Innovare e fare evolvere l’azienda lungo la strada dell’Industria 4.0 non può essere la tendenza di qualche imprenditore o manager “illuminato”: è l’unico modo per restare competitivi sui mercati mondiali. Questo vale anche per un settore, come il Tessile e il meccanotessile italiano, che ha una storica e forte tradizione, innanzitutto nei distretti di Como, Biella, Prato: un comparto che le imprese di oggi vogliono portare avanti cogliendo le opportunità offerte dalla Digital transformation.
Per farlo, devono affrontare e mettere in pratica un cambiamento senza precedenti, che alcuni hanno già iniziato a realizzare, altri si trovano a rincorrere. Ma senza alternative: chi non cresce, in termini di innovazione, è destinato alla marginalità o all’estinzione.
Gli operatori e i protagonisti del settore, abituati ad avere a che fare con macchine per filatura e telai, fibre e Design Made in Italy, devono maneggiare con sempre più abilità anche gli strumenti della tecnologia, tra Smart factory e digitalizzazione della produzione, Cloud, efficienza energetica, sostenibilità. Gli stessi fattori che sono stati al centro di un convegno, “Industria 4.0: trasformazione digitale dei processi di sviluppo dei prodotti tessili. Sfide e opportunità”, che si è svolto questa settimana a Villa Erba di Cernobbio, sulle sponde del lago di Como, organizzato da Messe Frankfurt Italia, con TexClubTec e Acimit.
Indice degli argomenti
La digital transformation del meccanotessile
“L’industria tessile, a livello mondiale, è interessata da una profonda trasformazione digitale. La digitalizzazione del processo produttivo è la condizione necessaria per avere un più rapido Time to market, e una produzione Just in time”, rimarca Alessandro Zucchi, presidente di Acimit, l’Associazione dei costruttori di macchinari per l’industria tessile. Che fa notare: “il contributo che la tecnologia italiana può dare in questo processo è fondamentale”.
Il settore meccanotessile, rappresentato da Acimit, coinvolge circa 300 aziende, per un totale di 12 mila addetti, e un giro d’affari annuo superiore ai 2,5 miliardi di euro, di cui l’80% circa è orientato all’Export, innanzitutto verso l’Asia, Turchia e India. Con mercati importanti anche nell’Unione Europea e Stati Uniti. Ma è la Cina a restare il primo mercato dei costruttori italiani: la sua quota rappresenta il 16% del totale esportato, e vale oltre 300 milioni di euro.
L’Italia è il terzo Paese al mondo nella produzione di macchinari per l’industria tessile, dopo Germania e Giappone. Nel 2016 l’Export italiano ha ricevuto il maggiore contributo dal comparto delle macchine per nobilitazione dei materiali (32% del totale). Vengono poi le macchine per filatura (22%), e quelle ausiliarie (22%). Le macchine per maglieria, tessitura, e altri macchinari, rappresentano quote inferiori delle esportazioni Made in Italy.
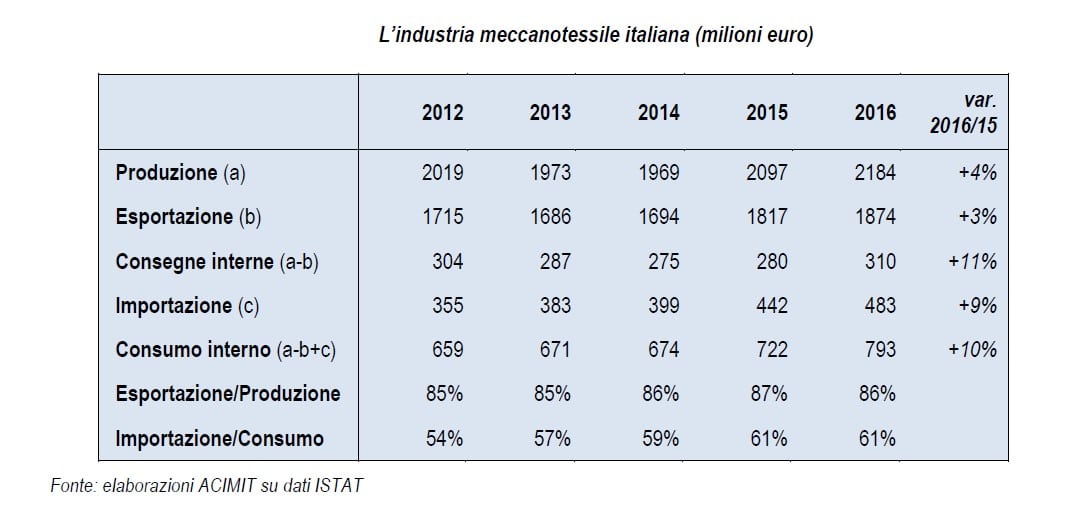
Nel complesso, “all’interno del nostro settore c’è una buona conoscenza delle tecnologie abilitanti, in particolare Cloud e stampa 3D, con l’utilizzo di queste risorse che porta a buoni riscontri sulla produttività, innanzitutto attraverso Cloud e Cybersecurity. Ma con la necessità di comprendere meglio come nuove tecnologie possano essere declinate alla propria realtà industriale”, rimarca Zucchi.
Le dinamiche del cambiamento nel settore tessile-abbigliamento, ad esempio, hanno costretto i rivenditori a cercare costi sempre più bassi, flessibilità nella progettazione, qualità e velocità verso il mercato. L’industria, dominata da piccole e medie imprese, ha in gran parte abbandonato la produzione a basso valore aggiunto, e aperto nuove aree di applicazione per i materiali tessili a maggiore qualità, innovazione e sostenibilità.
Tendenze e strategie aziendali
Le decisioni strategiche che un’impresa mette in atto, per raggiungere obiettivi di innovazione e sviluppo, “non possono prescindere da un’analisi dei megatrend, ossia di quelle tendenze che caratterizzano l’andamento del mercato”, sottolinea Elgar Straub, Managing director di Vdma, l’Associazione tedesca dei costruttori di macchine e impianti per la produzione tessile. “Per questo, un approccio per scenari e l’analisi di questi Trend rappresentano una parte importante della strategia aziendale per l’innovazione”, spiega Straub.
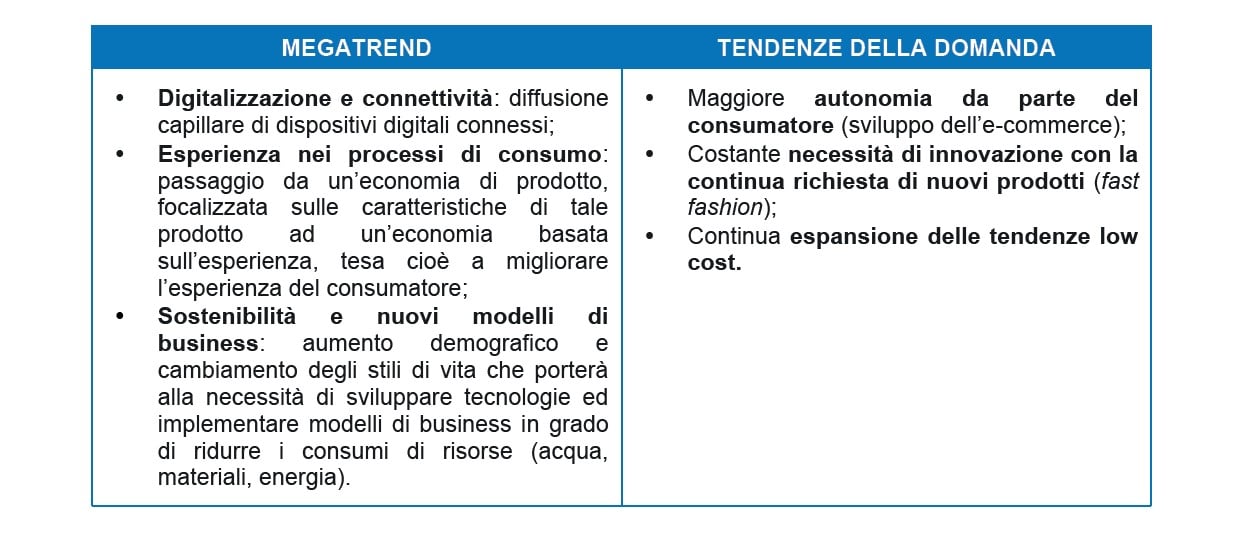
Per quanto riguarda il Business, la più grande innovazione introdotta da Industria 4.0, rileva il Managing director di Vdma, “è l’utilizzo di dati come strumento per creare valore. La possibilità di gestire grandi quantità di dati permette alle aziende di prendere decisioni in tempo reale sulla base di informazioni dettagliate, altrimenti non disponibili. L’acquisizione di queste informazioni, insieme a una rapida capacità di gestione del ciclo produttivo, favorisce alti livelli di flessibilità, una notevole capacità di personalizzazione del prodotto, un aumento di qualità, efficienza e produttività”.
E su un punto il manager tedesco è drastico: “chi non sta al passo, uscirà dal mercato”.
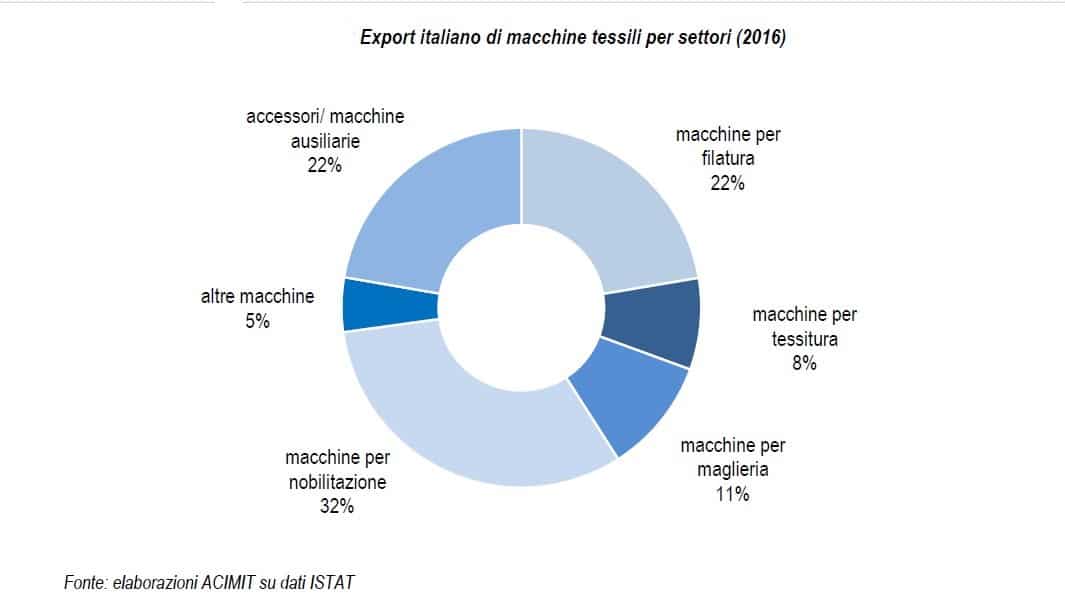
Oltre alla produzione speed-to market e a una filiera che deve lavorare just in time o just in sequence, altre tendenze del settore tessile abbigliamento, a cui le tecnologie devono dare risposte efficaci, sono la maggiore autonomia del consumatore nei processi di acquisto, via eCommerce e Mobile commerce, e la diffusione del mercato low cost.
‘Smarcarsi’ con soluzioni originali
Le prime azioni necessarie per raggiungere l’obiettivo di azienda meccanotessile 4.0, sono “l’adozione di tecnologie d’integrazione e di connessione aziendale e, più in particolare, l’applicazione dell’Internet of Things alla produzione industriale, il collegamento in rete di persone, prodotti e macchine, e l’utilizzo di sistemi automatici per il controllo e la gestione della produzione”, sottolinea Cristian Locatelli, General manager di Marzoli, azienda del gruppo Camozzi che si occupa di sistemi per la filatura, e vice presidente di Acimit.
Che rileva: “la Marzoli può contare su 336 brevetti internazionali, e il nostro Export ammonta in pratica al 99,9% delle nostre vendite di macchinari”, per un fatturato annuo attorno ai 50 milioni di euro.
“Risultati che otteniamo anche grazie alla nostra capacità interna di sviluppare algoritmi e software dedicati a nuovi macchinari e soluzioni, Intelligenza artificiale applicata”, sottolinea Locatelli: “attraverso speciali algoritmi, monitoriamo a distanza il funzionamento delle macchine, 24 ore su 24, 7 giorni su 7, e allertiamo il cliente in caso di anomalie. Abbiamo realizzato un Customer service digitale e online, sempre attivo”.
I 3 fattori principali che guidano l’innovazione di Marzoli sono: ottimizzare la produttività; continua ricerca di maggiore efficienza; flessibilità di produzione.
“L’innovazione va fatta, non c’è alternativa, o non si resta competitivi”, ribadisce anche Locatelli, “e nel sviluppare nuove tecnologie è anche importante smarcarsi, trovare soluzioni inedite, non si possono sempre inseguire le tecnologie che vengono da fuori”.
Innovare anche per risparmiare
L’industria 4.0 deve poi essere anche “conto economico, riduzione dei costi, ritorno dell’investimento. Deve portare benefici operativi, che si trasformano in benefici su costi e conti”, rimarca Nicola Lorenzi, direttore industriale dei 2 stabilimenti italiani di Itema, una “multinazionale tascabile” della Val Seriana, in provincia di Bergamo, parte del gruppo Radici, che produce telai per la tessitura.
E Lorenzi sottolinea: “in questi anni abbiamo ripensato le nostre logiche produttive e logistiche, con la digitalizzazione dei processi abbiamo più che raddoppiato la produzione. Siamo partiti dai processi più a valle della filiera produttiva, e da lì abbiamo ottimizzato tutta la catena del valore. In pratica, dall’ottimizzazione locale, siamo passati a quella complessiva”.
Stampa digitale, l’avanguardia italiana
Marco Brenna, responsabile del Reparto Ink jet della Stamperia di Lipomo, e rappresentante del Sistema Moda Italia, spiega: “nel campo della stampa digitale, applicata al tessile, nel territorio comasco abbiamo già raggiunto volumi superiori al 50% del totale, a fronte di una media del 5% nel mondo. E le nuove tecnologie ci permettono di sviluppare prodotti nuovi, che oggi sono seguiti, accompagnati, da tutte le informazioni che li riguardano, in tutte le fasi di produzione”.
Guardando allo scenario generale del tessile italiano, le fasi di produzione e manutenzione risultano essere quelle più strutturate per implementare le tecnologie di Industria 4.0: sistemi IoT e algoritmi di Intelligenza artificiale sono alcuni esempi pratici di applicazione, per monitoraggio remoto e manutenzione predittiva dei macchinari.
La fase di design e progettazione, invece, risulta essere più distante dall’obiettivo di Industria 4.0. Esempi di realtà virtuale e simulazione dei componenti del macchinario rappresentano i primi passi per l’adozione delle tecnologie anche nella fase di design.
“In azienda abbiamo fatto un importante investimento sul controllo di qualità e sul magazzino in ottica Industria 4.0”, sottolinea Alberto Paccanelli, amministratore delegato di Martinelli Ginetto Group, consigliere Smi, presidente del Cluster Tecnologico Made In, e presidente del Digital Innovation Hub di Bergamo.
E spiega qualche dettaglio: “nei nostri tre stabilimenti produciamo tessile di biancheria per la casa, ogni anno realizziamo circa 2 mila nuovi tessuti. Ora abbiamo rivoluzionato il processo di immagazzinamento di oltre 20 mila articoli, abbiamo realizzato sei magazzini verticali, con scomparti a vassoio, alti 17 metri, digitalizzati, per la movimentazione integrata. Ognuno dei 20 mila articoli, ha la sua carta d’identità digitale, che contiene tutte le informazioni sul prodotto, e sistemi robotizzati portano i tessuti alle fasi di taglio e spedizione”.
Il cambiamento passa anche dalle competenze
L’Industria 4.0 è focalizzata sul massimizzare le sinergie e l’equilibrio tra i tre modelli chiave per l’azienda: Business, organizzativo e tecnologico. I primi due rappresentano gli Asset aziendali immateriali, e sono più complessi da modificare; il terzo rappresenta lo strumento abilitante che mette l’azienda nelle condizioni di intraprendere un processo innovativo.
In quest’ottica, “la nostra innovazione si basa su tre pilastri: meccatronica, sistemi di automazione integrati, e Digital transformation”, rileva Giuseppe Testa, Sales director di Lenze Italia: “puntiamo anche a massimizzare i benefici del Cloud, che ha possibilità enormi nel manifatturiero: il prodotto diventa ‘perfetto’ strada facendo, per questo è essenziale usare i dati per svilupparlo”. Ma il Cloud è o non è sicuro? “Noi lo usiamo con criteri protetti e garantiti da un ente esterno”, rassicura.
Ma per adottare un approccio Industria 4.0 non è sufficiente affidarsi alle sole nuove tecnologie, “bisogna innanzitutto attuare un cambiamento a livello culturale nelle organizzazioni, attraverso un ammodernamento delle strategie e dell’organizzazione, e un coinvolgimento di persone che abbiano le competenze specifiche necessarie”, ricorda Giuseppe Rosace, ricercatore del Dipartimento di Ingegneria e Scienze applicate dell’Università di Bergamo: “fare automazione significa anche alzare il livello delle competenze”.
E spesso il problema è proprio questo, trovare le professionalità aggiornate e idonee, in un mercato del lavoro che cambia velocemente, come le tecnologie utilizzate, e che in Italia non offre grandi disponibilità di competenze specializzate.
“Le aziende devono confrontarsi e comunicare con le istituzioni e i centri di formazione sul territorio, per uno scambio continuo di informazioni”, rimarca Fulvio Alvisi, specialista comasco nel Design del Tessile, e membro del Board di Villa Erba a Cernobbio: “la collaborazione con SPS Italia nasce dall’opportunità di un incontro tra il Tessile, qui nel territorio lariano, nel suo distretto più creativo, e l’innovazione tecnologica, che coinvolge tutti gli operatori. Un percorso obbligato per riuscire a mantenere un saper fare, crescere nella qualità, rispondere alle esigenze di un settore che vive sulla novità e sulla velocità. Dobbiamo portare avanti una tradizione, che è alla base della formazione necessaria per affrontare il cambiamento, sempre in un’ottica di livello internazionale”.
Manifatturiero, distretti e territorio
Il convegno di Cernobbio è stato la prima tappa, la prima ‘Tavola rotonda itinerante’, del percorso di avvicinamento a SPS Italia, la fiera per l’industria digitale e intelligente, organizzata ogni maggio a Parma da Messe Frankfurt Italia. “Il rilancio del manifatturiero italiano passa attraverso i distretti e le regioni, e per questo organizziamo Tavole rotonde itineranti per entrare in diretto contatto con le aziende, le istituzioni del territorio e condividere esperienze di innovazione”, spiega Donald Wich, amministratore delegato di Messe Frankfurt Italia.
Che sottolinea: “Messe Frankfurt organizza ogni anno 150 fiere specializzate nel mondo, e di queste un terzo, circa cinquanta, sono dedicate al settore tessile”.
Le prossime tappe, e le altre Tavole rotonde tematiche, nel percorso verso SPS Italia 2019, sono in programma a Milano, il 26 febbraio, sul settore farmaceutico; a Bologna, il 20 marzo, sul mondo del Packaging; e a Torino, il 10 aprile, con focus sui settori Automotive e Aerospace.
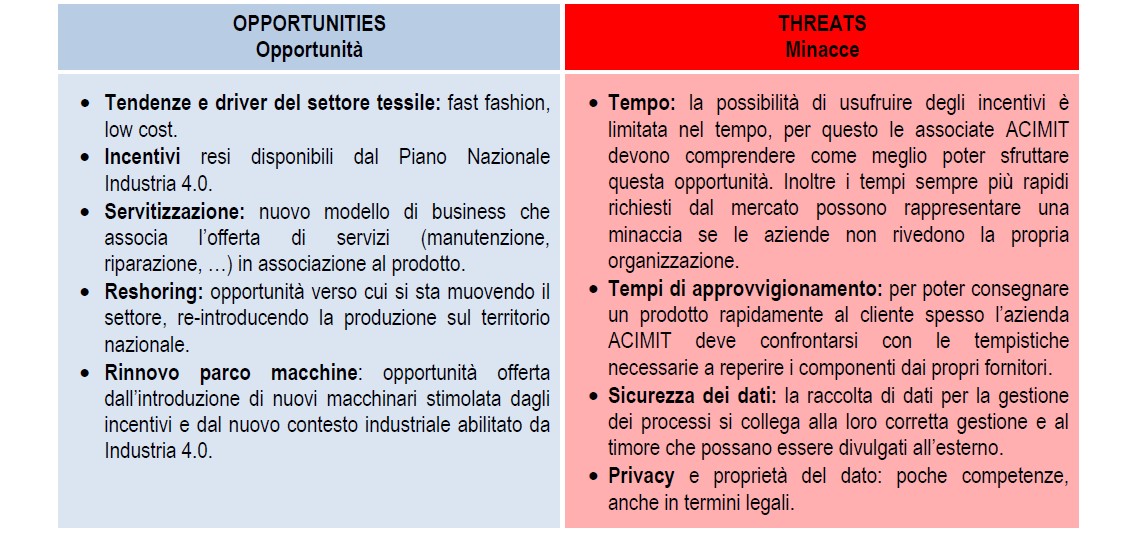