Nell’era dell’Industria 4.0 l’attenzione si è letteralmente spostata dall’hardware al software: la possibilità di connettere i macchinari tra di loro e con i sistemi IT aziendali, grazie all’Industrial Internet of Things (IIoT) e all’Intelligenza Artificiale (AI), permette alle aziende non solo di abilitare numerosi vantaggi in linea, ma anche di offrire nuovi servizi ai clienti e raggiungere nuovi segmenti di pubblico.
Il tema della convergenza tra i mondi IT e OT rappresenta uno dei mantra di questo paradigma: difatti, è proprio l’unione di questi due ambienti – che tradizionalmente venivano gestiti da tecnologie e competenze diverse – a rappresentare un fattore chiave per le aziende che vogliono raggiungere obiettivi di trasformazione digitale. Se da un lato la consapevolezza dei vantaggi di questa integrazione, legata a una maggiore visibilità, produttività degli impianti e flessibilità nella produzione, si sta sempre più diffondendo tra le aziende, è altrettanto vero che per tante altre rappresenta ancora una sfida.
Per questo l’industria si muove sempre di più verso un approccio all’innovazione standardizzato e aperto, basato su standard comuni per creare sistemi indipendenti dall’hardware. E quindi la sfida che si trovano davanti i fornitori di tecnologie è quella di creare soluzioni “a prova di futuro”, in grado non solo di rispondere alle esigenze di oggi, ma di anticipare anche quelle di domani, permettendo una più facile scalabilità e integrazione tra sistemi.
Sfide e opportunità di cui si è discusso nel corso dell’approfondimento speciale dal titolo “La sfida della convergenza tra IT e OT e le nuove frontiere dell’automazione” nell’ambito dell’Industry 4.0 360 Summit, l’evento digitale organizzato da Innovation Post, Industry4bisuness e ESG360, tre testate del network Digital360.
Indice degli argomenti
Il 4.0 si fa con l’integrazione fra IT e OT, ma parliamo ancora di una sfida
La consapevolezza che investire nelle tecnologie digitali e nell’automazione non sia solamente vantaggioso, ma necessario per restare competitive in mercati sempre più in rapido cambiamento e per reagire proattivamente a eventi disruptive, si è ormai diffusa nell’industria. A dimostrarlo sono i dati di mercato, come quelli diffusi all’Osservatorio Transizione Industria 4.0 della School of Management del Politecnico di Milano, che anche nell’anno più critico della pandemia (2020), nonostante i fermi produttivi e nonostante la crisi delle supply chain, hanno rilevato una crescita nel mercato dell’Industria 4.0 che è arrivato a superare il tetto dei 4,1 miliardi (+8% sul 2019).
E gli investimenti delle aziende si sono concentrati soprattutto in quelle tecnologie che abilitano la raccolta e l’utilizzo dei dati, quindi l’Industrial Internet of Things (che con un valore di 2,4 miliardi di euro ha rappresentato il 60% della spesa) e l’Industrial Analytics, che ha rappresentato il 17% della spesa totale, con 685 milioni di investimenti.
Stante questa maggiore consapevolezza che si concretizza in una chiara destinazione del budget aziendale, quando parliamo di convergenza tra IT e OT dobbiamo ancora parlare di sfide e dobbiamo farlo perché non tutte le aziende hanno adottato strategie di digitalizzazione di successo che hanno portato all’unione di questi due ambienti.
A dimostrarlo un recente rapporto del McKinsey Global Institute che ha analizzato lo stato dell’arte dell’IoT industriale nella manifattura. Secondo il rapporto, nell’ambito manifatturiero – dove l’IoT ha maggiore potenziale di generare valore – nonostante molte aziende stiano avviando progetti di trasformazione digitale, il 70% di quelle che hanno tentato di implementare l’IoT su larga scala non riescono ad andare oltre i progetti pilota.
Una situazione causata da diversi fattori, a partire proprio dalla presenza di impianti brownfield con attrezzatture eterogenee basati su standard diversi e alla presenza di sistemi legacy rigidi e altamente customizzati che ne complicano l’implementazione.
Come è cambiato il ruolo del software nel ciclo di vita della linea produttiva
Ad essere cambiato nel tempo, è l’approccio all’automazione della linea. Come spiega Lorenzo Zerbi, Responsabile Product and Segment Marketing di Bosch Rexroth “Tradizionalmente, sviluppare una linea di automazione industriale richiedeva un susseguirsi di attività e fasi, prima l’ingegneria meccanica, poi l’ingegneria elettrica ed elettronica ed infine, la parte dedicata allo sviluppo del software, inteso come sviluppo del codice macchina, quindi dire alla macchina cosa deve fare, che processo deve eseguire per poi metterla in produzione”.

“Oggi questo paradigma è totalmente cambiato, il software entra in tutte le fasi del ciclo di vita della macchina, fin dalla fase di ingegnerizzazione, dove vado a sviluppare il design della linea completamente in un mondo virtuale e quindi mi permette ridurre la possibilità di errore, i costi e i tempi di implementazione della linea”, aggiunge Zerbi. Ma il software lo si può utilizzare anche nello sviluppo del codice macchina direttamente nel mondo virtuale riducendo le operazioni di debug e quindi, con la possibilità di verificare che la linea si comporti come desiderato. Anche i tempi di settaggio e quindi di time-to-market sono brevissimi.
E quando la linea è operativa, i software di automazione permettono di monitorare la produzione, rendendola più efficiente e flessibile ai bisogni dell’azienda anche grazie ad algoritmi di intelligenza artificiale. Il software è presente in tutte le fasi e soprattutto quello che viene dal mondo IT che sta convergendo verso il mondo dell’OT apre tutta una serie di nuove possibilità e servizi per migliorare le performance produttive.
Vantaggi che però si scontrano, come già accennato, con le difficoltà legate all’hardware, con controllori che ancora non sono concepiti per queste attività e questi servizi. “Spesso – prosegue Zerbi – assistiamo al proliferare di ulteriori hardware, che complicano eccessivamente la linea. La sfida per i fornitori di tecnologie è dunque quella di introdurre nuove piattaforme di automazione industriale che siano flessibili, in grado di integrare questi software che arrivano dall’IT, mantenendo il programmatore nella sua area di comfort, ossia nei linguaggi di programmazione, che non vengono oggi utilizzati tantissimo nel mondo IT ma sono propri del mondo OT”.
L’ecosistema ctrlX Automation per integrare l’IT in fabbrica
Ed è proprio quello che ha fatto Bosch Rexroth con ctrlX Automation, una piattaforma aperta che incarna le esigenze del mercato e si ispira al sistema di app per gli smartphone, rispondendo ai requisiti fondamentali praticamente per tutte le applicazioni industriali.
Una piattaforma flessibile, in quanto permette – proprio come il sistema dell’app store per gli smartphone – di sviluppare e installare le piattaforme utili ai bisogni dell’azienda, indipendentemente dall’hardware utilizzato. Nuovi controllori dovranno svincolarsi dalla parte di hardware e dare la possibilità di installare come lo smartphone delle app mantenendo le funzioni necessarie.
Questo proprio perché si tratta di una piattaforma aperta, che può contare su un vero e proprio ecosistema di partner, ognuno con il proprio know how, in grado di portare conoscenze legate ai nuovi linguaggi di programmazione all’interno della linea. I controllori di domani dovranno saper apprendere e utilizzare questi altri linguaggi di programmazione, dando spazio al programmatore e portare il proprio know-how all’utente finale che lo importerà all’interno della propria linea.
E con un occhio particolare alla sicurezza, aspetto importantissimo per le aziende che devono poter contare su soluzioni in grado di resistere ad attacchi cibernetici esterni. “Parliamo tutti i giorni di IIoT, – spiega Zerbi – ma i nuovi controllori dovranno essere pensati nativamente con certificazioni legate al mondo dei router, dell’IT piuttosto che del mondo dell’automazione industriale, di modo da esporre il dato in modo sicuro”.
ctrIX challenge: coinvolgere giovani e nuove realtà per gestire l’integrazione IT-OT
Necessità che hanno spinto Bosch a creare un ecosistema aperto anche ai giovani sviluppatori, per raccogliere le idee più innovative. Proprio a questo è rivolta la ctrlX challenge, una sfida che invita sviluppatori italiani e internazionali a presentare idee creative che si basano sulla piattaforma di controllo ctrlX Automation. Idee che saranno poi sviluppate in applicazioni innovative per il controllo industriale.
Vision System è tra quelle software house che sono state selezionate per passare alla seconda fase della challenge. L’azienda non opera come un classico integratore, ma fornisce supporto ai processi di R&D delle aziende per permettere il salto di qualità ovvero garantire competività in un mercato che si muove con cicli di innovazione sempre più brevi tipici dell’IT e delle startup. Tuttora la norma nel mercato dell’automazione, per questo cerchiamo di spingere su sistemi di integrazione per la maggior flessibilità possibile.
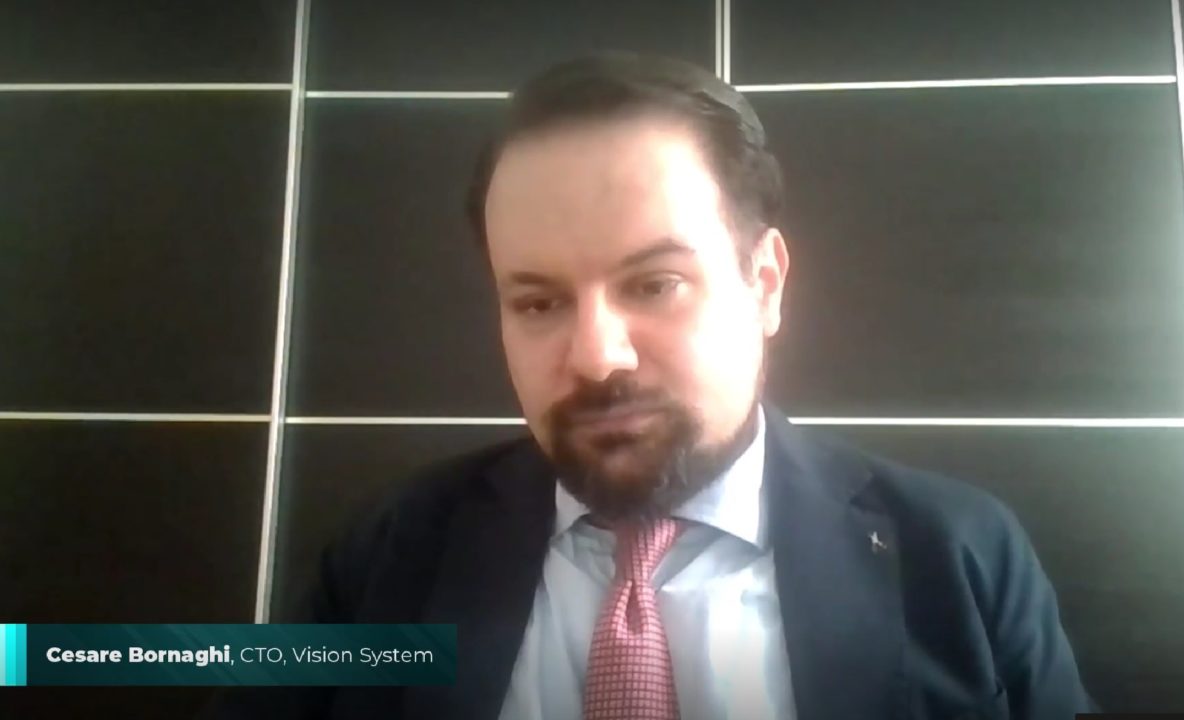
“Abbiamo partecipato – commenta Cesare Bornaghi, Chief technology Officer di Vision System – inserendo alcune delle nostre librerie nella ctrIX, che è di fatto un sistema evoluto basato su Linux, e questo ci ha permesso di integrare fermo divisioni e intelligenza artificiale per rappresentare un processo di automazione legato al controllo e alla gestione della visione in ambito industriale. Senza ctrIX non saremmo riusciti in tempi brevi a integrare protocolli strettamente legati all’IoT”.
“Nel futuro dell’automazione, – continua Bornaghi – il vantaggio tecnologico passerà necessariamente per nuove figure e realtà in grado di supportare end user e OEM sulla scelta del processo e non solo del prodotto. Il livello di integrazione sarà guidato da chi avrà la competenza per veicolare un determinato prodotto e potrà inserire questa competenza come valore aggiunto nel prodotto. Queste tecnologie sono legate all’AI, alla computer vision, ma anche all’IoT. Il fatto che Rexroth abbia promosso questa challenge è indicativo del fatto che l’azienda abbia compreso il bisogno di queste dinamiche e anche la necessità di attirare sempre più idee innovative anche dall’esterno”.
I vantaggi per i costruttori di macchine: la testimonianza di EDF Europe
I vantaggi sono sia per gli end-user (in questo caso le aziende) che per i costruttori di macchine. Lo sa bene EDF Europe, azienda che opera nella produzione di scatole in cartone ondulato. Un settore molto competitivo, dove i macchinari oltre a dover avere una elevata capacità produttiva devono essere molto più flessibili rispetto alle convenzionali linee di produzione industriali, nel senso che devono essere in grado di commutarsi in pochissimi minuti da una configurazione produttiva all’altra.
Si passa da una scatola di una determinata dimensione, ad una estremamente opposta in pochissimi minuti. E nonostante le linee siano automatizzate, nel caso in cui una scatola venga prodotta per la prima volta, obbliga l’operatore a intervenire su svariate regolazioni che in un primo avviamento terranno ferma la linea per parecchi minuti.
Per questo, “Il nostro primo obbiettivo – racconta Graziano Galletti, CEO di EDF Europe – è stato quello di cercare di capire quale fossero tutte le attività dell’operatore per ogni singola regolazione e messa a punto, tutte diverse al variare della tipologia di scatola, con la finalità di poter creare dei modelli tipici di set up da abbinare alle infinite variabili di prodotto”.

EDF Europe è riuscita, grazie a ctrlX Automation di Bosch Rexroth, a costruire il sistema di raccolta e informazione volto ad ottimizzare il processo produttivo, riducendo il carico di lavoro per gli operatori. Grazie alle app presenti nell’ecosistema di Bosch, l’azienda ha prima potuto raccogliere tutti i dati necessari dalla parte logica della macchina, gestirli, inviarli nel cloud ed elaborarli.
Così ha memorizzato tutte le azioni svolte dall’operatore – come quali pulsanti preme, oppure quale parametro cambia, abbinate alla dimensione della scatola o della tipologia di cartone utilizzato – ed evidenziato quelle azioni caratteristiche per tipologia di scatola prodotta, che invece di essere lasciate a totale discrezione dell’operatore vengono già suggerite dal sistema, alleviando quindi il carico di lavoro relativo alla messa a punto.
Grazie a queste analisi, l’azienda ha potuto offrire ai clienti delle linee produttive che non necessitano di elevati tempi di avviamento, elevando il ruolo dell’operatore a quello di supervisore, lasciando alla macchina il compito di suggerire la taratura corretta anche su scatole mai prodotte in precedenza. Attualmente il sistema è scalabile, pronto per nuove soluzioni.
“Ogni macchina installata da un nostro cliente, continua a fornire dati che permettono di far crescere il data base con tutte le informazioni necessarie a permettere nuove analisi che a loro volta generano nuovi miglioramenti; quindi, le nostre macchine saranno in grado di ricevere continui aggiornamenti per la totale durata della loro vita”, conclude Galletti.
Superare l’obsolescenza programmata dell’hardware per incontrare anche la domanda di sostenibilità
Di idee e competenze ci sarà sempre più bisogno nel futuro, perché se è vero che tante aziende sono ancora all’inizio del loro percorso di digitalizzazione, o non lo hanno ancora portato a termine, è altrettanto vero che il progresso tecnologico non si ferma (non a caso si inizia già a parlare di Industria 5.0). Tutto questo si aggancia a un altro aspetto centrale in tutto il PNRR: la sostenibilità in un’ottica di riduzione dei rifiuti e allungamento del ciclo di vita dei beni.
Allo stesso tempo, tuttavia, il prodotto deve anche essere efficientato per garantire un ridotto consumo di energia, favorendo la transizione verso un’economia circolare. Sfide che le aziende e gli OEM si trovano ad affrontare per abilitare quei vantaggi – in termini di flessibilità, riduzione dei costi, sostenibilità e personalizzazione dei prodotti – che devono poter offrire ai propri clienti per restare competitive sul mercato.
“I nuovi controllori e le nuove piattaforme di automazione industriale devono venire in soccorso con la possibilità di integrare app in un controllo già esistente. Io ho la mia linea che produce nel migliore dei modi, tra un paio d’anni andrò a integrare l’app 5G e la mia linea in poco tempo sarà attualizzata ad un nuovo standard. E’ il future proof dell’investimento – spiega Zerbi di Bosch Rexroth – Dall’altro lato, abbiamo nuove capacità computazionali dei controllori che continuano ad evolversi. Io porto tutta la mia customizzazione dal vecchio al nuovo, ma mi aspetto che mi dia la possibilità di concentrarmi solo ed esclusivamente sullo sviluppo del software, senza preoccuparmi dell’hardware. Con un nuovo processore, potrò migrare il software sul nuovo hardware”.
Sicuramente guardando al futuro, il software costituisce un aspetto critico soprattutto nel calcolo del valore aggiunto. Come osserva Bornaghi di Vision System “Le software house sono sempre più attente agli aspetti legati alla maintenance e alla proprietà intellettuale. In un ecosistema con tempistiche più strette, in cui è richiesto un rapido adattamento e una maggiore flessibilità, è indispensabile garantire supporto e aggiornamenti sulla base di piattaforme sempre più automatizzate e semplici. ctrIX permette di pacchettizzare l’applicazione e gestire aggiornamenti e rilasci in una prospettiva di continous integration tipica dell’IT“.
Spesso nell’ambito dell’automation ci sono software con tempi di vita di decine di anni e dopo vent’anni risulta impossibile attingere dal mercato risorse umane con competenze legacy e questo crea ai recruiter e ai tempi di vita e alla possibilità di mantenere le macchine grossi problemi. Per questo, un approccio a prova di futuro è sicuramente garantito non solo da un processo legato al software, che deve avere un canale di mantenimento specifico, ma anche garantito in un’ottica di sostenibilità da sistemi che possono essere sostituiti; nel senso che a parità di software, l’hardware può essere flessibilmente cambiato.
“ctrIX – continua Bornaghi – ha una piattaforma di virtualizzazione che permette alle nostre app di visione di viaggiare all’interno di questi container. L’assorbimento di ctrIX o di un edge computer permette di risparmiare anche in ottica di rispetto dell’ambiente e quindi il consumo energetico di una macchina abbattuto sulla parte di small processing anche del 30-40, a volte del 60%”.
Lontano dall’hardware e sempre più verso il software: i vantaggi della servitization
Il cambiamento del focus porta vantaggi non solo ai consumatori finali, ma anche ai produttori di macchine che possono sfruttare i dati raccolti dalle macchine installate presso i clienti sia per migliorare la macchine stessa, che per offrire nuovi servizi di business. Lo spostamento del baricentro del prodotto verso la parte software apre un’infinita possibilità di nuovi servizi da proporre alla propria clientela.
La raccolta e l’analisi dei dati consente di far crescere la macchina nel tempo, generando nuovi modelli di lavorazione in grado di aiutare l’operatore a raggiungere nel minor tempo possibile la miglior performance della linea, oltre a ridurre in maniera drastica tutti i tempi di avviamento. Un vantaggio che, come spiega Galletti, “è ben percepito dal cliente, che è disposto a pagare per avere questa scalabilità della prestazione e della riduzione dei tempi morti”.
Un altro vantaggio enorme è il rapporto costo-beneficio nello sviluppo delle nuove macchine: avere una macchina completamente controllata e connessa inclusa la conoscenza rispetto a quello che fa l’operatore, consente di accelerare enormemente la creazione di nuove soluzioni e abbatterne il costo.
Per EDF Europe, l’ecosistema di automazione di Bosch ha aperto la strada a un nuovo modo di essere connessi alle macchine, con la sicurezza che qualsiasi saranno le evoluzioni future della tecnologia, basterà aggiornare il software o scaricare una nuova app per avere una macchina che rappresenta lo stato dell’arte. “Per noi sarà questa la vera rivoluzione nell’ambito industriale”, osserva Galletti.
Il vantaggio si estende anche agli operatori, che possono avere una nuova esperienza di controllo del macchinario, permettendo di dominare il processo in maniera meno fisica, ma molto più strategica e di supervisione. “Serve che la macchina – afferma Galletti – sia in grado di mettere in condizione chi opera di avere più momenti di soddisfazione che di stress, riducendo anche il rischio di incidenti e migliorando la sicurezza dei processi. Oggi è l’operatore che spinge la macchina, quando dovrebbe essere la macchina a far generare interesse all’operatore nello scoprirne i limiti operativi. In questo modo, possono crescere insieme”.
Processi che si ottimizzano anche nell’ambito del lavoro delle squadre: gli operatori possono comunicare eventuali difficoltà nel produrre un determinato prodotto direttamente attraverso l’interfaccia HMI della macchina, che la renderà disponibile in tempo reale alla squadra di supporto tecnico, che a sua volta potrà direttamente interagire. Allo stesso modo, l’interfaccia diventa anche uno strumento per i confronto e la condivisione di importanti informazioni riguardanti i processi produttori tra gli operatori impiegati nei vati turni.
“Tutto è quindi finalizzato al migliorare l’esperienza dell’uomo e conseguentemente aumentarne la propria sicurezza nell’ambiente lavorativo”, conclude Galletti.
Immagine fornita da Shutterstock