Realizzare un magazzino a conduzione totalmente automatica secondo il concept di Industria 4.0 nell’ambito di un progetto di automazione improntato ai più moderni criteri di sostenibilità ambientale e di innovazione tecnologica: questa era la sfida di Orogel3. L’azienda, grande gruppo agroalimentare, ha lanciato il progetto Orogel3 a Cesena, dove si trova il più grande stabilimento fra i tre dedicati alla surgelazione dei vegetali. La necessità era quella di realizzare da un greenfield un magazzino molto grande – si estende infatti su una superficie di 14mila metri quadrati (per circa 230mila metri cubi di volume)-, in condizioni critiche, ossia che in esercizio a meno 25 gradi avrebbe dovuto conservare circa 40mila tonnellate di prodotto surgelato.
Orogel surgelati, una delle tre linee di prodotto, è oggi la prima realtà totalmente italiana del mercato dei vegetali surgelati e nel settore Food Service. È presente nelle zone più vocate in Italia con 12 stabilimenti produttivi e 30 centri di ritiro, così, i prodotti appena raccolti sono immediatamente lavorati, stoccati e confezionati, mantenendo intatta la loro freschezza.
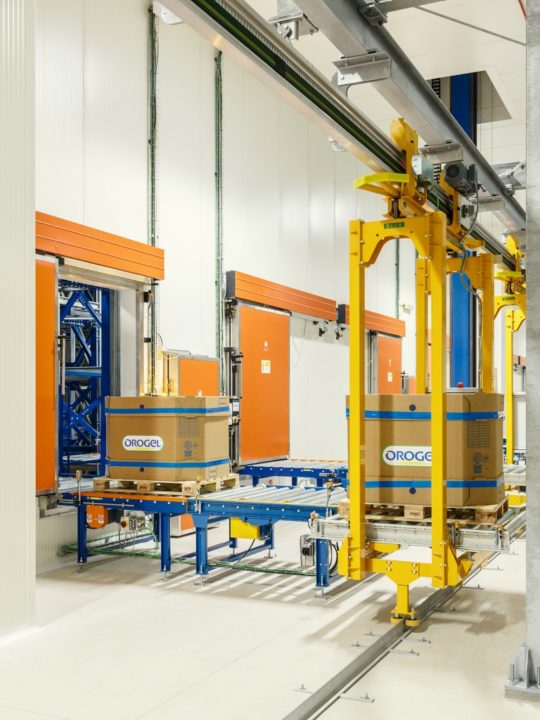
Stabilimento Orogel
Indice degli argomenti
Un progetto di automazione per un magazzino 4.0 a meno 25 gradi
Tra la fine degli anni ‘80 e l’inizio dei ‘90 l’azienda realizza i primi due impianti (Orogel 1 e 2), la crescita costante e le richieste del mercato hanno portato a gettare le basi di un progetto ambizioso, partito nel 2000. I due comparti sono stati ridisegnati per incrementare l’efficienza, ridurre i costi e aumentare gli spazi, il tutto garantendo i massimi standard igienici in tutto il percorso che va dal prodotto fresco, alla surgelazione fino alla consegna. Orogel 3 è il punto di arrivo di questo completamento, culminato con la messa in esercizio della nuova cella.
Orogel 3 sarà collegato agli altri due impianti da un ponte, che, grazie alla movimentazione meccanizzata servirà per trasferire i prodotti surgelati in andata e ritorno, in modo che la filiera produttiva all’interno dello stabilimento sia totalmente in continuità e meccanizzata con l’azzeramento conseguente del trasporto su gomma. L’adozione dell’automazione ha come obiettivo quello di eliminare l’uso dei muletti elettrici all’interno dei reparti a vantaggio dell’igiene e dell’efficienza. Il comparto sarà completato con un impianto di trigenerazione; produzione combinata di energia elettrica ma soprattutto di freddo.
Dalla simulazione alle tecnologie per l’automazione del magazzino fino alle reti industriali di comunicazione
L’automatizzazione è stata affidata a un grande e importante gruppo internazionale dell’ICT e comprende non solo la cella, ma arriva fino all’anti-cella e al punto in cui i prodotti vengono passati ai camion da trasporto.
Prima della realizzazione dello stabilimento, è stata fatta una simulazione per capire dove posizionare le nuove linee e per studiare i flussi del magazzino automatico. Nello specifico il plant simulator è servito a tre scopi: determinare le potenzialità della cella nel soddisfare i flussi; studiare il flusso di spedizione e studiare la movimentazione al primo piano.
La cella deve sostenere i flussi da e per i reparti di confezionamento, continuando a fare spedizione. Oggi con questo software di simulazione Orogel simula tutti i flussi. Il layout dell’automazione è il frutto delle risultanze che il plant simulator ha permesso di verificare in modo semplice.
La standardizzazione delle soluzioni rende semplice la manutenzione. Integrazione, omogeneizzazione, connettività tra i prodotti all’interno del sito: questi elementi permettono a Orogel di essere pronta e ben posizionata anche per il futuro.
Per garantire l’automazione in condizioni di temperatura critiche, l’azienda che ha realizzato il progetto ha modificato gli inverter (Sinamics G120M) per la messa in servizio fino a -25°. È stato un intervento tecnologico che ha richiesto competenze specifiche.
Tutti i dispositivi presenti nell’impianto sono collegati tra loro e integrati all’interno di un’unica piattaforma sia di programmazione sia di gestione operativa. Ciò è utile per le persone che lavorano nel sito di produzione. La piattaforma di gestione per le reti remote (Sinema Remote Connect) è un’applicazione server, per questo ha permesso di accedere alle macchine installate in modo semplice e sicuro.
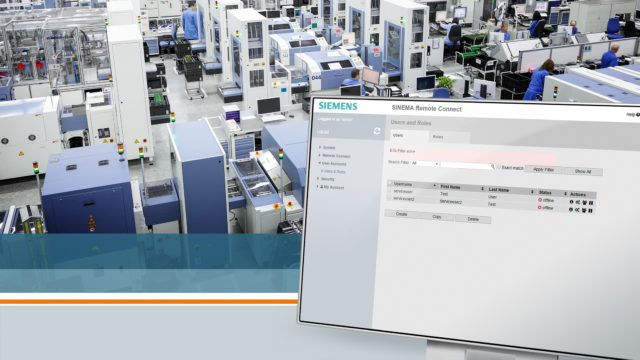
Programmare il futuro grazie all’analisi del dato ed efficienza energetica
Il passo successivo di Orogel è stato quello di incrociare le capacità produttive delle linee con le strategie di produzione del freddo.
Complessivamente Orogel ha installato parecchie centinaia di sensori, che rappresentano per l’azienda il valore aggiunto di un approccio progettuale innovativo. Oggi acquisire un’informazione dai sensori permette all’azienda di Cesena di creare delle correlazioni tra grandezze di origine diversa. Dalla misurazione di questo patrimonio di dati e conoscenze deriveranno le scelte di domani in un’ottica di miglioramento ed evoluzione continui.
Tutto ciò che è distribuzione elettrica, dalla media alla bassa tensione, è stato rivisto, con ritorni positivi dall’utilizzo dei trasformatori: la strumentazione ha consentito di reperire una serie infinita di grandezze sui consumi. La trasversalità dell’intervento si è estesa agli impianti di scurezza, di evacuazione, a quelli di rilevazione incendi. Tutti questi impianti confluiscono a un sistema di controllo di stabilimento che coordina gli avvisi e allarmi.
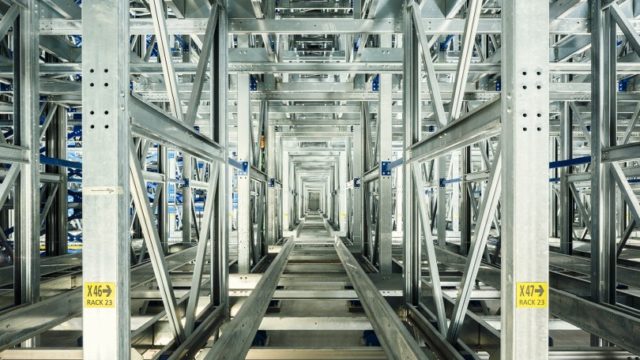
Una partnership per l’automazione all’insegna della co-creazione
La formula vincente è stata quella di creare un team di lavoro che ha visto la stretta collaborazione tra l’azienda esecutrice del progetto, il Solution Partner per gli azionamenti di automazione, Orogel, e i suoi fornitori. Oggi la grande cella per surgelati situata a Cesena e adiacente al polo produttivo è pienamente operativa e rappresenta un benchmark di impianto 4.0 per gli altri impianti di Orogel e per le sue esigenze future.