La manifattura veneta della lavorazione di metalli speciali ha deciso di puntare sul digitale, con la trasformazione digitale (digitalizzazione) di un’azienda tradizionale in un’organizzazione data driven attraverso la tecnologia, in sole sei settimane grazie alla metodologia Agile.
Si tratta di WPI, Welded Pipe Industries, azienda situata a Padova, specializzata nella produzione di costruzioni saldate per il settore chimico e petrolifero. Un’organizzazione giovane e dinamica che negli anni è riuscita a guadagnarsi una consolidata reputazione sui mercati internazionali: dalle grandi compagnie petrolifere, alle multinazionali della chimica.
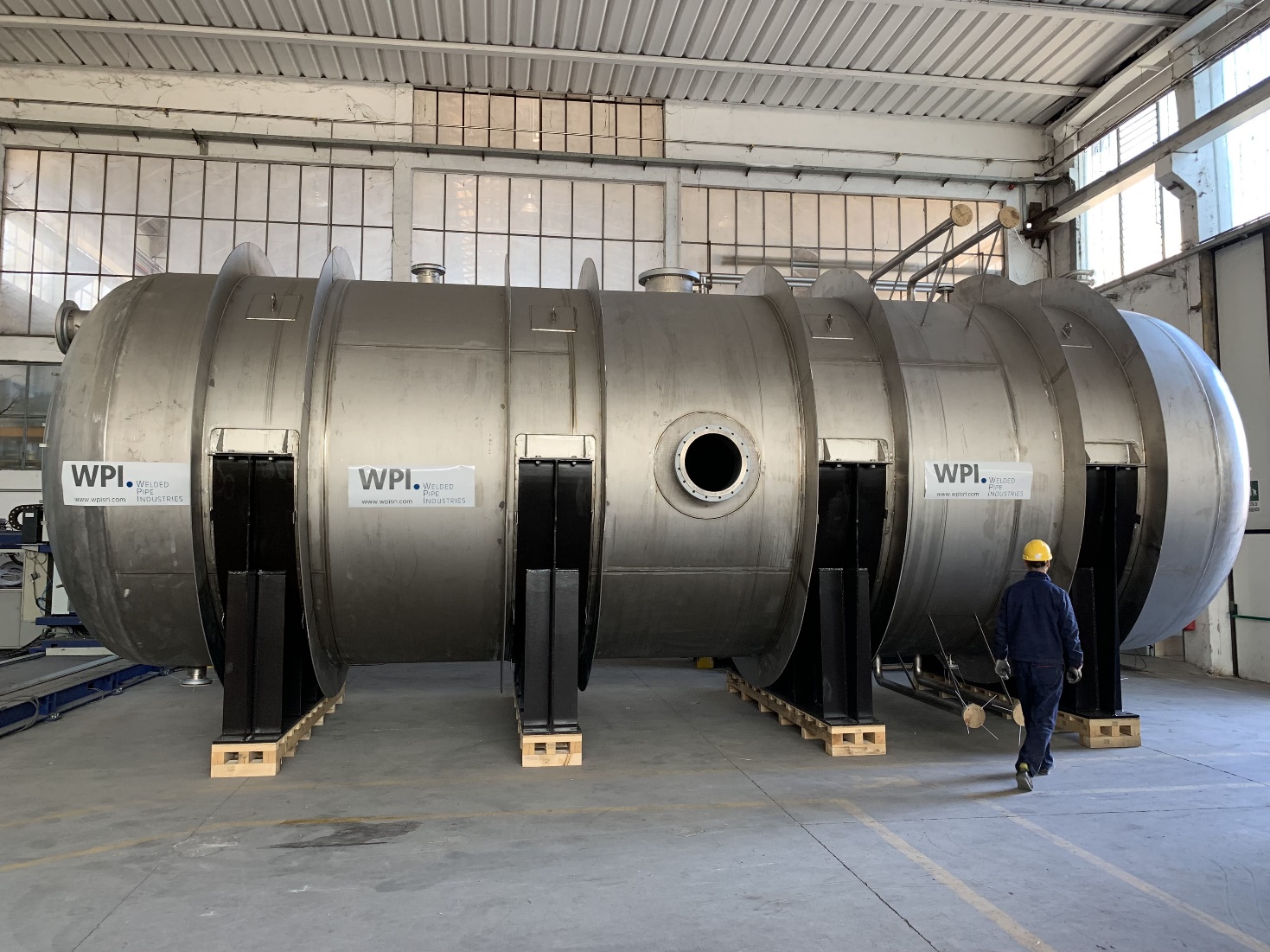
Indice degli argomenti
Un’azienda competitiva sul mercato internazionale della lavorazione di metalli speciali
WPI è un’azienda di piccole dimensioni, con un totale di circa 30 dipendenti, che lavora in un settore altamente specializzato, ovvero la costruzione di tubazioni saldate e di apparecchi di processo in pressione per l’industria chimica e oil and gas. Si occupa, dunque, della lavorazione di materiali speciali tra cui titanio, leghe di nichel, duplex, superduplex, 904L, 254SMO, acciai austenitici e super austenitici. Per questo motivo, WPI si trova a competere con produttori qualificati di ogni parte del mondo, dal Canada alla Cina, e a dialogare con project procurement manager molto preparati dei più grossi contractor del settore, come ad esempio SAIPEM in Italia.
È proprio il bisogno di far fronte a un mercato altamente competitivo che ha spinto l’azienda a cercare degli esperti della digitalizzazione per sfruttare le leve offerte dalla tecnologia. Si è rivolta così a un’innovativa società sempre con sede a Padova, specializzata nella digitalizzazione del mondo manifatturiero, che l’ha affiancata nel percorso di digital transformation, sviluppandolo in sole sei settimane attraverso la metodologia Agile.
La necessità di mappare i processi per stimare i costi
Dopo un’analisi delle reali esigenze di WPI, è emerso che la sua necessità principale era quella di disporre di strumenti che potessero dare un’indicazione sui tempi e sui costi di produzione per capire in modo più approfondito le spese necessarie per la realizzazione di un determinato manufatto e calibrare i preventivi di lavori successivi su una base storica attendibile.
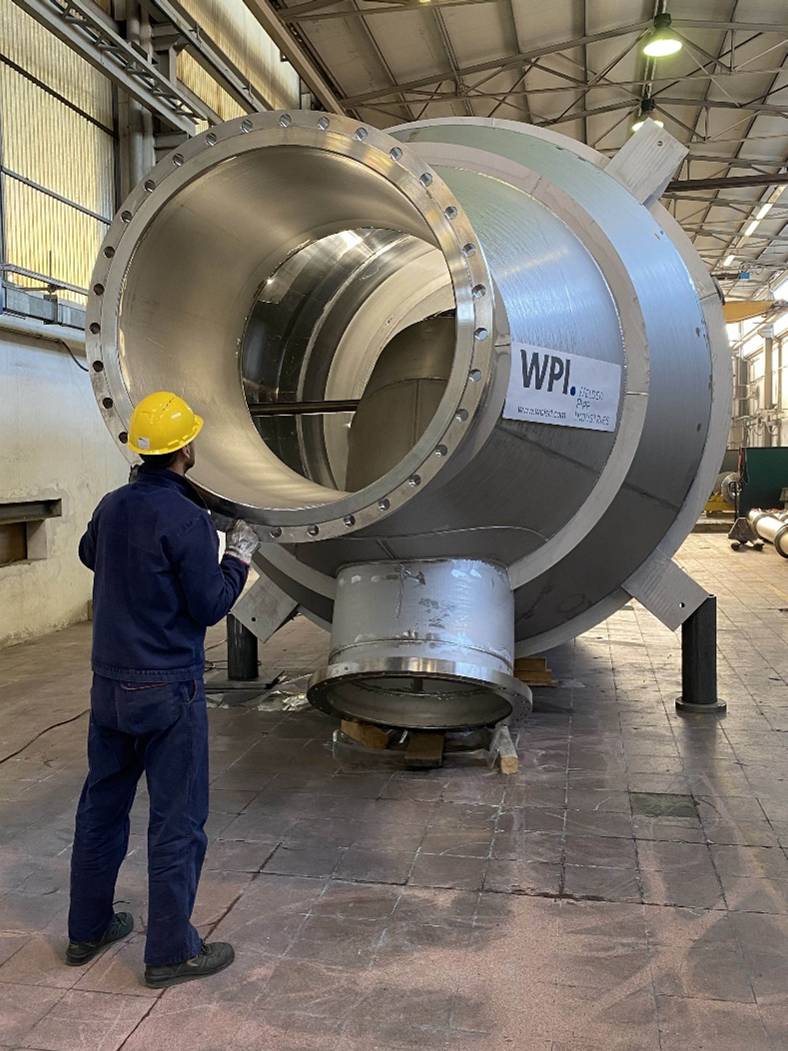
Su questo aspetto, il principale pain point dell’azienda consisteva nella mancanza di una mappatura dettagliata del processo produttivo, che si traduceva nell’impossibilità di tracciare i tempi di produzione, di identificare eventuali inefficienze e sprechi e di stimare in modo corretto la marginalità di commessa e i successivi lavori. Allo stesso tempo, la necessità era quella di sviluppare uno strumento semplice e intuitivo, che fosse utilizzabile da tutto il personale dell’ufficio tecnico e della produzione.
Si è deciso, dunque, di sviluppare un prodotto completamente personalizzato, e di farlo con la metodologia Agile. Questa scelta ha consentito di lavorare in modo veloce e dinamico, mettendo sempre al centro del processo le persone .
Concretamente, si è deciso di articolare il progetto di trasformazione digitale in sei settimane, suddivise in tre diversi sprint, ognuno dei quali caratterizzato da un obiettivo concreto da raggiungere. Il focus è stato posto sull’avanzamento di commessa. Infatti, uno dei temi emersi era la necessità di dotarsi di strumenti che permettessero la mappatura del processo (sequenze di lavoro), così come avviene in produzione, e contemporaneamente di rilevare i tempi di esecuzione delle singole sequenze. In questo modo sarà possibile: acquisire i veri cicli di lavoro, oggi principalmente patrimonio del singolo operaio specializzato; distinguere le attività di lavoro dalle rilavorazioni e acquisire i tempi di processo e di attraversamento di ogni singola commessa.
Con questi dati si potrà poi individuare gli sprechi e progettare azioni di miglioramento per efficientare il processo stesso e migliorare la capacità di stimare i futuri lavori.
La soluzione: il Custom Manufacturing Execution System (MES)
Dalla prima attività di analisi, che ha lo scopo di chiarire le necessità dell’azienda e gli obiettivi da perseguire, è emerso che i manufatti, seppur diversi, seguono un processo simile. Ma la categoria che assorbe più risorse e su cui si desidera avere una maggiore e migliore quantità di dati consuntivi sono i “pressure vessels” su cui viene sviluppata un’analisi specifica.
Tale analisi consiste nello studio del processo di fabbricazione dei manufatti in “Fasi”, “Attività” e “Cambi Fase”; nell’individuazione delle principali esigenze di raccolta dati e interazioni uomo-macchina (raccolta dati) e nell’identificazione dei KPI prestazionali del processo che si desidera visualizzare nelle dashboard.
L’output successivo alla prima fase analitica è la creazione di un Custom Manufacturing Execution System (MES), uno strumento che consente di conoscere nel dettaglio e in tempo reale i costi di produzione di ogni artefatto e stimare in modo accurato le commesse future.
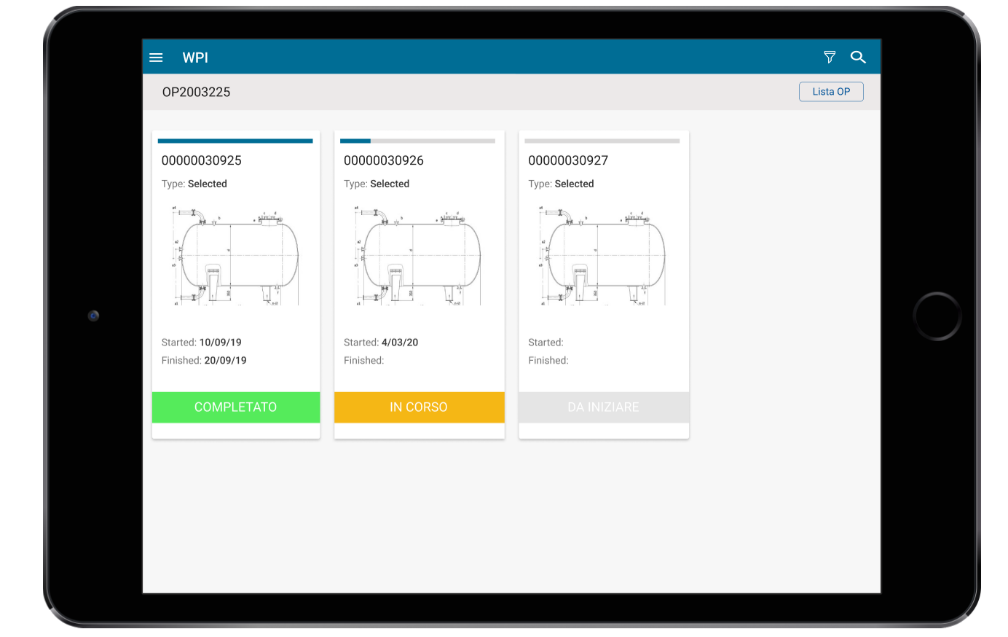
Sulla base delle informazioni ottenute, viene prodotto un mock up dell’applicativo. In esso viene prevista la creazione dell’ordine di produzione, che appare suddiviso in diverse attività raggruppate in fasi. L’operatore di turno selezionerà l’ordine, e mano a mano registrerà le attività che verranno svolte.
Il funzionamento del MES prevede che ogni operatore abbia accesso all’applicativo attraverso un tablet personale. Nella schermata di login, l’utente, dopo essersi autentificato, accede alle diverse funzionalità in relazione al suo ruolo. Dall’applicativo, l’utente può inserire e modificare l’ordine di produzione del manufatto sia singolarmente che in modo massivo; inoltre, in un’apposita sezione è possibile visualizzare gli ordini in modo aggregato e verificarne i dettagli e lo stato di avanzamento nel processo produttivo. La piattaforma comprende anche un Welding Book, ovvero la vista di tutti i giunti del manufatto, le specifiche tecniche e i documenti di riferimento per l’operatore.
Il sistema consente di visualizzare le prestazioni dei singoli seriali della commessa e di monitorare i tempi e l’avanzamento del processo. Il tutto in tempo reale. L’operatore, in base alla fase del processo produttivo, potrà scegliere l’elemento su cui lavorare e l’attività da svolgere, con la possibilità di accedere a tutti i dati del pezzo in real-time (caratteristiche tecniche, fase di avanzamento). Semplicemente interagendo con la piattaforma, gli altri colleghi saranno aggiornati in tempo reale sul corso dell’attività.
Una volta concluso il processo, sarà possibile visualizzare la lista di tutte le attività e i relativi dettagli. Infine, grazie all’integrazione il calendario consegne, si possono facilmente controllare e gestire le commesse, decidendo di visualizzarle a seconda di determinati filtri scelti al momento dall’utente.
I risultati: dati in tempo reale a disposizione di tutto il team
Grazie al MES, ora WPI è in grado di stimare in modo corretto la marginalità di commessa e di migliorare i successivi lavori. infatti, i dati raccolti dall’applicativo consentono di conoscere nel dettaglio e in tempo reale i costi di produzione di ogni artefatto e di calibrare su di essi i preventivi dei lavori futuri. Attraverso l’utilizzo della metodologia Agile, lo staff di WPI ha potuto vedere in modo concreto i progressi del progetto, non solo una volta concluso, ma anche durante il suo svolgimento, scegliendo le funzionalità a cui dare priorità e lasciando le altre in un “back log” per i futuri sviluppi. La metodologia, infatti, prevede la suddivisione del progetto in diversi sprint, ognuno dei quali è caratterizzato da un sotto-obiettivo concreto da raggiungere. Questi step intermedi hanno dato la possibilità all’organizzazione di vedere crescere il progetto in tutte le sue fasi, verificando il raggiungimento di goal intermedi, senza perdere di vista l’obiettivo finale.
Già dopo i primi risultati ottenuti attraverso l’utilizzo della tecnologia, WPI ha dichiarato di essere estremamente soddisfatta e ha deciso di investire ulteriormente sulla digitalizzazione dell’azienda.
In particolare, c’è la volontà di ampliare le funzionalità e le potenzialità del MES. Grazie ai dati che verranno raccolti dall’utilizzo dell’applicativo, emergeranno nuove necessità, sulla base delle quali si andranno a stabilire le nuove features da implementare. Primo tra i prossimi progetti che verranno realizzati sarà l’integrazione dell’applicazione con il sistema gestionale, allo scopo di avere un unico collettore di dati a 360 gradi all’interno dell’organizzazione.