Il settore manifatturiero si trova oggi ad affrontare un percorso di profonda trasformazione, spinto da un’ondata di progresso tecnologico guidata principalmente dall’intelligenza artificiale (AI) e dalla robotica, ma anche dalle altre tecnologie abilitanti che già nell’era di Industria 4.0 hanno permesso a tante aziende di efficientare impianti e processi.
La sfida, soprattutto in alcuni settori come la moda e l’arredamento, è soprattutto quella di coniugare ammodernamento e rispetto dei processi artigiani che hanno garantito il successo del made in Italy nel mondo.
Se ne è parlato con le testimonianze di aziende come Hugo Boss e Simonelli, nel corso della tappa di Ancona di SPS Italia on Tour, il percorso di avvicinamento a SPS Italia 2024, in programma a Parma dal 28 al 30 maggio 2024.
Indice degli argomenti
Il “viaggio” dell’intelligenza artificiale nell’innovazione industriale
L’intelligenza artificiale non è una tecnologia nuova. La sua origine risale infatti al 1956, quando un gruppo di studiosi si riunisce al Dartmouth College con lo scopo di esaminare le congetture che ogni aspetto dell’intelligenza possa essere, in linea di principio, descritto in modo tanto preciso da poter far sì che una macchina lo simuli.
Ed è a quel momento che viene fatta risalire la nascita di una nuova disciplina, che il matematico John McCarthy propose di chiamare “intelligenza artificiale”. E due sono i compiti che vengono attribuiti all’AI: comprendere l’intelligenza umana per risolvere i problemi con gli stessi processi usati dall’uomo e risolvere problemi in maniera razionale, ma non necessariamente come farebbe un uomo.
Ed è da questa base che è proseguito il percorso di evoluzione della tecnologia, che ha portato poi alla sua progressiva adozione anche in ambito industriale, fino a rendere l’AI (e, soprattutto, l’AI generativa) uno dei temi più rilevanti di questo periodo, con il potenziale di rivoluzionare diversi aspetti della gestione dei processi, sia a livello di fabbrica che dipartimentale.
Un ruolo da protagonista a cui l’AI è giunta grazie alla sua eccezionale capacità computazionale e alla qualità dei dati che può gestire. Queste caratteristiche hanno aperto la strada a innovazioni come l’uso di reti neurali per generare rappresentazioni tridimensionali o migliorare i sistemi di controllo qualità attraverso tecniche di data augmentation, permettendo di identificare difetti precedentemente insospettabili.
L’interesse per l’AI generativa deriva anche dalla sua capacità di generare creatività e nuovi contenuti, trovando applicazioni in settori vari come la moda e la progettazione industriale. Inoltre, l’approccio delle Large Language Models (LLM) alla gestione della conoscenza sta dimostrando il suo valore, sottolineando l’importanza della proprietà intellettuale e offrendo nuovi strumenti di supporto per i team aziendali.
Nonostante ci sia, nel discorso comune, forte preoccupazione su come e quando queste tecnologie porteranno alla sostituzione dell’uomo, è proprio la conoscenza e la consapevolezza su cosa sono e cosa possono fare l’unica arma di difesa contro un approccio normativo che ingabbi l’innovazione.
“Assistiamo già a tanti casi in cui la ricerca viene bloccata e credo che abbiamo così tanto da fare con queste tecnologie che non possiamo permetterci questo approccio. Bisogna chiedersi cosa facciamo con questi strumenti, capire perché sono di interesse, visto che dietro vi è una cultura legata alla generazione di creatività alla creazione di contenuti”, ha commentato Emanuele Frontoni, Professore Ordinario di Informatica Università di Macerata e Co-director VRAI Vision Robotics & Artificial Intelligence Lab.
Ed è proprio in virtù di queste grandi potenzialità che l’AI generativa sta raccogliendo sempre più interesse anche tra le aziende manifatturiere.
Queste evoluzioni evidenziano come questi strumenti stiano progressivamente diventando un elemento cruciale nell’innovazione e nello sviluppo industriale, nonostante le sfide che ancora si pongono nella sua comprensione e integrazione.
Le tecnologie digitali e l’AI a servizio delle realtà manifatturiere: la parola agli utilizzatori di tecnologie
Queste sfide non riguardano unicamente l’intelligenza artificiale ma, ancora oggi, l’utilizzo delle tecnologie 4.0 (a partire dalla raccolta e l’analisi dei dati) per mettere a terra quei paradigmi (tecnologici e non) necessari per cavalcare le trasformazioni che stanno interessando le aziende industriali.
Per comprendere meglio come queste tecnologie abilitino vantaggi competitivi irrinunciabili, la prima tappa di SPS Italia On Tour ha come di consueto lasciato ampio spazio a esempi virtuosi di percorsi di digital transformation e di collaborazioni di ecosistema.
La tecnologia a servizio dell’artigiani del Made in Italy: il percorso verso digitalizzazione e sostenibilità di Hugo Boss
Il percorso di digital transformation portato avanti da Hugo Boss rappresenta un esemplare caso di integrazione tra tecnologia avanzata e sostenibilità nel settore manifatturiero della moda.
L’azienda ha, già da diversi anni, implementato un sistema di automazione all’avanguardia nel suo stabilimento di Morrovalle, introducendo software per la gestione dell’illuminazione e del controllo degli impianti di areazione. Queste innovazioni non solo hanno migliorato la manutenzione degli impianti, ma hanno anche portato significativi benefici economici. Inoltre, Hugo Boss ha posto un accento particolare sull’uso dell’illuminazione naturale per garantire che i colori dei prodotti corrispondano a quelli percepiti dai clienti finali.
La sostenibilità è stata un pilastro fondamentale per Hugo Boss, che già nel 2012 ha preso misure significative per migliorare la salubrità dei prodotti e la sostenibilità ambientale, coinvolgendo tutti i fornitori in un impegno condiviso verso la riduzione dell’uso di sostanze chimiche dannose. Tra le altre iniziative, nel 2019, l’azienda ha sostituito le colle tradizionali con composti organici a base d’acqua, avviando un percorso verso l’ottenimento di certificazioni ambientali e di sicurezza, culminato con la certificazione sull’energia nel 2021.
Il Progetto RAMS, avviato nel 2017 e concluso nel 2019, ha visto l’implementazione dell’automazione in particolare nelle aree di cardatura e incollaggio del fondo delle scarpe. Gli obiettivi erano ambiziosi: eliminare le attività a basso valore aggiunto, come il carico/scarico delle scarpe e l’applicazione della colla, affidate a robot per ridurre i movimenti ripetitivi e il lavoro usurante, arricchendo così il ruolo dei lavoratori.
Hugo Boss ha investito nella formazione del personale, coinvolgendolo attivamente nel progetto e informandolo sui miglioramenti previsti. Un’innovazione significativa è stata l’adattamento del sistema per utilizzare il parco forme esistente senza sprechi.
I risultati del progetto includono la riqualificazione dei lavoratori impegnati nelle operazioni automatizzate, l’eliminazione dei movimenti ripetitivi e un miglioramento degli standard di qualità.
“A tutte le aziende dico che dovremmo essere più propensi ad accogliere questo connubio tra tecnologia e artigianalità perché è questa conversione all’essere ibridi che sarà la sfida per i prossimi anni. Per restare competitivi dobbiamo essere bravi a cogliere e utilizzare la tecnologia mantenendo questi prodotti artigianali. Non bisogna aver paura”, ha spiegato Paolo Cecchi, Project Manager Innovation & Technology di Hugo Boss.
Sigma, il focus sulla manutenzione predittiva
Rosario Capparuccia, manager del reparto Ricerca e Sviluppo di Sigma, azienda che produce macchinari per automazione bancaria e bigliettazione, ha sottolineato l’importanza cruciale della manutenzione e della disponibilità degli apparati per la propria azienda. Per affrontare questa sfida, Sigma ha avviato un innovativo progetto di manutenzione predittiva, sfruttando l’enorme mole di dati generati dagli apparati connessi ai suoi data-center.
L’obiettivo era quello di anticipare eventuali guasti, ottimizzando così le operazioni di manutenzione e riducendo i costi. La peculiarità di questo progetto sta nella sua natura collaborativa, che ha coinvolto diverse aziende (tra cui anche Nuova Simonelli di cui diremo nel prossimo paragrafo) e l’Università delle Marche, ricevendo anche il sostegno finanziario del Ministero dello Sviluppo Economico.
La strategia adottata ha previsto l’analisi dei dati disponibili e l’adattamento delle macchine per prevedere i guasti prima che questi si verifichino. Il risultato è stata la creazione di una piattaforma versatile, capace di supportare diversi casi d’uso e aperta all’integrazione di modelli personalizzati da parte delle aziende, in un ambiente multi-tenant.
Completato a maggio, il progetto è ora nella fase di installazione pilota, con la raccolta di dati reali dagli apparati coinvolti. L’approccio adottato da Sigma e dai suoi partner conferma la validità dell’investimento iniziale, grazie all’efficiente utilizzo di una grande quantità di dati precedentemente inesplorati, aprendo nuove prospettive per il settore della manutenzione industriale.
Le tecnologie digitali tra vantaggi e implicazioni etiche e normative: l’approccio di Simonelli Group
Il progetto di Simonelli Group rappresenta un eccellente esempio di come l’innovazione sostenibile possa essere integrata nel settore della produzione di macchine per il caffè.
Attraverso l’adozione di principi di eco-design, il progetto mira a prolungare la vita dei prodotti e a ridurre gli sprechi di materiali, enfatizzando l’importanza della manutenzione predittiva.
La chiave di questo approccio innovativo è l’implementazione di sensori avanzati, come microfoni e accelerometri, e lo sviluppo di algoritmi sofisticati capaci di rilevare segnali predittori di malfunzionamenti imminenti. Questo permette di identificare precocemente potenziali problemi, come perdite o anomalie sonore, che potrebbero indicare la necessità di interventi di manutenzione.
Tuttavia, l’introduzione di queste tecnologie solleva questioni importanti relative a normative e privacy, specialmente quando si considera l’uso di microfoni in ambienti pubblici come i bar. Il team di Simonelli Group ha affrontato queste sfide conducendo analisi approfondite per correlare i dati relativi ai difetti, scoprendo correlazioni inaspettate che non sarebbero state intuitive per l’occhio umano.
Un aspetto particolarmente innovativo del progetto è l’automazione della regolazione del macinino, un compito tradizionalmente complesso e soggetto a errori umani. Attraverso l’analisi dei dati, il sistema è in grado di auto-regolarsi, sia tramite un sistema embedded nella macchina stessa sia attraverso algoritmi esterni, riducendo così il margine di errore.
Bentivogli: “Recuperare il ritardo accumulato dalle PMI”
A concludere la giornata è stato l’intervento di Marco Bentivogli, Coordinatore Nazionale Base Italia ed esperto di politiche di innovazione, che ha posto l’accento sulla necessità di comprendere le tecnologie e di recuperare il ritardo sui percorsi di digital transformation per evitare che le aziende italiane restino ancora più indietro in questa fase di accelerazione tecnologica.
“Il rischio è che ci si attendono delle risposte che non arriveranno mai da alcune tecnologie e che ci sia totale sconforto sulla loro inutilità perché troppo spesso si ha un’idea di robotica e AI nelle versioni precedenti”, ha spiegato.
Bentivogli sottolinea come l’era dell’Industria 4.0 abbia suscitato grande interesse verso l’innovazione tecnologica, ma avverte che l’Industria 5.0 non rappresenta un paradigma completamente nuovo, bensì un’evoluzione che punta a rendere le tecnologie abilitanti non solo integrate tra loro ma anche sostenibili, umano-centriche e resilienti.
“Purtroppo questa accelerazione considera da un lato una verticalizzazione nuova delle produzioni ma molti non sono ancora passati per la fase della digitalizzazione. Una prima fase fondamentale sarebbe quella di insegnare bene alle imprese a raccogliere e usare i dati che già producono. In questa fase di gigantesca accelerazione abbiamo un tessuto industriale dove il 90% ha meno di 10 dipendenti per cui se l’accelerazione non ha possibilità di abbassare soglia di accesso priveremo gran parte del tessuto imprenditoriale italiano di accedere a queste opportunità”, ha proseguito.
Per superare questo ostacolo, Bentivogli propone un modello di trasferimento tecnologico e di competenze ispirato al sistema tedesco, dove la ricerca di base è affidata alle università e agli istituti, mentre la ricerca applicata è gestita da entità come l’Istituto Fraunhofer.
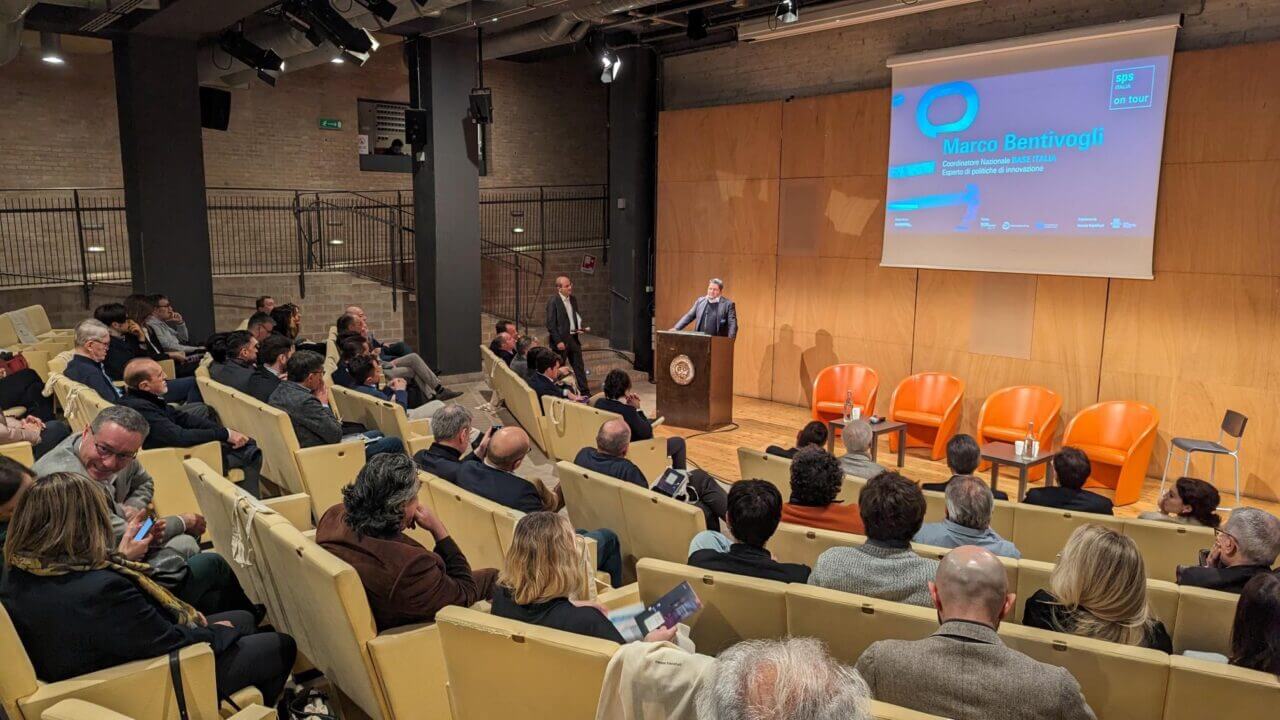
Per quanto riguarda l’AI generativa, Bentivogli ritiene essenziale riportare l’attenzione su u tema che ancora ostacola l’adozione di strumenti di AI nelle imprese, ovvero la mancanza di un’infrastruttura che permetta alle imprese, specialmente quelle di piccole e medie dimensioni, di implementare soluzioni AI efficaci. L’investimento in quest’area è cruciale per mantenere le imprese italiane competitive sul mercato globale.
L’atteggiamento verso tecnologie di automazione, compresa l’AI, non deve essere quello di paura suscitato da tanti scenari allarmistici. Tuttavia – ha spiegato il Coordinatore Nazionale Base Italia – è importante capire e prepararsi agli effetti che queste tecnologie avranno sul mercato del lavoro: la riduzione dei compiti ripetitivi; la valorizzazione dei lavoratori specializzati, che vedranno una maggiore occupabilità; e l’effetto combinato di sostituzione di alcune professioni, generazione di nuove professioni e integrazione/supporto tramite l’AI.
“Dobbiamo creare un ecosistema che permetta una partecipazione inclusiva all’innovazione tecnologica e di non lasciare indietro nessuno nel processo di trasformazione digitale”, ha concluso.
SPS Italia On Tour, le prossime tappe
Dopo la tappa di Ancona, il percorso di SPS On Tour proseguirà nel resto d’Italia per portare questi ed altri temi al centro del dibattito e promuovere la conoscenza di come sia oggi possibile attuare questi percorsi di trasformazione che diventeranno sempre più determinanti alla competitività aziendale.
I prossimi appuntamenti saranno a Padova (27 marzo, Competence Center Smact) e Torino (17 aprile, Competence Center CIM4.0). Ci sarà infine anche un appuntamento digitale, il prossimo 20 marzo, in occasione dell’Industry 4.0 360 Summit.