SmartFactoryKL è uno dei consorzi tecnologico tedesco (KL sta per Kaiserlautern, la città dove ha sede) maggiormente impegnati nello sviluppo di applicazioni sperimentali in chiave Industry 4.0 (o meglio Industrie 4.0). Alla prossima Hannover Messe, i 19 partner industriali coinvolti nel progetto, insieme con il centro di ricerca tedesco per l’intelligenza artificiale DFKI, presenteranno gli ulteriori sviluppi della loro ricerca applicata.
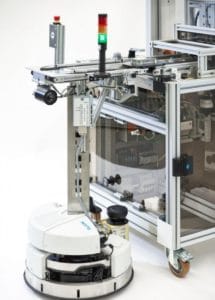
La nuova demo su cui sono al lavoro i membri di questo progetto vede per la prima volta protagonisti non più moduli produttivi disposti lungo un’unica linea, ma moduli distribuiti su tre diverse isole di produzione. In fiera verrà mostrato come sia possibile combinare gli elementi delle isole in modi differenti, a seconda delle esigenze produttive, grazie all’utilizzo di un sistema di trasporto flessibile composto da una piattaforma robotica (un robot autonomo) e da nastri trasportatori.
A decidere chi e come procederà alla lavorazione del pezzo sarà il sistema MES, sulla base delle informazioni sulla topologia dell’impianto ricevute dal bus utilizzato per l’integrazione. Nel caso della demo presente in fiera, il sistema di trasporto flessibile distribuirà il prodotto in un’area limitata; nel caso delle applicazioni reali, invece, questo sistema potrà essere applicato su diverse linee produttive o addirittura su diversi siti produttivi.
Siccome il ciclo delle lavorazioni relative a un determinato prodotto è salvato nella memoria presente sul tag RFID, e quindi gestita dalla struttura IT, è sempre possibile trovare il modulo giusto per il successivo step di elaborazione.
Il ruolo degli standard
Alla base degli sviluppi di questa evoluzione della demo SmartFactoryKL c’è il rispetto di tre tipi di standard. Il primo è relativo al tag RFID per la descrizione dei dati di lavorazione, che è codificato sulla base della normativa ISO 15693. Ciò fa sì che tutti i lettori RFID presenti nel sistema possano leggere i dati in maniera indipendente dal produttore che li ha scritti.
Il secondo standard è il protocollo di comunicazione OPC UA. Attraverso OPC UA la stazione di carico comunica quando un prodotto debba essere spostato. Allo stesso tempo ogni modulo utilizza lo stesso set di dati di OPC UA e lo passa al server in modo che sia assicurata la comunicazione standard tra tutti gli elementi.
Il terzo step è la standardizzazione dell’hardware: la stazione di carico che è stata recentemente introdotta come parte del sistema esteso può essere utilizzata con flessibilità perché le funzioni meccaniche di base di tutti i moduli sono standard. Per esempio la posizione di ciascuno dei nastri trasportatori è determinata da un sensore che “legge” l’ambiente circostante.
Le aziende partner che sono state coinvolte nel sistema sono: Belden/Hirschmann, Bosch Rexroth, Cisco, Eplan Software & Service, Festo, Harting, Ibm, iTAC, Lapp Kabel, Mettler Toledo, Minitec, Phoenix Contact, Pilz, proAlpha, Sap, TE Connectivity, TÜV Süd, Weidmüller e Wibu-Systems.