Parlare di Industria 4.0 nel mondo del manifatturiero significa in primo luogo parlare di una fabbrica connessa, nella quale i dati assumono un ruolo centrale, dando la possibilità alle imprese di migliorare la propria efficienza ed efficacia grazie a un nuovo processo decisionale basato su un’accurata analisi delle informazioni.
Sono questi i temi al centro dell’incontro “Digital Transformation, Vantaggi e Opportunità della fabbrica connessa: parlano i casi d’uso”, organizzato dalle nostre testate Industry4business.it e Internet4things.it, in collaborazione con Siemens.
In apertura dei lavori, Andrea Bacchetti, CEO di IQConsulting e ricercatore dell’Università di Brescia, ha offerto una panoramica di scenario, partendo dai risultati della Ricerca sull’Industria 4.0 sviluppata dal Laboratorio RISE e sviluppato su un panel di 115 medie aziende del manifatturiero.
Indice degli argomenti
Cosa sono Smart Factory e Industria 4.0
“L’industria 4.0 – ha spiegato – rappresenta un argomento gettonato che si compone di diversi moduli, come un grande puzzle. Fa parte di questo puzzle, naturalmente, una componente tecnologica importante, in costante evoluzione, che presuppone non solo la sussistenza di competenze verticali, ma anche la capacità e la possibilità di orientare i clienti verso le tecnologie stesse, utilizzandole come leve per la generazione di valore”.
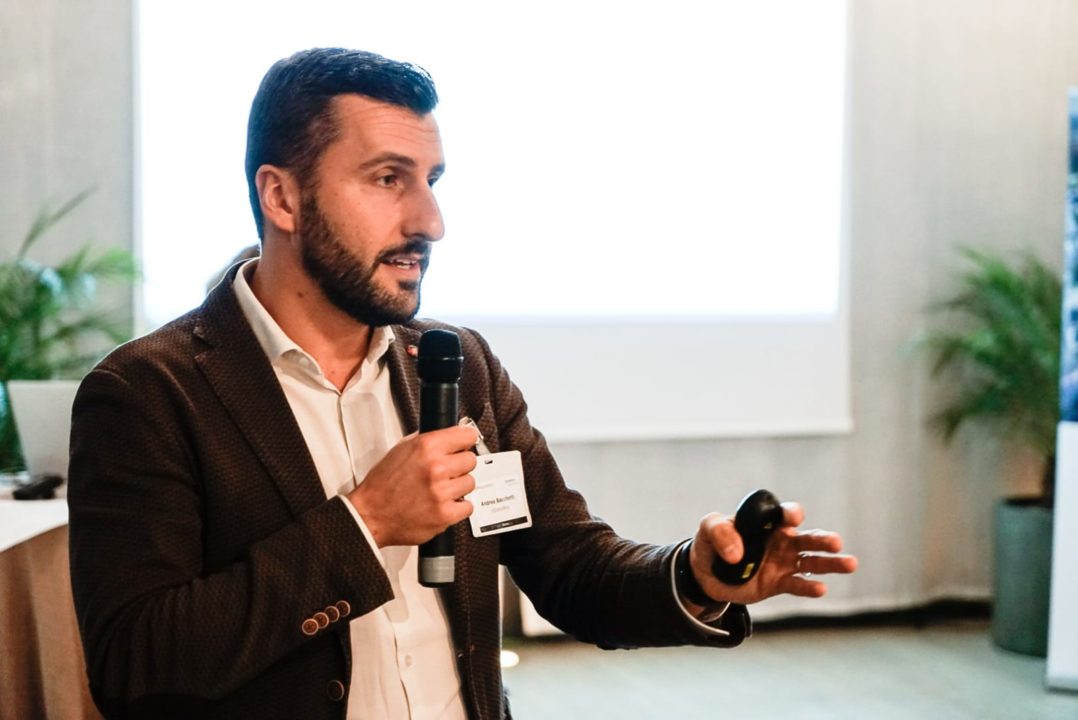
Attenzione, però, raccomanda Bacchetti: “Se il percorso di trasformazione del manifatturiero viene affrontato dal solo punto di vista delle tecnologie, non si coglie appieno la portata del fenomeno. Bisogna adottare un approccio diverso, per comprendere come generare nuovo valore, identificare le competenze e il gap che ci sono negli organici e solo a quel punto si identificano le tecnologie digitali che abilitano realmente il processo di trasformazione”.
Le smart factory (fabbriche connesse) cambiano il manifatturiero
Pragmaticamente, tuttavia, Bacchetti riconosce come dall’indagine del RISE emerga chiaramente che questo tipo di percezione del fenomeno Industria 4.0 ancora non vi sia: “Nella metà del campione analizzato, questa percezione completa del fenomeno e delle opportunità non c’è ancora: in alcuni casi c’è una visione troppo technology-oriented, e in qualche caso il concetto viene associato esclusivamente al mondo dell’IT. La fase di divulgazione e sensibilizzazione delle opportunità è ancora aperta”.
Nella sua analisi, RISE ha ricondotto le imprese a quattro cluster principali:
– Ritardatari: aziende ferme o che stanno lavorando su di una sola tecnologia, senza interventi su competenze ed organizzazione
– Tech verticali: aziende che hanno implementato singole tecnologie non integrate tra di loro. Lavorano per silos e non hanno avviato un percorso di adeguamento di competenze ed organizzazione
– Tech integrate: aziende che hanno implementato diverse tecnologie in modo integrato, ma non hanno ancora avviato un percorso di adeguamento di competenze ed organizzazione.
– Super star: aziende che si muovono in maniera organica e hanno investito per ripensare la struttura organizzativa e lavorano sulle competenze delle persone che la popolano.
Dall’Industria 4.0 alle filiere 4.0 attraverso la fabbrica connessa
Al di là delle definizioni, va detto che percentualmente c’è una fetta importante di aziende in ritardo: la maggior parte delle aziende lavora per silos, mentre le aziende che dimostrano una forte maturità nei confronti della trasformazione sono meno del 20%.
Per quanto riguarda invece le leve tecnologiche, centrali restano IoT e i software per la gestione dei Big Data: “Due leve che hanno in comune la gestione del dato e la capacità di trasformarlo in informazione e di prendere decisioni consapevoli e tempestive, il cuore della trasformazione 4.0”.
Ma ci sono altre evidenze che emergono dall’analisi.
In primo luogo, che le dimensioni contano: all’aumentare delle dimensioni tende ad aumentare la maturità.
Parimenti, sembra esistere una relazione forte tra il modo in cui l’IT partecipa in maniera attiva ai processi di trasformazione digitale e la maturità digitale dell’azienda, così come c’è una correlazione tra l’informatizzazione dei processi di business e il livello di maturità digitale: “Un’azienda non pronta alla copertura informativa dei processi e con una funzione IT non adeguatamente coinvolta, fa fatica a muoversi verso una trasformazione digitale”.
Alla luce di queste considerazioni, è naturale domandarsi chi guidi effettivamente il cambiamento.
“C’è ancora una componente direzionale forte, con iniziative top-down. Man mano che aumentano le dimensioni entrano in campo i CIO e altre prime linee: nel 10% dei casi abbiamo assistito alla nascita di nuovi ruoli spesso assunti dall’esterno. C’è una revisione della struttura organizzativa: la governance della trasformazione viene affidata ad una figura con caratteristiche di trasversalità per evitare silos verticali”.
I freni delle smart factory e dell’innovazione
Ma cosa frena le imprese?
“Tutto sommato – spiega Bacchetti – ci sono meno timori rispetto alla maturità delle tecnologie abilitanti. Resta importante il tema degli investimenti necessari, così come pesa l’incertezza politica. Ma soprattutto le aziende temono di non avere le competenze sia interne che esterne necessarie ad affrontare la trasformazione digitale”.
È però uno sguardo al futuro quello che offre Bacchetti: “Da Industria 4.0 siamo gradualmente passati alle imprese 4.0: il prossimo step sarà quello delle filiere 4.0, ovvero ecosistemi allargati ai diversi attori che partecipano alla realizzazione della trasformazione digitale. È comunque un percorso ancora lungo, che va sostenuto con esempi virtuosi che vengono da aziende che condividono le loro esperienza, con percorsi di formazioni mirati, con il prosieguo degli incentivi fiscali, che rappresentano una leva importante soprattutto per le imprese piccole, con poca capacità di spesa, che spesso giocano un ruolo chiave in catene del valore specifiche.
La testimonianza: la smart factory e la sicurezza dello stabilimento sughi Barilla di Rubbiano
Proprio il tema degli empi virtuosi è stato immediatamente ripreso, con una testimonianza proveniente da una realtà “faro” nel sistema industriale italiano: Barilla.
In particolare, Andrea Di Nicola, Responsabile Automazione in Barilla, e Federico Tarzia, Sales Engineer in ITCore, partner del progetto stesso, hanno raccontato la loro esperienza relativa a un progetto di ampliamento e miglioramento dell’impianto produttivo di Rubbiano in provincia di Parma, nel quale si producono salse, sughi e pestati.
“Il Plant di Rubbiano, nato nel 2012, è stato recentemente oggetto di un ampliamento, di cui si è approfittato per effettuare investimenti di miglioramento in alcune aree produttive – spiega Di Nicola -. In particolare, abbiamo scelto di investire in una nuova infrastruttura di rete per rispondere alle richieste in termini di cybersecurity, poter disporre di una infrastruttura di teleassistenza robusta ed efficiente che garantisca il controllo totale degli accessi, avere una rete strutturata e dare una certa forma alla rete di automazione”.
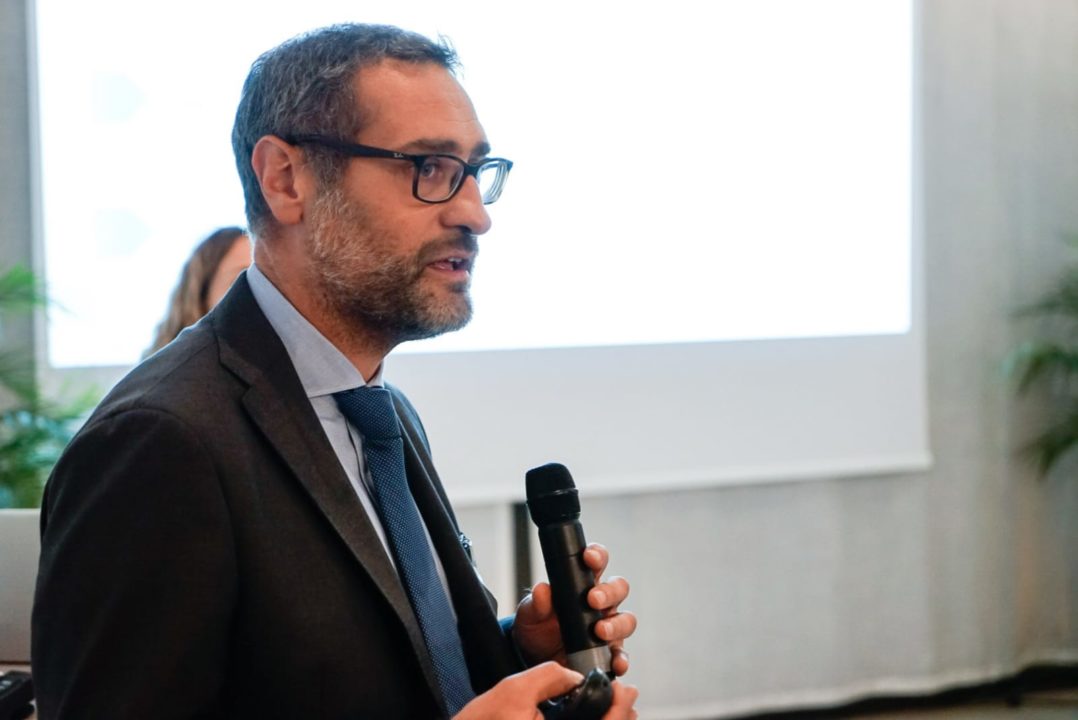
ITCore, che opera come Industrial Strength Networks Partner di Siemens Italia, ha messo al servizio del progetto le sue competenze nella pianificazione, implementazione e protezione delle reti industriali.
Spiega Tarzia: “Siamo partiti dalla verifica della rete esistente per verificarne la congruità rispetto agli obiettivi. Abbiamo deciso di non realizzare un impianto ex novo, ma di migliorare l’esistente. In questo percorso, abbiamo coinvolto anche il responsabile IT di Barilla: non si poteva affrontare un percorso di revisione del networking senza il coinvolgimento di IT e OT. Insieme a Siemens, poi, si è stilato il progetto del nuovo networking industriale: requisiti, materiale e stesura delle fasi operative fino alla realizzazione della nuova rete. ITCore è stata coinvolta nella fase di progettazione e realizzazione, nella fase operativa, nella fase di change request, ovvero di meeting e variazioni di progetto. Il tutto per garantire la migrazione alla nuova infrastruttura senza interrompere l’operatività quotidiana”.
Gli aspetti tecnici del progetto e la logica della fabbrica connessa
L’infrastruttura di rete prevista poggia su un backbone di switch collegati tra loro ad anello per garantire la continuità, sopra il quale esistono tutte le reti dei vari fornitori. Una grossa variazione rispetto al plant precedente, nel quale era presente una rete per ogni fornitore. A monte di ogni linea di sottorete è stato introdotto un firewall di cella per segmentare le informazioni in entrata e uscita.
Si è passati da una infrastruttura “piatta” a una infrastruttura segmentata e sicura completa di un sistema di monitoraggio attivo: un processo che è durato due anni e che ha visto una sempre più stretta collaborazione tra Barilla e ITCore.
“Oggi – spiega Di Nicola – siamo in grado di misurare quanto la nostra struttura è più affidabile rispetto a prima, quanto la ricerca guasti a livello di rete è migliorata e quanto siamo più efficienti nella ricerca di eventuali problemi. Un altro KPI emblematico di questo progetto è relativo al controllo accessi: riusciamo a controllare chi e quale fornitore interviene in teleassistenza. Abbiamo un controllo più stretto sugli interventi manutentivi dei fornitori e sappiamo chi, come, perché e per quanto tempo un fornitore resta inserito nella nostra rete”.
Per Barilla, oltre ad aver aumentato la sicurezza complessiva dell’infrastruttura, il progetto sviluppato con ITCore ha rappresentato uno stimolo per colmare il gap di competenze: “L’abbiamo visto come opportunità per accrescere le competenze dei manutentori. C’è sempre qualcosa da migliorare e lo stiamo approcciando giorno per giorno sia con training formali, sia direttamente sul campo: è uno stimolo a migliorare la qualità della manutenzione in generale oltre che la sensibilità a certi temi”.
Unire le esigenze di IT e OT nelle smart factory
Interessante, in questo progetto, è la sua replicabilità: “Abbiamo approfittato di un momento di ampliamento per effettuare questo investimento, con l’obiettivo di rendere Rubbiano un modello anche per altri plant Barilla”.
Si tratta di un progetto che ha messo in luce l’importanza della collaborazione tra IT e OT.
“I due mondi si sono aperti le porte a vicenda. La realtà dei fatti era che tutta la rete di automazione o di supervisione era dominio dell’IT, adesso si è creata una sinergia che ha portato sicuramente benefici. Si sono soddisfatti i requisiti provenienti da entrambe le parti: lato IT era importante la sicurezza, lato OT la continuità operativa. Affrontando questo processo insieme si sono soddisfatte entrambe le richieste”.
La visione e le proposte di Siemens
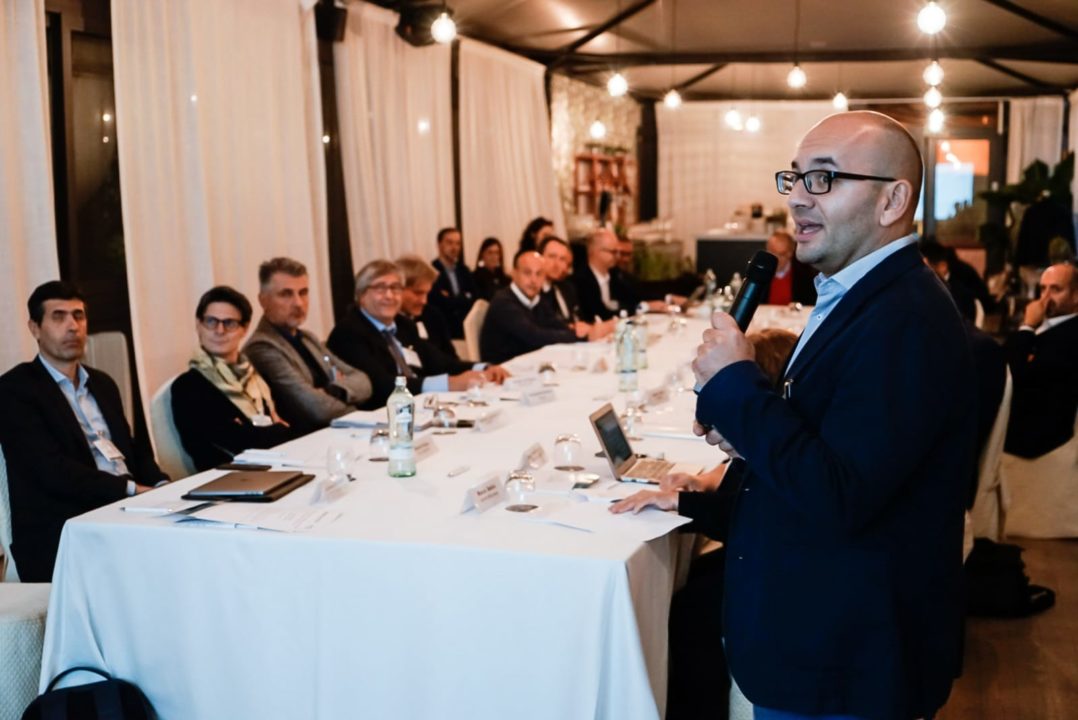
“Siemens è il facilitatore – dichiara Marcello Scalfi, Sales Specialist Industrial Networks della società – di questo dialogo tra IT e OT. Il progetto Barilla è stata una sfida, un’opportunità di crescita. Abbiamo dovuto imparare a collaborare a tutti i livelli cercando di soddisfare il cliente in tutte le esigenze e facendo attenzione al suo obiettivo. Abbiamo le fondamenta nel mondo OT, ma stiamo cercando di riuscire a facilitare questa comunicazione, non solamente con i prodotti ma anche con l’attività di tutti i giorni, incontrando nuove realtà così come i clienti clienti che hanno bisogno di trasformare digitalmente la propria struttura”.
Secondo Scalfi, spesso le aziende non sanno nulla riguardo al loro plant.
“La mia rete è sicura? Come posso gestire le reti per garantire elevata efficienza? Sono queste le domande che i nostri clienti. Sono temi che riguardano l’OT, ma anche l’IT, cui spettano la supervisione e il dominio di alcune competenze chiave in un contesto di digital transformation”.
C’è bisogno di una digital connectivity, che dunque abbracci aspetti di networking industriale, network management, industrial security.
“Spesso le strutture industriali non hanno integrazione – spiega ancora Scalfi -. Le macchine non sono collegate o non lo sono in modo puntuale e concorde a tutti i livelli. Ci mettiamo al lavoro con soluzioni che devono soddisfare requisiti importanti in termini di determinismo, visibilità, flessibilità, safety. Soluzioni, cioè, che garantiscono sicurezza, separazione, ridondanza e collegamento in alta affidabilità verso le reti IT”.
In questo scenario entrano in campo anche altre partnership di ecosistema, come quella siglata con HPE Aruba con l’obiettivo di creare un ponte tra IT e OT, in una logica di reale integrazione tra questi due mondi.
Il ruolo della sicurezza nella smart factory
È comunque uno scenario che richiede un approccio molto attento alla sicurezza. Spiega ancora Scalfi: “Il numero di attacchi cresce sempre di più: i dati rilevati da fonti autorevoli parlano di situazioni sempre più drammatiche, impianti in tutto il mondo anche in Italia soffrono di business interruption a causa di attacchi hacker. Siemens sposa una soluzione basata su uno standard internazionale la dephense in depth: concetto olistico che prevede soluzioni per mettere in sicurezza i plant, network security e che ci permettono di garantire l’integrità del sistema. Siemens si è fatta fautrice e ha lavorato all’estensione di alcuni aspetti del paradigma 4.0”.
Si parla dunque di segmentazione delle celle e di protezione da parte dei firewall delle linee produttive, garantendo nel contempo l’accesso da remoto. “Parliamo di protezione a tutti i livelli. Non possiamo ignorare che molto spesso gli attacchi arrivano dall’interno, per mancata strutturazione di policy, mancata informatizzazione delle aree e mancato utilizzo di metodologie sicure per l’accesso alle macchine. Esistono soluzioni che, sfruttando ML e AI, cercano di prevenire possibili attacchi, rilevando tutti i dispositivi all’interno della rete stessa, avvisando automaticamente in caso di anomalie, tenendo sotto costante controllo la rete. Se si vogliono iniziare percorsi di digital transformation, bisogna farlo su fondamenta solide!”.
Smart manufacturing nel 2020: l’era del 5G e delle reti per fabbriche che diventano iperconnesse
Obiettivo, dunque, è quello di fabbriche iperconnesse, nelle quali sono rappresentati tutti gli aspetti di sicurezza.
“La possibilità di avere reti connesse e in real time all’interno delle aziende produttive è fondamentale: l’informazione deve transitare velocemente. Per questo lavoriamo su quella che viene definita Time Sensitive Networking, ovvero una estensione dell’Ethernet e ci permetterà di avere comunicazioni real time a tutti i livelli utilizzando gli stessi componenti. Parimenti è molto importante anche il tema del 5G in azienda, per tutto quanto riguarda il controllo della latenza, del traffico all’interno delle strutture aziendali. Siemens sta lavorando in maniera importante per garantire comunicazione wireless ad alta affidabilità su queste tipologie di infrastrutture”.
Concorda Angelo Candian, Responsabile Industrial Communication di Siemens Italia: “Per poter intraprendere un percorso di digital transformation, le aziende hanno bisogno di un’infrastruttura che faccia sì che il dato possa venire controllato in maniera efficiente, capillare e trasparente nel settore. L’infrastruttura di rete diventa fattore abilitante per consentire alle imprese di attivare il percorso di trasformazione. E in questo scenario diventa indispensabile saper collaborare con aziende competenti in ambito IT: per questo ci proponiamo sul mercato tramite dei solution partner certificati sui prodotti Siemens. Un approccio di ecosistema è oggi l’unico possibile”.
Innovazione, digitalizzazione, fabbriche connesse, sicurezza e modelli di business: il confronto
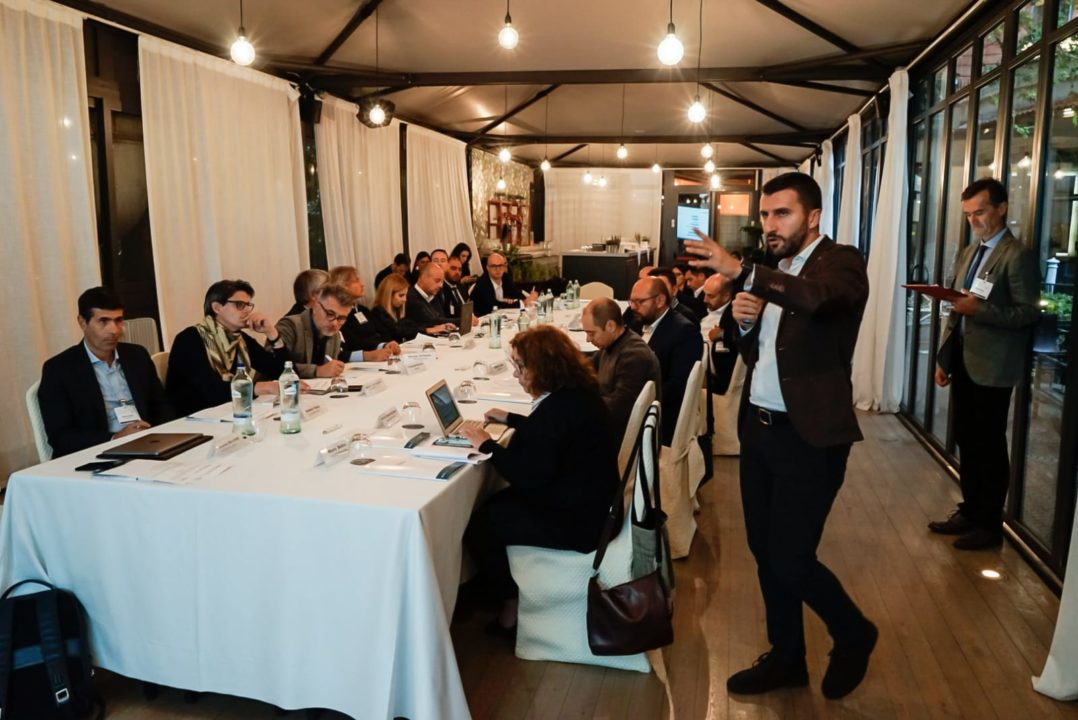
Nel momento di confronto successivo alle presentazioni, Paolo Coletti, Solution Architect and Innovation Manager, International Innovation Team di Bizerba, ha sottolineato come ancor prima di parlare di tecnologie c’è una infrastruttura culturale da creare. “Senza i soft skill non si riesce ad interpretare il mercato in cui ci si muove e diventare partner delivery. Bisogna costruire sia la filiera fisica sia quella culturale”.
Fabrizio Pagnoncelli, Tecnico commerciale Bizerba,
dal canto suo esprime preoccupazione rispetto al corretto utilizzo dei dati raccolti. “Molti dati non vengono raccolti e molti non vengono usati. A volte i Big data troppo big per i nostri clienti. Eppure, bisogna avere la consapevolezza che se è vero che il tema delle macchine connesse è diventato importante per poter ottenere gli sgravi fiscali, una volta iniziato il cammino i dati ci sono e bisogna saperli sfruttare.
A sua volta Enrico Pana, Digital Manager for Operations DAB Pumps riconosce che entrano in gioco dinamiche difficili. “Abbiamo provato a mettere competenze multidisciplinari intorno ad un tavolo favorendo la massima interattività. Ci siamo mossi in maniera progressiva e interattiva con un solo business case e coinvolgendo IT, operation e altri dipartimenti. Può funzionare. Le difficoltà sono sostanzialmente legate a una resistenza importante anche a livello culturale. E qui la chiave di volta sta nella capacità di individuare persone con tanta energia da riuscire a innestare il cambiamento: è qui che il progetto ha iniziato a muoversi”.
Uno dei temi chiave per il successo di progetti di digitalizzazione e di innovazione è nella motivazione delle persone, nella capacità di coinvolgere tutti coloro che vivono la fabbrica e che “fanno” l’azienda. E non si tratta solo di un tema di competenze che sono senza dubbio importanti.
Nicolò Rubino, IT Manager di Procos, azienda attiva nel mondo Pharma, ha a sua volta portato la propria testimonianza: “La nostra è una realtà in forte crescita, che lavora a ciclo continuo, e nella quale i manutentori devono essere reperibili in modalità 24×7: la possibilità di ricevere in modalità remota informazioni sullo stato di salute degli impianti è sicuramente un vantaggio in termini di operatività ed efficienza. Ma all’inizio non c’era interconnessione tra i sistemi di automazione industriale: la nostra prima necessità è stata mettere in comunicazione i sistemi di automazione industriale sia con il mondo esterno sia con i manutentori interni. Nel contempo, c’è stata l’esigenza di interfacciare questi sistemi con la rete corporate, rendendo accessibili le informazioni del mondo automation alle altre funzioni aziendali”.
Un tema non semplice, non solo dal punto di vista tecnico ma anche per gli aspetti di security, tenendo conto che Procos opera in un settore altamente regolato, con ispezioni periodiche da parte degli enti preposti. “Sempre più spesso l’OT ci chiede supporto per gestire le policy di accesso ai sistemi e per tutte le problematiche di integrazione a livello di networking, di directory, di management. Senza una collaborazione fattiva tra IT e OT non si va avanti”.
Anche per Danilo Duina, Responsabile sistemi informativi di ORI Mattel, il tema dell’integrazione tra IT e OT è di stretta attualità. “L’azienda opera nella filiera integrata dell’automotive. Investiamo da anni nella digitalizzazione degli impianti produttivi, abbiamo sistemi di automazione industriale, di rilevazione delle grandezze, di controllo di processo integrati con la produzione. L’integrazione tra IT e OT è un obiettivo: dobbiamo capire che le iniziative di innovazione possono nascere in qualunque area aziendale, solo se c’è un governo congiunto di queste due entità”.
Infine, Antonio Pisano, direttore sistemi informativi di Illva Saronno, torna a porre l’accento sul tema culturale: “Da alcuni mesi stiamo affrontando il tema dei big data, visto che ora con i nuovi impianti, siamo in grado di raccogliere dati di qualità, puliti, attendibili. Ma restano le difficoltà legate al fattore umano, alla capacità delle persone di adattarsi non solo alle nuove macchine, ma anche ai nuovi modelli e ai nuovi processi”. Non è semplice, ma il dialogo costante è la chiave per indirizzare correttamente tutte le criticità.
Articolo originariamente pubblicato il 22 Nov 2019