di Ajei Gopal, Presidente e CEO, ANSYS
Per oltre 40 anni la simulazione ha supportato i team di sviluppo in tutto il mondo nel mettere a punto innovazioni, accelerare i lanci di prodotto e ridurre i costi associati a design e progettazione. Nonostante il processo di creazione di prodotti altamente ingegnerizzati non sia mai stato così facile, i team di product development odierni devono affrontare sfide che, 40 anni fa, erano addirittura inimmaginabili. I prodotti sono sempre più complessi, dotati di funzionalità intelligenti e di software integrato.
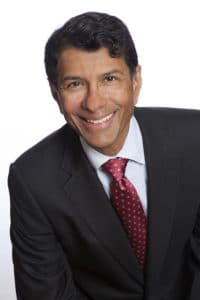
Prodotti innovativi operano in ambienti mai esplorati prima d’ora. E da essi ci si aspetta che siano efficienti in condizioni ambientali ancora più critiche. I consumatori chiedono e si aspettano sviluppi più importanti e con maggiore frequenza, che siano però anche economicamente abbordabili. E, in alcuni casi, i clienti non chiedono, ad esempio, un prodotto come può essere una turbina, ma un risultato in termini di kilowatt/ora.
La buona notizia è che gli avanzamenti nella tecnologia di simulazione sono in grado di soddisfare queste domande.
Il software si è ampliato e arricchito, abilitando la modellazione di molteplici forze fisiche — elettromagnetica, strutturale e fluidi — e inserito software e sistemi con una piattaforma di simulazione integrata. I semiconduttori possono essere progettati sfruttando i modelli chip–package–system di modo che i problemi vengano individuati molto prima di prototipazione e sign-off. I miglioramenti nelle capacità di elaborazione e l’avvento del cloud hanno condotto all’emergere di funzionalità high performance computing (HPC) che semplificano e accelerano anche le simulazioni più impegnative e permettono a diversi team di ingegneri di collaborare.
I prototipi digitali e l’esplorazione digitale sono più facili e semplici da implementare che mai. Ma non è tutto qui. L’Internet of Things (IoT) porta con sé tecnologia e modelli di costo pratici per l’installazione di sensori in una vasta gamma di prodotti e l’invio di grandi quantità di dati in real-time. L’avvento delle piattaforme software IoT abilita l’integrazione di dati operativi in tempo reale con tutte le informazioni digitali che un’azienda ha su un determinato prodotto, assicurando la realizzazione di un digital twin.
La simulazione è l’unico strumento che permette di trarre vantaggio dalle potenzialità offerte dal gemello digitale. I dati di field product performance possono essere integrati con quelli relativi a prestazioni future di quel prodotto all’interno dell’ambiente in cui opera. Questa capacità predittiva potrebbe, per esempio, ottimizzare gli schedule di manutenzione e ridurre i downtime non pianificati, così come incrementare in modo significativo le prestazioni operative.
Ma i digital twin offrono un vantaggio strategico ancora più importante: i team di product development possono applicare le informazioni dei twin direttamente all’interno del processo di sviluppo. Le versioni future di prodotti o processi possono essere progettate con nuove funzionalità, forme e materiali che indirizzano direttamente le problematiche identificate tramite il processo del digital twin, accelerando drasticamente l’innovazione.
Già utilizzati dalle realtà più grandi, i digital twin rappresentano il futuro in molti settori industriali. L’uso di prototipi digitali e l’esplorazione digitale per affrontare l’aumento nella complessità dei prodotti, ambienti di progettazione sempre più estesi e l’emergenza dei digital twin aprono l’uso della simulazione a nuovi utenti e sviluppano collegamenti con i prodotti in essere. Siamo all’inizio di una nuova era che ci porterà dallo sviluppo simulation-driven al simulation-driven engineering.