SCM Zanussi srl è un’azienda con sede a Cordenons (PN) oggi riconosciuta quale punto di riferimento globale nel campo della meccanica automobilistica. In particolare, è stata l’introduzione del digitale ad aver rivoluzionato i tradizionali processi di lavoro, permettendo all’impresa di conseguire nuovi traguardi in termini di efficienza e di ritorno economico. Con una digitalizzazione progressiva, metodica e incentrata su pochi obiettivi focali SCM Zanussi è un esempio per tutte le realtà industriali interessate a muovere i primi passi verso un’applicazione intelligente delle tecnologie 4.0. Per questo motivo l’azienda è stata selezionata da IP4FVG, il digital innovation hub regionale, tra i “FARI Manifatturieri” della trasformazione digitale del Friuli Venezia-Giulia.
Indice degli argomenti
SCM Zanussi: storia ed evoluzione
SCM Zanussi vanta attualmente più di mezzo secolo di attività. Fondata nel 1964 dai fratelli Rolando e Giuseppe Zanussi, la gestione dell’impresa è stata assunta molti anni fa dagli eredi Enrico Zanussi e Marco Zanussi, rispettivamente oggi presidente e amministratore delegato.
Con un plant produttivo in Italia e una filiale dedicata al service in Austria, SCM Zanussi si occupa della progettazione e produzione di stampi per la pressofusione di leghe leggere destinati alla realizzazione di componenti per il settore automobilistico.
Nel corso della sua lunga attività l’azienda è evoluta progressivamente, fino a imporsi quale leader internazionale del settore: più del 90% della sua produzione è destinata oggi all’export. Per farlo, si è resa necessaria una trasformazione identitaria: da una realtà d’impresa marcatamente “artigianale” a un’attività organizzata secondo criteri industriali di efficienza ed efficacia, in grado di proporsi alle più importanti case automotive del mondo. È stato appunto l’impegno profuso nel migliorare costantemente la performance dei processi ad avvicinare il team Zanussi alla trasformazione digitale, sviluppando soluzioni che le sono valse la nomina a Faro Manifatturiero del Friuli Venezia-Giulia. In particolare, il merito riconosciuto all’azienda dalla giuria riguarda gli interventi di revamping e il retrofitting degli impianti che hanno agevolato l’analisi dei parametri critici di lavorazione e il conseguente miglioramento delle prestazioni operative.
Il primo passo verso la digitalizzazione: il Sentinel
La fresatura di precisione di componenti particolarmente voluminosi, come quelli lavorati da SCM Zanussi, comporta l’utilizzo di CNC di grandissime dimensioni e potenza, oltre ad alte asportazioni nella fase di sgrossatura che aumentano il rischio di usura prematura e rottura dell’utensile. Di norma, la prevenzione del rischio è affidata alla sorveglianza dell’operatore, il quale decide di intervenire interrompendo il processo nel caso intuisca, sulla base della propria esperienza, eventuali complicanze durante il funzionamento della fresatrice, in modo da tutelare sia l’integrità della macchina, sia quella del manufatto.
Obiettivo dell’azienda è stato superare questo tradizionale approccio di lavoro, affidando il controllo dei macchinari a strumenti automatici, oggettivi ed estremamente affidabili. È stato dunque progettato il Sentinel: un sistema di monitoraggio in tempo reale capace di raccogliere costantemente dati dalle linee produttive, analizzarli e stabilire per ogni materiale, per ogni tipo di lavorazione, per ogni strategia di fresatura soglie massime di efficienza connesse con il rendimento massimo dell’utensile e del macchinario. Il sistema di monitoraggio permette cioè alla macchina di lavorare al limite delle possibilità dell’utensile per il maggior tempo possibile assicurando, anche in assenza di operatori, gli adeguati controlli. È il sistema stesso, infatti, ad impedire agli strumenti di superare i limiti fisici riconosciuti ed evitare conseguenti rischi di rottura o collisione.
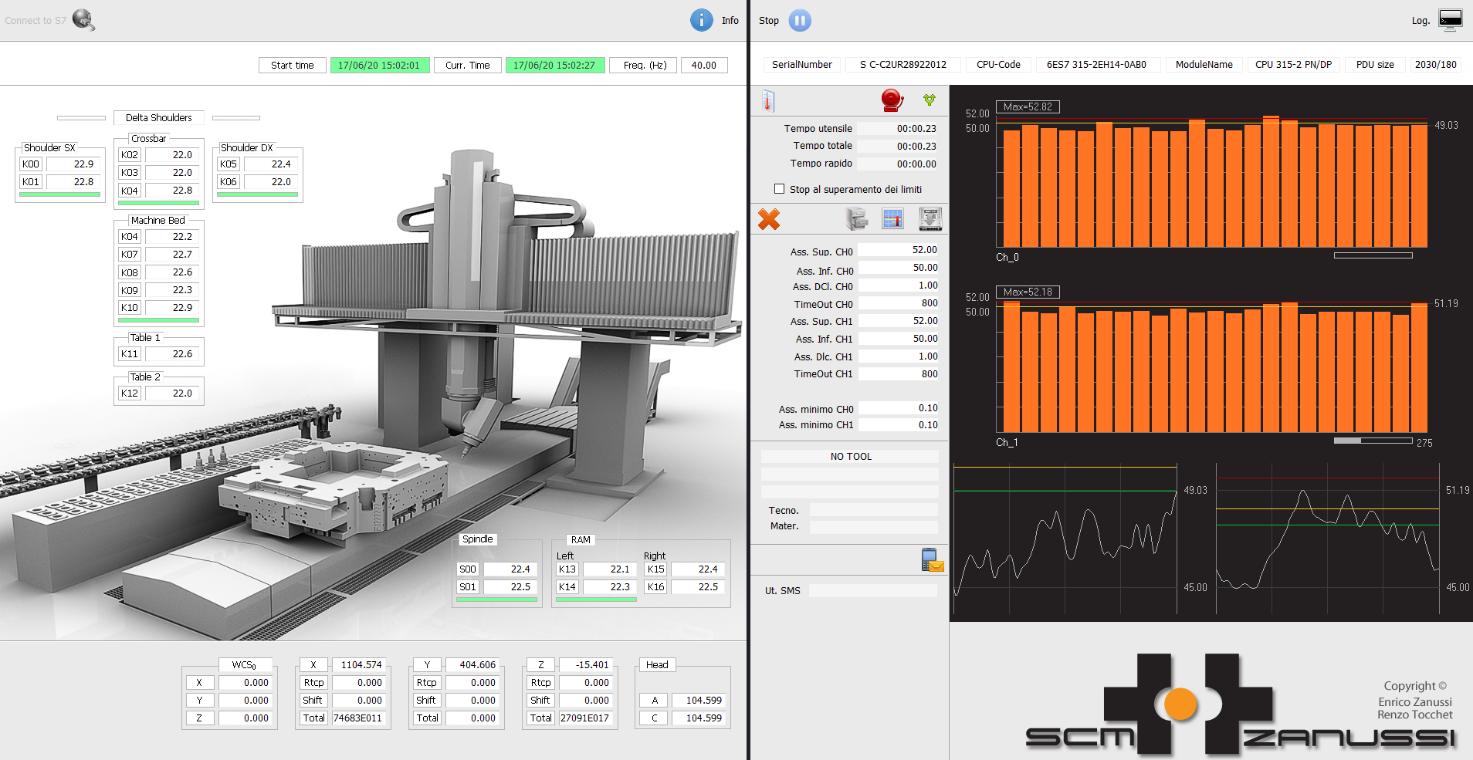
Figura: schermata del sistema Sentinel
Ma prevenire possibili condizioni di rischio non è il solo scopo del Sentinel e della data collection.
I dati raccolti e organizzati in un unico database vengono infatti riutilizzati per analisi multidirezionali finalizzate a migliorare le strategie di lavorazione (dalla velocità, agli avanzamenti, alla profondità di asportazione). Analisi che si concentrano, oltre che sull’acquisizione di parametri tecnologici, anche su aspetti di carattere economico, considerando il rapporto costi/benefici per ciascuna delle diverse strategie adottate.
L’efficientamento dei processi ha riguardato, in particolar modo, due aspetti: l’asportazione effettiva di truciolo e le operazioni unattended. Da un lato, infatti, è stato notevolmente ottimizzato il cosiddetto “contatto truciolo”, cioè il tempo impiegato dall’utensile per prelevare e asportare il truciolo in eccesso, dall’altro le ore di lavoro svolte in assenza dell’operatore (durante la notte nei fine settimana) sono incrementate in modo significativo.
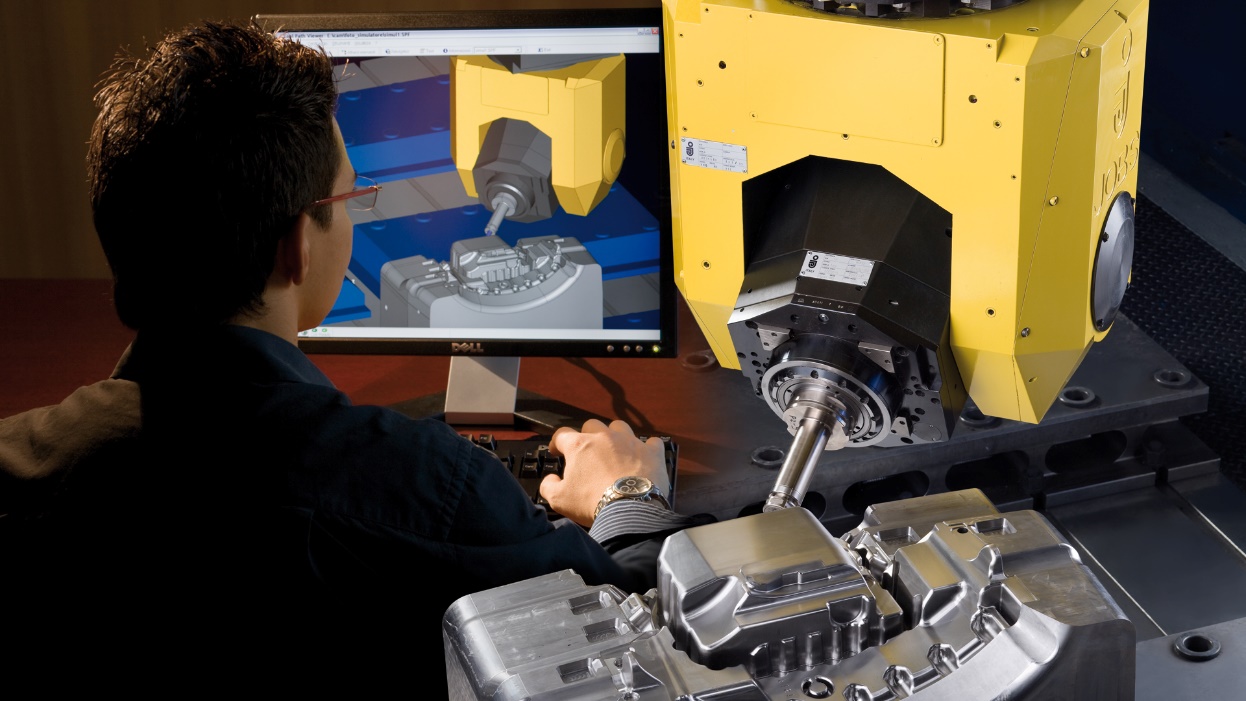
Figura: il CAM di SCM Zanussi
Gli sviluppi: dal revamping al monitoraggio della temperatura
Il primo passo verso la completa digitalizzazione è stata dunque l’implementazione di sistemi di controllo e programmazione della produzione che avessero un duplice scopo:
- raccogliere dati dalla linea produttiva da cui ricavare feedback utili, in termini sia tecnologici che economici, sul corretto funzionamento delle diverse fasi di lavorazione.
- mantenere un controllo in tempo reale lungo tutto il processo produttivo.
Punto qualificante di questa strategia è stata l’elaborazione di un sistema proprietario hardware e software in grado di acquisire in real time i parametri di lavorazione dalle macchine sensorizzate, onde ricavare una base di dati atta a definire, oltre ai livelli di massimo rendimento e le soglie di assoluta sicurezza entro cui i centri di lavoro CNC devono operare, anche i margini di ottimizzazione dei percorsi utensile. Ciò ha permesso all’azienda di incrementare l’efficienza delle operazioni, standardizzando il più possibile i processi produttivi, definire un percorso di miglioramento continuo delle tecnologie adottate e individuare le strategie di lavorazione più adatte per ridurre il consumo energetico, l’usura dei macchinari e il consumo di utensili.
Nello specifico, il Sentinel è in grado di leggere i segnali dal sistema di sensorizzazione e, attraverso un’apposita scheda di acquisizione, di distribuirli lungo diversi canali in tempo reale e ad alta frequenza (fino a 200 Hz), monitorando gli sforzi distribuiti sugli assi della macchina e sull’utensile stesso. I sensori implementati sono di diverso tipo: alcuni rilevano le vibrazioni e le pressioni dell’utensile, altri sono sensori di acquisizione e assorbimento di potenza, altri ancora misurano la temperatura della macchina. Grazie a quest’ultimi, in particolare, l’azienda è riuscita a far fronte ad un’esigenza importante, legata al monitoraggio della temperatura negli ambienti di lavoro. Avendo grossi blocchi in lavorazione, questi risultano essere molto sensibili agli sbalzi di calore durante l’anno, da qui la necessità di mantenerli costantemente a temperatura ottimale. Proprio attraverso un lavoro di raccolta dati, applicato con cadenze regolari, si è riusciti a risalire al comportamento della macchina ad una data temperatura e stabilirne la relativa deriva termica. Sulla base di tali informazioni è stato poi progettato un software che, agendo direttamente sul CNC, modifica la cinematica del macchinario, compensandone al bisogno le derive termiche.
Inoltre, l’introduzione del sofisticato sistema di monitoraggio innanzi descritto ha permesso all’azienda di compiere un ulteriore passo avanti in tema di digitalizzazione, ossia attuare il revamping completo di grandi macchine per l’asportazione del truciolo. Macchine che, pur essendo ormai obsolete, presentano caratteristiche fisiche e strutturali difficili da reperire nei macchinari di moderna costruzione. La profonda conoscenza delle fasi di lavorazione e delle logiche di controllo del processo di produzione ha permesso a SCM Zanussi di rinnovare le proprie macchine in ottica 4.0, integrandone la solidità e la robustezza produttiva con la flessibilità e le potenzialità offerte dal digitale. La capacità di intervenire direttamente sui macchinari ha rappresentato una svolta cruciale per l’azienda, permettendole di impiegare esclusivamente soluzioni, se non totalmente, almeno in parte customizzate secondo le proprie esigenze. Ciò significa che per ogni macchina introdotta, anche se si tratta di un prodotto di mercato, l’azienda si riserva la facoltà di modificarne i parametri di efficienza, in accordo con il costruttore, sfruttando le informazioni ricavate dal proprio storico dei dati, in modo da allinearla alle occorrenze e ai ritmi di lavoro richiesti dalla linea produttiva.
Dal sistema di controllo automatizzato all’attività di revamping, l’applicazione delle tecnologie e gli sforzi in ottica 4.0 attuati da SCM Zanussi sono stati ben focalizzati e mirati al raggiungimento di precisi obiettivi strategici, in grado di offrire all’impresa un notevole vantaggio competitivo, massimizzando i profitti, riducendo costi e tempi.
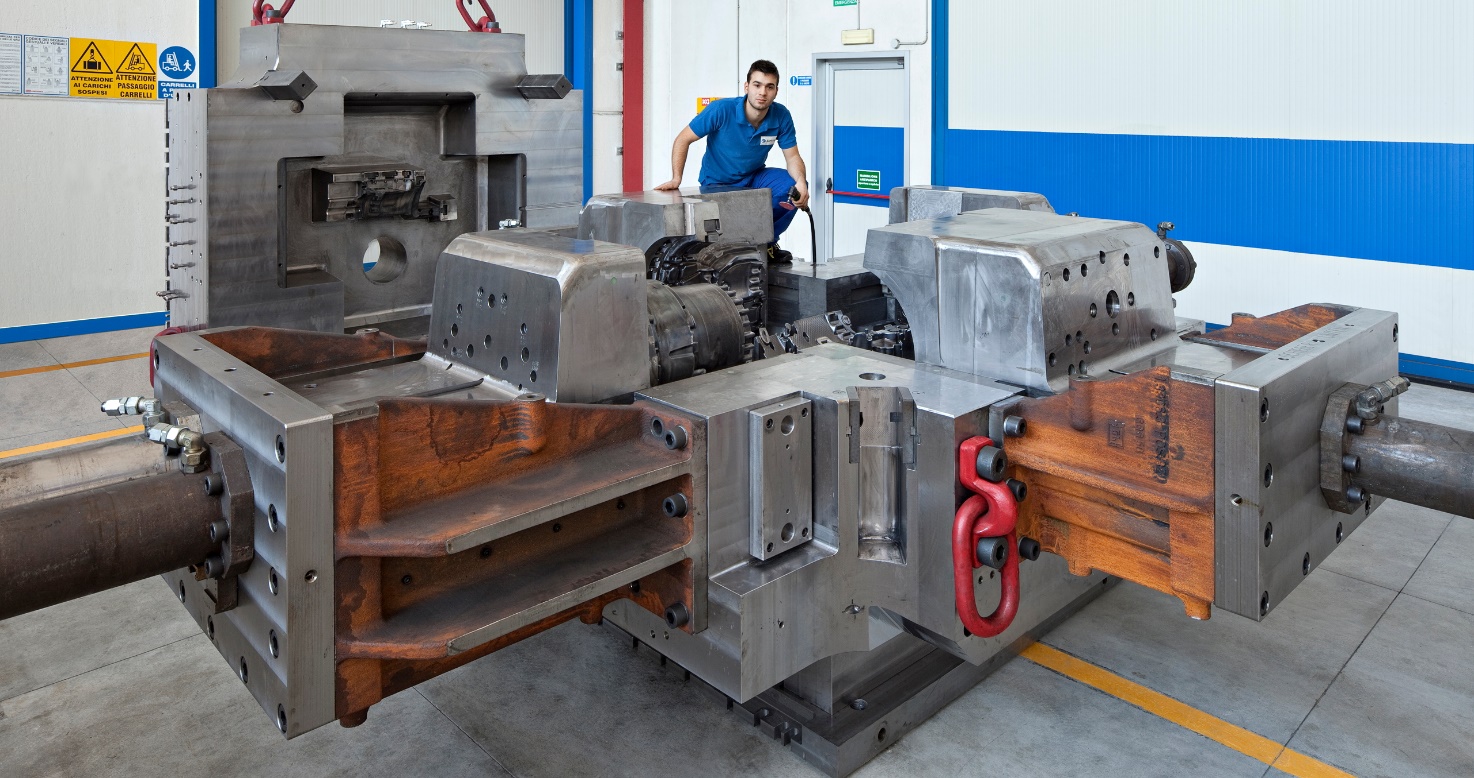
Figura: lo stampo realizzato da SCM Zanussi
Vantaggi e prospettive
La soluzione implementata ha portato innanzitutto una serie di notevoli vantaggi in termini di ottimizzazione dei tempi di produzione. Infatti, se le ore di lavoro presidiate sono rimaste invariate (16h/giorno distribuite su doppio turno), le ore giornaliere non presidiate sono aumentate del 300% (da 2 a 6) così come quelle settimanali, aumentate del 500% (da 6 a 30). In generale, le ore di attività annuali della macchina sono incrementate del 60% (da 4000 a 7200), ma il miglioramento più significativo riguarda l’efficienza del contatto truciolo, interessata da un incremento del 32%.
Nonostante i brillanti risultati già conseguiti, nel futuro di SCM Zanussi si prospettano nuove e imminenti sfide. Prima fra tutte, un ulteriore efficientamento delle capacità predittive del Sentinel, attraverso l’interfaccia diretta con i sistemi CAM. Tale evoluzione si rende necessaria dal momento che, come detto, il lavoro di fresatura riguarda blocchi di grandissime dimensioni e deve rispettare tolleranze molto stringenti, fino a 2 centesimi di millimetro su pezzi di 2 metri o più. Proprio per le sue considerevoli estensioni, la superficie del materiale lavorato è spesso caratterizzata da condizioni di tenacità dell’acciaio più o meno resistenti, a seconda delle zone. Occorre quindi un sistema di monitoraggio che riesca a modulare in corso d’opera, con estrema immediatezza e precisione, la velocità e la profondità della fresatura, agendo direttamente sui parametri di programmazione della macchina senza necessità in interrompere il processo di lavorazione.
SCM Zanussi ha intrapreso il proprio percorso di trasformazione digitale predisponendo attività di R&D focalizzate esclusivamente sugli aspetti premianti delle diverse fasi di lavoro e mantenendo l’attenzione su un approccio integrato di data management. L’excursus sulle diverse soluzioni implementate al suo interno dimostra le enormi potenzialità offerte da un’attività di raccolta e analisi dati sofisticata e mirata, da parte di un’azienda che, partendo da un’esigenza contingente (performare l’attività di controllo sui propri macchinari) ha saputo aprirsi nuovi orizzonti di sviluppo e di successo. Questo caso di digitalizzazione consente di comprendere come l’azienda di Cordenons abbia saputo “cavalcare” il 4.0 per ottenere un significativo vantaggio competitivo.
Si ringrazia Marco Zanussi (managing director di SCM Zanussi) per l’intervista rilasciata, che ha reso possibile la stesura di questo articolo.