Come sostituire un controllore di area produttiva secondo i principi di innovazione tecnologica. Nel secondo decennio del nuovo millennio, chi scrive si è occupato di un progetto di revamping di un sistema MES (Manufacturing Execution System), il sistema informativo per le aziende manifatturiere, adibito al controllo di un’area specifica di produzione dell’azienda per la quale lavoravo allora. A metà anni ’90 infatti, l’azienda installò una linea di produzione, a elevata automazione, di suole per cingolati.
Questa linea fu realizzata da diverse società, una decina in tutto, ognuna responsabile per un gruppo di macchine che svolgevano la stessa funzione. Un’azienda genovese poi si occupò della produzione e dell’istallazione del MES. Dopo oltre 20 anni di onorato servizio si pose il problema di un aggiornamento profondo del sistema non avendo più la possibilità di ricorrere a interventi di assistenza sul vecchio sistema e avendo in programma la sostituzione del vecchio ERP CICS con il più moderno SAP.
Indice degli argomenti
Il flusso di produzione
Il flusso di produzione, piuttosto complesso, era composto dalle seguenti fasi di lavoro:
Prima fase: Taglio
La fase di taglio consentiva di realizzare la suola a partire da una barra profilata; la suola veniva “staccata” da una barra mediante una cesoia idraulica, sagomata e forata mediante una punzonatrice idraulica e i fori erano poi smussati attraverso l’utilizzo di una piccola macchina utensile in linea con le macchine oleodinamiche (linea di taglio suole TA).
Le suole prodotte (semilavorato) venivano pallettizzate automaticamente su pallets di ferro che venivano trasportati in automatico (a mezzo navette su via rulli motorizzati, LTP) e potevano essere stoccati in magazzini automatici inter-operazionali per le successive fasi di lavorazione sulla linea, oppure estratte dalla linea per effettuare lavorazioni esternamente.
Seconda fase: Bonifica / trattamento termico
La fase di bonifica (o trattamento termico) consisteva nel sottoporre le suole ai processi di tempra e rinvenimento attraverso un forno in due sezioni.
Le suole da trattare erano poi pallettizzate su pallet di ferro che provenivano dal taglio, dai magazzini o da lavorazioni esterne; i pallet venivano de-pallettizzati da un robot cartesiano (DEP), secondo i codici pezzo, prima dell’immissione nel forno di trattamento dopodiché le suole venivano immesse in forno, per mezzo di un trasportatore a rulli, raggruppate in cariche/lotti e trattate secondo ricette inviate dal MES.
Le suole trattate (uscite dal forno) venivano smistate da una “linea di trasporto” verso una macchina sabbiatrice (SAB) e un sistema di pallettizzazione e reggiatura (RE) che realizzava i pallet di prodotto finito; in alternativa la linea di trasporto poteva inviare le suole alla fase verniciatura.
Terza fase: Verniciatura
Le suole provenienti dal trattamento termico o da lavorazioni esterne venivano caricate a mezzo di un sistema automatizzato su una catenaria con ganci appesi (LTS, linea di trasporto suole) che le trasportava nel sistema di verniciatura ove venivano verniciate per immersione ed essiccate in un apposito forno a bassa temperatura, adatta alla vernice ad acqua.
Le suole verniciate venivano infine sganciate dalla catenaria e inviate a un sistema di pallettizzazione (PA7) e reggiatura (RE7) che realizzava i pallet di prodotto verniciato finito.
La topologia dei collegamenti fra le macchine è riportata nella figura sotto:
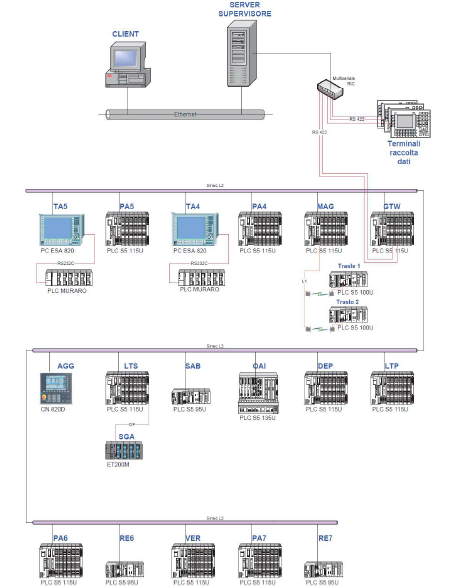
Analisi del sistema di revamping
Si trattava di una connessione Profibus via Sinec L2 con i componenti rete Siemens serie S5 che comunicavano al MES attraverso un PLC gateway per la rete Sinec L2 con lo scopo di coordinare la comunicazione tra il sistema MES e i PLC; il PLC gateway inoltrava infatti i messaggi del sistema MES verso i PLC e viceversa. Il sistema MES colloquiava con il PLC Gateway in rete Ethernet attraverso uno scambio di messaggi su canale socket TCP-IP. Il PLC gateway colloquiava con i PLC di automazione mediante messaggi AG/AG (Profibus FDL).
Si decise di procedere con il revamping della parte relativa a Server e MES, aggiungendo anche una rete industriale LAN con la più moderna tecnologia allora disponibile, ovvero Profinet su cavo Industrial Ethernet, collegato ai client operativi posizionati in ufficio di area e collegato anche a tre pannelli a PLC di controllo e monitoraggio dei dati di processo per ricavare l’indice di performance della linea (OEE), secondo il seguente schema:
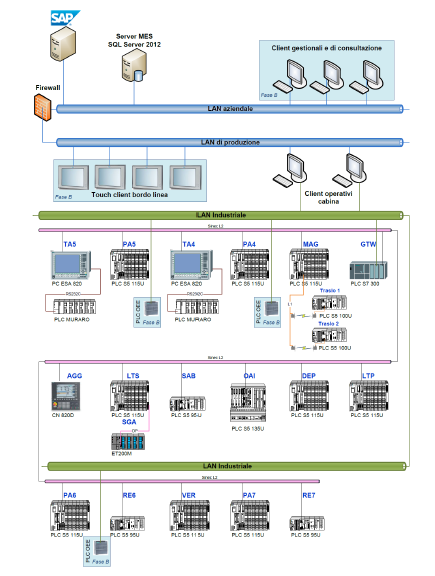
SAP
Il sistema ERP SAP assolveva ai compiti gestionali e amministrativi a livello aziendale.
Dal punto di vista dell’interfaccia con il sistema MES il sistema host:
- assolve ai compiti amministrativi, di gestione della produzione, logistica e rintracciabilità della Committente;
- gestisce la lista degli ordini di produzione e le relative fasi per ogni linea / macchina.
Server MES
Il server del sistema MES assolveva ai compiti di gestione della base dati del sistema e ai seguenti compiti di application server:
- i servizi di accesso alle applicazioni client;
- interfacciamento con SAP.
Reti
Lo schema di architettura (vedi sopra) prevedeva tre layer di rete:
- LAN aziendale: permette il collegamento dei personal computer in uso agli impiegati e ai responsabili della produzione;
- LAN di Produzione: permette il collegamento dei personal computer e dei dispositivi presenti nei reparti di produzione;
- LAN Industriale: permette il collegamento tra i client operativi del sistema MES e i dispositivi di automazione della linea.
Le reti erano tra loro isolate mediante firewall.
Di seguito vengono definite le macro-funzionalità previste per il sistema nelle fasi di revamping:
- Fase A: Revamping sistema MES con le funzionalità attuali;
- Fase B: Integrazione delle funzionalità di OEE e tracciabilità colate;
- Fase C: Integrazione in Ethernet dei dispositivi di automazione;
- Fase D: Integrazione macchine di verniciatura.
L’interfacciamento con SAP si realizzò mediante RFC (Remote Function Call) considerando un livello di real time di circa un minuto.
Interfacce SAP -> MES Interfacce SAP <– MES
Anagrafica articolo Avanzamento produzione per turno
Anagrafica operatori Consuntivazione dettagliata scarti
Turni e disponibilità macchine Consuntivazione dettagliata fermi
Dati ordini e conferme di produzione Consuntivazione dettagliata manodopera
Il grado di automazione e distribuzione delle informazioni raggiunto fu giudicato più che soddisfacente e per questo il nuovo MES fu approvato dopo circa sei mesi di attività in area.