Information Technology più Operational Technology uguale Industria 4.0. Alla base del concetto di smart factory c’è la convergenza fra gli strumenti hardware e software per la gestione delle informazioni, e le soluzioni di controllo e automazione a supporto delle operazioni. Uno scenario ibrido, che impegna le aziende in una trasformazione sotto il profilo tecnico e organizzativo e arriva a comprendere le più più avanzate applicazioni dell’Industrial Internet Of Things.
Indice degli argomenti
Smart factory, un’idea nata in Germania e negli Usa
L’idea di smart factory, o di fabbrica intelligente, ovvero di processi di produzione secondo le linee dell’Industria 4.0, prende le mosse negli anni 2011-2012 dalle iniziative intraprese in Germania e negli Usa. È il governo tedesco, del resto, a usare per primo il termine “Industry 4.0”, nel 2011, nel suo piano volto a promuovere politiche di lungo termine per la digitalizzazione del settore manifatturiero, coinvolgendo l’intera filiera: imprese, associazioni di settore, università e centri di ricerca, con l’obiettivo comune di potenziare la competitività della Germania.
Cuore del piano di innovazione digitale tedesco è il concetto di cyber-Physical Systems (cPS), sistemi sono composti da un elevato numero di sensori installati sui macchinari (indicatori di stato, ambientali e di esercizio) che ne permettono l’interconnessione, ponendo le basi per l’autoregolazione dei sistemi produttivi. I principi dell’Industry 4.0 impongono quindi alle aziende di adottare i cPS nelle fabbriche, oltre a robot, allo scopo di raggiungere un’elevata flessibilità produttiva basandosi anche sull’analisi dei manufacturing Big Data raccolti dagli stessi macchinari.
Quasi nello stesso tempo (2012), negli Stati Uniti nasce la Smart Manufacturing Leadership Coalition (SMLC), un’associazione no profit che ha lo scopo di favorire la collaborazione tra aziende produttrici, enti di ricerca e università, nonché organizzazioni di produttori, nella ricerca e nello sviluppo di standard, piattaforme e infrastrutture condivise per l’adozione dello Smart Manufacturing. Qualcosa di molto simile, insomma, all’Industry 4.0 tedesco. A differenza di questo, l’iniziativa americana è incentrata sui principi di riduzione dei costi, condivisione di pratiche e tecnologie, definizione collettiva di aree di R&D, innovazione attraverso processi collaborativi.
I cyber-Physical Systems sono sistemi informatici che permettono alle macchine di comunicare e operare a contatto con il mondo reale, si tratta quindi di macchine robotizzate e in grado di prendere decisioni in maniera autonoma, interagendo con l’ambiente circostante.
Viene da chiedersi, a questo punto, se smart manufacturing e industry 4.0 non siano, nella sostanza, la stessa cosa. Appare evidente che i due piani, quello tedesco e quello americano, fanno riferimento al concetto comune che le tecnologie digitali sono in grado di abilitare l’interconnessione e la cooperazione delle risorse utilizzate nella fabbrica e lungo la catena del valore, che si traduce in maggiore efficienza e competitività delle imprese manifatturiere. I risultati in termini economici di questi ultimi anni di Germania e Usa sembrano confermarlo pienamente.
Lean smart production per la trasformazione digitale delle aziende
La trasformazione digitale all’interno delle fabbriche richiede la razionalizzazione dei processi relativi sia alla produzione sia all’informazione. Per raggiungere gli obiettivi di efficienza, l’operatività deve essere ottimizzata attraverso i principi della lean smart production, che permettono la minimizzazione dei lotti e la gestione just-in-time dei materiali, delle commesse e degli approvvigionamenti, minimizzando le giacenze e garantendo maggiore flessibilità alle esigenze del mercato. L’obiettivo è ottenere l’agilità di processo necessaria a realizzare prodotti in serie brevi e diversificati, senza perdere i vantaggi delle economie di scala, per andare incontro alle richieste di personalizzazione dei modelli e alle nuove dinamiche dell’e-commerce, che si traducono in acquisti sempre più frequenti e frammentati, anche di singole unità.
In particolare, due tecniche lean permettono di rispondere alle nuove necessità manifatturiere:
- la produzione per logica pool, per cui l’ingresso dei materiali in fabbrica viene attivato solo in seguito alla ricezione degli ordini così da evitare l’accumulo delle giacenze;
- Il one-piece flow, che permette la fabbricazione di una singola unità alla volta in modo flessibile ed economico, migliorando la qualità dei prodotti e riducendo i tempi.
La riorganizzazione dei processi, requisito di base per lo smart manufacturing, coinvolge anche le attività di raccolta, gestione e distribuzione dei dati, che vanno riorganizzati per consentire flussi informativi snelli, veloci e funzionali. Bisogna quindi individuare i parametri e le indicazioni chiave che servono per affinare il decision-making a ogni livello del processo produttivo, garantendo comunicazioni puntuali tra le persone con i giusti strumenti. Nella data economy, la condivisione della conoscenza aziendale è alla base del successo competitivo.
Le soluzioni software che possono essere adottate dalle aziende per la digital transformation (ad esempio quelle di Microsoft Azure IoT e Machine Learning) consentono di avere un’unica piattaforma e di integrare i macchinari esistenti. Inoltre, partendo dalle informazioni raccolte, possono favorire l’integrazione con i dati provenienti da altri sistemi che gestiscono il ciclo di vita del prodotto (Mes, Erp, Crm, Plm). Le informazioni eterogenee raccolte vengono elaborate dalla piattaforma in cloud, con la possibilità di accedere a un insieme di servizi in grado di raccogliere enormi quantità di dati (Big Data Analytics aziendali) prima non gestibili, estrarre informazioni con modelli di machine learning, allo scopo di ottenere informazioni volte a migliorare l’efficienza del processo.
Smart factory in Italia, progetti e investimenti
In Italia quello della smart factory è uno dei processi aziendali 4.0 più vivace. Su quasi 800 aziende censite dal Politecnico di Milano per l’Osservatorio Industria 4.0 2019, il 42% dei progetti riguarda la smart factory (produzione, logistica, manutenzione, qualità, sicurezza e rispetto delle norme). Le altre aree aziendali coinvolte nel processo di digitalizzazione sono Smart Lifecycle (sviluppo prodotto, gestione del ciclo di vita e gestione dei fornitori) col 33% dei progetti e Smart Supply Chain (pianificazione dei flussi fisici e finanziari) col 25%. Le tecnologie più diffuse sono quelle dell’ambito Industrial IoT (connettività e acquisizione dei dati), pari al 25%.
Per quanto riguarda gli investimenti programmati, le aziende hanno intenzione di concentrarli maggiormente in Industrial IoT (48%), Industrial Analytics (39%) e Advanced Automation (33%). Ampliando l’orizzonte delle previsioni a cinque anni l’Advanced Automation assume la priorità, seguito da Cloud e Additive manufacturing. Ancora poco rilevanti, in termini di investimenti, intelligenza artificiale e Blockchain, salvo alcune eccezioni costituite dalle aziende di grandi dimensioni.
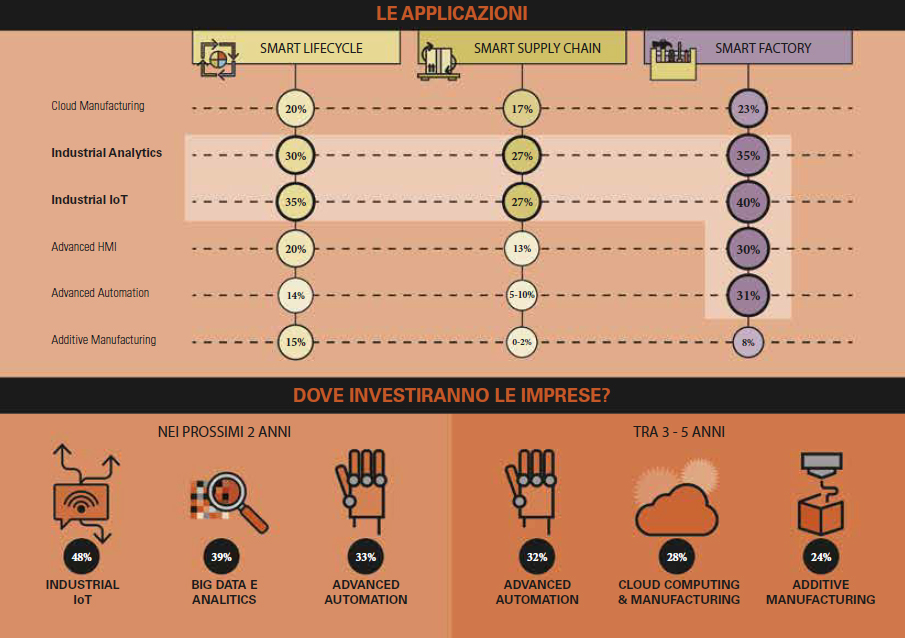
Osservatorio Industria 4.0 – 2019 – Politecnico di Milano
I dati forniti dall’Osservatorio del Politecnico di Milano sembrano indicare che nell’Industria 4.0 siano determinanti gli oggetti connessi (IoT) e i Big Data. Due tecnologie fortemente legate con i sistemi cPS. La sfida, per le imprese, è sostituire le macchine tradizionali con nuovi macchinari, a tutti gli effetti oggetti dell’Internet of Things. Ciò consentirà alle imprese di controllare in tempo reale tutti i processi aziendali e di raccogliere dati da utilizzare nei modi più diversi per accrescere la competitività. Tramite i Big Data sarà possibile effettuare analisi predittive, previsioni e simulazioni ed essere in grado quindi di fronteggiare i mutevoli scenari di mercato.
Articolo originariamente pubblicato il 17 Feb 2020