Per chi lavora nel mondo dell’automotive e per gli appassionati di auto sportive e da corsa il nome Dallara è un punto di riferimento. “Facciamo tutte le auto che gareggiano in Formula 2, Formula 3, Super Formula, Formula e nei circuiti Indicar, Nascar e nell’Endurance”, ricorda l’amministratore delegato dell’azienda Andrea Pontremoli. “Forniamo anche consulenza a clienti privati per aiutarli a costruire propri modelli da corsa o supercar”.
Tra questi clienti privati troviamo nomi come Alfa Romeo, Audi, Ferrari, Lamborghini, Maserati o Porsche. Ed è grazie alla collaborazione con Dallara che Bugatti ha costruito la Chiron, l’auto da strada oggi più veloce al mondo: sfiora i 500 km/h.
Senza dimenticare che anche alcune monoposto di Formula 1 sono state realizzate a Varano de’ Melegari, in provincia di Parma, presso la sede Dallara. Pontremoli sottolinea, però, “tra gli elementi che contribuiscono alle prestazioni di un’auto, il motore incide per il 15%, il peso per il 35% e l’aerodinamica per il 50%. Noi non facciamo motori, ma ci occupiamo del restante 85%”.
Indice degli argomenti
Simulare prima di costruire
Il DNA di Dallara è sinonimo di innovazione. E lo è ancor di più oggi che la tecnologia digitale le permette di progettare auto sempre più sofisticate in tempi particolarmente rapidi.
“La realizzazione di un’auto di Formula 1 richiede circa nove mesi di lavoro, otto per la progettazione e le simulazioni e uno per la costruzione”, aggiunge Pontremoli. In questo periodo di tempo, grazie alla Computational Fluid Dynamic, Dallara realizza 40.000 modelli differenti di tale auto. Per verificarne il comportamento in situazioni reali (quantomeno di alcuni di detti modelli) sono prodotte auto identiche a quelle reali, ma in un formato ridotto del 50%. Si può dire che siano degli enormi puzzle tridimensionali perché sono costituiti da decine di migliaia di pezzi realizzati al computer e prodotti con stampanti 3D, ognuno dei quali può essere modificato.
Quando finalmente le simulazioni hanno dato i risultati desiderati, il modello in scala ridotta viene testato “in condizioni reali” nella galleria del vento, dove si ottiene una verifica quantitativa della risposta alle forze a cui sarà sottoposta l’auto. In questa fase ogni singolo pezzo del puzzle può essere ancora modificato sei risultati non sono soddisfacenti.
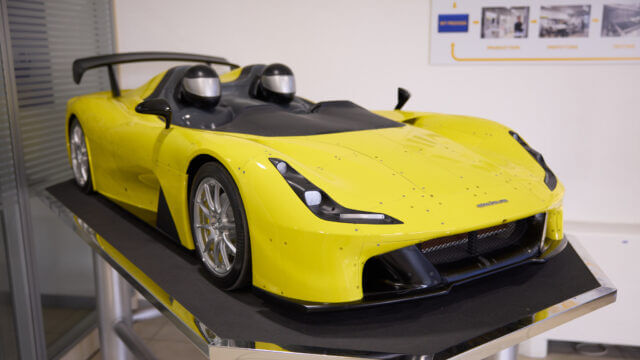
Un fattore strategico: i dati
Ma cosa rende tanto ambita la collaborazione di Dallara nella progettazione di un’auto potente e di prestigio? La risposta è semplice: i dati. “Abbiamo un’enorme mole di dati – sostiene Pontremoli – nessun’altra azienda nel nostro mercato dispone di così tante informazioni. Ogni weekend circa 300 nostre macchine corrono in circuiti o percorsi in tutto il mondo. I dati che ricaviamo da tali macchine ci permettono di validare i digital twin, i modelli matematici, con una precisione unica”.
Per elaborare tali dati e ottenere le simulazioni, Dallara usa un’infrastruttura IT costituita da un insieme di computer ad altissime prestazioni prodotti da Lenovo. Tale infrastruttura è stata implementata nel 2019, quella in uso attualmente è l’aggiornamento effettuato lo scorso anno e che “ha permesso di avere un incremento di prestazioni del 600%”, come afferma Fabrizio Arbucci, Responsabile Innovazione Digitale e ICT dell’azienda. Oggi il sistema di HPC (high performance computing) usato da Dallara comprende 142 nodi Lenovo ThinkSystem SR630 V2 e otto nodi Lenovo ThinkSystem SR650 V2. Questa infrastruttura rende disponibile a Dallara una capacità di calcolo di 720 teraflops, ovvero può eseguire 720mila miliardi di operazioni al secondo, che è usata per la quasi totalità nelle simulazioni che sono eseguite H24, 7 giorni su 7.
Per non incontrare colli di bottiglia e vedere ridotte le sue potenzialità, tale infrastruttura ha bisogno di una connettività adeguata. Per questo, il sistema di calcolo è collegato con sottosistemi storage ad alte prestazioni attraverso una rete di gestione da 1 Gbps, una rete interna Ethernet da 25 Gbps e una rete InfiniBand ad alta velocità e bassa latenza da 100 Gbps.
Per migliorare ulteriormente l’efficacia dell’infrastruttura, Lenovo sta lavorando sull’impiego di algoritmi di intelligenza artificiale per massimizzare l’utilizzo dei sistemi. “L’obiettivo è evitare che ci siano tempi morti – afferma Alessandro de Bartolo, Country General Manager, Italy, Infrastructure Solutions Group, Lenovo –. In tal senso, viene verificato che la sequenza dei task scelta dell’operatore sia la più funzionale. Se così non è, viene modificata la programmazione delle attività”.
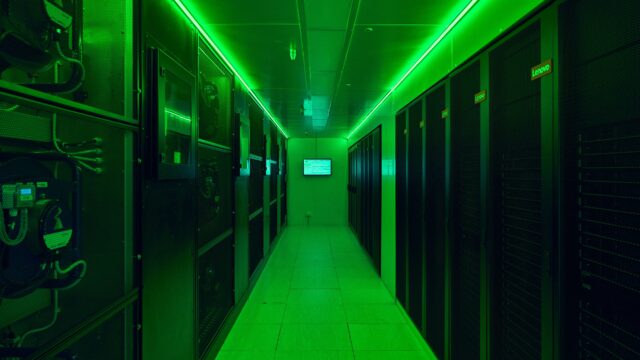
Da egosistema a ecosistema
Alla base dell’innovazione di Dallara c’è sicuramente la possibilità di effettuare decine di migliaia di simulazioni con una mole di dati unica. Ma ancor prima c’è il fattore umano, le competenze e l’ingegno.
“Spesso – sostiene Pontremoli – ci chiedono: le soluzioni tecnologiche che usate sulle vostre supercar quando saranno disponibili anche sulle auto che si guidano tutti i giorni? Noi usiamo prodotti già disponibili e che può utilizzare chiunque. È il modo in cui li usiamo che è differente”.
Pontremoli evidenzia che un ruolo essenziale nella realizzazione di un’auto lo rivestono i fornitori, i quali però devono poter lavorare come sanno e non devono essere forzati: “Ci troviamo nella Motor Valley e ci sono otto brand molto conosciuti che aggregano 16.500 aziende di varie dimensioni. Ciascuna di queste, nel suo campo, è al primo o al secondo posto a livello globale e si confronta quotidianamente col mondo. La chiave è scegliere fornitori che non lavorino unicamente per un’azienda, ma che competano con i concorrenti. Poi bisogna passare da un egosistema a un ecosistema. Nell’egosistema un’unica azienda dice alle altre cosa devono fare, nell’ecosistema, invece, si mettono insieme le migliori competenze per far funzionare il sistema nella sua globalità. Purtroppo, troppo spesso, prevale l’egosistema”.
Il ruolo centrale della formazione
Un aspetto su cui punta molto Dallara, soprattutto in ottica ecosistema, è la formazione. In tal senso, l’azienda ha avviato una serie di progetti per avvicinare lo studio teorico degli istituti tecnici o delle università alla realtà lavorativa e tecnologica.
“Cerchiamo di formare ingegneri che lavorino sulla parte applicata”. E questo avviene tramite la Muner – la Motorvehicle University of Emilia-Romagna – iniziativa che, oltre a Dallara, coinvolge 9 altre aziende: Ducati, Ferrari, Haas, HPE Coxa, Lamborghini, Magneti Marelli, Maserati, Pagani e Toro Rosso.
“Mettere allo stesso tavolo dei concorrenti non è stato facile – dichiara Pontremoli – però hanno capito che possono competere nel mondo cooperando nella produzione delle competenze. Così abbiamo disegnato otto corsi di laurea in ingegneria che non esistevano e li abbiamo proposti alle quattro università dell’Emilia Romagna cercando di convincerle a istituire una laurea interuniversitaria che valesse per tutte e quattro le università”.
L’iniziativa ha avuto successo e così è stato realizzato un campus grande come tutta la regione: in parte si studia a Bologna, in parte presso Dallara e in parte in Ferrari, a Maranello. L’obiettivo è abituare gli studenti alla diversità, a vedere aziende diverse, università diverse, metodi di insegnamento diversi. I corsi sono esclusivamente in inglese e c’è una clausola: il 20% degli studenti deve essere extraeuropeo. La laurea interuniversitaria, che è di tipo magistrale, è partita quattro anni fa e quest’anno raggiungerà i 200 laureati. Oggi il rapporto tra richieste e studenti accettati nei corsi è 4 a 1.
“Abbiamo organizzato anche quattro master post-universitari – aggiunge Pontremoli –. Tre sono tenuti in Dallara: uno sulla simulazione, uno sull’aerodinamica e uno sulla fibra di carbonio. Il quarto è invece a Maranello e ha come tema i motori Formula 1. Abbiamo poi fatto una serie di master con la Bologna Business School per formare i manager”.
Gli studenti devono poter lavorare sulla tecnologia più moderna
La Muner ha avviato una nuova iniziativa no profit inerente alla formazione di base: si chiama Innovation Farm e prevede la costruzione di laboratori per i ragazzi degli istituti tecnici. Ne sono già stati creati 5 a Fornovo. “Questi laboratori riguardano il processo di lavorazione della fibra di carbonio, dal taglio laser fino alle autoclavi. Inoltre, ci sono il CAD, la robotica e le macchine a controllo numerico e 26 simulatori. Sinora abbiamo speso sei milioni di euro, tutti finanziati dalle aziende nostre partner”.
L’Innovation farm deve mettere a disposizione della scuola i laboratori, facendo la manutenzione e assicurando che siano attrezzati con la tecnologia più recente (se è il caso aggiornandola ogni anno). “I ragazzi devono poter lavorare sull’ultima tecnologia, che è quella che troveranno in azienda una volta usciti dalla scuola. Prima usavano torni dismessi vent’anni prima. Come si poteva pretendere che fossero innovativi e lavorassero volentieri?”, commenta Pontremoli.
Dell’informatizzazione dei laboratori e dell’allestimento di un’infrastruttura per la didattica a distanza (DAD) si è occupata Lenovo.
Inoltre, siccome la scuola usa i laboratori dell’Innovation Farm solo per il 20% del tempo disponibile, il restante 80% è stato suddiviso equamente tra le aziende associate, che mandano i loro dipendenti per degli aggiornamenti, e corsi di reskilling per disoccupati del territorio: per accedere basta avere un diploma di scuola superiore. “Le prime 10 persone che hanno seguito questi corsi hanno trovato subito lavoro – conclude Pontremoli –. Il nostro obiettivo è alzare il livello dei nostri fornitori operando nella logica di ecosistema. E tutte le iniziative dirette alla formative vanno proprio in tale direzione”.