Molta pratica, tanti progetti concreti e un numero considerevole di persone formate. Questo il bilancio dei primi due anni di attività del MADE, il Competence Center per Industria 4.0 situato presso il campus Bovisa del Politecnico di Milano (una struttura di circa 2.500 mq), tracciato da Marco Taisch, Presidente di MADE4.0. Il MADE, lo ricordiamo, è una realtà nata dal MISE (Ministero Italiano dello Sviluppo Economico), in grado di supportare le aziende manifatturiere nel processo di adozione delle nuove tecnologie, a prescindere dal livello di maturità digitale. In particolare con attività di orientamento, formazione e finalizzazione di progetti di trasferimento tecnologico. Come spiega Taisch “Non siamo sicuramente un laboratorio di ricerca, dal momento che tutto quello che si vede all’interno di Made 4.0 funziona davvero e le tecnologie che utilizziamo possono essere realmente comprate sul mercato. Per svolgere le nostre attività ci appoggiamo a 51 partner, ovvero le migliori aziende in Italia che fanno e vendono tecnologie per il 4.0, comprese società di consulenza e utilizzatori”.
Indice degli argomenti
I numeri di MADE dopo due anni
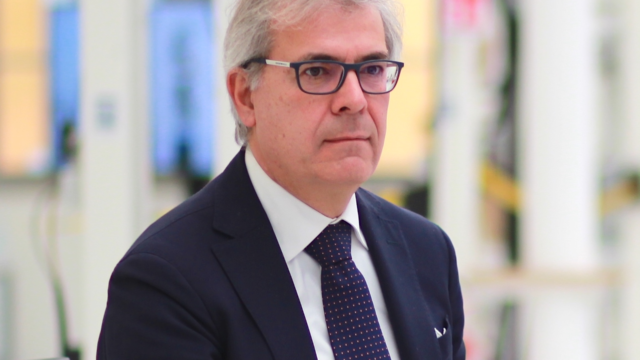
All’interno del Competence Center sono state implementate sei aree tecnologiche, in ognuna delle quali si sperimentano uno o più processi fondamentali del ciclo di vita di un prodotto e vengono trattati i temi legati all’Industria 4.0 in maniera pratica. In ognuna di queste aree sono presenti dimostratori tramite i quali è possibile vivere circa 90 “esperienze” per comprendere e toccare con mano le principali tecnologie che abilitano il manifatturiero digitale. Made ha dato vita anche alla Scuola di Competenze 4.0, dove è possibile apprendere le tecnologie, i metodi e i processi di produzione presenti nelle aree tecnologiche di Made, impararne le funzioni, e scoprire in prima persona i vantaggi di una fabbrica interconnessa.
In due anni questo doppio binario è stato sperimentato con successo al Made: innanzitutto sono stati organizzati 310 tra workshop e webinar, che hanno visto la partecipazione di 17.000 imprese e 6.000 imprese professionisti. Molto alti sono stati i numeri della Scuola di competenze, che ha visto ben 210 corsi erogati, 4000 partecipanti (per 1350 aziende) e 27.000 ore di formazione. Una scuola che – sottolinea Taisch – è basata sul concetto di teaching factory, dunque non prevede soltanto lezioni frontali nelle aule tradizionali, ma soprattutto l’impiego delle moderne tecnologie digitali, quali visori per la e macchinari connessi.
Ma il vero e proprio fiore all’occhiello del Made sono gli oltre 140 progetti realizzati nel biennio (non soltanto in Lombardia, molti anche al Centrosud), di cui 56 hanno beneficiato del finanziamento statale di 3,35 milioni di euro. Ad esempio questi progetti hanno permesso alle aziende di realizzare digital twin del proprio impianto, oppure di ridisegnare i propri processi in ottica snella e do lean manufacturing. O ancora di migliorare la salute e sicurezza sul lavoro, grazie all’utilizzo di robot collaborativi e sistemi di visione intelligenti, oppure di monitorare i consumi energetici interni.
Tecnologie chiave per restare sul mercato
“Abbiamo avuto circa 130 aziende contrattualizzate con questi progetti. Come le abbiamo intercettate? Un ruolo chiave è stato giocato dalle associazioni di categoria: in questi due anni abbiamo incontrate circa 850 aziende, le altre 700 imprese con cui non abbiamo avviato un progetto hanno probabilmente spesso preferito farlo in autonomia. Ultimamente siamo diventati anche molto attivi anche nei progetti europei, così da sviluppare nuovo know-how. In un anno e mezzo abbiamo partecipato 24 progetti, cosa che ci aiuta a finanziarci e rimanere aggiornati. Ad esempio siamo uno dei sette centri riconosciuti da Bruxelles per testare l’AI nelle imprese, unico caso italiano”. Eppure, l’opinione di Taisch è che questi numeri siano ulteriormente incrementabili, dal momento che molte aziende non hanno ancora ben messo a fuoco l’importanza di una rapida e sostenibile trasformazione digitale. “Io stesso, nel momento della presentazione del piano Industria 4.0 sostenevo che le tecnologie dovessero essere intese come un abilitatore della competitività d’impresa. Oggi invece il messaggio deve essere ancora più forte: senza queste tecnologie il rischio è di essere fuori dal mercato. Per questo motivo abbiamo nel nostro mindset l’obiettivo di aiutare le aziende a essere più competitive nel contesto internazionale. L’Italia è un Paese leader nel manifatturiero, ma non possiamo limitarci a essere solo dei follower”.
I trend di riferimento per il manifatturiero
Secondo il numero uno del Made, l’Italia potrebbe beneficiare di una serie di macro trend, tra cui il rientro di una serie di operatori industriali nel nostro Paese, come conseguenza delle difficoltà della logistica nel post pandemia. D’altra parte, però, la digitalizzazione è fondamentale per rispondere a esigenze ormai estremamente diffuse sul mercato quali la complessità crescente dei prodotti, la riduzione dei tempi di consegna e, naturalmente, la sostenibilità.
“Un altro trend importantissimo è quello dei servizi, non semplice per un tessuto industriale come il nostro abituato soprattutto a produrre cose. In futuro serviranno dei modelli di business fondati sulla servitizzazione e sul pay per use. L’imprenditore italiano è pronto a tutto questo? Insomma: per agire in quest’ottica questo serve lavorare sui dati, raccoglierli, sfruttarli e ricavarci informazioni. Industria 4.0 è soprattutto questo, non è dunque inserire robot in fabbrica”. Taish ha riservato infine una battuta sul tema degli incentivi di Transizione 4.0: “Ritengo un errore grave la riduzione delle aliquote, perché così non si aiutano quelle imprese che sono rimaste indietro, non poche, aumentando il gap tra leader e follower. Ancora più grave è aver tolto gli incentivi sulla formazione”.
Articolo originariamente pubblicato il 19 Gen 2023