La rivoluzione dell’Industry 4.0 è iniziata da qualche anno, ma per molte aziende italiane si tratta ancora di una novità, se non addirittura di un’idea da prendere in considerazione per un futuro più o meno prossimo. E anche chi ha già cominciato a implementare progetti 4.0 nelle sue aziende spesso è partito con un approccio non ottimale. Spesso, infatti, si è sfruttata la leva fiscale – in particolare l’iperammortamento – per rinnovare il parco macchine aziendale, e ci si è fermati lì, in attesa di capire quale dovesse essere il secondo passo. Ne abbiamo parlato, insieme ad altri argomenti, con Marino Crippa, Direttore Marketing di Bosch Rexroth.
Il gruppo Bosch è impegnato sul fronte industria 4.0 fin dall’inizio, ed è fra le poche aziende che possono vantare un “doppio ruolo” di produttore e cliente di sé stessa. “Diciamo subito che Bosch è socio fondatore del consorzio tedesco per l’industria 4.0, nato nel 2011 – conferma Crippa – quindi sono circa 8 anni che Bosch lavora attivamente su progetti di digitalizzazione e digital trasformation, in un contesto che è particolare. Da un lato ci sono 270 stabilimenti che hanno necessità di continuo miglioramento, e dall’altra divisioni prodotto, come la Rexroth, che sono fornitori di tecnologia. Per cui questa dualità, questo essere contemporaneamente user e provider, per noi è un volano per il miglioramento continuo dei nostri prodotti e processi, e ci permette di sfruttare il know-how tecnico e di processo acquisito internamente per portare le nostre soluzioni sul mercato”.
Come vede Bosch Rexroth l’innovazione e il rapporto tra aggiornamento tecnologico e innovazione di processo? “Nella nostra idea di fabbrica del futuro, la tecnologia è, diciamo così, un collateral: è un qualcosa di subordinato alla robustezza del processo. Noi siamo un’azienda maniacalmente orientata alla lean production, per cui per noi Industry 4.0 è uno strumento per abilitare un continuo miglioramento dei processi stessi, un elemento di trasparenza dei processi per continuare a migliorarli e conseguentemente aumentare la produttività, far scendere il costo unitario per prodotto generato eccetera. È un percorso logico che ci porta dal processo alla raccolta dei dati, adesso possibile in modo efficiente attraverso la tecnologia digitale, l’analisi dei dati e soprattutto la generazione di decisioni in un tempo infinitamente inferiore rispetto alla raccolta dei dati manuale. Usiamo la tecnologia 4.0 perché ci permette di prendere decisioni sul processo, per migliorarlo in tempi sempre più brevi”.
E come fa tutto questo? “Lo facciamo attraverso gli use case. Uno dei claim che usiamo è think big, start small, ovvero pensare all’azienda digitale ma cominciare con progetti circoscritti e limitati. Il manuale dell’industria 4.0 non esiste, va costruito progetto dopo progetto, per cui definire lo use case in maniera precisa, circoscritta con degli indicatori di business, con la tecnologia necessaria e soprattutto le persone che devono governare questo nuovo processo in evoluzione lo diventa importante. Quindi nello use case allineiamo processo, obiettivi di business, tecnologie abilitanti ma soprattutto formazione e profili professionali abilitanti all’evoluzione del processo”.
È vero che la tecnologia è il mezzo e non il fine di una trasformazione dell’azienda in chiave digitale, ma i trend tecnologici hanno sicuramente un loro peso nel plasmare l’evoluzione. Quali sono i trend significativi secondo Bosch Rexroth? “Parlando di tecnologia, quelli che vediamo come trend tecnologici nel breve sono il TSN, come bus di campo a livello di network di macchina, e il 5G a livello network di fabbrica. Di conseguenza l’estensione del volume di dati metterà in primo piano il tema della cybersecurity. Da tenere anche presente il ruolo che l’intelligenza Artificiale, avrà a medio termine a supporto dei processi decisionali”.
I trend del futuro quindi sono abbastanza definiti, ma cosa sta succedendo adesso nelle fabbriche italiane? “In Bosch Rexroth abbiamo un claim, che è Now, Next, Beyond, che va a identificare il livello di maturità che ci aspettiamo nelle aziende. Quello di cui abbiamo parlato finora è un Next avanzato. Girando spesso per le fabbriche quasi quotidianamente vedo parecchio potenziale di sviluppo per il Now. Troppe volte trovo ancora chi pensa che cybersecurity significhi mettere l’antivirus sul computer. Su questi argomenti ci sarà da ragionare e diffondere competenza. Ma prima di arrivare lì, le aziende devono cominciare a irrobustire i processi. Di lean production se ne parla da 10 anni, ma c’è ancora strada da fare, andando oltre all’impulso dato dall’iperammortamento”.
Intende dire che non si è intervenuti a ridisegnare i processi per sfruttare le potenzialità delle nuove macchine? “Grazie al piano Impresa 4.0, l’industria ha doverosamente rinnovato il parco macchine, mediamente vecchio di 17 anni, ma a volte in maniera non sincrona all’ottimizzazione di processo, che la nuova tecnologia potrebbe abilitare. Bisogna lavorare anche sul valore dei dati forniti dalla macchina, ed è anche una questione di mindset; questa macchina mi dà dei dati, per esempio, sul comportamento del motore: cosa faccio con questi dati? Abilito un processo di manutenzione predittiva? Abilito un monitoraggio di disponibilità di macchina per capire se posso migliorare i costi di produzione? Quello che vedo come Now è ancora molto legato all’evoluzione culturale che permetta di avere la consapevolezza del valore dei dati che queste macchine adesso possono fornire, e dei miglioramenti che possono portare ai processi”.
Indice degli argomenti
Oleodinamica 4.0
“Le faccio un esempio relativo a un nostro nuovo prodotto, CytroBox”, spiega Crippa. “È una centrale oleodinamica, come dire tecnologia percepita come matura. Ma CytroBox trasforma il paradigma di generazione della potenza idraulica, perché grazie alla digitalizzazione, occupa un quarto di spazio in meno, e quindi supponendo di avere 10 centrali oleodinamiche in una piccola azienda che fa stampaggio della plastica, fa risparmiare metri quadri che ampliano lo spazio produttivo. Avendo risparmiato spazio sulla centrale, posso mettere una macchina da stampaggio in più, e aumento la produttività per metro quadro del mio capannone”.
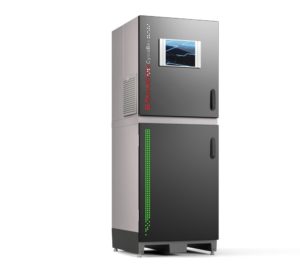
E poi c’è il risparmio energetico, un altro grande trend che sarà da affrontare nei prossimi anni. “CytroBox risparmia l’80% in termini di energia e di risorse in generale, perché tra l’altro usa un quarto dell’olio utilizzato da centrali di concezione tradizionale. Quindi immaginiamo la riduzione di impatto ambientale, dovendo smaltire il 75% dell’olio che gestivo prima. Altro tema è il rumore. CytroBox riduce del 30% il rumore della centrale, quindi le condizioni di lavoro migliorano, l’ambiente di lavoro e la relazione uomo-macchina migliorano, è un altro tema che possiamo incominciare a trattare nello stesso contesto dell’oleodinamica industriale. Ecco come una tecnologia matura, magari poco sexy mostra tutto il suo potenziale di sviluppo nella digital trasformation”.
Anche questo è un elemento di trend che è da sottolineare, e a SPS Italia Bosch Rexroth andrà a sottolinearlo, perché porterà CytroBox per presentarlo nell’ottica del brand e di che cosa abilita la tecnologia digitale in un prodotto “tradizionale”.
“Il messaggio che porteremo in SPS – dice Crippa – non è il prodotto in sé, ma come il prodotto possa abilitare il percorso di trasformazione digitale sia per chi costruisce macchine sia per chi utilizza. E non portiamo solo prodotti, portiamo una macchina di un cliente, una stampante 3D – è un trend anche questo, uno dei prodotti è una moto elettrica completamente stampata con la stampante 3D -, e presentiamo i vantaggi che una macchina costruita con le tecnologie che Bosch Rexroth ha sviluppato porta ai costruttori: riduzione del time to market nella costruzione della macchina, utilizzo di tecnologie per andare a recuperare macchine che adesso non sono intelligenti ma continuano a fare il loro lavoro, aggiungendo intelligenza. Significa che il costruttore di macchine può andare ad allungare il ciclo di vita delle macchine esistenti aumentando i guadagni, avviando una manutenzione predittiva al posto di quella lasciata in carico all’end user. Un altro tema è quello della servitizzazione delle macchine. Se lavoro in mercati sufficientemente maturi, posso cominciare a non vendere più la macchina, e vendere la funzione della macchina. Uno dei modelli di business che stiamo studiando per la CytroBox è vendere non il prodottto ma la potenza erogata. Perché alla fine un costruttore di macchine non ha bisogno della fisicità della centrale, ha bisogno della portata e della pressione che vengono prodotte dalla macchina”.
Verso la servitizzazione
Questo trend si è affermato da anni nell’IT. IBM vendeva i mainframe con il massimo di CPU installate, ma il cliente pagava per le CPU che usava effettivamente, e se serviva più potenza, venivano sbloccate (e pagate) più CPU. Le stampanti aziendali ormai non si vendono, si noleggiano a lungo termine con contratti basati su numero di pagine stampate e costo/pagina concordato. E i servizi in cloud sono l’apoteosi del concetto: non compro più il centro di calcolo, ne affitto uno e lo pago per quanto lo uso. Nell’OT dell’Industry 4.0 Bosch prevede quindi una dinamica simile?
“I trend sono questi, e porteranno a cambiare la prospettiva del go-to-market di un prodotto. Certo vendere la centrale, vendere la componentistica è ancora il core business di Bosch Rexroth, ma cominciare a pensare a lavorare a quattro mani con il costruttore, per andare dal suo cliente e dirgli che, a fronte di questi vantaggi, non si deve più parlare di prezzo, ma cominciare a parlare di total cost of ownership, di return on investment, non tanto del singolo componente ma dato da tutta la macchina. Alla fine a un’azienda che produce contenitori per cucina non interessa quanto paga la macchina, gli interessa quanto gli costa ogni scatola che produrrà. E se riusciamo a spostare il capitale investito, anche in iperammortamento, da capex a costi operativi, probabilmente riusciamo a cambiargli anche le dinamiche di cassa, e magari riusciremo ad avere un approccio – ma questo è molto, molto Beyond – e un modello di business che permetterà di abilitare macchine diverse e tecnologie diverse che saranno disponibili al momento o tra 2 o 3 anni, come il 5G”.
Ma anche senza lanciarci avanti verso i futuri modelli di business legati alla servitizzazione, già oggi ci sono argomenti concreti per ricorrere a soluzioni di questo tipo. “La centrale CytroBox costa di più di una tradizionale, però risparmia l’80% di energia. Potremmo anche pensare di dare la centrale allo stesso costo di quella tradizionale e recuperare il delta con il risparmio energetico del mio cliente. Non perché siamo generosi, ma perché il nostro prodotto gestisce un numero tale di dati che saremo noi a presentargli la bolletta. Cambia la prospettiva. La tecnologia è disponibile, se non adesso fra tre mesi o tre anni. Il tema impatta sull’intera architettura aziendale dalla progettazione del prodotto al gestione che per supportare la servitizzazione io devo avere un sistema gestionale, un Erp, che oltre gestire la vendita di un codice prodotto deve prevedere la vendita di servizi o addirittura basare la remunerazione sulla produzione del cliente”.
Dal piccolo progetto al quadro complessivo
Il dubbio, a questo punto, è sul come si sposa il fatto di avere una visione complessiva e contemporaneamente partire con piccoli progetti. Non si rischia di trovarsi con tanti standard che non parlano fra loro?
“Due punti importanti: il primo è che Bosch crede fermamente negli standard aperti, OPC UA, TSN, per esempio, e tutti quegli elementi costitutivi dell’architettura HW/SW che ci contraddistinguono rispetto a chi sceglie protocolli proprietari. Questo è un tema che ci permette di entrare in un’azienda, dove tipicamente si trovano scenari disomogenei, e uniformarli attraverso sistemi HW/SW, così che i sistemi informativi possano vedere la fabbrica o la linea di produzione secondo standard aperti. È importante riuscire in futuro a uscire dalla numerosità degli standard dei bus di campo che abbiamo a bordo delle singole macchine, e spero che il TSN ci aiuterà a fare questo. Nel frattempo noi ci appoggiamo a standard di fatto come OPC UA – Bosch Rexroth ha l’OPC UA tra i più sviluppati sul mercato – e riusciamo a essere veramente precisi sui dati necessari da raccogliere rispetto alla macchina. Abbiamo i nostri gateway che sono nativamente configurabili rispetto a standard di fatto come Mysql, ad Azure, ad AWS”.
La battaglia fra standard proprietari, e standard aperti è un deja-vu per chi arriva dall’IT. Ma Bosch partecipa a iniziative di standardizzazione in qualche modo?
“Ovviamente sì, il gruppo Bosch è presente nei consorzi di standardizzazione di Industry 4.0, siamo nei consorzi di OPC UA e TSN, nel consorzio per l’embedded software, siamo parte integrante di quei comitati di standardizzazione che afferiscono agli standard aperti. Abbiamo fatto questa scelta di lavorare su standard aperti molti anni fa, perché per noi saranno fondamentali e garanzia di soluzione a prova di futuro. Pensi alle aziende che sono di fronte a una sfida evolutiva di integrazione delle macchine, dove non c’è una chiara direzione. Qual è quell’architettura che può essere future-proof? Solo quella aperta, perché mi permette di adattare la mia architettura di fabbrica all’evoluzione più opportuna. Se io mi blindo rispetto a una piattaforma, mi devo affidare che sia il meglio possibile rispetto al mio fabbisogno, invece di lavorare sfruttare la flessibilità di standard condivisi”.
Quindi si tratta non di una scelta di campo, ma di una scelta di vantaggi competitivi che magari nel presente non si vedono, ma che in prospettiva diventano evidenti. “Siamo in una fase in cui sono partite diverse iniziative, e chi sopravvivrà è ancora da vedere: il tema della standardizzazione è complesso. Il TSN è sulla buona strada e siamo nel consorzio come lo siamo in quelli che offrono maggiore garanzia in termini di prospettiva. Estendendo il concetto, siamo anche attivi nel mondo blockchain. Ma l’uso della blockchain nell’automazione va, al momento per quanto riguarda l’automazione, oltre il beyond…”.