Nella produzione industriale, fino a poco tempo fa il mercato era presidiato da ecosistemi proprietari hardware e software che definivano la direzione dello sviluppo tecnologico, rallentando anche i processi innovativi. Negli ultimi anni si sono sviluppate tecnologie alternative caratterizzate da apertura e standardizzazione. Tecnologie agnostiche rispetto al produttore di macchinari consentono alle piccole e medie imprese italiane di intraprendere un percorso di digitalizzazione graduale anche in termini di investimento economico e di formazione. I principali vantaggi sono la possibilità di sfruttare il parco macchine esistente e di sviluppare un processo di trasformazione verso l’industria 4.0 a piccoli passi, cosiddetto “retrofit“, definendo gli specifici obiettivi di interesse, utilizzando esclusivamente i dati necessari a raggiungere quegli obiettivi e poter gradualmente valutare l’effettivo ritorno dell’investimento (ROI).
Indice degli argomenti
Perché è importante digitalizzare la produzione
La digitalizzazione industriale in ottica 4.0 parte dal monitoraggio della produzione mediante l’estrazione di parametri dai macchinari con l’obiettivo di efficientare la produzione stessa (calcolo del tempo ciclo, analisi in tempo reale della produzione con indicazione del rapporto pezzi/scarti, calcolo in tempo reale dell’OEE overall-equipmente-efficiency). Ma consentono anche e soprattutto di efficientare la manutenzione abilitando il passaggio da manutenzione preventiva a manutenzione predittiva e di ottimizzare la logistica interna ed esterna facilitando la migrazione verso metodologie di gestione della produzione on-demand e più in generale l’evoluzione verso una reale strategia di produzione Lean.
Come automatizzare il magazzino alimentare: meno errori, più velocità.
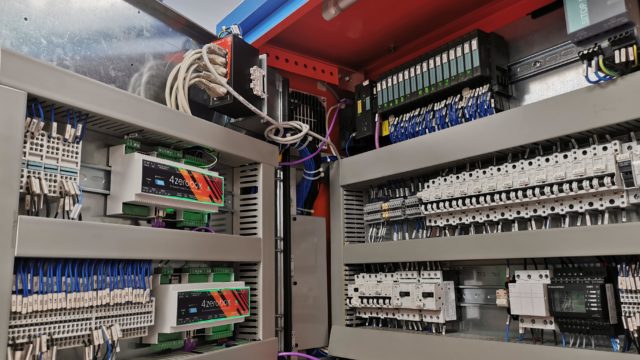
Esempio di inserimento di due moduli 4zerobox per acquisire i segnali dalla linea di collaudo
I macchinari industriali nelle PMI italiane: green e brown field
La stragrande maggioranza delle piccole e medie imprese italiane ha un parco macchine che ha in media più di 10 anni di vita. Una macchina di 10 anni non è però considerabile come obsoleta, anzi, è spesso ben performante in termini di capacità produttiva ma non dispone di sistemi di controllo tali da consentirne l’interfacciamento con i moderni sistemi 4.0.
La sostituzione in toto di questi macchinari non è sostenibile da parte della maggioranza delle PMI italiane, anche perché è particolarmente difficile prevedere il ritorno dell’investimento. L’alternativa alla sostituzione è il retrofit dei macchinari industriali ancora performanti aggiungendo nuove funzionalità in modo poco invasivo. Il retrofit abilita così i macchinari a funzionalità tipiche dell’industria 4.0, come la raccolta dei dati di produzione, l’elaborazione dei dati stessi e la produzione di KPI necessari a migliorare l’efficienza dell’intero processo produttivo.
Per comprendere processi e tecnologie necessarie al retrofit, è importante definire i diversi tipi di macchinari: green field, brown field con PLC e brown field senza PLC.
I macchinari “green field” sono macchinari moderni, pronti per le tecnologie e le connessioni 4.0 e quindi in grado di inviare dati a sistemi gestionali e di ricevere “ricette” di produzione e parametri di configurazione. Spesso sono associati a sistemi gestionali proprietari ma sono in genere configurabili per interfacciarsi anche con sistemi software e cloud di terze parti
I macchinari “brown field” sono invece macchinari datati che non hanno capacità di collegarsi a sistemi gestionali 4.0 mediante i moderni protocolli di comunicazione (ad esempio: macchine a controllo numerico CNC, robot industriali, celle di montaggio automatizzate, sistemi di piegatura metalli robotizzati, etc.). Alcuni di questi macchinari, i più moderni, sono dotati di PLC (Programmable Logic Controller) dei computer industriali che controllano la macchina andando a gestire il ciclo di lettura sensori e controllo attuatori. I PLC hanno solitamente porte di connessione digitali che in teoria ne permetterebbero l’interfacciamento con altri sistemi e quindi l’estrazione dei dati.
Purtroppo, però, spesso il possessore del macchinario non conosce il protocollo usato dal PLC per comunicare oppure è limitato dal fatto che il PLC comunica grazie a protocolli proprietari che quindi non sono utilizzabili per l’interfacciamento con sistemi 4.0 di terze parti. Esistono poi macchinari brown field più datati che spesso non hanno neanche un PLC e che quindi sono gestiti da sistemi di automazione elettromeccanica che non hanno porte digitali e che quindi non sono in nessun modo collegabili a sistemi gestionali moderni (tipicamente: torni, frese, taglierine, nastri trasportatori, pompe, compressori etc.)
Macchinari green e brown field possono essere digitalizzati attraverso dispositivi come lo 4ZeroBox di Zerynth che consentono il retrofit dei macchinari industriali. Tale dispositivo consente di fare interagire il mondo dell’OT (Operation Technology, i sistemi di comunicazione di fabbrica) di interfacciarsi con il mondo IT (Information Technology, il mondo delle connessioni Internet e della tecnologia cloud) per creare un “gemello digitale” di qualsiasi macchinario industriale anche obsoleto attuando quindi una strategia di retrofitting per il 4.0.
Retrofit di macchinari obsoleti per l’efficienza dei processi
Un esempio di retrofit applicato a macchinari brownfield è quello dell’acquisizione dati da presse per iniezione plastiche. Tipicamente queste macchine hanno una vita media molto superiore ai 10 anni e nel nostro Paese la maggior parte di questi macchinari ha quindi più di 5 anni di vita. Queste macchine sono tipicamente controllate da PLC programmati dal produttore con codice chiuso e scambiano dati solo ed esclusivamente attraverso porte e protocolli proprietari.
L’azienda di produzione che utilizza questi macchinari ha tipicamente i seguenti bisogni:
- monitorare la produzione (pezzi prodotti per lotto, tempo ciclo, etc);
- monitorare i consumi energetici (kWh medi per lotto e per pezzo, picchi di consumo, anomalie di consumo elettrico, etc.);
- monitorare i parametri operativi della macchina (temperature di iniezione e del sistema refrigerante e lubrificante, settaggi macchina da acquisire per essere associati al lotto di produzione, quantità di materia prima utilizzata per lotto/pezzo).
In Zerynth abbiamo resto smart e 4.0 le presse da iniezione plastica andando a monitorare il consumo energetico direttamente nel quadro elettrico dell’azienda mediante l’uso di pinze amperometriche non invasive. Per il monitoraggio delle temperature abbiamo invece installato delle sonde di temperatura sulle tubazioni del sistema refrigerante e del lubrificante e sulla testa di iniezione. Abbiamo poi monitorato alcuni segnali dei sensori già installati dalla macchina andando a leggerli in parallelo al PLC. Con questi segnali siamo stati in grado di ricostruire gli eventi principali del ciclo di produzione e calcolare quindi il tempo ciclo per pezzo e per lotto. Grazie alla misurazione dei dati di produzione si possono ridurre i costi e quindi si può raggiungere il risultato finale di un miglioramento dell’efficienza.
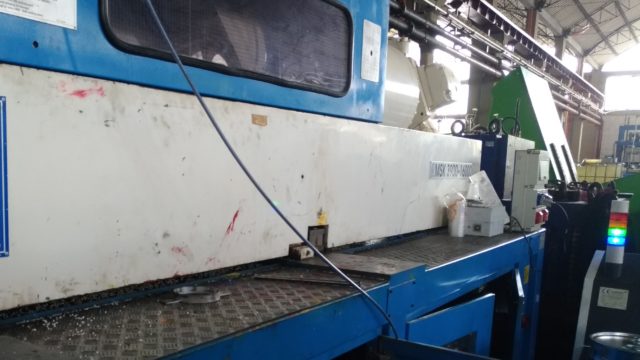
Un caso di “brown field”: pressa a iniezione plastica
Estrazione dati da macchinari moderni (4.0 ready) per la manutenzione predittiva
Nel caso di macchinari moderni, detti 4.0 ready, abbiamo invece la possibilità di acquisire direttamente i dati mediante protocolli di interfacciamento digitali che sono supportati nativamente dai PLC delle macchine. Siamo quindi nel caso detto green field.
In questo caso è comunque consigliabile, e spesso necessario, evitare di mandare i dati direttamente dal PLC al server aziendale dove abbiamo costruito il data-lake (database di raccolta dati atto all’abilitazione di processi di analisi dei dati “data science”). Questo perché non è detto che tutti i dati prodotti dal PLC debbano essere mandati così come sono “raw data” nel data lake e soprattutto perché se abbiamo optato per un servizio di raccolta e analisi dati “on cloud” è sempre consigliabile evitare di inviare dati grezzi di produzione sulla rete pubblica (ciò che è sicuro oggi potrebbe non esserlo domani).
Quindi, anche nel caso di green field è necessario andare a inserire in azienda dei gateway di interfacciamento che scambiano dati con i PLC dei macchinari, facciano una pre-analisi e filtraggio locale (edge processing) e poi inviino al data lake aziendale o al SaaS cloud i KPI di alto livello, gli allarmi, e altri parametri di alto livello che devono essere progettati sulla base degli obiettivi di efficientamento aziendale identificati in fase di progettazione del percorso di digitalizzazione.
È questo il caso dei progetti di manutenzione predittiva, in cui abbiamo la necessità di elaborare localmente i dati ad alta velocità per identificare anomalie e derive nei segnali che daranno origine ad allarmi locali (molto veloci) al fine di consentire al reparto manutenzione e alla gestione della produzione di intervenire repentinamente. Al contempo questi dati vengono anche inviati al data lake o al cloud e quindi diventano una utile sorgente di informazione per il miglioramento degli algoritmi di predizione e abilitano l’analisi statistica degli eventi di guasto e quindi consentono di efficientare le strategie di manutenzione e di gestione della produzione.
Abbiamo lavorato a un percorso di questo tipo per l’azienda Vitesco Technologies Italy dove vari banchi di test realizzati in-house e dotati di moderni PLC sono stati interfacciati con il sistema 4ZeroBox che è stato programmato per analizzare in tempo reale i dati e produrre allarmi sulla base di soglie e parametri che possono essere aggiornati tramite il cloud e sono specifici di ciascun macchinario. I dati vengono inviati insieme agli eventi generati al cloud aziendale dove vengono eseguiti gli algoritmi di machine learning che periodicamente vanno ad aggiornare le soglie di intervento dei singoli 4ZeroBox associati a ciascun banco di test. Per maggiori dettagli si può leggere il case study di Vitesco.
Cloud as a service o in-house?
Tutte le aziende vorrebbero avere tutti i dati in house perché è ormai chiaro a tutti che i dati sono e saranno sempre più il vero asset del futuro. È altresì vero però che i beni di valore devono essere gestiti e trattati con attenzione altrimenti, da opportunità di crescita, possono diventare sorgente di problemi. La sicurezza informatica è al giorno d’oggi un tema che non è più possibile trascurare. Un sistema è considerato sicuro se il costo necessario per “bucarlo” è superiore al guadagno che si può ottenere avendo accesso ai dati in esso contenuto. È quindi chiaro che il concetto stesso di sicurezza è relativo, ciò che è sicuro oggi potrebbe non esserlo domani. È sempre bene quindi partire con soluzioni cloud based in cui la responsabilità e la competenza sulla gestione dell’infrastruttura informatica e di sicurezza è demandata ad esperti del settore. È però altrettanto necessario scegliere delle soluzioni che in caso di necessità consentano di migrare in maniera semplice ed efficace da una soluzione “cloud based” a una “on-premises” qualora l’azienda lo ritenesse opportuno.
Nella scelta cloud vs on-premises c’è anche da tenere in considerazione la questione della connettività Internet. Inviare dati grezzi prodotti da decine e centinaia di macchinari a un cloud richiede una banda che non sempre è disponibile in azienda, quindi nei contesti di industria 4.0 è preferibile l’uso di soluzioni ibride (cloud e on-premises) rispetto a strategia puramente cloud based dal momento che è poco scalabile e comunque costosa in termini di infrastruttura tecnologica. In futuro si prevede quindi la diffusione in ambito 4.0 di tecnologie “edge” dove i gateway e i sistemi di interfacciamento dei macchinari avranno capacità di analisi e processamento e, quindi, parte del calcolo sarà svolto direttamente a bordo macchina andando, da un lato, a ridurre la banda richiesta per l’invio dei dati al cloud e, dall’altro a estrarre dei dati derivati che se “rubati” non consentirebbero comunque al malintenzionato di poter risalire ai parametri di produzione attraverso un processo di ”reverse-engineering”.
Conclusioni
Le più recenti tecnologie IoT aperte e standardizzate consentono di fare retrofit di macchinari industriali moderni o più datati. Abbiamo sviluppato una tecnologia per il retrofitting di macchinari datati che consente, con un investimento ridotto e tempi di setup molto brevi, di connettere qualsiasi macchinario industriale a qualsiasi sistema gestionale o cloud aziendale, come descritto nel dettaglio nel Whitepaper Retrofit di macchine industriali.
Il retrofit consente quindi alle imprese manifatturiere italiane di medie e piccole dimensioni con macchinari green field e brown field di sviluppare un processo graduale verso l’industria 4.0, con bassi costi, brevi periodi di fermo macchina, allungando la vita dei macchinari presenti in azienda. Le PMI potranno quindi monitorare i KPI relativi ai principali obiettivi quali ad esempio l’efficienza della produzione, la riduzione dei costi operativi, il miglioramento della manutenzione e della previsione di possibili guasti, la riduzione degli errori umani con conseguente aumento della sicurezza. Non ultimo, naturalmente, la possibilità di velocizzare e monitorare le decisioni di business basate sulla raccolta di dati dai macchinari.
Diventa competitivo nell'era dell'Industria 5.0: Ecco le tecnologie per una Manifattura Intelligente