“Data Integration e Cybersecurity per l’Industria 4.0 – Digital Transformation, IT Data Integration e Data Protection: come costruire nuove forme di valore e di competitività per le imprese produttive”, questo il titolo di un incontro organizzato pochi giorni fa dalla nostra testata Industry4Business, in collaborazione con Siemens, con l’obiettivo di esplorare l’approccio migliore alla digitalizzazione, soprattutto come abilitare quella comunicazione veloce, affidabile e sicura tra sistemi di produzione, automazione e infrastruttura IT, necessaria perché la progettualità di Industria 4.0 possa prendere corpo.
Indice degli argomenti
Le opportunità dell’impresa connessa: nuovi modelli organizzativi
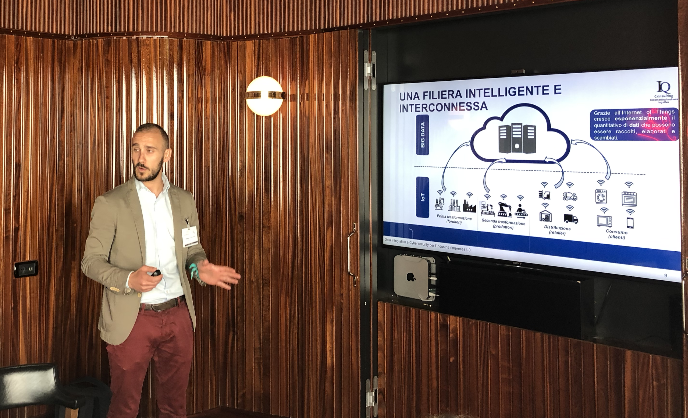
In apertura di incontro è stato Massimo Zanardini, Senior Consultant IQ Consulting, Spin-Off dell’Università degli Studi di Brescia, offrire una visione di scenario e di contesto.
“In un momento di forte evoluzione e cambiamento, nel quale si parla di personalizzazione di massa, di circular economy, di sostenibilità, di sharing economy, con Industry 4.0, al di là della definizione specifica legata al Piano Calenda, oggi si intende la modalità con cui le imprese rispondono al cambiamento. E come rispondono? Integrando, interconnettendo, spesso creando una vera e propria commistione di tecnologie tradizionali con le nuove tecnologie digitali”.
Più che di Industria 4.0 o di Impresa 4.0, prosegue Zanardini, oggi si parla di impresa connessa, termine che non riguarda più solo il processo produttivo, ma abbraccia tutte le funzioni aziendali, “al di fuori delle mura dei singoli reparti, ma anche al di fuori di una singola azienda, snodandosi lungo tutta la supply chain”.
In sostanza, è la riflessione proposta da Zanardini, non è in gioco la sola dimensione tecnologica, ci sono anche nuovi modelli organizzativi, di business e di servizio: le aziende devono focalizzarsi su più fronti e devono muoversi “in una filiera intelligente e interconnessa”
In questo scenario, il tema dell’industrial connectivity ha ruolo importante, perché consente la raccolta di dati da punti diversi della filiera stessa: linee di imballaggio, linee di produzione, linee di approvvigionamento.
“Di fatto, tutto il mondo dell’industrial connectivity porta a generare informazioni destrutturate sicuramente importanti ma che devono essere correttamente gestite”.
Attenzione a non affogare nei dati, è la prima raccomandazione di Zanardini, che spiega come oggi oltre la metà dei dati generati e raccolti appartenga alla categoria dei cosiddetti “dark data”: dati non sfruttati che creano sono complessità e costi.
“Per questo diciamo che il motore dell’Industria 4.0 è la data integration: senza una fase di allineamento dei dati provenienti da tutte le fonti non è possibile arrivare a quei livelli di predicibilità che oggi servono”.
Ma quante sono le aziende che già sono in grado di declinare concretamente ciò che questi modelli prefigurano?
“Al momento possiamo definire davvero 4.0 probabilmente solo un 5% delle aziende, anche se, va detto, sono molte di più, nell’ordine del 40% quelle che si sono messe in moto”. Protagoniste di questo scenario sono le imprese che sono in grado di integrare IT e OT, ma non è un percorso privo di ostacoli, soprattutto perché le imprese “denunciano” una cronica carenza di competenze adeguate.
“Serve un approccio olistico per includere tutti i tasselli del puzzle, tecnologie, clienti, persone. Soprattutto serve poter e saper ragionare su un orizzonte temporale ampio, dai 5 ai 10 anni. Bisogna disegnare una roadmap che parta dalla definizione del livello di maturità digitale dell’azienda per arrivare all’assessment tecnologico, all’identificazione delle priorità, fino al disegno di un piano d’azione”, conclude Zanardini.
Non c’è Industria 4.0 senza una costante attenzione alla sicurezza
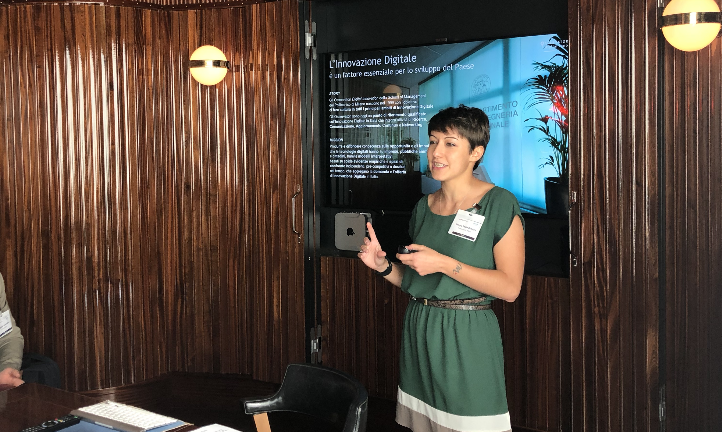
C’è un tema che tutti, a prescindere dalla tipologia di azienda o di stadi di avanzamento del percorso, non possono non prendere in considerazione ed è quello della Security.
È Giorgia Dragoni, dell’Osservatorio Information Security & Privacy del Politecnico di Milano, che analizza il tema partendo dai dati: “Secondo i dati più recenti del Clusit, lo scorso anno si sono registrati 1552 attacchi che hanno causato perdita di reputazione o di business per le aziende che li hanno subiti. Soprattutto, lo scorso anno sono cresciuti del 43 per cento i casi di attacchi a infrastrutture critiche”, racconta, citando il caso recente di attacco hacker all’industria Norsk Hydro che nel mese di marzo ha dovuto fermare la produzione a causa di un ransomware.
Lo spettro degli attacchi è quantomai ampio e va dal phishing, al ransomware fino agli attacchi mirati alle vulnerabilità OT, o a quelli che prendono di mira specifiche aziende.
La centralità dell’OT security
“Il tema dell’OT security non può dunque essere trascurato, soprattutto perché le criticità non sono certo poche, a partire dalla scarsa consapevolezza dei rischi effettivi, passando poi alle possibili vulnerabilità correlate all’interconnessione IT e OT, alla interconnessione di sistemi non progettati per esserlo, alla differenza tra i cicli di vita dei sistemi IT, generalmente molto brevi, dei sistemi OT, molto più lunghi, via via passando dal fenomeno della consumerizzazione del mondo OT”.
Quest’ultimo aspetto merita attenzione: si parla infatti dell’ingresso nel perimetro aziendale di dispositivi non pensati per il mondo industriale, con conseguente aumento della superficie d’attacco.
In effetti, spiega, se è vero che gli obiettivi di alto livello sono comuni tra IT Security e OT Security, è vero che le due funzioni non hanno lo stesso approccio e “la funzione Operations spesso non considera la security prioritaria o addirittura la considera un impedimento. Non solo, il presidio dell’OT Security è in capo all’IT e non sempre si registra in azienda la presenza di figure specializzate in materia di OT Security”.
Per questo motivo, sottolinea ancora Dragoni, serve un approccio risk based al tema della sicurezza, analizzando gli scenari di rischio e valutando correttamente i possibili impatti che deriverebbero dal verificarsi di un evento di sicurezza.
“Ci sono poi il tema delle responsabilità in caso di incidente di OT Security, quello dell’identificazione delle figure da coinvolgere in caso di incidente, per velocizzare i tempi di risposta e limitarne le conseguenze, della definizione ex ante dei meccanismi di gestione e segnalazione dell’incidente”.
La Digital Connectivity di Siemens nel segno della sicurezza
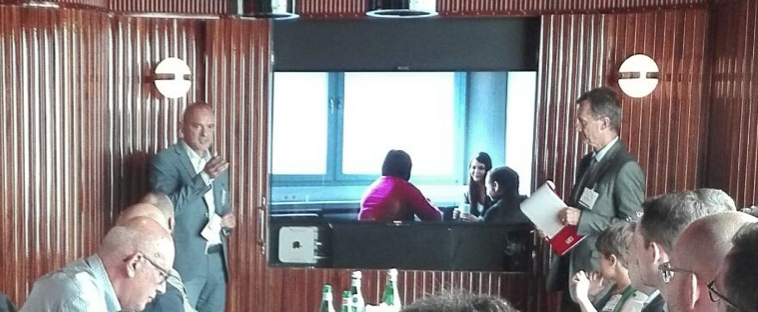
È in questo scenario che si colloca Siemens, che proprio della Digital Connectivity ha fatto la sua bandiera, nella piena consapevolezza non solo delle enormi opportunità legate all’utilizzo dei dati delle operation, ma anche dei rischi legati alla sicurezza e all’integrità dei dati.
Giuseppe Biffi, Digital Enterprise Business Development, Siemens Italia, spiega, nel confronto con il direttore di Industry4Business Mauro Bellini, la vision e l’approccio.
“Va detto che ci muoviamo in uno scenario estremamente eterogeneo, in un brownfield che per sua stessa natura impedisce un approccio omogeneo sia al tema dell’interconnessione, sia a quello della sicurezza”.
Il punto di partenza è che Siemens è il primo banco di prova delle proprie soluzioni: “Nelle nostre fabbriche usiamo le tecnologie digitali che proponiamo ai nostri clienti: capiamo come si utilizzano, come si implementano. Siamo noi stessi nei panni dei nostri clienti e siamo soggetti alle loro stesse pressioni”, racconta.
Reti industriali come sistema nervoso della fabbrica connessa
In un percorso verso la fabbrica connessa le reti industriali sono indispensabili: “Anzi, sono come il sistema nervoso centrale del corpo umano”. Tuttavia, prima di parlare di 4.0, ironizza ma non troppo Biffi, bisogna essere a posto con il 3.0. “Bisogna fare in modo che lo shop floor sia interconnesso, altrimenti i dati non possono salire verso il cloud, verso il MES, o verso il gestionale”. E non a caso questo è il primo tassello sul quale Siemens lavora nelle imprese.
Con migliaia di clienti attivi nel nostro Paese, Siemens lavora con un ampio ecosistema di partner, in grado di seguirli e supportarli: “Noi siamo presenti a livello di filiera o su clienti molto grandi: sul resto dei clienti ci appoggiamo a un ecosistema certificato, che è di fatto una nostra estensione, con conoscenze tecnologiche, di processo e di territorio”.
Interessante, per Siemens, è poi oggi il tema della servitizzazione, che sta già esplorando con alcuni clienti, soprattutto nell’ambito delle macchine di produzione, dove qualcuno comincia a vendere cicli di utilizzo del macchinario, invece che il macchinario stesso.
“In realtà – spiega Biffi – è un volano virtuoso che si innesta con una serie di ricadute positive. I clienti finiscono per adottare più tecnologie che si supportano a vicenda e abilitano scenari nuovi, come le simulazioni, le analisi what if, i digital twin”.
Sul tema della sicurezza, poi, Biffi esprime un certo ottimismo: “ La situazione è molto migliorata, anche in termini di consapevolezza: oggi è normale che si forniscano macchine con sicurezza integrata”.
Una sicurezza future-proof anche nel brownfield
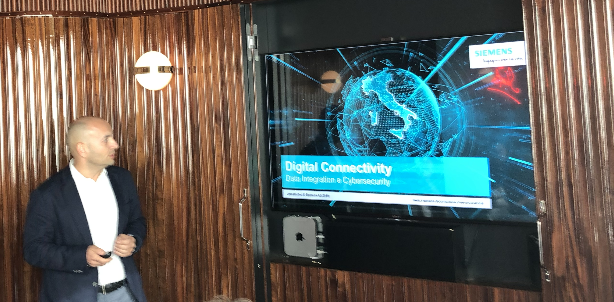
Su questo tema specifico arriva anche il contributo di Marcello Scalfi, sales specialist Industrial Networks Siemens che spiega: “In un mondo nel quale cresce il numero di reti interconnesse, abbiamo sempre più bisogno di tecnologie sicure e soprattutto future-proof. E poiché i percorsi che stiamo disegnando verso la fabbrica 4.0 sono guidati dai dati, abbiamo bisogno di trasparenza, per portare i dati da quel livello dark si cui si parlava all’inizio, fino a farli diventare davvero informazioni”.
Questo significa partire da oggetti smart e via via salire fino a portare i dati alle funzioni di business.
“Il grosso del lavoro oggi è partire dal brownfield per arrivare alla fabbrica connessa”. Sui requisiti della connectivity per il mondo industriale pochi dubbi: robustezza, elevata disponibilità, determinismo, security, safety.
“Per realizzare la spina dorsale della digitalizzazione abbiamo bisogno di celle di produzione protette, di meccanismi di ridondanza di rete, di una reale separazione tra IT e OT, di topologie di rete flessibili”, spiega, sottolineando come uno degli aspetti fondamentali della digitalizzazione è proprio la strutturazione della rete, che rappresenta anche una sfida in termini di security, soprattutto perché molti impianti non sono stati progettati per essere connessi a Internet.
E proprio in considerazione di tutte le complessità correlate a sicurezza, topologia, strutturazione, che assumono un ruolo determinante i protocolli e gli standard. Così Siemens utilizza il protocollo Profinet e gli switch Industrial Ethernet per l’integrazione di comunicazione standard e Real Time, Protocolli Standard per assicurare l’interoperabilità, nonché lo standard IEC62443, “che garantisce una defense in depth, quindi una protezione a più livelli e by design”.
“Servono standard di riferimento – prosegue Scalfi -. Rispetto al tema della sicurezza, Siemens parte dal principio di awareness, ovvero di consapevolezza sui livelli di rischio ed eroga servizi come l’industrial anomaly detection che autonomamente riconosce le anomalie e avvisa”. (leggi a questo proposito il servizio Cybersecurity per l’Industria 4.0: come produrre senza rischi)
Il tavolo di lavoro sulla digitalizzazione di fabbrica con i CIO
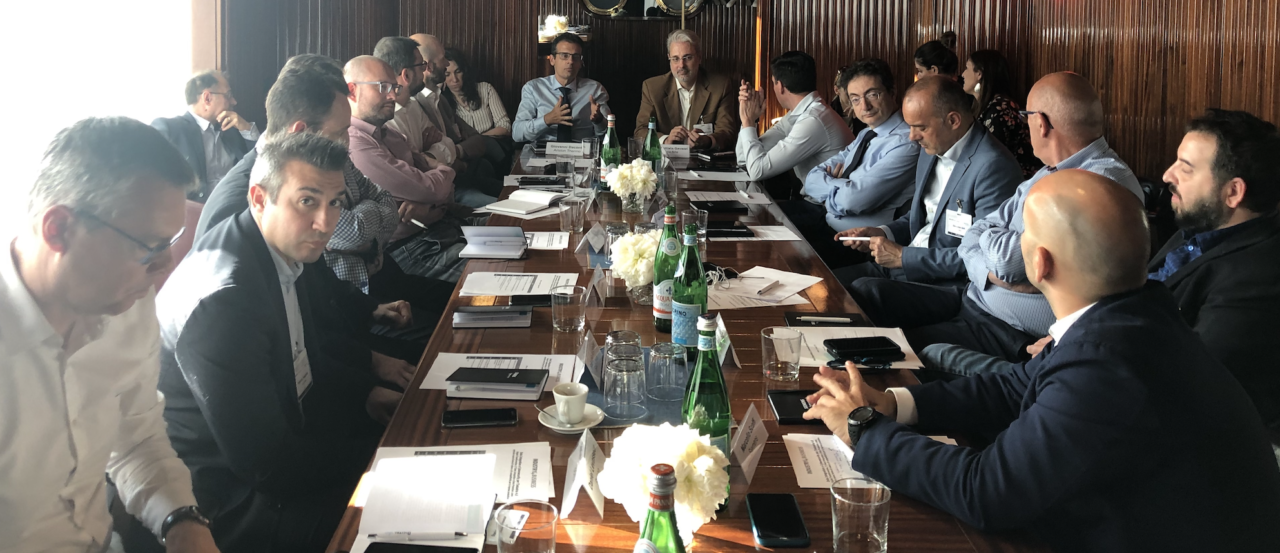
Il dibattito: CIO a confronto sulle prospettive della fabbrica connessa e sulla collaborazione IT – OT
Sui temi della digitalizzazione di fabbrica, sul ruolo dell’Industrial networking, della fabbrica connessa, della sicurezza nel mondo della produzione, della collaborazione tra IT e OT e in generale sui temi dell’innovazione digitale per il mondo della produzione si è sviluppato un interessante dibattito con il contributo di rappresentanti di importanti aziende impegnate in diversi settori del mondo manifatturiero.
Serioplast
Giancarlo Andreoli, di Serioplast, azienda manifatturiera di Bergamo specializzata nella produzione di prodotti in materie plastiche e di sistemi di produzione, spiega come in azienda sia toccato all’IT guidare il percorso di innovazione verso Industria 4.0 e ci tiene a sottolineare l’importanza strategica del dato e delle soluzioni produttive e organizzative che partono proprio dalla gestione del dato.
“Siamo partiti – sottolinea – dalla connessione degli asset e ci siamo immediatamente resi conto di una serie di problemi: protocolli aperti, connessione di PLC di diverse generazioni. Una esperienza importante che ci ha permesso di lavorare sulle conoscenze e anche sulla base delle esperienze acquisite questo stiamo valutando anche il retrofitting come opzione”.
È comunque un tema caldo: “Per noi Industria 4.0 porta vantaggi in termini di recupero economico: abbiamo 27 sedi in diverse parti del mondo e puntiamo a creare una infrastruttura di comunicazione che abiliti il dialogo con tutte le soluzioni di produzione”. La connessione di fabbrica poi a nostro avviso è da vedere come connessione tra diversi impianti produttivi. Un altro tema importante e non banale è quello della mappatura degli impianti, del censimento preciso di tutti i sistemi di produzione e del loro livello di digitalizzazione, un passaggio strategico anche per indirizzare obiettivi di compliance rispetto agli standard e per gestire lo sviluppo in modo uniforme. L’azienda ha scelto di investire su una progettualità seguita con risorse interne investendo nella crescita di competenze aziendali e per questo ha creato un gruppo di lavoro dedicato allo sviluppo e una figura professionale interna espressamente dedicata alle attività di system integration.
Balconi
Andrea Bettoni, CIO di Balconi, a sua volta sottolinea la “discrasia tra i tempi dell’IT e quelli dell’OT. L’OT vuole la velocità ed è focalizzata sulla produzione ed esprime dei kpi molto stringenti. L’IT, soprattutto per queste fasi di passaggio e di evoluzione deve procedere con collaudi e con test perché il digitale in ambiente di produzione non è come applicare il digitale “in altri ambiti”. Da due anni in azienda, Bettoni ha affrontato difficoltà di portare una soluzione di digitalizzazione nella propria realtà con macchine e sistemi di produzione datati, con la volontà di mediare tra sistemi di produzione arrivati in azienda da diversi anni e la necessità di renderli attivi in un ambiente connesso. Un tema questo comune a tante aziende italiane che vivono la coesistenza tra sistemi concepiti per essere interconnessi e macchine che hanno bisogno di essere “arricchite” di sistemi e apparti IoT.
“È chiaro che l’IT non può arroccarsi sulle proprie posizioni, però deve essere coinvolto fin dalle fasi di design, altrimenti il progetto non funziona”. Il tema è ancora una volta legato alla cultura delle imprese di produzione e di prodotto dove l’impianto di produzione e lo stabilimento hanno la priorità assoluta e – arriva a concludere -, ironizzando un po’ che “una delle battute più frequenti in azienda è che se il problema è grave, allora è compito dell’IT, se si può risolvere, allora è di competenza dell’OT”.
Rold
Di approccio e di strategia digitale parla Luca Cremona, Industrial Business Unit di ROLD, che racconta come già dieci anni fa l’azienda, di stampo familiare, abbia deciso di portare al proprio interno un manager proveniente dal mercato, con competenze del tutto nuove, soprattutto in ambito meccatronica, proprio pensando alle opportunità legate alla digitalizzazione di fabbrica.
“Questo è stato l’inizio della trasformazione di Rold verso il digitale – racconta – e verso nuovi business, anche grazie alla creazione di partnership di valore con realtà nazionali e internazionali nel mondo degli elettrodomestici, per i quali produciamo componentistica”.
Muoversi in una logica di prodotti e fabbriche connesse porta risultati tangibili, ma occorre concentrasi sui dati e sul loro valore. “Avere strumenti che raccolgono dati dalla produzione, aiuta a creare una base su cui lavorare per l’ottimizzazione dei processi e per l’innovazione”.
Rold è una realtà con più di 200 dipendenti con una forte vocazione all’esportazione e all’innovazione di prodotto. L’azienda lavora con grandi produttori di elettrodomestici per nuove soluzioni in termini di appliance in un settore che è soggetto a forti accelerazioni in termini di innovazione. Per aumentare la competitività abbiamo fatto un grosso lavoro sul processo, con la integrazione di soluzioni che coinvolgono oltre 90 macchine di produzione in diversi stabilimenti e sull’inserimento di competenze digitali e abbiamo lavorato come una software house con una forte attenzione e specializzazione sulle nostre specifiche esigenze, creando una forte competenza interna che ci ha permesso di avviare anche una forma di diversificazione del business proprio nella proposizione di queste soluzioni.
Rold è la prima “utente” delle proprie soluzioni: “Questo ci ha aiutato a capire cosa vuol dire in termini di cambiamento dei processi, cosa vuol dire gestire la digitalizzazione anche in aziende con macchine di una certa età, cosa vuol dire gestire persone e competenze che servono per far funzionare il digitale nella fabbrica”. Tra l’altro il World Economic Forum WEF ha selezionato ROLD con Lighthouse plant, ovvero ha riconosciuto il valore del progetto ROLD in termini di lean, qualità, coinvolgimento del personale.
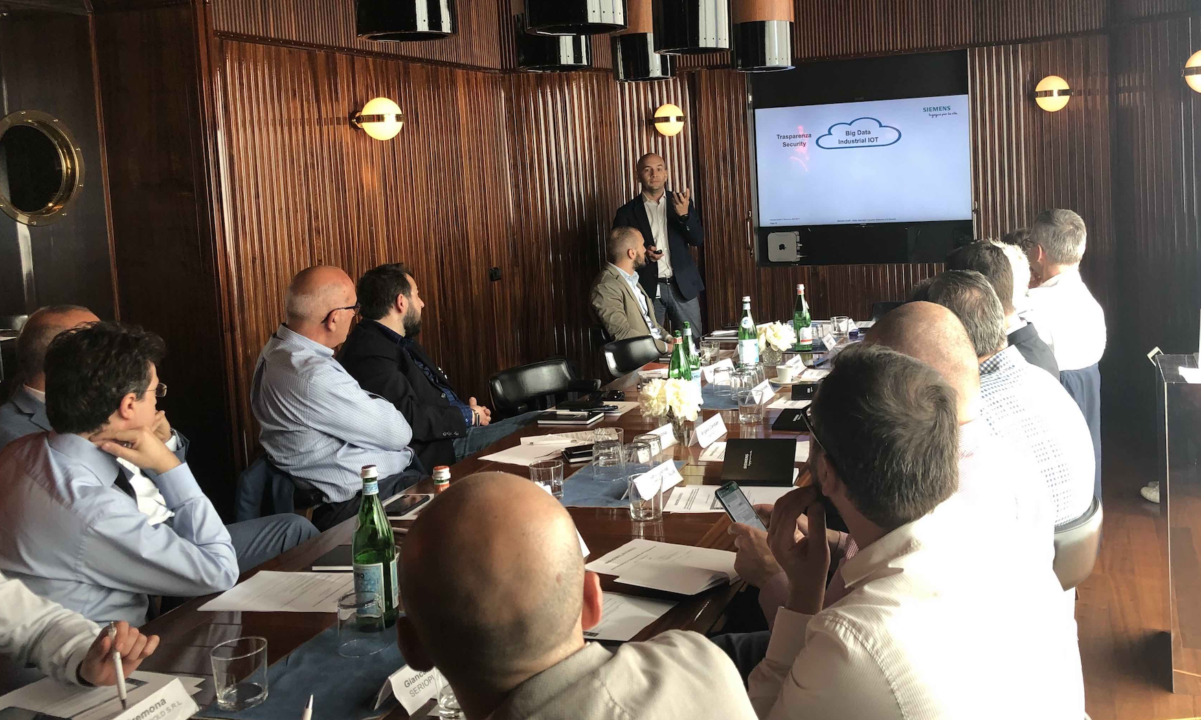
Laboratoires Boiron
Daniel Levasseur, CIO & Chief Logistic Officer – CLO Laboratoires Boiron, concorda sul fatto che fabbrica e digitale si muovono ancora a velocità diverse ed è un tema IT quello di arrivare a definire delle modalità e delle nuove forme di collaborazione: “Se vogliamo, il paradosso è quello di aver dimostrato che il processo di modernizzazione si può fare, che l’IT ha lasciato la sua torre ed è andata sul campo, in ambiente di produzione. Tuttavia, questa vicinanza non si è ancora pienamente realizzata con le operation”. C’è un grande lavoro anche di tipo culturale che deve essere portato avanti per le differenze di approccio, di metodo e di sensibilità a determinati temi. L’IT è abituata all’apertura, alla connessione, il mondo OT ha gestito la propria innovazione all’interno di perimetri molto definiti e molto “protetti”.
L’ambiente produttivo è un ecosistema a sé e occorre trovare una corretta mediazione tra l’apertura della digitalizzazione e il “bisogno” di sicurezza dello “stabilimento”. “Anche in uno scenario di informatizzazione sempre più spinta, la fabbrica è una cosa e il digitale è un’altra. Ci sono barriere e timori, soprattutto quando si parla di mettere in rete una macchina: la macchina va equipaggiata con sensori e sistemi, ma il presupposto è che i sistemi devono essere nella condizione di parlare la stessa lingua e devono essere in grado di farlo in modo sicuro”.
Levasseur aggiunge poi che i processi legati alla connessione di fabbrica, alla condivisione dei dati e alla digitalizzazione della produzione porta anche a nuove forme di valutazione dei rischi, a una riconsiderazione profonda dei temi legati alla sicurezza e alle misure per prevenire le minacce o ancora meglio per comprenderle. Anche in questo caso c’è un tema culturale che se ben gestito può portare benefici molto chiari e molto evidenti a livello di business.
Mapei
Di un clima favorevole alla collaborazione tra il mondo digitale e le operation produttive parla Lorenzo Anzola, corporate IT Director in Mapei, e sottolinea come grazie all’innovazione digitale sia cresciuta la collaborazione tra il mondo IT e il mondo della produzione, anche con lo spirito e la volontà di superare alcuni aspetti importanti a livello strutturale. Il tema sul tappeto attiene alla necessità di gestire impianti eterogenei: c’è un brownfield che consegna tante differenze che vanno gestite e che impongono un confronto con situazioni in cui si ha a che fare con macchine e sistemi di automazione che vanno dai 2 ai 10 ai 20 anni di età”. L’IT non è “abituata” a questi cicli di vita.
Ma a parte questa dimensione Anzola porta l’attenzione sul tema del dato e sulla centralità del dato per tutta l’azienda. Prima di tutto si sente la necessità di una governance centrale proprio sui dati. Grazie all’ingresso di tanti apparati, dell’Internet of Things a tanti livelli, si dispone di una crescente ricchezza di informazioni ed è sempre più importante capire come utilizzarli e come gestirli. La realtà poi premia la capacità di iniziativa: “Alla fine i dati sono di chi li utilizza al meglio”
Anzola si dice assolutamente convinto che “in una azienda di processo, dove si lavora 364 giorni all’anno, dove la produzione è centrale per il valore dell’azienda è indispensabile che qualsiasi processo di innovazione e di digitalizzazione possa contare su una vera collaborazione tra IT e OT.
IVM Chemicals
Adriano Marrocco, CIO di IVM Chemicals, sottolinea che “investire in progetti di Industria 4.0 o di digitalizzazione della fabbrica richieda lungimiranza in termini manageriali. E’ molto importante saper aggiungere anche una capacità di visione, ovvero di contestualizzare anche eventuali scelte tattiche all’interno di un disegno, dove l’innovazione è accompagnata anche da interventi a livello organizzativo.
In particolare Marrocco sottolinea che in azienda ha avuto modo di iniziare a collaborare con la produzione su alcuni temi specifici. un esempio è sul tema della sicurezza, che in fondo è uno degli elementi di maggiore importanza e che è in grado di far crescere consapevolezza e sensibilità. Un esempio aiuta a capire questo passaggio, e ricorda quando i sistemi SCADA non erano gestiti dall’IT ma a fronte di un incidente si è reso necessario effettuare interventi, anche di tipo conoscitivo, che hanno convinto la direzione della necessità di riportare all’IT anche questa parte”.
Solo – Fattorie Scaldasole
Fabrizio Argiolas, CIO di Solo – Fattorie Scaldasole, porta la sua testimonianza di un’azienda che sviluppato diverse esperienze e che con queste ha portato “in casa” nuove competenze : “Da noi il mondo delle operation aveva iniziato un processo di innovazione e di digitalizzazione partendo da una serie di esigenze specifiche legate alla produzione, ma dopo due anni ci si è resi conto che i risultati non avevano raggiunto le aspettative. Ecco che in quel momento si è deciso di chiamare in causa il mondo dell’IT, anche se con un coinvolgimento parziale. Ci sono state circostanze che hanno favorito un avvicinamento e lo sviluppo di nuove forme di collaborazione. Non è ancora la soluzione ottimale, dal momento che ancora non riusciamo a creare un reale coordinamento tra IT e OT: ma ci sono stati passi avanti molto importanti e oggi siamo nella condizione di scegliere una piattaforma in grado di integrare più linee e impianti e stiamo lavorando e ragionando a una modalità progettuale che permetta di affrontare e risolvere i temi della sicurezza. Nella nostra esperienza possiamo dire che non basta attivare delle forme di collaborazione, anche se molto intense e con obiettivi definiti, per ottenere risultati importanti anche dal punto di vista della strategia serve una vera e propria cabina di regia”.
La difficoltà nella selezione del giusto partner è un altro tema sul quale Marrocco porta la propria attenzione: “I fornitori OT sono fortemente orientati verso il “loro mondo “e non si rivolgono di default al mondo della tecnologia, e questo alla lunga diventa un problema. Serve un approccio nuovo anche a livello di identificazione dei partner e dei fornitori”.
Ariston Thermo Group
Da Giovanni Daconto, CIO di Ariston Thermo Group arrivano segnali positivi: “Come tante aziende, anche noi stiamo investendo nella digitalizzazione delle linee di produzione. Abbiamo progetti di innovazione che portano il digitale nello stabilimento e nei reparti di produzione. Devo dire che in tutto questo percorso c’è stato un importante coinvolgimento dell’IT, ma non c’è dubbio che l’integrazione sia ancora da migliorare. In particolare per Daconto la chiave di lettura di questo processo di innovazione deve essere collocata nei dati e nel valore del dato per l’azienda. “”I dati vengono usati ancora poco rispetto alle loro potenzialità e in particolare risiedono prevalentemente su robot e PLC. Accanto a questo aspetto c’è anche un approccio disomogeneo alla gestione del dato, che deriva appunto anche da come viene visto e gestito il sistema dal quale arriva “quel dato”. E’ molto importante lavorare alla costruzione di una visione di insieme, ed è estremamente importante capire e definire in modo preciso quali sono e dove sono i layer di integrazione”.
Un discorso a parte merita poi il tema della sicurezza, e su questo Daconto sottolinea come in un ambiente come quello di fabbrica, nel quale lavorano più fornitori con sistemi diversi, pensati e progettati in epoche diverse e spesso con modalità operative eterogenee, la sicurezza rischia di essere penalizza e soprattutto corre il rischio di non essere vissuta in modo realmente strutturale. Il manager avverte la necessità di identificare un soggetto che sia nella condizione di guardare a questo fenomeno e di avere una “visione” più oggettiva proprio per arrivare a ottenere una maggiore omogeneità di approccio”.
Solvay Chimica
Le aziende sono anche luoghi si “sperimentazione”, di creazione e sviluppo di esperienze che entrano a far parte del “bagaglio” aziendale e permettono di creare nuovo valore, ad esempio identificando il modo più appropriato, per ciascuna azienda, di indirizzare il proprio percorso di innovazione. Antonio Giustino, Information Systems & Industrial Risk Manager in Solvay Chimica, racconta come nel caso della sua azienda si sia scelto di creare un laboratorio Internet of Things con una focalizzazione sull’Industrial IoT. Un progetto che ha visto anche la collaborazione di società esterne e che ha permesso di capire come affrontare la diffusione di progetti basati su sensori e apparati IoT, creando anche le competenze per poi gestire i progetti stessi.
“Si tratta di un approccio con una sua specificità che permette di esprimere un diverso valore rispetto al tradizionale coinvolgimento dell’IT nei processi e nei progetti di digitalizzazione della fabbrica. Sui temi della sicurezza, occorre essere molto determinati e categorici: da una parte la security è la base che deve caratterizzare tutti i prodotti Internet of Things e non solo e così pure le logiche legate, per altri versi, alla sicurezza fisica. Ma Giustino ci tiene a sottolineare anche il ruolo fondamentale degli standard. Su questo tema è importante dare vita a una forma di corresponsabilità tra tutti gli attori in un progetto che deve comprendere anche clienti e fornitori. La sicurezza è un fattore che deve riguardare tutti e che si “vince” con il contributo di tutti gli attori. Occorre avere ben chiaro che occorre essere proattivi e chi non chiede e pretende sicurezza rischia di essere responsabile come chi non è in grado di fornirla e garantirla”.
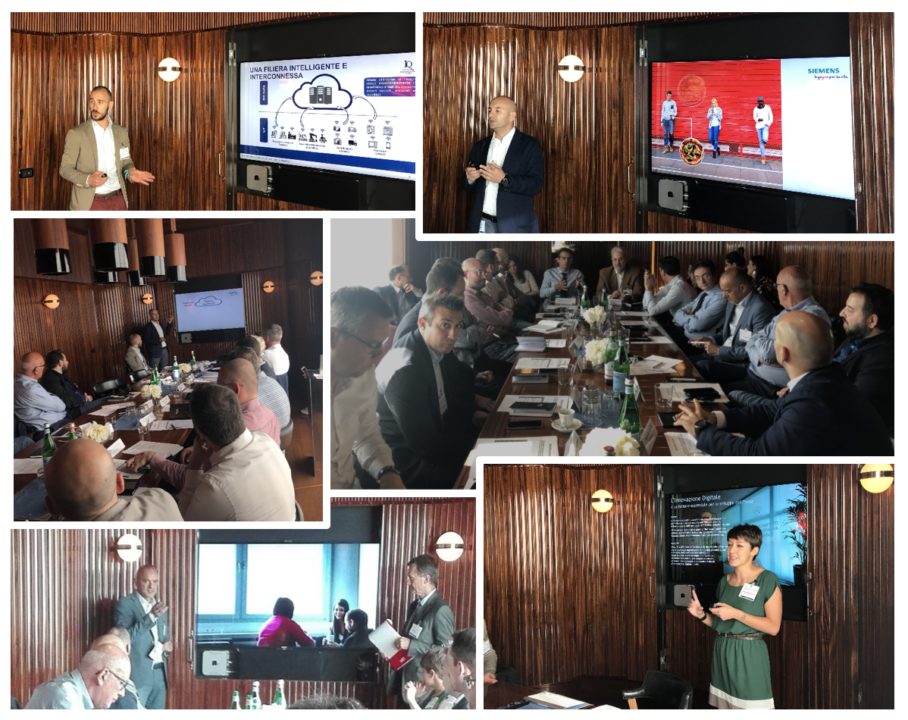