“Accelerare la digitalizzazione per un domani sostenibile”: è questo il filone tematico alla base dell’offerta che Siemens porta in mostra alla 33° BiMu, la biennale internazionale della macchina utensile che si svolge a Fiera Milano Rho fino al 15 ottobre 2022.
L’azienda porta in fiera, presso il suo stand al padiglione 13 (D19), soluzioni hardware e software integrate che combinano mondo reale e mondo virtuale per permettere ai costruttori di macchine utensili e agli utenti finali di accelerare il loro percorso di trasformazione digitale.
Soluzioni che rispondono alle esigenze dei costruttori di macchine e utilizzatori di modificare velocemente e flessibilmente macchine e manufatti, per difendere quote di mercato, per orientarsi su nuovi business o per rispondere a trend tecnologici e richieste mutevoli.
“La digitalizzazione e l’automazione integrata Siemens offrono risposte concrete a queste esigenze. Attraverso l’utilizzo intelligente dei dati e la loro rielaborazione, la simulazione di macchine e processi di lavorazione, e l’uso dell’AI, è possibile fornire soluzioni innovative per nuove tecnologie come l’Additive Manufacturing, adottando soluzioni modulari per mitigare efficacemente i rischi correlati alla cybersecurity”, spiega Filippo Giannini, Head of Machine Tool Systems di Siemens Italia.
Indice degli argomenti
I vantaggi dell’utilizzo sinergico di tecnologia additiva e di asportazione
In più, quest’anno BI-MU costituisce un’opportunità unica per mostrare uno dei molteplici risultati ottenuti grazie alla sinergia tra il portfolio completo e integrato Siemens e le elevate competenze del Digital Enterprise Experience Center (DEX) di Piacenza.
I processi produttivi saranno rivoluzionati dalla Realtà Aumentata? Scoprilo in questo White Paper
Infatti, presso lo stand di Siemens viene illustrato come, tramite l’utilizzo sinergico di tecnologia additiva e di asportazione, è possibile effettuare il processo di riparazione di una girante destinata a un impianto di produzione dell’energia, al posto di produrne una “ex novo” riducendo in questo modo al minimo, o eliminando del tutto la necessità di ricambi.
Tutto ciò permette di ridurre di oltre il 20% l’energia e di oltre il 40% il tempo necessari per realizzare una girante pienamente utilizzabile. Inoltre, Sinumerik One e i gemelli digitali assicurano un risparmio dei tempi di preparazione dei pezzi e di lavorazione e, più in generale, permettono una riduzione degli scarti, una maggiore efficienza dell’officina e, di conseguenza, una maggiore produttività e sostenibilità.
La girante è stata prodotta presso il Siemens Digital Enterprise Experience Center (DEX) di Piacenza sfruttando sia le grandi potenzialità di un centro di lavoro equipaggiato con Sinumerik One, e relativi gemelli digitali, sia i vantaggi dell’utilizzo di una catena CAD-CAM-CNC NX – Sinumerik pienamente integrata.
La nuova cella robotizzata multiprocesso di Prima Additive
Il processo di riparazione tramite tecnologia additiva Direct Energy Deposition (DED) è stato realizzato grazie alla cella robotizzata multiprocesso Ianus, presentata in anteprima mondiale da Prima Additive (società del gruppo Prima Industrie dedicata alle tecnologie per l’Additive Manufacturing), presso il suo stand a 33° BiMu.
Ianus è costituita da un braccio robotico Autonox e da una sorgente laser, inseriti all’interno di una cella con un volume di lavoro pari a 1600 x 1200 x 700 mm, e gestiti direttamente da un controllo numerico Sinumerik One, e dal relativo portfolio di digitalizzazione di Siemens.
Anche se questa speciale cella può essere configurata su diversi processi laser, quella esposta alla biennale è equipaggiata solo con la Direct Energy Deposition (DED) basata sull’utilizzo di polvere metallica per la costruzione di componenti da zero, per la riparazione, per il rivestimento e per l’aggiunta di parti custom su pezzi in metallo.
Grazie alla flessibilità di Ianus, è possibile eseguire processi DED basati anche sull’utilizzo di filo di metallo come materiale di partenza o, uscendo dall’ambito dell’Additive Manufacturing, optare per la saldatura laser (di prossimità o remota) e la tempra laser.
Grazie all’ integrazione tra il braccio robotico di Prima Additive e il CNC “nativo digitale” di Siemens, poi, si esprime maggiormente il potenziale di Ianus. Attraverso la funzionalità Sinumerik Run MyRobot / Direct Control l’utilizzatore può eseguire la movimentazione e la programmazione del robot utilizzando istruzioni tipiche di una macchina utensile. L’impiego integrato di CAM e CNC, reso possibile dall’utilizzo della piattaforma NX e del controllo numerico Sinumerik One, viene completato dall’integrazione di soluzioni digitali e di gestione e rielaborazione dati.
La soluzione, che si basa sull’ecosistema aperto MindSphere, prevede l’uso di App Siemens, tra cui: Manage MyMachine, che consente di visualizzare, gestire e ottimizzare la produzione; e Manage MyMachine /Remote, che permette di gestire sistemi di monitoraggio e controllo da remoto (teleservice).
A completamento di tale offerta digitale vi sono alcune applicazioni specifiche, in grado di gestire dati ad alta frequenza, basate sulla piattaforma Industrial Edge for Machine Tools di Siemens.
Non ultimo, l’uso di Create MyVirtual Machine ha permesso di sfruttare al massimo le potenzialità di Sinumerik One: il software, che genera il gemello digitale del sistema, ha agevolato il lavoro di engineering nelle varie fasi di sviluppo e ottimizzazione della macchina, permettendo inoltre una notevole riduzione del time to market.
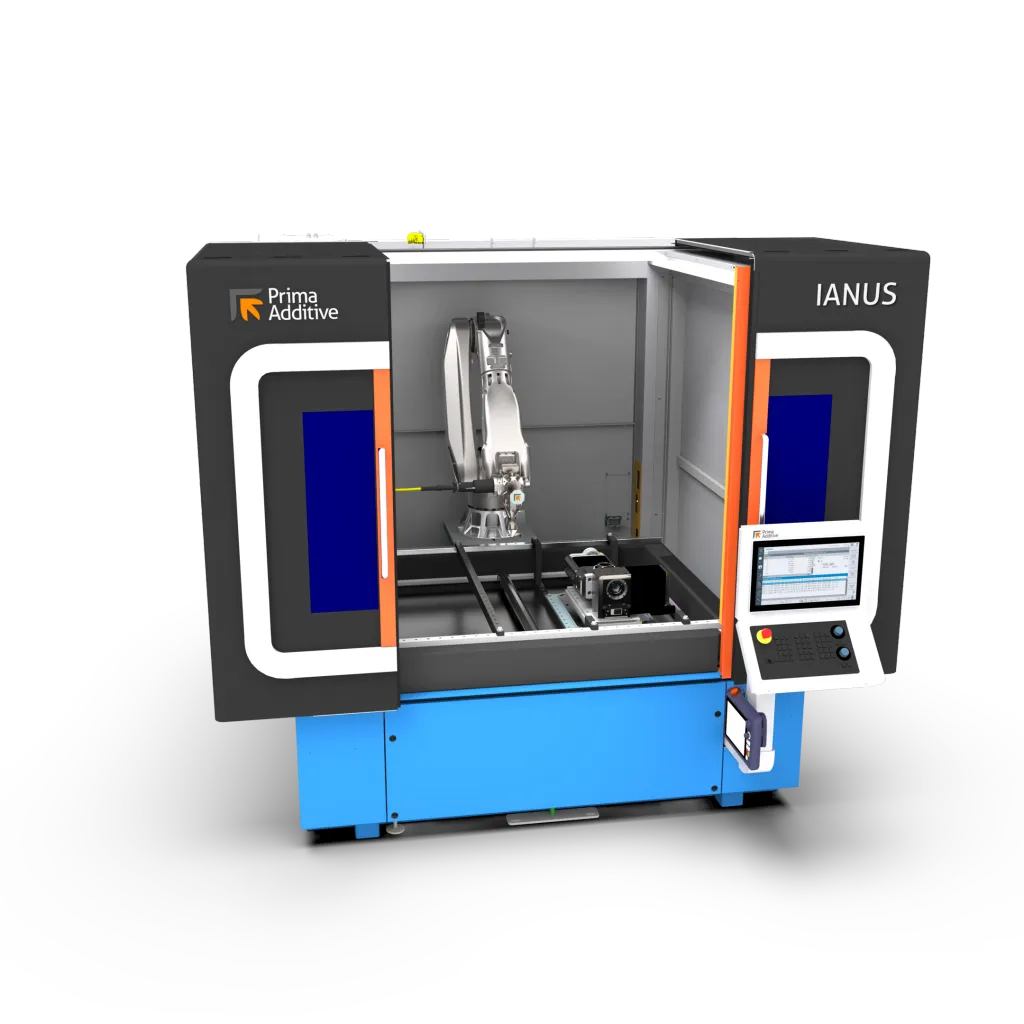
Nuove funzioni tecnologiche per Sinumerik One
Un’offerta, quella del CNC “nativo digitale” di Siemens, che l’azienda ha deciso di ampliare grazie alla versione Sinumerik V6.20, con nuove funzioni tecnologiche che semplificano il funzionamento, contribuiscono a ridurre l’usura della macchina e aumentano la produttività.
Con la nuova funzione di tornitura “Y Turning”, Sinumerik One risponde alle richieste di mercato per le macchine che utilizzano l’asse Y in tornitura. A questo scopo, sono stati creati nuovi tipi di utensili, nei quali viene esercitata una pressione verticale e non laterale, con un avanzamento fino a 3 volte superiore e, di conseguenza, un aumento della produttività.
La funzione “Advanced Rapid Movement” è un’altra delle novità per quanto riguarda le funzioni tecnologiche. Consente di ottimizzare i tempi di movimento in caso di frequenti riposizionamenti (es. percorsi di foratura ripetuti), il che significa che tra una lavorazione e l’altra si effettuano movimenti più rapidi. Non è necessario modificare il programma del pezzo e la lavorazione generale ne risulta fino al 10% più veloce.
Con la funzione “Reduced Dynamic Mode”, è possibile ridurre l’usura della macchina e degli utensili, ottimizzando le risorse e aumentando così disponibilità e produttività. Attraverso il programma PLC è possibile monitorare e reagire a influenze esterne, quali arresto notturno, mancanza di alimentazione improvvisa e comandi manuali da operatore macchina.
La funzione “NCK”, infine, consente alla macchina di passare automaticamente al funzionamento ridotto in presenza di fattori esterni, riportando alla condizione di lavorazione ottimale, in mancanza del fattore scatenante.
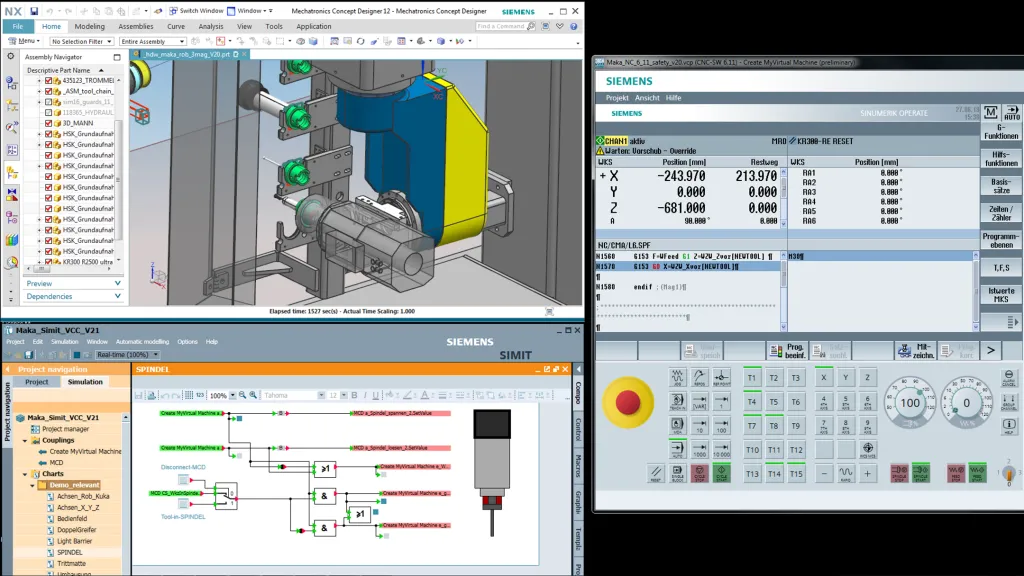
Anche in ambito hardware sono state introdotte alcune novità, progettate per semplificare ulteriormente l’utilizzo di Sinumerik One. Sono disponibili nuove tastiere (MCP – Machine Control Panel) e pannelli (ITC – Industrial Thin Client e IFP – Interactive Flat Panel) per il controllo macchina da 15 a 24 pollici, con risoluzione fino a 1920 x 1080 pixel.
Le nuove MCP sono integrate anche nel gemello digitale di Sinumerik One (Create e Run MyVirtual Machine), in modo che l’aspetto e il funzionamento corrispondano in tutto e per tutto al CNC reale.
Inoltre, il gemello digitale di Sinumerik One è stato dotato di nuove funzioni che semplificano la progettazione e la preparazione del lavoro, tra cui l’opzione 3D, che offre il supporto per un secondo canale. In più, a ogni utensile può essere assegnato un colore individuale, in modo che le superfici lavorate siano evidenziate a seconda dell’utensile utilizzato.
Il rilevamento delle collisioni offre ora anche funzionalità estese, come la visualizzazione di tutti i corpi in collisione, la linea del programma NC e molto altro ancora, in modo da poter indagare ed eliminare rapidamente la causa scatenante.
Quanto è sicura la tua linea di produzione? Scopri se è a prova di attacco cyber