Il termine Industria 4.0 compare già da qualche anno come un refrain nelle slide e nei discorsi di chi si occupa di innovazione tecnologica. Questo termine si rivolge principalmente alle aziende manifatturiere, che possono trarne vantaggio inserendosi nel panorama digitale e interconnesso in cui tutti noi siamo immersi.
Potente caratteristica delle tecnologie di Industria 4.0 è che esse possono apportare tangibili benefici a qualsiasi tipo di industria che si occupi di:
- produrre (si pensi alla produzione di alimenti, automobili, medicinali o persino di energia);
- manutenere gli impianti di produzione;
- gestire lo stoccaggio e/o lo smistamento di quanto prodotto.
Poiché i processi elencati stanno alla base della quasi totalità delle aziende di manufacturing, gli esperti di Industria 4.0 sono in grado di portare profitto in contesti estremamente variegati che possono andare dalle industrie farmaceutiche ai produttori di penne stilografiche passando per le fabbriche di indumenti o per gli impianti di generazione e distribuzione del gas.
Indice degli argomenti
La sfida dell’Industria 4.0: contesto di riferimento
I modelli di Industria 4.0 riescono a essere così adattivi perché generano valore superando ostacoli che, in fin dei conti, sono sempre gli stessi: i macchinari – e, più in generale, l’ambiente – di produzione generano una miriade di dati (Big Data) che, proprio in virtù della loro grande quantità, non sempre possono essere elaborati in modo ottimale e i motivi sono molteplici, tra cui:
- la mancanza di sistemi dalla adeguata potenza di calcolo;
- l’assenza di opportuni algoritmi di analisi dei dati (Data Analytics);
- l’inaccessibilità ai dati, ad esempio perché generati da strumentazione obsoleta e dunque difficile da connettere a sistemi esterni.
D’altro canto i dati sono stati definiti “il nuovo petrolio” giacché una loro sapiente interpretazione conduce le imprese a considerevoli guadagni legati a:
- Ottimizzazione della produzione, sia in termini di quantità che di qualità;
- Ottimizzazione della manutenzione (si pensi alle soluzioni di fault detection e manutenzione predittiva);
- Ottimizzazione della gestione delle scorte (inglobando talvolta metodologie di tracciamento come la blockchain).
Pertanto, la grande sfida dell’Industria 4.0 è quella di trasformare i tanti dati grezzi in informazione sintetica di qualità e dalla consultazione efficace, in modo che possa essere valido materiale di supporto alle decisioni. Da non sottovalutare, inoltre, che un sistema di Industria 4.0 consente la memorizzazione strutturata di tutti i dati rilevati, il che si traduce nel costruire una vera e propria “miniera di dati” che diventa facilmente accessibile.
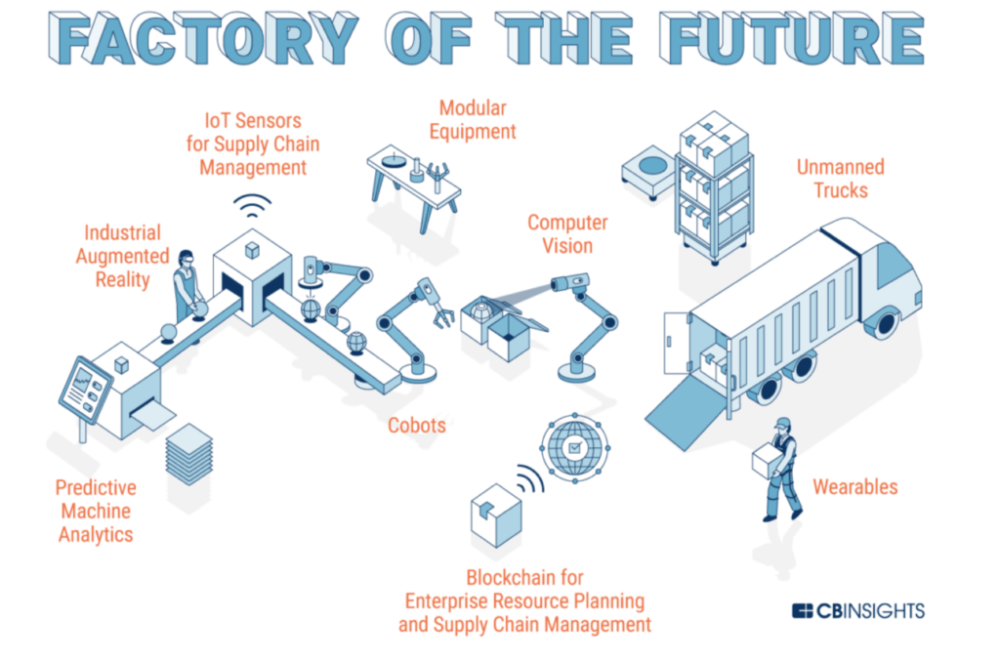
Figura 1 – Fonte CBS Insight
Le tecnologie abilitanti per Industria 4.0
La versatilità delle soluzioni di Industria 4.0 risiede nel fatto che la maggior parte degli enablers che consentono di vincere la suddetta sfida è indipendente dall’industria in cui si applicano. Che si tratti di un sito di produzione di pneumatici o di frigoriferi, le armi giuste provengono perlopiù dal mondo dell’informatica e sono comunemente impiegate per: l’estrazione dei dati dalle macchine; l’elaborazione dei dati, che spesso si accompagna alla memorizzazione sia dei dati estratti che dei risultati delle elaborazioni stesse; la visualizzazione rapida e proficua dei risultati.
Estrazione dei dati
I moderni dispositivi che generano dati possiedono nativamente la capacità di connettersi al mondo esterno: quale che sia la tecnologia usata, riescono facilmente a comunicare con altre macchine e a navigare su Internet. Tuttavia, anche la strumentazione più obsoleta può ormai godere di un gemello digitale (digital twin) e di una connessione con le reti esterne per tramite di tecnologie anche poco costose: tra queste vi sono i cosiddetti sensori IoT (Internet of Things), distribuiti da fornitori di hardware che sanno come scardinare dispositivi obsoleti.
Un’altra alternativa è inserire un “dispositivo di mezzo” che faccia da ponte nella comunicazione tra le macchine e il mondo esterno, curando altresì la traduzione dei pacchetti di dati in arrivo. Dispositivi del genere sono i broker o gateway.
Di solito, tutti questi sistemi si avvalgono di protocolli come MQTT o OPC UA e rendono disponibili i dati in output sotto forma di pacchetti JSON (tecnicismi utili specialmente per le comunicazioni dei dati in tempo reale). In gergo, si dice che i dispositivi menzionati connettono la rete OT alla rete IT.
Elaborazione e memorizzazione
Sensori IoT e broker inviano quindi i dati alle componenti che li elaborano e li memorizzano. Qui sta un altro punto di forza dell’Industria 4.0, ovvero la connessione al cloud I dati vengono spediti in sicurezza su Internet verso servizi cloud in grado di applicare complessi algoritmi di analytics o machine learning per generare valore a partire dai dati ricevuti. Le aziende possono decidere di demandare non solo il trattamento ma anche la memorizzazione dei dati ai fornitori delle soluzioni cloud. Il tutto in massima sicurezza e con la possibilità di accedervi in qualsiasi momento (resta inteso che la proprietà dei dati rimane di chi li genera e non dell’azienda che vende i servizi cloud).
I principali vantaggi di questo paradigma sono i seguenti:
- l’industria che sfrutta il cloud paga esclusivamente le risorse che utilizza, liberandosi dall’onere di dover scegliere pacchetti precostituiti che, in un secondo momento, potrebbero rivelarsi di dimensioni inappropriate. Ciò rende l’infrastruttura facilmente scalabile in base alle effettive necessità;
- l’apertura ai servizi cloud evita alle aziende sia l’acquisto di sistemi di elaborazione e memorizzazione dati sia le attività di gestione, che vengono totalmente demandate ai fornitori dei servizi. Esempi di attività di gestione possono essere l’allocazione di una potenza di calcolo adeguata a far funzionare i modelli di analytics o l’implementazione di politiche di sicurezza sui database in cloud.
Esposizione dell’informazione
Una volta ricavata l’informazione utile, va mostrata nel migliore dei modi a chi deve prendere decisioni in merito alle varie fasi del processo produttivo. Per andare nel concreto, vanno forniti idonei insight che permettano di rispondere alle domande che si pone chiunque gestisca delle linee di produzione, tra cui:
- posso ottimizzare la produzione aumentando la velocità di quel macchinario?
- conviene ridurre il numero di interventi manutentivi annuo per questo dispositivo?
- quali conseguenze ha sulle produzioni un abbassamento della temperatura dell’ambiente?
- variando alcune condizioni di esercizio, è possibile ritardare sensibilmente l’insorgenza di guasti alla linea?
L’utilizzo di strumenti IT che aiutino a trovare le risposte giuste a quesiti del genere ha un impatto diretto sul miglioramento delle performance, tanto nelle fabbriche di lampadine quanto in quelle di biciclette.
Punto chiave qui è la rappresentazione semplificata e accessibile delle informazioni in gioco. Anche in questo caso vengono in soccorso i servizi cloud. Infatti, le suite in cloud di solito contengono sistemi di visualizzazione e reportistica per lo sviluppo di dashboard su cui mostrare le informazioni in arrivo dagli altri servizi (i.e. dati raccolti e risultati delle elaborazioni).
E c’è più. Il cloud dà la possibilità di accedere a queste dashboard in modalità mobile. Tradotto: chiunque voglia consultare l’informazione, può farlo senza il vincolo di doversi trovare fisicamente in linea di produzione. Basta avere con sé un dispositivo aziendale portatile – sì, compresi smartphone e tablet – e una connessione a Internet e il gioco è fatto! Comodi i sistemi di Industria 4.0, vero?
Quali ostacoli all’adozione di modelli di Industria 4.0?
Per concludere, uno sguardo ai principali game stopper per la diffusione delle soluzioni di Industria 4.0.
Di frequente si verifica che i principali impedimenti non sono di natura tecnologica, bensì culturale.
Infatti, gran parte delle aziende fa ancora fatica ad accettare l’idea di “mandare i propri dati in Cloud” poiché si crede erroneamente che ciò comporti una divulgazione inappropriata dei dati stessi.
L’antidoto a questo timore è naturalmente quello di ingaggiare fornitori esperti che possano dimostrare ai “non addetti” tutti i vantaggi del cloud in materia di data security.
Una seconda barriera è rappresentata dalla mancanza di sinergia tra chi produce i dati e chi li tratta. Per andare più in dettaglio, si leggeva sopra che i modelli di data analytics, machine learning e intelligenza artificiale sono spesso gestiti da chi offre i servizi cloud, che generalmente mette a disposizione anche il know-how essenziale per adattare i modelli al contesto del cliente che li richiede. Tuttavia, l’adattamento di tali sistemi non può prescindere dall’interazione continua tra chi conosce le tecniche di elaborazione dei dati (i data scientists dei fornitori dei servizi cloud) e chi conosce il significato dei dati che si stanno elaborando (i responsabili delle linee di produzione).
Calare correttamente gli algoritmi di data processing nella realtà della singola industria è sempre molto affascinante per i data scientists ma richiede il continuo affiancamento di qualcuno che sappia quali benefici vuole ottenere da quegli algoritmi e sotto quali vincoli. Va superata, dunque, la visione per cui i dati devono solo essere spediti a un qualche tecnico esperto e poi è sufficiente aspettare per qualche settimana mentre ci si dedica ad altro; così facendo, nessun data scientist restituirà la lista di correttive magiche da seguire per generare maggiori profitti.
Photo Credit: fonte IBM