Con il lancio del sistema di trasporto e movimentazione senza contatto Acopos 6D B&R, azienda austriaca che sviluppa soluzioni di automazione industriale e da qualche anno parte del gruppo ABB, mette una nuova soluzione ad elevato contenuto tecnologico a disposizione delle aziende manifatturiere che vogliono muoversi nella direzione della “produzione adattiva”: il sistema infatti è pensato proprio per la produzione di piccoli lotti con frequenti cambi di design e dimensioni da un prodotto all’altro.
“Acopos 6D è l’ultima novità per la movimentazione intelligente che B&R propone al mercato dopo il SuperTrak e AcoposTrak”, spiega Dario Rovelli, Head of Product Management – Motion & Mechatronic Systems di B&R. “Acopos 6D è pensato per la movimentazione all’interno della stazione di lavoro ed è quindi un complemento rispetto ad AcoposTrak, che è invece pensato per muovere i prodotti tra diverse stazioni di lavorazione”.
L’innovativo sistema, pensato per applicazioni nel farmaceutico, nel packaging e nelle operazioni di assemblaggio, si compone di un controllore in grado di controllare fino a un massimo di 200 segmenti (che uniti insieme compongono il pavimento del sistema) e fino a 50 shuttle o navette.
Gli shuttle sono delle piastrelle quadrate o rettangolari disponibili in diverse dimensioni (minimo 12 cm e massimo 45 cm per lato) che supportano a loro volta diverse portate, da 600 grammi a ben 14,4 kg.
Indice degli argomenti
Acopos 6D, flessibilità senza contatto
Tra shuttle e segmenti viene formato un campo magnetico controllato che permette la levitazione delle navette, che sono così in grado di muoversi senza contatto con accelerazioni fino a 20 mq/s e velocità di 2 m/s. Tra segmenti e shuttle dunque non c’è mai contatto, rendendo quindi superflue le operazioni di lubrificazione. Questo spiega perché un sistema del genere sia particolarmente indicato per ambienti in cui la pulizia non è un optional. A questo si aggiunga che i segmenti offrono un grado di protezione IP 67 e possono quindi essere utilizzati anche senza protezione.
Grazie al sistema di controllo, gli shuttle possono muoversi avanti e indietro (asse Y), a destra e sinistra (asse X) e anche in altezza (asse Y). A queste tre dimensioni si aggiungono altre tre dimensioni, cioè la possibilità di ruotare lungo ciascuno dei tre assi. La rotazione lungo gli assi è utile perché permette di compensare oscillazioni di liquidi o favorire il carico/scarico del materiale.
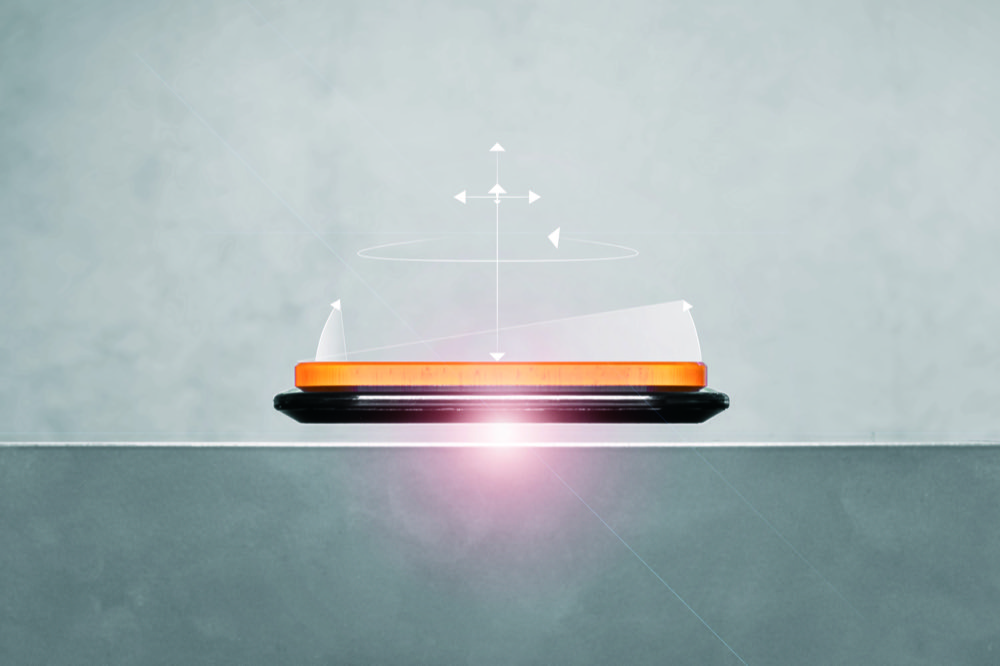
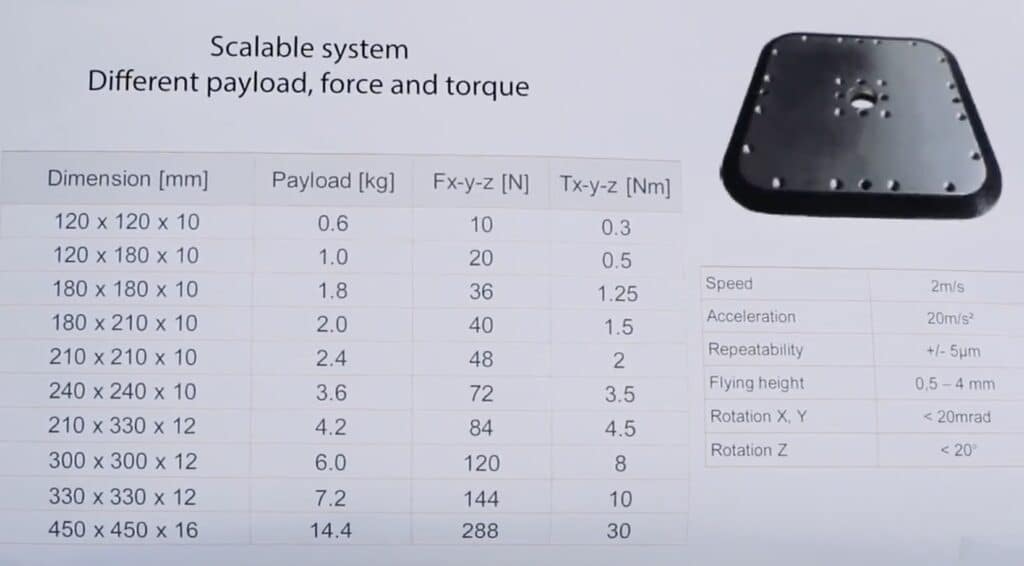
Il sistema di controllo, in grado di gestire forza e coppia, può anche effettuare la pesatura del carico con una precisione di +/-1 grammo indipendentemente dal carico.
La movimentazione delle navette viene gestita via software e ne consente l’impiego ad alta velocità sia individualmente sia in gruppo (anche a distanza zero tra diverse navette), con adeguati algoritmi che consentono di evitare collisioni. Le navette possono essere utilizzate anche come assi nelle stazioni di lavorazione. Una navetta che trasporta un pezzo può, ad esempio, seguire un percorso CNC permettendo il montaggio rigido dell’utensile di lavorazione.
L’applicazione può essere completamente virtualizzata per poter testare i diversi layout prima del loro deployment.
A ogni navetta viene assegnato un ID univoco a livello globale. All’avvio, il controllore localizza immediatamente ogni navetta sui segmenti del motore, e la produzione può iniziare senza lunghe sequenze di homing o input manuale da parte di un operatore. Le navette offrono una ripetibilità di posizionamento di ±5 µm, rendendo Acopos 6D perfettamente adatto per applicazioni con requisiti di posizionamento stringenti, come quelle nell’industria elettronica e nell’assemblaggio di componenti meccanici ed elettronici.
Una caratteristica da non trascurare è la possibilità di montare il sistema non soltanto in orizzontale, con le navette che corrono lungo il piano magnetico, ma anche in verticale e addirittura “a testa in giù”. Questa caratteristica può risultare interessante per alcune applicazioni in cui, per esigenze di spazio o applicative, il sistema viene montato a soffitto.
Il sistema di trasporto è inoltre agevolmente scalabile: poiché la potenza computazionale è decentralizzata, è possibile accrescere le dimensioni del sistema senza dover cambiare il PLC che si occupa del coordinamento del sistema.
Produzione, assemblaggio e packaging
Il sistema proposto da B&R e sviluppato in collaborazione con l’azienda canadese PMI (Planar Motor Inc) è pensato per diversi ambiti applicativi.
Il primo è l’ambito farmaceutico per applicazioni di riempimento asettico, lavorazioni in clean room e macchine per la sterilizzazione. In questi ambienti viene infatti apprezzata l’assenza di lubrificanti e di usura meccanica.
Il secondo ambito è quello del packaging primario e secondario, soprattutto nel settore del Food. Qui infatti il sistema Acopos 6D consente un’importante riduzione del buffering e del sorting; vengono inoltre apprezzate le funzionalità del sistema come la possibilità di pesare i carichi con grande previsione e la riduzione degli ingombri.
Il terzo ambito applicativo è quello dell’assemblaggio nel mondo dell’elettronica, dell’automotive e delle batterie di nuova generazione. Qui i fattori più apprezzati sono l’ambiente pulito e la buona ripetibilità (5 micrometri).
