Non si tratta di un grande impianto per la produzione di massa, ma il nuovo assetto dell’impianto Audi Böllinger Höfe (a Heilbronn nel Baden-Württemberg) è comunque interessante. In questo stabilimento vengono infatti assemblate due supercar quali l’elettrica ad alte prestazioni Audi e-tron GT quattro, sulla la stessa piattaforma della Porsche Taycan, e la R8 con un possente motore V10: produzioni di élite che sono state rivoluzionate secondo i dettami dell’industria più moderna.
Indice degli argomenti
Calcoli centralizzati
L’innovazione di Audi è focalizzata sull’automazione industriale e ha il suo caposaldo nell’utilizzo del server locale Edge Cloud 4 Production.
La capacità di calcolo viene centralizzata in questi server, che prendono il posto di centinaia di PC industriali, e il software assume un ruolo preponderante rispetto all’hardware: si tratta di una sorta di software defined plant.
Gerd Walker, Membro del Consiglio di Amministrazione di Audi AG per Produzione e Logistica, osserva infatti che “prima dovevamo acquistare hardware per introdurre nuove funzioni, ora basta acquistare applicazioni software: è un grande passo in avanti verso la produzione basata sull’IT”.
I PC industriali sono stati sostituiti con thin client, terminali ‘leggeri’ che servono più che altro per raccogliere gli input dell’operatore e visualizzare i dati richiesti/necessari: l’aspetto computazionale risiede infatti prevalentemente nei server.
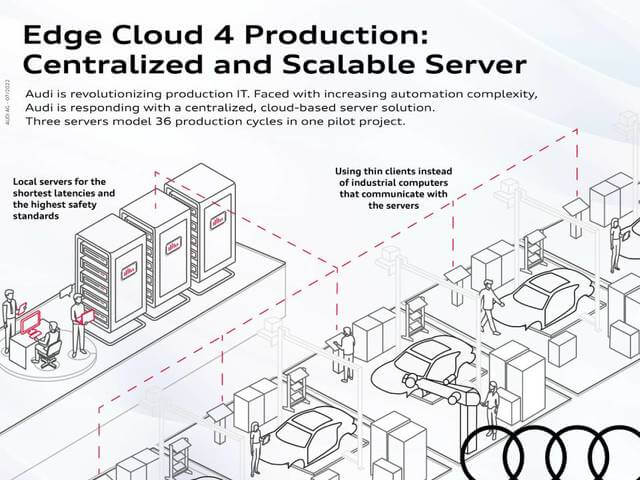
Ottimizzare le risorse
Questi terminali hanno quindi un consumo energetico ridotto che ne permette l’alimentazione in modalità PoE – Power-over-Ethernet: un cavo per la rete dati era comunque necessario ma rimane il solo, semplificando quindi il layout degli impianti dello stabilimento.
Ricordando un altro vantaggio promesso dall’Edge Cloud 4 Production – la sostituzione di un gran numero di PC industriali – è facile rendersi conto che non c’è più bisogno di manutenere i loro dischi rigidi, alimentatori e memorie di massa individuali, cosa che riduce anche il carico di lavoro degli addetti. Migliora anche la sicurezza del processo, perché in caso di malfunzionamenti il carico può essere spostato su altri server grazie a una certa ridondanza: un classico PC industriale guasto andava invece sostituito o riparato con aggravio di tempi e costi.
La capacità dei client è calibrata: per vedere cosa deve essere montato su un veicolo è inutile usare un PC, che risulta sovradimensionato per capacità di elaborazione e archiviazione. Un altro vantaggio sostanziale è la facilità con la quale si possono ‘propagare’ gli aggiornamenti, anche nel settore della cybersecurity. L’infrastruttura basata su cloud permette infatti di installare in pochi minuti a tutti i terminali le patch e gli update senza problemi di fermo-macchina.
Nel nome dell’Iperconvergenza
I server Edge Cloud 4 Production, situati localmente nell’impianto Böllinger Höfe pertinente al grande stabilimento di Neckarsulm hanno una infrastruttura di tipo Iperconvergente (Hyper-Converged Infrastructure – HCI).
Si tratta di un sistema software-defined che combina tutti gli elementi di un data center e cioè archiviazione, elaborazione, rete e gestione. Funzionalità quali il web server, il database e il sistema gestionale sono quindi riconfigurabili via software, il cloud può essere rapidamente adattato ai diversi requisiti della produzione e i server locali permettono latenze molto basse. Il sistema non è però collegabile a un cloud pubblico per rispettare i requisiti di sicurezza della produzione industriale: i server sono usati in modalità Edge Computing vicini all’ambiente di produzione.
Dalla fibra ottica al 5G
I due data center dello stabilimento di Neckarsulm sono pronti per la produzione in serie e sono collegati attraverso un cavo in fibra ottica al Böllinger Höfe, mentre la rete cellulare veloce 5G sarà introdotta più avanti.
A oggi tutti gli AGV – i veicoli a guida automatizzata per la movimentazione interna – hanno un loro computer distinto che, oltre a presentare limiti nel riuscire a implementare nuove funzionalità, va quindi aggiornato individualmente.
Per poterli controllare con un client c’è quindi bisogno di una rete wireless veloce e ad alta affidabilità. Il 5G è comunque già soggetto a intense sperimentazioni nei laboratori dell’Audi Production Lab in vista di una sua futura adozione.