Accelerare il passaggio dalla fabbricazione tradizionale a quella additiva per le applicazioni produttive in volumi medi e ridotti non coperte dai metodi di fabbricazione tradizionali: questo è l’obiettivo di Stratasys, che annuncia il lancio di 3 nuove stampanti 3D.
Con questi 3 nuovi prodotti l’azienda, specializzata in soluzioni di stampa 3D a base di polimeri, punta a coprire un’ampia quota del mercato multimiliardario della fabbricazione additiva di parti di uso finale.
“Stiamo entrando rapidamente nell’era della Fabbricazione Additiva 2.0, nella quale vedremo i protagonisti della produzione globale andare oltre la prototipazione per sfruttare appieno tutta la flessibilità che la stampa 3D apporta all’intera catena del valore della produzione. L’industria è a un punto di svolta e noi vogliamo esserne protagonisti”, commenta Yoav Zeif, CEO di Stratasys.
Indice degli argomenti
3D Origin One, per la produzione di parti finali
Tra le novità, la stampante 3D Origin One, progettata per la produzione di parti di uso finale. Il lancio del prodotto segue di pochi mesi l’acquisizione della start-up Origin One da parte di Stratasys, nel dicembre 2020, in linea con la strategia dell’azienda di posizionarsi come leader nel nel settore della stampa 3D di polimeri in ambito manifatturiero.
Il sistema Origin One utilizza la tecnologia brevettata P3 per produrre parti in una vasta gamma di materiali ad alte prestazioni con risultati di precisione, ripetibilità e tempi di lavorazione senza precedenti.
Il nuovo prodotto rappresenta un aggiornamento della precedente Origin One, con un vassoio di produzione più grande, un flusso di lavoro hardware e software rinnovato, migliori prestazioni e un più alto grado di fruibilità. Ulteriori aggiornamenti al software verranno resi disponibili attraverso un sistema in cloud non appena verrà avviata la distribuzione della Stratasys Origin One, attualmente programmata per il quarto trimestre dell’anno.
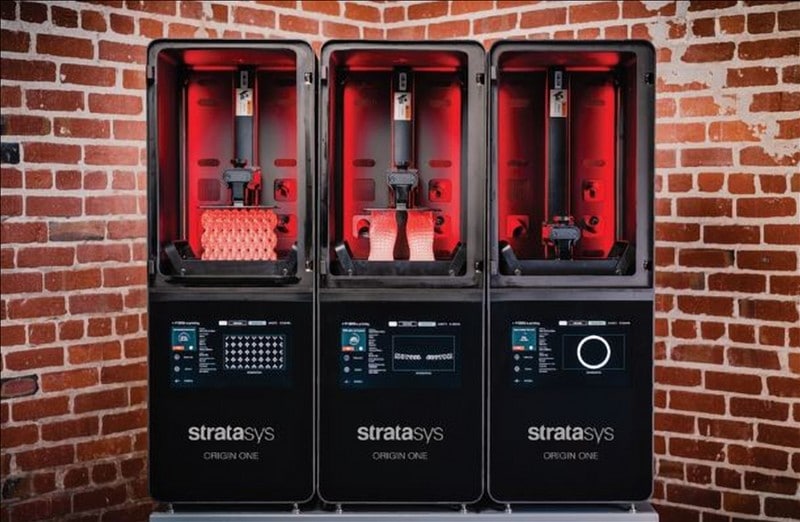
La stampante è già in utilizzo presso alcuni clienti, tra cui l’azienda TE Connectivity, specializzata nella produzione di connettori e sensori. L’azienda ha collaborato con Origin e Henkel allo sviluppo di un fotopolimero di grado aerospaziale, che ha superato i rigorosi test ambientali richiesti dal settore.
Grazie a questa collaborazione, TE Connectivity è in grado, ad oggi, di produrre migliaia di pezzi, compreso il suo primo prodotto per l’industria aerospaziale stampato in 3D, ovvero il supporto del connettore della serie 369, progettato per mantenere i connettori accoppiati all’interno degli aerei.
“Ci siamo concentrati sulla capacità di soddisfare rigorosi criteri di accuratezza e ripetibilità per i connettori stampati in 3D che richiedono una precisione in micron a doppia cifra. Stratasys e Origin sono stati dei partner eccellenti nell’aiutarci a raggiungere questi obiettivi e a dimostrare che è possibile utilizzare la fabbricazione additiva su scala per produrre decine di migliaia di parti”, commenta Mark Savage, responsabile e senior manager per la fabbricazione additiva presso TE Connectivity.
La nuova stampante FDM per le applicazioni industriali
Tra i prodotti presentati, anche una nuova stampante di grande formato, pensata per applicazioni industriali: si tratta del modello F770, con una diagonale di 117 cm e la camera di costruzione totalmente riscaldata più lunga presente sul mercato.
Lo spazioso vassoio da più di 340 decimetri cubi (372 litri) apre nuove opportunità di produzione, prototipazione e fabbricazione di parti impossibili da ottenere con stampanti più piccole.
La F770 stampa materiali termoplastici standard e utilizza materiale di supporto solubile consentendo di progettare e realizzare parti con strutture interne complesse e interventi di post-lavorazione ridotti al minimo. Inoltre, il software integrato GrabCAD Print semplifica il flusso di lavoro dal file CAD alla stampa, anche per parti con geometrie avanzate
e di grandi dimensioni.
Stratasys fornisce la funzionalità di connessione alle applicazioni aziendali attraverso lo standard MTConnect e il suo GrabCAD Software Development Kit. Il funzionamento 24 ore su 24 e 7 giorni su 7 è assicurato dal monitoraggio tramite dispositivo mobile e l’uso di una telecamera integrata, per un massimo di 140 ore di stampa non presidiata.
La F770 aiuta i produttori a evitare gli alti costi e i lunghi tempi di lavorazione dei metodi tradizionali, la complessità di alcune stampanti 3D di fascia alta, oltre alla scarsa qualità e ai costi nascosti di molte altre stampanti 3D di grande formato di fascia bassa presenti sul mercato. Il sistema, inoltre, ha una precisione di meno 0,25 mm sull’asse XY e un’area di costruzione di 1000 x 610 x 610 mm.
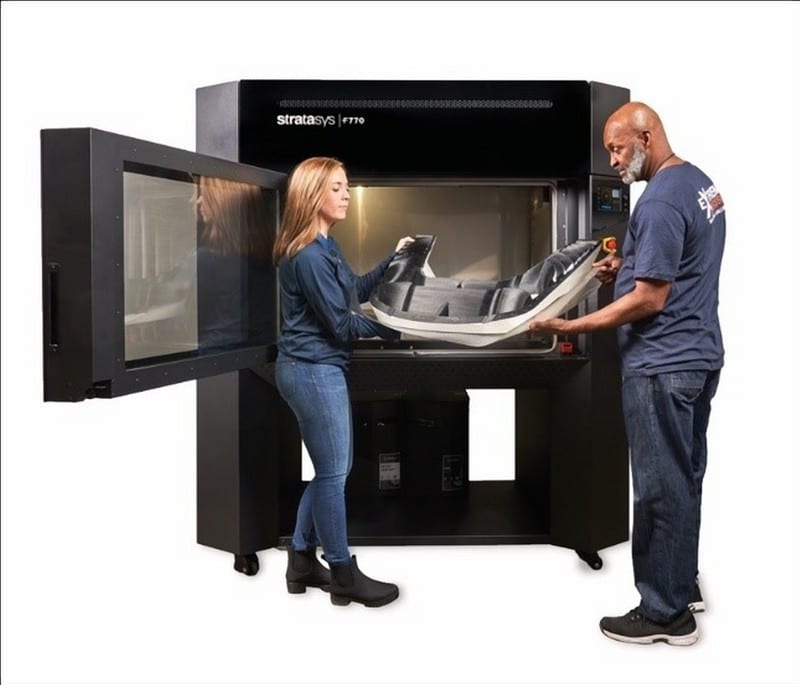
Le applicazioni principali includono maschere e staffaggi di grandi dimensioni, grandi prototipi funzionali come i pannelli di veicoli e la costruzione simultanea di numerose parti di produzione, sfruttando tutta la superficie del vassoio.
“A mano a mano che l’uso delle stampanti 3D aumenta negli stabilimenti di produzione, i fabbricanti possono sfruttarne la capacità sia per produrre pezzi di grandi dimensioni sia per realizzare contemporaneamente più pezzi di dimensioni più piccole. Abbiamo costruito la F770 per offrire opzioni di produzione capaci di adattarsi ad ogni misura”, aggiunge Dick Anderson, vicepresidente senior e responsabile di fabbricazione di Stratasys.
Sub-Zero Group, produttore statunitense di elettrodomestici di fascia alta è tra i clienti che hanno avuto modo di testare la versione beta del prodotto e ha riscontrato una riduzione dei costi di fabbricazione che va dal 30 al 40%, grazie alla possibilità di realizzare internamente anche le parti di maggiori dimensioni.
“Il nostro laboratorio di stampa 3D si trova ad affrontare la costruzione di nuovi prodotti ogni sei settimane. Quanto più velocemente riusciamo a far girare le cose, tanto meglio. E il modo più rapido di farlo è cercare di produrre internamente il più possibile. La F770 è in grado di soddisfare questa esigenza”, dichiara Doug Steindl, supervisore del laboratorio di sviluppo aziendale presso il Sub-Zero Group.
La F770, il cui costo sarà inferiore ai 100 mila dollari, sarà disponibile con il materiale ASA in avorio o con l’ABS-M30 nero, insieme al materiale di supporto solubile SR-30. Il prodotto è attualmente disponibile per gli ordini, mentre l’azienda prevede di iniziare con le prime consegne entro fine giugno.
La stampante 3D H350 basata sulla tecnologia SAF per la produzione su larga scala
Supportata dalla tecnologia SAF, la nuova H350 è progettata per offrire alle aziende omogeneità di prodotto, costi unitari competitivi e prevedibili, come pure un controllo completo della produzione in serie di migliaia di parti. La stessa H350 monta una dozzina di componenti diversi stampati in 3D con tecnologia SAF.
Questa tecnologia di fabbricazione additiva di qualità industriale esegue i passaggi chiave della stampa tridimensionale sempre nella stessa direzione lungo tutto il vassoio e all’interno di tutto il volume di costruzione, assicurando l’uniformità termica e quindi l’omogeneità di tutte le parti stampate, indipendentemente dalla loro posizione sul vassoio.
Inoltre, grazie alla tecnologia SAF, la stampante 3D H350 può contribuire a ridurre i costi operativi e ad aumentarne la prevedibilità: il sistema di gestione della polvere Big Wave, per esempio, riduce l’invecchiamento della polvere, mentre le testine piezoelettriche di qualità industriale, coperte da garanzia, sono progettate in modo tale da non necessitare di
sostituzioni regolari.
La nuova H350 è dotata di una serie di caratteristiche di controllo pensate appositamente per le aziende pronte a implementare la fabbricazione additiva per la produzione in serie: tutti i dati di costruzione vengono infatti registrati per consentire la tracciabilità del processo e restano sotto il controllo completo del cliente. Anche i materiali possono essere controllati, tracciati e rintracciati, mentre le impostazioni di stampa possono essere ottimizzate in funzione delle esigenze di ciascun cliente.
“La nuova H350 non è solo una stampante, ma una soluzione completa pronta all’utilizzo. Abbiamo curato sia la parte di hardware che di software, per fornire ai nostri clienti una soluzione plug & play”, aggiunge Yoav Zeif.
Per la costruzione di questo modello, l’azienda ha impiegato una plastica a base biologica realizzata a partire da materie prime rinnovabili ricavate da olio di ricino prodotto in modo sostenibile. Rispetto al PA12, il PA11 ha un impatto ambientale minore, una maggiore resistenza termica e una minore fragilità. Ha superato i test iniziali tra cui ISO 10993-5 per la citotossicità e UL94 HB per l’infiammabilità.
A questo Stratasys ha aggiunto la tecnologia SAF, che permette di compattare le parti nel volume a una densità
standard fino al 12%, rispetto al 6-10% delle stampanti 3D con fusione su letto di polvere, permettendo di produrre più parti per ogni ciclo di stampa o in tempi di produzione ridotti.
Inoltre, la stampante potrà essere integrata con i sistemi degli impianti di produzione, grazie allo standard MT Connect. In futuro, Stratasys fornirà anche il supporto di GrabCAD Print per la preparazione del processo di stampa.
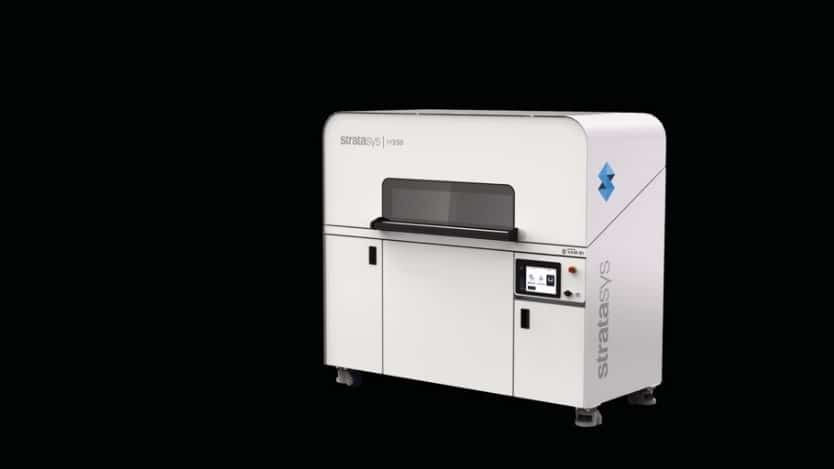
Anche per questa stampante le applicazioni sono numerose (tra cui cover, connettori, cerniere, portacavi, alloggiamenti per componenti elettronici e condotti) e rivolte soprattutto a quelle aziende che hanno l’esigenza di produrre rapidamente grandi volumi di parti stampate in 3D con costi vantaggiosi e prevedibili.
“La stampa 3D su larga scala sta progressivamente trasformando la produzione in diversi settori in tutto il mondo, mentre le imprese puntano ad acquisire maggiore snellezza ed efficienza”, commenta Omer Krieger, vice presidente esecutivo per la strategia di prodotto e lo sviluppo aziendale di Stratasys.
Il modello H350 è l’ultimo della serie H, che sfrutta la tecnologia SAF per la produzione additiva su larga scala, che l’azienda ha presentato lo scorso mese.
La stampante è già in utilizzo, in versione beta, presso alcuni clienti Stratasys, tra cui Goetz Maschinenbau, un centro servizi tedesco che fornisce parti on-demand e che rifornisce di parti in plastica di uso finale un ampio portafoglio di clienti dei settori dell’automobile, dei beni di consumo e medicale.
“Abbiamo evaso ordini sia per parti di grandi dimensioni che per diverse centinaia di parti più piccole. Siamo rimasti colpiti dalle prestazioni del sistema e alloggiamento del circuito e staffa stampati in 3D con la stampante Stratasys H350. La produzione tradizionale richiederebbe diversi pezzi separati da produrre e assemblare insieme. La produzione additiva
con la H350 permette di produrlo come un unico pezzo dalla tecnologia SAF, che assicura risultati uniformi all’interno di tutto il volume di costruzione. Inoltre, il sistema ha dimostrato di essere straordinariamente affidabile”, commenta Philipp Goetz, proprietario di Goetz Maschinenbau.
La stampante sarà disponibile a partire dal terzo trimestre del 2021, mentre le parti stampate con l’H350 sono già disponibili in quantità limitate attraverso il servizio Stratasys Direct Manufacturing.
Perché è il momento di passare alla manifattura additiva
“La manifattura additiva non può più essere vista come un’opzione. Gli avvenimenti dell’ultimo anno hanno dimostrato come occorre pensare a una produzione più agile e flessibile, in grado di resistere anche ad eventi improvvisi”, sottolinea Zeif, citando la pandemia, ma anche il recente blocco del Canale di Suez e i sempre più frequenti eventi meterologici estremi provocati dai cambiamenti climatici.
“Non si tratta solo una maggiore flessibilità – aggiunge il CEO di Stratasys – la stampa 3D permette di rispondere alle sfide che stiamo vivendo, alle necessità di avere metodi produttivi più efficienti e sostenibili, in grado di ridurre i tempi di messa sul mercato del prodotto”.
Nel 2020 l’azienda ha realizzato più del 25% dei suoi profitti da applicazioni legate alla produzione. In futuro, con un portafoglio completo e integrato di soluzioni hardware, software, materiali e servizi per la stampa 3D, Stratasys prevede che il suo fatturato di produzione supererà gli altri segmenti, con un tasso annuo di crescita superiore al 20% a partire dal 2022.