Quando il Laboratorio RISE nel 2013 cominciò il proprio percorso di ricerca nella digital transformation, quanto meno in Italia, nessuno ancora parlava di “4.0”, ma era ormai chiaro che le trasformazioni digitali già in corso nella vita di ciascuno di noi si stavano affacciando anche nel mondo industriale. Nel tempo, si affermò la denominazione di “Industry 4.0”, e successivamente il fenomeno si estese oltre l’industria e al di là della produzione, abbracciando tutti i processi aziendali (Enterprise 4.0) ed oltrepassando i confini delle singole imprese (Supply chain 4.0). Oggi, sarebbe più corretto parlare di “transizione digitale”, come un nuovo paradigma e non più come l’applicazione di qualche tecnologia digitale, più o meno nuova, ai processi manifatturieri.
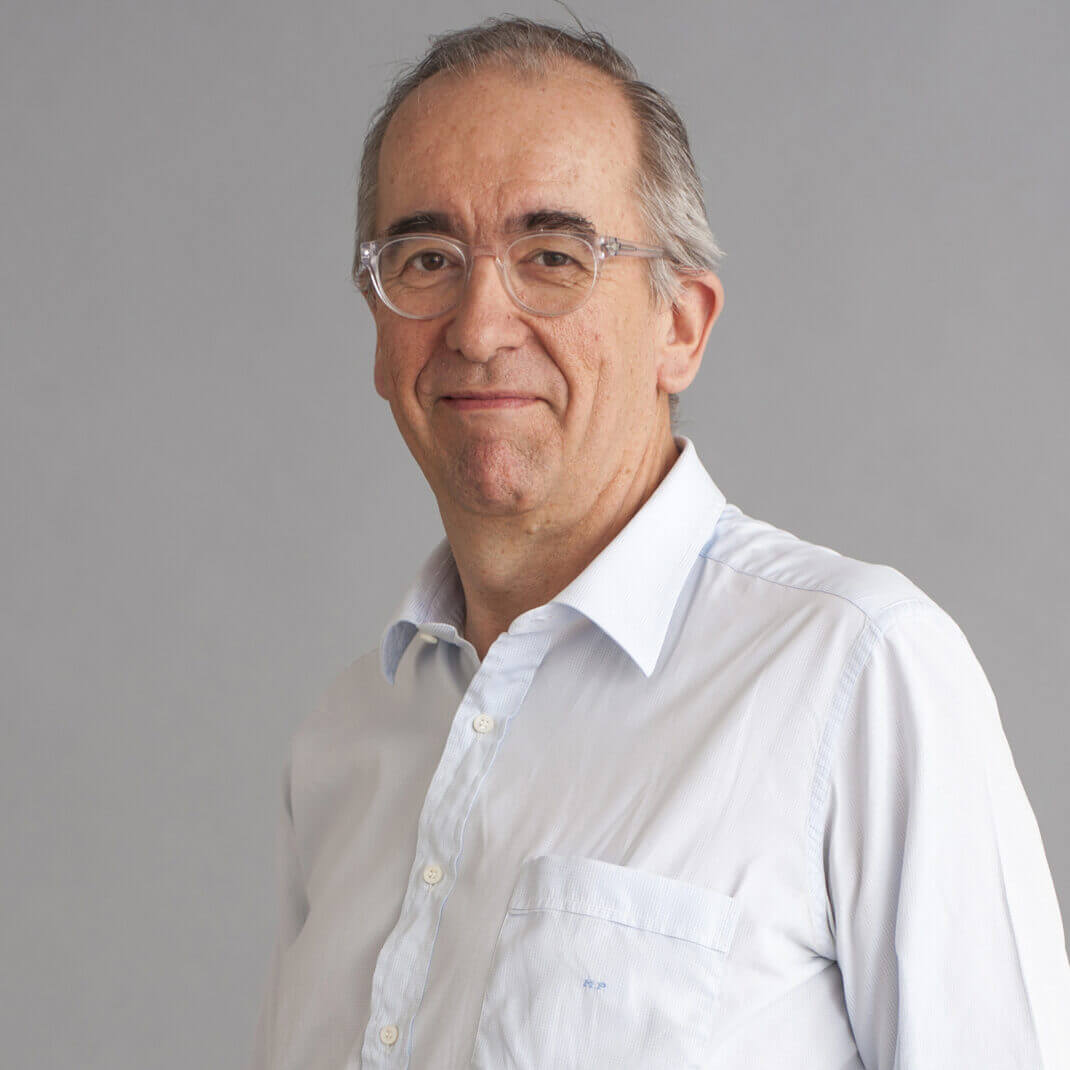
Come precisa Marco Perona, Professore dell’Università di Brescia e direttore scientifico del Laboratorio RISE, la leva digitale mette a disposizione delle aziende una quantità esorbitante di dati e informazioni che devono essere necessariamente analizzati e interpretati per guidare nuovi modelli di business che vedono il digitale intersecarsi e “saldarsi” con altri paradigmi che si stanno affermando altrettanto vigorosamente nel panorama attuale, quali ad esempio la cosiddetta “servitizzazione” e, forse ancor di più, l’economia circolare.
Il Laboratorio RISE ha raccolto la sfida di portare per mano le imprese del nostro territorio e del paese nel complesso verso un percorso di sviluppo delle strategie aziendali, di un’azienda smart che, anche grazie alla diffusione di nuove soluzioni digitali (4.0), riesca ad abbracciare (anche) i paradigmi della servitizzazione e dell’economia circolare. E, vista la fortissima enfasi che arriva anche dal consumatore e risale lungo tutte le supply chain, perseguire questi obiettivi di circolarità connessi a temi come il riutilizzo e la minimizzazione degli sprechi rapresenta un boost, un acceleratore per gli investimenti in tecnologia 4.0
Indice degli argomenti
La quarta edizione della ricerca RISE Impresa Smart 4.0
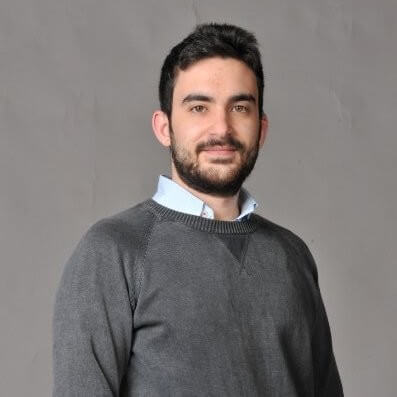
“Di pari passo con l’affermarsi e il diffondersi di questo nuovo paradigma abbiamo visto svilupparsi e crescere nel tempo l’ampiezza e l’intensità delle nostre ricerche: e così, partendo dal campione di sole 74 impese rispondenti del 2014, oggi possiamo contare su un campione di ben 165 imprese. Attraverso questa massiccia adesione riceviamo valore di due tipi: di tipo scientifico, visto che un campione (più) ampio significa una maggiore validità e rilevanza delle evidenze empiriche raccolte; ma anche valore di tipo relazionale e motivazionale, che ci spingerà nel futuro a proseguire e ad intensificare gli sforzi” esordisce Marco Ardolino, Post-doc research fellow all’Università di Brescia in occasione della presentazione dei risultati della quarta edizione della ricerca “Impresa Smart 4.0. La trasformazione digitale del manifatturiero nell’era del Covid“.
L’edizione di quest’anno, caratterizzata da un nuovo questionario semplificato, si è prefissata l’obiettivo di proseguire la valutazione dello stato dell’arte delle imprese italiane, in termini di conoscenza e, soprattutto, effettiva adozione delle tecnologie digitali a supporto dei processi di business. Naturalmente, una particolare attenzione è stata dedicata alle implicazioni, già in essere e in divenire, della pandemia Covid-19 sul tessuto manifatturiero italiano. Ma diamo uno sguardo alla composizione del campione preso in esame.
Identità del campione e domande di ricerca 2021
Metà del campione (52%) è composto da aziende di grandi dimensioni, l’altra metà fa riferimento alle piccole (20%) e medie (28%) imprese. Significativa la polarizzazione in termini di localizzazione geografica (oltre l’80% dei rispondenti è situato al Nord Italia soprattutto in Lombardia). Guardando ai settori, una discreta percentuale (41%) è quella che interessa macchinari, macchine utensili e apparecchiature, il 16% il metallurgico e il 7% i veicoli a motore, rimorchi e semi-rimorchi. Il 29% dei rispondenti ricopre un ruolo nella direzione e il 59% è in azienda da oltre dieci anni.
Sei gli obiettivi che sono stati indagati, spaziando dalle sfide e opportunità che inibiscono o di contro accelerano il paradigma 4.0 in Italia, dallo stato dell’arte relativo all’implementazione del paradigma 4.0 nelle aziende come i benefici attesi e ottenuti dall’implementazione delle tecnologie per arrivare a indagare competenze e misure necessarie per incentivare gli investimenti e colmare i gap.
Certo è che quest’anno non è stato possibile esimersi dal considerare un fenomeno che ha polarizzato l’attenzione del Laboratorio RISE e quella di moltissimi rispondenti: la pandemia da Covid-19 ha avuto un impatto tragico e improvviso, di cui l’Italia, uno dei primi paesi colpiti sia dal punto di vista sanitario che economico, ha pagato lo scotto maggiore rispetto alla media globale. La pandemia ha causato una drastica riduzione del PIL globale: a livello di factory ha costretto le aziende a lockdown produttivi, a misure rigide di distanziamento sociale e per forza di cose ad una revisione o addirittura una riprogettazione delle postazioni e degli spazi di lavoro, come alla quasi obbligata prassi dello smart working; ha messo in crisi le supply chain rispetto alla criticità di approvvigionamento materie prime e componenti, alle restrizioni dovute alle limitate esportazioni, alla variazione delle abitudini di acquisto dei consumatori come al panic buying; e nel complesso, ha avuto ripercussioni sull’intero ecosistema con continue variazioni nelle regolamentazioni di prodotto come l’incremento della produzione di rifiuto e di rischio banca rotta.
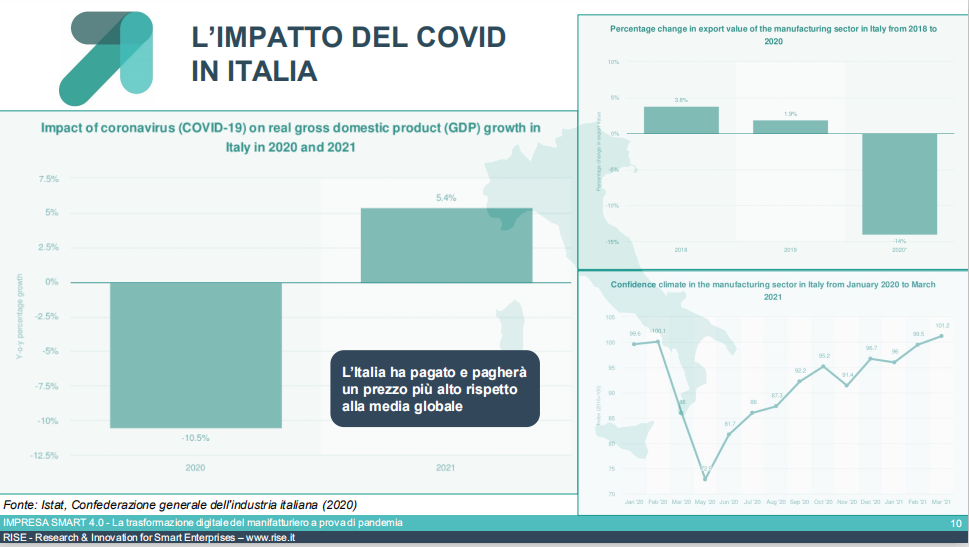
L’impatto della pandemia sul fatturato delle imprese italiane
Le indicazioni delle imprese fotografano impatti per lo più significativi sia sull’esercizio 2020 che in previsione sul 2021. Molte aziende (46%) hanno dichiarato una forte contrazione degli introiti economici nel 2020 o una riduzione moderata (35%), pochissime segnalano un effetto positivo (8%). Questo anche perché la maggior parte è riuscita a rispondere solo parzialmente alla sfida posta dalla pandemia: da un lato, quasi tutte le imprese hanno riconvertito con facilità in remoto sia le riunioni che il lavoro dei “white collar”; dall’altro, solo una ristretta minoranza di esse è riuscita a remotizzare efficacemente anche le attività produttive, o quanto meno il controllo della produzione. Si legge un maggiore ottimismo relativamente al 2021 con la maggioranza relativa del campione (36%) convinta di centrare il budget e più del 15% che pensa di andare oltre.
Ciò che è certo è che il Covid ha reso esplicito che ora è indispensabile un cambio di passo nella digitalizzazione, che permetta non solo il lavoro agile anche in produzione, ma soprattutto che faciliti la nascita di capacità predittive “data-driven”, stimoli una crescente integrazione tra partner di filiera, aumenti la trasparenza delle catene del valore, ed in generale aumenti l’agilità e la resilienza dei sistemi economici, rispetto alle grandi perturbazioni che certamente vivremo nuovamente nel futuro.
Accelera la remotizzazione del lavoro d’ufficio, IoT e Analytics IoT le tecnologie rilevanti
I benefici sono per lo più riconducibili al supporto al lavoro da remoto, e quindi direttamente connessi alle opportunità di effettuare riunioni e meeting a distanza (90%) come la completa remotizzazione dei cosiddetti white collar (80%). Paradossalmente se guardiamo agli effetti legati alle riconversioni produttive flessibili e durature come alle vera remotizzazione del controllo dell’avanzamento della produzione, le tecnologie non sono state così d’aiuto (10%), un dato empirico rappresentato bene dalla letteratura scientifica che vede pochissimi contributi che riguardano l’apporto delle tecnologie a supporto dei processi manifatturieri e non prettamente d’ufficio.
Entrando nel merito delle tecnologie tra quelle più ricercate e conosciute dalle aziende, prevale sicuramente il focus sulle tecnologie legate alla acquisizione, all’analisi e all’elaborazione dei dati. Guadagnando rispettivamente il +30% e +20% di incremento rispetto agli anni precedenti, Big Data Analytics e Internet of Things sono ai primi posti. Alle loro spalle, cresce l’Intelligenza artificiale (+33%), quasi trascurabile nelle precedenti rilevazioni. Continua a crescere anche la robotica collaborativa (+25%) che con la necessità di mantenere le distanze continuerà ad aumentare.
Dall’altro lato della medaglia, notiamo tecnologie che stentano a decollare nonostante sulla carta siano promettenti, come la Blockchain molto rinomata per le capacità di migliorare tracciabilità, trasparenza e sicurezza che afferisce alla pianificazione logistica tattica e strategica, rimane un’eterna sconosciuta.
Aumenta il numero medio di tecnologie adottate, ma sono molte le aziende ancora al palo
Il panorama raccolto, se confrontato con quello delle precedenti ricerche, illustra sì un progresso, ma purtroppo più lento di quanto desiderato: aumenta di poco il numero di tecnologie 4.0 adottate mediamente dalle imprese (da 1,7 tecnologie mediamente impiegate nel 2017, al dato di quest’anno di 3,0). Un dato molto incoraggiante che fa capire come le aziende non si limitino ad adottare una sola tecnologia, ma stia prendendo piede la visione di un’adozione globale che copre tutti i processi e soprattutto tecnologie che collaborano tra loro. Tra le più adottate Big Data Analytics, Robotica collaborativa e IoT in ordine. La Blockchain stenta a decollare.
Incrociando ora la rilevanza delle tecnologie rispetto all’utilizzo. Si vede come crescono, ma non di molto le aziende che usano con criterio molte tecnologie, le stelle crescono del +4%. Si riduce, ma di poco (-5%), la percentuale delle aziende “ritardatarie”, cioè di quelle aziende che non si sono attivate e che non attribuiscono alla transizione digitale la corretta rilevanza, e pertanto non danno a vedere di volersi attivare a breve: e queste restano comunque un terzo circa delle imprese censite! Aumenta (del +26%) la percentuale di aziende che, pur avendo acquisito una buona consapevolezza sul fenomeno 4.0, rimane ancora al palo dal punto di vista dell’implementazione e che compone il gruppo dei teorici, mentre è molto più moderato l’incremento della percentuale di aziende “in movimento”. L’approccio dei praticoni pian pianino si sta dipanando (-15%) e si vede come l’approccio che porta ad adottare una tecnologia solo per sfruttare l’incentivo senza sapere esattamente cosa fa e se serve, in questo momento non sta pagando.
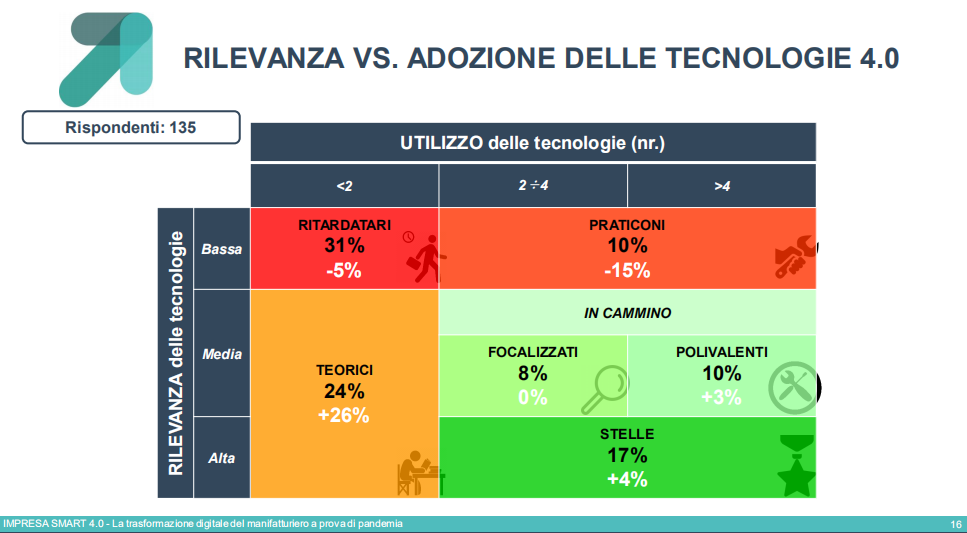
Progetti 4.0: guidati dalla Direzione, impattano la Produzione
In questo quadro resta pressoché statica la fotografia delle funzioni, aree e processi aziendali più rilevanti nella trasformazione, ossia quelle che da un lato stimolano e guidano i progetti e dall’altro sono l’oggetto degli interventi.
La Produzione è il processo maggiormente impattato (oltre il 50%), al secondo posto si conferma la Ricerca e sviluppo (poco meno del 40%), la parte dell’IT, dei sistemi informativi fa da collante tra le aree aziendali. Purtroppo, la logistica è indietro. Rispetto alle rilevazioni precedenti, la palla è nelle mani delle funzioni impattate rispetto ad altre funzioni e processi che potrebbero essere maggiormente impattanti.
Le prime linee sono sempre più direttamente coinvolte in questa trasformazione, le restanti sezioni rispetto al 2019, rimangono più o meno invariate. Il ruolo di principale agente del cambiamento rimane in capo in primis al vertice aziendale. La Direzione (37%) resta la funzione aziendale tipicamente alla guida della trasformazione, anche se cresce il ruolo del CIO (18%) e di altri manager della C-suite (28%), segnatamente Operations e R&D, le cui funzioni restano anche al centro degli interventi. Colpisce invece il ruolo completamente marginale della direzione HR, sia come ente che lancia e controlla iniziative 4.0, sia come destinatario di progetti in quest’ambito.
La carenza di competenze adeguate frena la digital transformation
E stupisce soprattutto perché, non diversamente dalle edizioni precedenti, il fattore che emerge con chiarezza come maggiore freno all’implementazione della trasformazione digitale e come l’ingrediente della ricetta di cui si avverte la maggiore carenza, è legato alle competenze, sia del personale a organico, sia delle nuove risorse da reperire all’esterno.
Anzi, all’atto pratico, il segnale meno positivo che pare emergere da questa nuova edizione della ricerca è proprio il progressivo allargarsi del divario tra le aziende effettivamente capaci di sviluppare internamente, oppure di attrarre dall’esterno queste competenze, e quindi di alimentare in maniera più organica e sostenibile il processo di trasformazione digitale; e quelle che, magari anche animate dalle migliori intenzioni di investimento, vedono i propri sforzi produrre risultati meno incoraggianti proprio a causa della mancanza di risorse umane con le competenze necessarie.
Il tema delle competenze resta al centro, occorre lavorare sull’adeguamento delle risorse che si immettono nel mondo del lavoro per guidare l’impresa verso la transizione 4.0. Solo una azienda su quattro ritiene che le competenze presenti in aziende siano idonee. Un campanello d’allarme importante per il contesto universitario che deve accelerare il suo impegno nel fornire al mondo delle imprese figure professionali formate adeguatamente per interpretare e fare uso delle tecnologie digitali.
Come ha voluto sottolineare durante il webinar Maurizio Tira, Rettore dell’Università di Brescia “Gli Osservatori ci fanno rendere conto dello stato dell’arte in cui siamo, stimolano l’innovazione e chi è ancora indietro. Questa pandemia ci ha trasmesso pressioni diverse e urgenze maggiori e la recente trasmissione del Piano Nazionale di Ripresa e Resilienza (PNRR) ci stimola a far sì che l’investimento enorme che interesserà il nostro Paese possa costituire un trampolino di lancio per rendere il livello di sviluppo dell’Italia davvero pronto alle sfide del mondo. Le Università stanno facendo egregiamente il loro lavoro, come le imprese. E la continuità dell’Osservazione è una delle fondamentali caratteristiche per ottenere risultati”.
Il 4.0 favorisce la resilienza delle imprese
Ora, incrociando il numero e il livello di implementazione delle tecnologie 4.0 con l’integrazione e l’interconnessione ai sistemi informativi, il backbone IT legato ai sistemi CRM, MES ecc, e con l’adeguatezza delle competenze per gestire le tecnologie 4.0 e la disponibilità di un piano di azione per lo sviluppo futuro si ottengono diversi cluster allargati nei quali si posizionano le aziende:
- campioni: il 18% rispetto al 5% nel 2019 non solo adotta svariate tecnologie 4.0, ma ha a disposizione le corrette competenze per poterle impiegare e armonizzate con l’infrastruttura informativa. Completato al 100% il percorso di trasformazione digitale, ora devono mantenerne adeguato l’utilizzo.
- digitali: il 26% su 12% della ricerca precedente dispone di tante tecnologie integrate con i sistemi informativi, ma è in un momento di adeguamento delle competenze per governare la trasformazione.
- al palo: crescono dal 34 al 38% le aziende ancora ferme che hanno adottato poche tecnologie digitali e non hanno competenze idonee per partecipare alla trasformazione.
- informatizzati: passati dal 49 al 18% hanno una ossatura informativa pronta a recepire tecnologie da innestare, ma ancora non si sono portate in casa queste tecnologie da integrare.
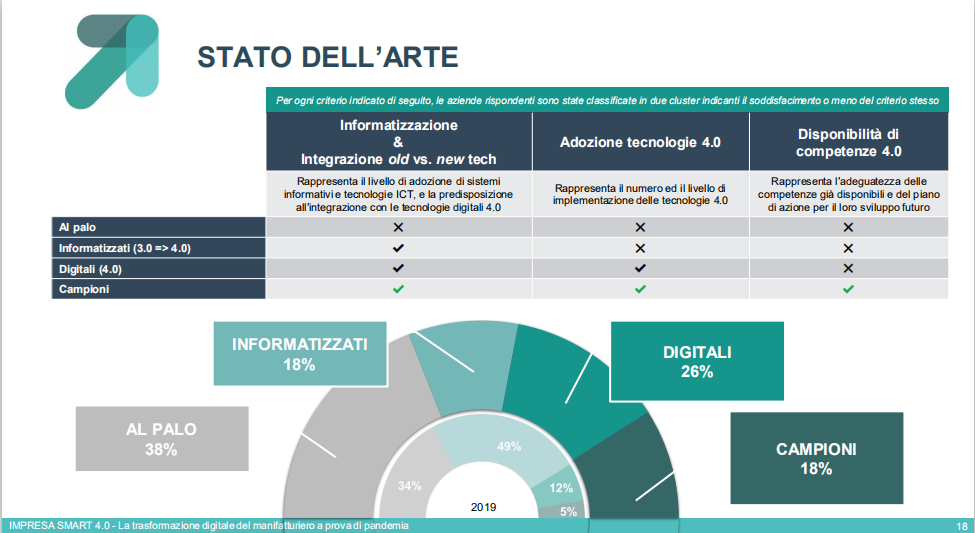
Un dato interessante emerge confrontando le stime sul ritorno economico degli investimenti in tecnologie 4.0 e quanto queste aziende che sono già digitali o campioni siano confidenti nella ripresa per il 2021. Quello che si evince è che più aumenta il cluster di digitalizzazione e più aumenta la fetta di aziende confidenti in una crescita rispetto alle stime per il 2021 in termini di fatturato. Spostandoci verso le aziende un po’ più arretrate la confidenza decresce, con previsioni negative in vista del 2021.
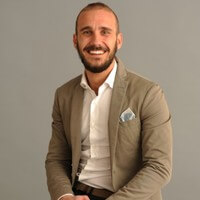
“Tutto ciò è coerente con altre ricerche emesse da altre fonti da cui è emerso come le aziende maggiormente digitalizzate siano più pronte nel rispondere, equipaggiate con nuovi modelli business, al cambiamento repentino e destabilizzante del contesto. Al di là del ROI, il 4.0 dovrebbe facilitare l’interpretazione delle esigenze di mercato e la risposta rapida agli imprevisti” spiega Massimo Zanardini, Consulente senior IQ Consulting, spin-off UNIBS.
Risorse adeguate e incentivi fiscali: le leve per la trasformazione 4.0
Buona parte dei rispondenti indica che sebbene il 4.0 sia molto importante, ad oggi non è alla portata di tutti. Ci sono ostacoli che non lo rendono accessibile a tutte le imprese. Il 41% ritiene che sia la direttrice necessaria per sopravvivere ad un mercato globale. Una impresa su 10 la vede come opportunità per effettuare investimenti e rinnovare il parco macchine sfruttando gli incentivi statali.
L‘elemento significativo è legato alle risorse umane adeguate (81%) con particolare attenzione alle esigenze di riqualificazione delle loro competenze: servono in primis competenze tecnologiche e in crescita, il fabbisogno di competenze analitiche e manageriali, a distanza, anche la sensibilità verso le competenze relazionali. La rivoluzione 4.0 infatti non è una rivoluzione solo ed esclusivamente tecnologica, anzi è human-centered con l’umano che rappresenta l’ingrediente necessario della ricetta per ottenere un risultato di successo. In secondo piano, si collocano gli incentivi fiscali che favoriscono gli investimenti (74%), abilitanti all’interno delle politiche industriali ritenute efficaci.
Gli incentivi fiscali sono ritenuti ancora un importante fattore abilitante: iper e super ammortamento risultano le misure più adottate; cresce l’interesse verso il credito di imposta specifico per le attività di formazione, a riprova di una maggiore sensibilità verso il tema della riqualificazione delle competenze delle persone.
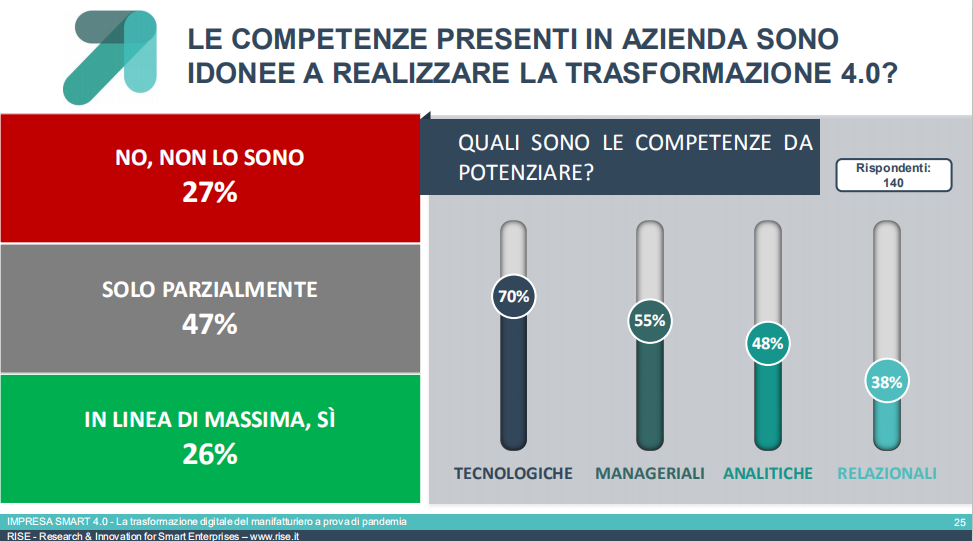
Transizione 4.0: tra benefici e percezioni delle aziende
Seppure vi siano ancora alcuni scettici, la maggioranza dei rispondenti guarda al paradigma 4.0 come ad una concreta opportunità per rilanciare il settore manifatturiero Italiano. I benefici della trasformazione digitale risultano piuttosto trasversali, con un lieve focus sul miglioramento e l’efficientamento dei processi. La riduzione degli errori di picking, l’aumento della produttività di magazzino e la maggiore puntualità delle consegne sono i benefici più rilevanti in ambito logistico. Ancora poca l’enfasi verso il supporto ai processi di pianificazione.
Si evidenzia una certa difficoltà da parte delle imprese nello stimare i benefici associati agli investimenti 4.0. I vincoli finanziari sono comunque rilevanti. Anche in logistica prevale la difficoltà a stimare i benefici associati agli investimenti, la cui entità risulta essere l’ostacolo in assoluto più significativo. Si segnalano difficoltà anche sul fronte dell’integrazione tra tecnologie 4.0 e l’infrastruttura IT preesistente.
In termini invece di impatto delle tecnologie sugli operatori a livello occupazionale: più del 50% non ritiene che ci sarà un saldo negativo, le tecnologie non sostituiranno più lavoro di quanto ne verrà creato, ma richiederanno una composizione diversa del mix. Il 25% ritiene addirittura che l’implementazione dell’Impresa 4.0 avrà un impatto positivo generando nuovi lavori. Dall’altro saranno tipicamente più complessi rispetto ai tradizionali (48%).
Impresa 4.0: una concreta opportunità per rilanciare il manufacturing italiano
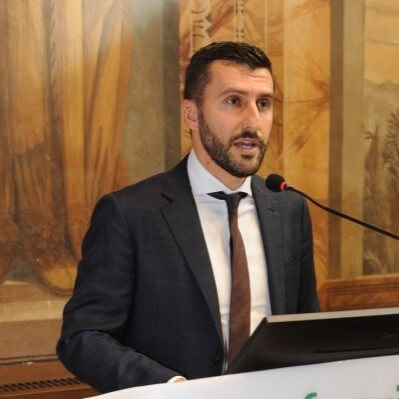
“Abbiamo positivamente rilevato che per gran parte delle imprese (l’80%) il 4.0 costituisce una concreta opportunità per rilanciare il manifatturiero italiano. Siamo positivamente sorpresi dal maggiore ottimismo a cui soprattutto le aziende digitalmente più mature guardano alla ripresa post pandemia con una crescita nell’attecchimento delle soluzioni. Le imprese italiane, comunque, si percepiscono in ritardo soprattutto quelle che competono a livello internazionale e si fa sempre più profonda la frattura tra le aziende che stanno investendo e seguendo una roadmap di trasformazione verso la configurazione 4.0 (i campioni digitali) rispetto alle aziende ferme al palo. C’è un aspetto culturale che va superato grazie ad operazioni di sensibilizzazione e di informazione che noi nel nostro piccolo cerchiamo di fare con iniziative come questa” interviene Andrea Bacchetti, Ricercatore e Professore Associato all’UNIBS.
Ora, l’impatto del Covid non potrà che imprimere un’accelerazione alla consapevolezza delle aziende ed alla loro motivazione ad investire: i numeri dimostrano che le imprese digitalmente più mature sono quelle che stanno reagendo meglio agli effetti della pandemia. E poi, la consapevolezza ormai raggiunta dal mondo accademico sull’esigenza di attivare processi formativi finalizzati alla creazione di profili (più) vicini alle esigenze delle imprese, fa ben sperare per il futuro. Infine, l’Italia è il Paese Europeo che ha ricevuto la parte più corposa del Recovery Fund, il programma di stimolo finanziario più grande mai varato dall’Unione: più di 200 miliardi di Euro che il Governo utilizzerà anche per potenziare gli stimoli alla digitalizzazione delle imprese.
Il Laboratorio RISE continuerà a monitorare e misurare lo stato effettivo di questo nuovo paradigma digitale, stimolando ed eventualmente supportando le imprese nella progettazione di consapevoli roadmap di trasformazione.
Ma ora veniamo alle case history, in particolare a un primo progetto che ci porta nel nucleo del paradigma 4.0 direttamente nei reparti di produzione.
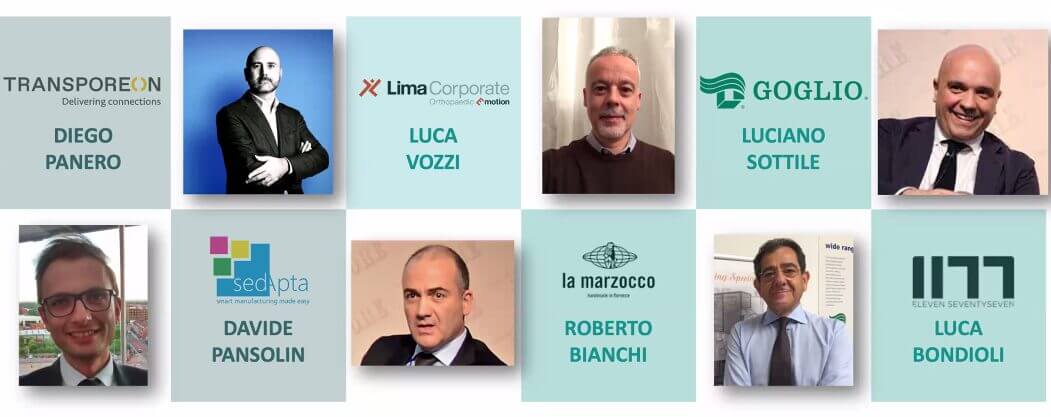
Il progetto MES sedApta con Poltrona Frau nell’arredamento di alta gamma
sedApta è un gruppo internazionale nato dall’aggregazione di alcune tra le migliori aziende tecnologiche con sedi in Italia, Germania, Francia e Brasile. Con oltre 25 anni di esperienza nel Manufacturing, IT e Supply Chain Management, oggi può contare su più di 1.000 clienti. Il Progetto MES in Interiors in Motions è stato attivato su una delle tre Business Unit, la divisione che serve il mondo Automotive e Rail, del Gruppo Poltrona Frau, un’azienda italiana che opera nel settore dell’arredamento di alta gamma con sede a Tolentino dal 2016 controllata dal gruppo americano Haworth Inc.
È un progetto che si è sviluppato in due anni, con un progetto pilota nel 2019 che ha richiesto 3-4 mesi di studio, e il progetto vero e proprio reso live nel 2020 nonostante il problema pandemico importante da marzo a maggio che ha costretto a spostare molte attività da remoto, facendo vincere a Poltrona Frau il premio LEANicon FIRST PRIZE 2020, molto importante a livello manufacturing. Il 2022 vedrà il porting della soluzione sulle altre divisioni (Casa & Ufficio e Contract) e ulteriori funzionalità.
Davide Pansolin, Industry Manager sedApta spiega “Gli obiettivi specifici del progetto erano: monitorare la cadenza delle linee produttive (ricopertura) e controllare i cicli produttivi, snellire e migliorare l’esecuzione dei controlli presso tutte le linee di produzione (il change management è stato importante), distribuire la documentazione di produzione (ILC, OPL, PC) direttamente sulle linee di produzione aggiornata in tempo reale per i modelli in produzione (evitare di portare in giro documentazione che deve essere a disposizione in linea), migliorare le fasi di controllo qualità sul prodotto finito raccogliendo le informazioni sui difetti, garantire la tracciabilità dei consumi di pelle per fornitore (la materia prima deve essere top level), integrare il MES con il sistema di rilevazione presenze per la corretta analisi delle ore di produzione dichiarate dagli operatori, utilizzare terminali touch screen, lettori bar code e RFID per velocizzare le attività di dichiarazione di produzione e collegamento utenti”.
Per fare tutto ciò, sedApta ha utilizzato: lo Shop Floor monitor per monitorare le performance degli impianti, il MES, la parte Analytics per misurare le performance di processo e i PC industriali all’interno del reparto. I risultati vanno dal miglioramento dell’efficienza della manodopera e della riduzione degli scarti di processo, dalla standardizzazione del processo produttivo grazie alla possibilità di mostrare in postazione i documenti di processo specifici per la lavorazione in corso, dalla reportistica che permette di monitorare i reparti a livello capillare con informazioni di dettaglio non solo sugli impianti, ma soprattutto sulla manodopera, alla individuazione dei principali sprechi all’interno della filiera produttiva, al monitoraggio accurato e in real time delle performance di processo, alla riduzione del lead time e del WIP, al monitoraggio visual grazie all’introduzione degli Andon, dello stato di avanzamento della produzione e di eventuali ritardi o anticipi rispetto al target.
Cloud e GPS di Transporeon per la logistica 4.0 di Burgo
Dal reparto produttivo, passiamo allo step immediatamente successivo che concerne la movimentazione e quindi la logistica che si occupa della parte distributiva per arrivare agli utilizzatori, che siano industriali o finali. Parliamo di un’esperienza decennale maturata all’interno di una realtà importante nel mondo della carta e che tocca aspetti legati alla logistica collaborativa e sistemi data-driven a supporto dei processi decisionali e che nell’ultimo anno ha vissuto un ulteriore step legato al progetto di track and trace in real time delle spedizioni” inizia Diego Panero, Global Sales & Account Manager Transporeon.
Transporeon è un’azienda e una soluzione cloud che da vent’anni aiuta le aziende a collaborare in maniera efficace ed efficiente con i propri trasportatori. Lo fa con circa 1300 aziende hanno scelto i suoi servizi e che collaborano quotidianamente con circa 120.000 trasportatori con una copertura geografica su 100 countries. La soluzione è adottata su diversi verticals e un aspetto che accomuna i brand è la rilevanza in termini di numerosità della componente trasporti.
Con 12 stabilimenti principalmente in Italia, 15 linee produttive e una vendita di quasi due milioni di tonnellate di carta, Burgo Group è uno dei principali produttori europei di carte grafiche, specialties, carte da imballaggio e per il comparto del packaging. Lo scenario competitivo in cui Burgo si è mossa, tipico di tutte le aziende del settore paper ma con aspetti che riguardano tutte le aziende manifatturiere in generale, è contraddistinto da una forte attenzione ai costi, rilevanti soprattutto per chi produce un prodotto molto povero come la carta, così come l’aspetto della sostenibilità, molto importante per il settore che deve sottostare a certificazioni particolari. Tipico del settore è poi la logistica del riciclo molto complessa perché i fornitori di macero sono tendenzialmente molto frammentati nel territorio e tipicamente aziende molto piccole con un livello di informatizzazione e propensione all’utilizzo di tecnologie informatiche sicuramente non elevatissimo.
Un aspetto fondamentale del progetto di Real time visibility è il passaggio da un modello reattivo a un modello predittivo che si riconduce al concetto delle soluzioni data-driven che supportano il decision making. Oggi ci si trova spesso a gestire una quantità enorme di dati che nel caso della logistica distributiva riguardano gli automezzi in movimento e i fornitori che possono prestarsi ad un servizio di trasporto. La possibilità di disporre di tutto il parco mezzi dei fornitori connesso in real time ha consentito e sta consentendo, con un progetto partito l’anno scorso, di ottenere degli elevatissimi livelli di servizio nei confronti del cliente, ma soprattutto di realizzare quelle sinergie in termini di incrocio domanda-offerta dei servizi di trasporto che in qualche modo consentono di ridurre i costi di trasporto e i chilometri a vuoto e quindi la CO2 prodotta.
Dieci anni fa Burgo nel voler digitalizzare la logistica dei trasporti ha scelto una tecnologia Cloud per gestire la distribuzione a 360 gradi, ad oggi parzialmente adottata in particolare per la parte di assegnazione dei trasporti, della gestione degli slot temporali e della tracciabilità in real time che racchiude altri aspetti che verranno ampliati man mano. La scelta non si è limitata alla tecnologia. Infatti, Burgo ha ricercato anche l’adozione di un network. Oggi Transporeon consente alle aziende clienti di colloquiare con circa 120.000 trasportatori connessi e questa potenza sta nel consentire a tutti i clienti di individuare il giusto trasportatore sul territorio, ma soprattutto la qualità del servizio fornito abilitando il match making tra domanda e offerta di trasporto.
Il processo che Burgo ha implementato tocca sia l’approvvigionamento della merce che la distribuzione vera e propria, inbound e outbound. Distribuzione significa consentire a Burgo di trovare il trasportatore migliore che possa offrire un determinato servizio al cliente diretto o al distributore nei tempi e nei modi richiesti. Questo accade grazie a questo match making, e uso della soluzione cloud che diventa lo strumento unico attraverso cui Burgo e i suoi trasportatori comunicano ogni giorno il che ha consentito di eliminare la comunicazione destrutturata come e-mail o telefonate ingaggiando il trasportatore migliore con i dettagli della spedizione, ma soprattutto andare ad individuare effettivamente il trasportatore migliore sfruttando il mercato dei ritornisti. Avendo i trasportatori collegati in real time e geolocalizzati è più semplice individuare il trasportatore in prossimità del punto di carico e che deve magari ritornare a destinazione che potrebbe coincidere con la destinazione del cliente Burgo magari vuoto. Questo permetterebbe a Burgo di avere un servizio economico e al trasportatore di evitare di fare un percorso vuoto riducendo per lui un aspetto di costo e soprattutto a livello ambientale evitare un’emissione di CO2 non necessaria.
Fondamentale è l’aspetto di organizzazione delle operazioni di carico e scarico tramite la logica di calendarizzazione degli slot di carico che ha consentito la riduzione dei tempi di attesa e delle code alle baie di carico, dall’altro avendo automatizzato queste operazioni con sistemi di controllo accesso veicoli leggendo la targa ha evitato l’eccessiva iterazione tra persone e questo anche in ottica del Covid è stato particolarmente apprezzato e consentito l’efficientamento delle operazioni di magazzino. Con una prenotazione verificata dalla presenza di un veicolo geolocalizzato all’approcciare del veicolo nel punto di carico Burgo sapeva esattamente cosa aspettarsi e quindi c’è stato un efficientamento a livello di magazzino.
In ultimo, lo sviluppo più rilevante è legato alla possibilità di consentire ai clienti di ottenere una visione del posizionamento fisico dell’automezzo sulla mappa con vantaggi come la riduzione della comunicazione tra azienda e trasportatore prima molto elevata perché il cliente si rivolgeva a Burgo per sapere dove si trovava l’automezzo e quando sarebbe arrivato. Ora il sistema invia automaticamente un estimated time of arrival aggiornandolo a seconda degli eventi sul tragitto e ottimizza i tempi di attesa definendo le priorità di gestione del carico in arrivo.
Tra i vantaggi sicuramente si annoverano: l’abbattimento dei costi di processo dovuto ad una riduzione drastica delle comunicazioni destrutturate, la riduzione dei costi di trasporto con un più efficace match making tra domanda e offerta dei servizi di trasporti, la diminuzione dei tempi di attesa alle baie di carico-scarico e l’incremento della soddisfazione dei clienti che possono avere a disposizione l’esatta informazione sul posizionamento fisico dell’automezzo.
Lima e l’esigenza di una configurazione 4.0 nell’ambito ortopedico
Se c’è un settore che è stato profondamente impattato e coinvolto dalla pandemia è quello della sanità e degli ospedali, business nei quali Lima Corporate opera. Si tratta di un’azienda italiana con sede a Villanova di San Daniele del Friuli attiva nello sviluppo, produzione e commercializzazione di protesi ortopediche sostitutive delle articolazioni ossee per ginocchio, anca, spalla e articolazioni minori. In che modo un’azienda così ha reagito all’impatto forte e inatteso della pandemia Covid e in che modo ha contributo la leva delle tecnologie digitali?
“Il medicale è stato impattato in maniera forte ma non meno di altri settori. Abbiamo avuto la fortuna di dimostrare di essere stati molto più resilienti rispetto ad altri settori industriali. Abbiamo sofferto un calo drastico nella primavera dell’anno scorso, con un -90% di colpo almeno fino a giugno e poi abbiamo chiuso con un -20% rispetto agli anni precedenti. Ma sempre pronti a cogliere i segnali e siccome non era possibile entrare negli ospedali, abbiamo lavorato senza sosta allo sviluppo di soluzioni per continuare ad essere presenti in questo mercato” racconta Luca Vozzi, Vice President “La formazione a distanza e l’uso di Realtà aumentata e Realtà virtuale hanno aiutato a tenere ingaggiati i chirurghi. Noi non siamo molto grandi in questo settore, competiamo con colossi americani presenti in tutto il mondo. Ebbene, quando gli ospedali erano chiusi, la nostra presenza di fronte ad un video aveva le stesse probabilità di un concorrente 10 volte più grande di noi, alla fine la dimensione dello schermo è la stessa per tutti. Abbiamo dunque cercato di sfruttare questa condizione di valore per essere sempre presenti e fare rumore nel mondo dell’ortopedia”.
Con 15 anni di esperienza nella stampa 3D in titanio, Lima è in grado da anni ormai di fornire soluzioni ortopediche ricostruttive delle articolazioni e delle ossa di tipo personalizzato. Inoltre, è un’azienda manifatturiera che ha iniziato un percorso di digital transformation più di cinque anni fa, più o meno in linea con il paradigma 4.0, lavorando sull’Intelligenza Artificiale per affinare la previsione della domanda commerciale, sulla tracciatura delle spedizioni dei prodotti in tutto il mondo attraverso la definizione di digital twin dei modelli distributivi passando attraverso i temi di digital manufacturing come l’automazione dei processi, le interazioni smart con le macchine, l’uso della tecnologia RFID e la manutenzione predittiva. La pandemia non ha toccato questi progetti, la scelta è stata di non rimanere indietro continuando ad investire su temi che possono garantire continuamente il vantaggio competitivo in termini di efficienza rispetto ad alcuni competitors. Così Lima, ha sfruttato il periodo pandemico per fornire ai clienti soluzioni completamente digitalizzate per proporre modelli di business diversi.
Lima ha sviluppato una piattaforma di interazione con i chirurghi che permette loro di comunicare con gli ingegneri per definire la soluzione personalizzata, da attività di simulazione a prototipazione rapida a stampa in plastica dell’anatomia del paziente fino alla consegna del prodotto sterile, una divisione che raccoglie 300-400 casi all’anno molto complessi e tumorali difficili da risolvere con soluzioni tradizionali. Nel 2018, ha acquisito una società americana attraverso cui eroga, anche sul mercato europeo un pacchetto che offre al chirurgo una soluzione di pianificazione dell’intervento dalla TAC in cui il software ricostruisce l’anatonomia del paziente attraverso l’uso dell’AI che si basa su una banca dati delle ossa e il chirurgo riesce attraverso il catalogo 3D dei componenti standard a scegliere le componenti ottimali per il paziente alla sala operatoria con l’utilizzo di strumentazione smart il chirurgo riesce a seguire in maniera allineata a quanto pianificato in studio l’esito del processo operatorio in sala. Questo garantisce al paziente la perfetta esecuzione dell’intervento tracciato, e una guida importante al chirurgo per eseguire nel minor tempo possibile e con la migliore sequenza di operazioni tutta la pratica chirurgica da definire.
“Come ultimo elemento – sottolinea Vozzi – poco più di un mese fa abbiamo tagliato il nastro virtuale della prima fabbrica digitale in un ospedale a Manhattan. Dal Friuli Venezia Giulia, Lima sfrutta la tecnologia digitale e tutto quello che concerne la stampa 3D per offrire all’ospedale un prodotto finito, mantenendo una maggior vicinanza al cliente finale. Secondo me nessuna trasformazione che sia digitale può prescindere dalle persone, il vero sforzo di tutti è avere la giusta passione e la corretta comunicazione affinché i timori legati al cambiamento si assopiscano. Bisogna sicuramente fare attenzione alla bulimia dei dati, è importante un’identificazione delle informazioni significative a livello di business e sostenibilità ambientale. Sul tema governance non possiamo prescindere dall’avere qualche illuminato all’interno, che tutti percepiscono come elemento di differenziazione a cui le stesse persone ispirarsi. Senza, qualsiasi progetto fallisce. Occorre avere l’illuminazione e l’impegno e il contributo finanziario per una trasformazione che tenga”.
In fabbrica La Marzocco digitalizza assemblaggio e logistica
Ritorniamo ad un mondo manifatturiero tradizionale con una chiara visione del paradigma 4.0 con interventi forti che coinvolgono produzione e logistica. La Marzocco è un’azienda toscana che costruisce e vende macchine da caffè per uso professionale ma anche domestico di lusso. Roberto Bianchi, Chief Operating Officer spiega “Ci siamo affacciati a questo mondo circa quattro anni fa e abbiamo declinato il progetto in tre parti: la priorità è stata dotarci negli stabilimenti produttivi di sistemi di video conferenza; la seconda quella di connettere i nostri prodotti per avere la possibilità di migliorarli, di fare manutenzione predittiva e di conoscere i nostri clienti finali; la terza gamma riguarda la produzione e la logistica”.
Il nome del progetto in questo caso è Artigiano 4.0. La Marzocco costruisce a mano le macchine da caffè che vengono spostate su carrelli nei vari reparti produttivi dell’azienda, quindi l’idea è stata lasciare al 100% la costruzione a mano dei progetti e vedere gli operatori un po’ come chirurghi che intervengono sull’assemblaggio e sulla costruzione con il supporto del digitale. Lo sforzo principale è stato quindi progettare l’infrastruttura affinché potesse essere utilizzata da persone anche non super competenti. La usability è stato il driver principale. Gli operatori sono stati dotati di i-Pad da usare nell’orario di lavoro e affiancati da applicazioni che li supportino dalla pianificazione all’avanzamento produzione consentendo di associare la propria fase di lavorazione al carrello su cui è disposta la macchina dichiarando se la macchina del caffè è pronta o ferma, dichiarare tempi di lavorazione e gli scarti, e usufruire di un buttone per condividere l’informazione. Una dashboard mostra lo stato di avanzamento della produzione in tutte le aree aziendali. In fase di costruzione, ci sono check list per guidare l’operatore nelle fasi di assemblaggio. Non tutti gli operatori sono formati alla stessa maniera, di conseguenza, la documentazione tecnica personalizza le fasi di assemblaggio, con un sistema che propone all’operatore di assemblare solo una determinata categoria di prodotti per cui è formato. Quello che si ottiene sono ottimi risultati nel coinvolgimento dell’operatore e nella riduzione degli scarti come dei tempi di assemblaggio.
La seconda parte riguarda la logistica: un paio di anni fa La Marzocco digitalizza l’arrivo dei materiali da parte dei fornitori con piattaforme 4.0 che interrompono la diffusione di bolle cartacee e riducono un sacco di errori di e tempo. Anche in questo caso, l’obiettivo è stato facilitare l’usabilità e ipotizzare un’infrastruttura hardware sensorizzando i colli di materiali che la logistica porta in produzione. Ogni scatola è equipaggiata con sensori RFID e passando nei varchi della fabbrica si può conoscere esattamente la posizione come quando l’operatore consuma il materiale, dichiara il vuoto e lì i sensori dichiarano l’informazione e la priorità di riempimento per ridurre il numero di mancanze. oggi questo sistema ci sta dando grossi vantaggi: i fornitori stanno allungando molto i tempi di consegna e lavorare sulla logistica ci sta dando tanti vantaggi.
La roadmap verso l’imballaggio 4.0 di Goglio
Dalle macchine del caffè ci muoviamo ai sistemi di imballaggio che hanno in buona parte a che fare con il business del caffè. Negli ultimi anni Goglio ha vissuto un significativo turn around dal punto di vista di fatturato e risultati, quali sono stati i pilastri di questa roadmap di trasformazione, in particolare dal punto di vista della leva digitale?
“Non c’è un percorso di digital transformation che possa esaurirsi nell’ambito di un singolo progetto o intervento per quanto possa essere ampio e trasversale e non si costruisce dall’oggi al domani. Ci vuole visione e una capacità di progettare in ottica triennale e un Project Manager, una governance complessiva che faccia convergere gli interventi verso gli obiettivi strategici dell’azienda” spiega Luciano Sottile, General Manager Goglio.
Goglio è una multinazionale italiana del confezionamento con base ad Arese. Conta 1800 persone e un fatturato al 2020 di 350 milioni con un piccolo calo rispetto all’anno prima, 8 stabilimenti e 7 uffici commerciali. Il 50% del fatturato appartiene al mondo del caffè e Goglio si occupa sia della costruzione delle macchine che della produzione dei materiali di confezionamento. Il fatturato delle macchine nel complesso del gruppo non è preponderante, però quando Luciano si è inserito in società, il passo è cambiato e ci si è dotati di una roadmap precisa.
Sono sostanzialmente quattro i pilastri su cui si è poggiata la journey to 4.0 di Goglio. Il primo step ha riguardato l’ottimizzazione dei processi abbracciando logiche lean partendo dall’ufficio tecnico dove tradizionalmente la resistenza al cambiamento è maggiore per poi estendere l’azione nell’ambito logistica e produzione.
Il secondo pilastro del turn around è stato l’evoluzione del modello di business che dal vendere la macchina di imballaggio e i pezzi di ricambio annessi, ha sposato la logica della servitization: non più la macchina come focus principale di vendita ma la macchina come base per innestare servizi a valore aggiunto possibilmente crescente.
Il terzo elemento del programma di cambiamento è stato quello delle tecnologie abilitanti. La più utile e funzionale al business è stata l’Internet of Things direttamente collegata alla servitizzazione. Oggi Goglio ha 100 impianti collegati h24 che restituiscono dati di efficienza della macchina, resoconti produttivi, analisi di manutenzione, alert attivi che ci informano sullo status e le performance delle macchine, dati di telemetria analizzati e conservati per analisi successive. Qualche anno fa, si è dotata di una piattaforma IoT commerciale per poi sostituirla con una completamente proprietaria più funzionale ai suoi obiettivi.
L’ultimo elemento del sistema è il fattore umano sotto l’aspetto delle competenze e della motivazione. Goglio si è concentrata sia sull’acquisizione delle competenze, cercando poi di mantenerle all’interno dell’azienda, che sulla ricerca di competenze in società esterne pronte per essere utilizzate. Oggi il contenuto di informatica cresce sempre di più. E poi, quando si introducono tecnologie e modalità nuove di lavorare il problema è sempre quello di superare la resistenza agendo sui fattori che la determinano, una è la paura dell’ignoto. Per far sì che le persone avessero un comportamento più aperto e collaborativo abbiamo cercato di capire cosa significasse per noi trasformazione digitale. Il risultato conseguito è questa digital joruney.
Il “pay per pack” è una forma avanzata di rapporto tra produttore e utilizzatore che nel nostro settore è prematuro, ma si sta andando in quella direzione. Sicuramente servono visione, sviluppo di competenze e dell’organizzazione per arrivare al modello competitivo del futuro.
“Nel nostro caso – continua Sottile – i dati raccolti dalla piattaforma IoT sono a disposizione nostra e dei clienti. Il problema è far sì che il cliente percepisca il valore di questi dati. Ci risulta facile costruire servizi a valore aggiunto che, al livello più alto, sono rappresentati dal full service dove il cliente paga solo in funzione del prodotto che è riuscito effettivamente a produrre e immettere sul mercato. Nella nostra esperienza, questa mentalità ha portato ad efficienze di linea dal 60% all’80-85%, percentuali che rendono il cliente più propenso a pagare. Questa è la direzione per evolvere i nostri servizi al cliente”.
Dal tessile al digitale al food: il fil rouge è la contaminazione 4.0
Last but not least, una testimonianza che aiuta a capire come le tecnologie digitali e il paradigma 4.0 possano costituire la spina dorsale di diversi settori di business. Al centro, il tema della contaminazione positiva tra diversi business che dal mondo del tessile sbarca in quello alimentare per efficientare il processo e il servizio, anche in un periodo così complicato come quello che abbiamo vissuto e continuiamo a vivere tutt’ora che richiede a tutte le aziende anche e soprattutto la capacità di reinventarsi in tempi rapidi.
A raccontarsi è Luca Bondioli, CEO 1177 & Ciocomiti “La nostra azienda nasce nel 1982 con un business consolidato nel distretto della calza. Abituata da sempre a pensare fuori dagli schemi, nel 2014 iniziamo a realizzare prodotti tessili innovativi. Ci inventiamo il primo sistema di pagamento digitale per le vending machine, colleghiamo poi un robot umanoide nel 2017 chiamato Pepper, un’e-commerce fisico dove si poteva comprare il prodotto ed essere seguiti come dall’assistente digitale perché sia la macchina che Pepper parlavano 19 lingue. Nel 2019 quando abbiamo iniziato a posizionare le prime macchine, i primi sentori di Covid ci hanno portato a rallentare ma altri imprenditori contemporaneamente ci chiedevano come l’avevamo fatto e di replicarlo per altre aziende. 1177 ha così iniziato a progettare altri dispositivi come soluzioni di pagamento o self order o sistemi di digital signage, per una smart communication finendo per acquisire un system integrator per realizzare le tecnologie in casa”. Ricerche
Tutto questo mondo digitale che cambia in modo veloce ha contaminato positivamente l’azienda tessile rendendola ancora più agile. Tanto che nei 15 giorni di piena pandemia su richiesta della provincia di Brescia e Mantova, 1177 è riuscita in tempi brevissimi a riconvertire la produzione alle mascherine per tamponare la mancanza di un prodotto vitale sfornandone circa 500 mila. Ma non era quello il core business, così cessata l’urgenza, 1177 passa allo sviluppo di termoscanner, sistemi di accesso e di sanificazione.
Parallelamente nel 2017 da temperatrice in un garage di un bar, l’azienda Ciocomiti inizia ad evolvere e in 1 anno e mezzo guadagna 500 mila euro di fatturato. Da lì la decisione di usare il modello 1177 applicato al mondo del food eliminando gli errori del tessile ma applicando l’impronta digitale. Nasce il brand che apre i primi punti vendita a Madonna di Campiglio in Trentino nella Val di Sole grazie anche all’investimento di Trentino e Sviluppo che ha permesso di rispettare i parametri ambientali nella costruzione delle strutture.
Come aggiunge Bondioli “La logica Artigiano 4.0 de La Marzocco l’abbiamo sposata in pieno: facciamo una trasformazione a freddo con macinatura da 70 a 120 ore e la portiamo dopo 2 mesi a raffinare a 2200 metri. Essendo artigiani, potevamo sbagliare qualcosa nel processo generando problemi di qualità del cioccolato o di estrusione del burro di cacao. Allora abbiamo creato un algoritmo per standardizzare la qualità dei lotti e ricavare tutti i dati per un cioccolato perfetto“.
Lo scorso anno la parte tessile ha perso il 25%, la parte digitale ha mantenuto il fatturato, la parte del food ha fatto +48%. Secondo le aspettative di quest’anno: la parte digitale triplicherà, ci sarà una crescita nel food e il tessile manterrà. E’ proprio grazie alla contaminazione che è stato possibile dare linfa e trasmettere motivazione all’interno dell’azienda quando i negozi di abbigliamento sono stati costretti a chiudere, lavorando ad altri progetti che ci permettono di restare in piedi.
Immagine fornita da Shutterstock