro di competenza START 4.0 sotto l’egida del programma di ricerca europeo Horizon 2020. Il Centro di Competenza START 4.0 avrà un ruolo strategico all’interno del progetto diventando uno dei 6 Digital Innovation Hub (DIH) europei, entità di accentramento e moltiplicazione dei risultati del progetto che puntano a creare il contesto nel quale tutti i soggetti coinvolti nel ciclo di vita di un prodotto possano dialogare, dalle PMI manifatturiere ai produttori di macchine, dai fornitori di tecnologia ai clienti finali. Tra i compiti, ci sono obiettivi che sono identitari per START 4.0, come quello di attirare finanziamenti nazionali e regionali, promuovere e gestire il processo di Open Call, orientare le parti interessate del settore manifatturiero e contribuire alla creazione di un network di PMI per co-creare e sperimentare innovazioni digitali. Durante il progetto sono previsti 21 esperimenti, 7 dei quali sono in svolgimento già dalla partenza (1 luglio 2020), per validare la soluzione DIGITbrain e alimentare la piattaforma con informazioni provenienti da più aree del settore manifatturiero. Di questi, due sono progetti pilota che seguiremo con il gruppo guidato da START 4.0 e che sono partiti a luglio e dureranno un anno: il primo è Digital style e coinvolge la filiera del fashion di lusso, il secondo è Digital Brain for Laser-Cutting and Forming of Aluminium e vede protagonista Gigant, una PMI manifatturiera che offre soluzioni complete e integrate per la lavorazione della lamiera.
Se pensiamo a un classico gemello digitale, questo si limita a simulare uno specifico processo o asset fisico. L’obiettivo di DIGITbrain, che verrà testato in questi esempi concreti, è quello di migliorare questi modelli sfruttando le fasi precedenti e successive alla produzione, come l’applicazione del gemello digitale a una macchina per la tessitura del cashmere per il mondo del lusso che, oltre ai parametri sulla produzione, integra anche i valori della logistica e degli acquisti. Questo permetterà non solo di rendere più efficiente il macchinario col tempo, ma anche di sapere quali lotti sono piaciuti maggiormente ai clienti, e hanno ottenuto il maggior successo commerciale, supportando il management nel prendere decisioni di business più efficaci.
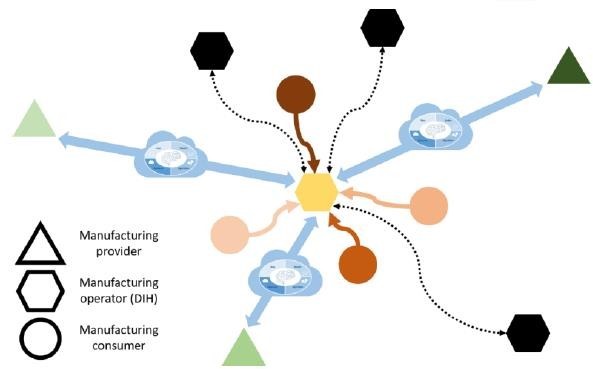
I principali ‘ingredienti’ del progetto complessivo saranno le tecnologie manifatturiere basate sulla simulazione, l’analisi di big data e l’intelligenza artificiale. I gemelli digitali saranno quindi un fattore abilitante chiave per la simulazione degli impianti manifatturieri nei rispettivi ambienti, costantemente in evoluzione e mutazione. Questo consentirà un’agilità estrema nell’adattamento a nuove condizioni produttive riducendo il tempo di riconfigurazione e modifica alle linee, uno dei principali ostacoli per le PMI che tendenzialmente hanno produzioni in piccoli lotti con un alto livello di customizzazione.
Gli sviluppi progettuali seguiranno due linee principali finalizzate alla
- riduzione dei tempi necessari per la modellazione di gemelli digitali
- creazione di una piattaforma basata sui principali standard in uso su cui possa avvenire il deploy, l’esecuzione e l’utilizzo dei modelli.
Il cervello digitale si integra verticalmente con sensori, dispositivi IIoT (Industrial Internet of Things), sistemi di produzione cyber-fisici (CPPS), dati, modelli, algoritmi e risorse. Orizzontalmente, il cervello digitale si aggiorna e memorizza gli eventi lungo il ciclo di vita dell’impianto manifatturiero, dalla progettazione allo smaltimento o riutilizzo, in un’ottica fortemente orientata all’economia circolare. L’acquisizione e analisi di dati lungo tutto il ciclo di vita è sicuramente un elemento chiave del cervello digitale che contribuirà a una progettazione sostenibile e più eco-friendly degli impianti manifatturieri.
Da Digital twin a Manufacturing as a Service
Analogamente al cervello umano, il cervello digitale punta all’auto-preservazione; in quest’ottica il cervello digitale saprà adattarsi a fronte di condizioni variabili con l’obiettivo di raggiungere il proprio target produttivo dal punto di vista di qualità, costo e sostenibilità con la minima resistenza. A tal fine il cervello digitale memorizza gli eventi fisici e digitali che coinvolgono l’impianto manifatturiero sfruttando dati, modelli, algoritmi e risorse (di calcolo e a disposizione dell’impianto stesso) per definire e controllare le azioni. Questa combinazione di dati acquisiti e modelli dedicati lungo le varie fasi del ciclo di vita dell’impianto consente all’impianto manifatturiero di adattarsi ed evolvere, aprendo scenari nuovi come la possibilità di controllare e ottimizzare da remoto il comportamento e le performance degli impianti manifatturieri per rispondere a variazioni esterne.
Il digital twin tradizionale approssima il sistema e si aggiorna con dati sul campo che sfrutta per prendere decisioni. Ma si ferma qui. Il progetto DIGITbrain mira a realizzare uno scenario che si auto-aggiorna e si collega a elementi collegati come la parte di logistica o di testing. Questo scenario consentirebbe ai provider di tecnologie manifatturiere (i.e. produttori di impianti manifatturieri) di offrire i propri prodotti in modalità ‘as-a-Service’ garantendone un’operatività e carico di lavoro ottimale. Questo scenario prende il nome di ‘Manufacturing as a Service’ (MaaS) e i Digital Innovation Hub avranno il ruolo di agire come facilitatori del modello di business, fornendo accesso ai propri impianti manifatturieri o agendo come broker tra produttori di impianti manifatturieri (e detentori di capacità produttiva) e la rispettiva domanda.
Il progetto DIGITbrain quindi è un sogno europeo, che poggia su solide basi e coinvolge un consorzio internazionale di imprese e partenariati provenienti da vari paesi (Italia, Finlandia, Estonia, Austria, Germania, Spagna, Ungheria, Repubblica Ceca, Danimarca ma anche Regno Unito e Russia). L’obiettivo è quello di realizzare un’evoluzione del concetto di digital twin da mettere a disposizione delle aziende tramite una piattaforma aperta, alla quale tutti possono contribuire. In conclusione, la democratizzazione dell’industria manifatturiera.
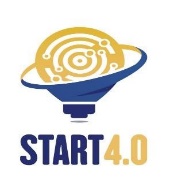
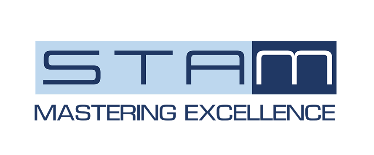